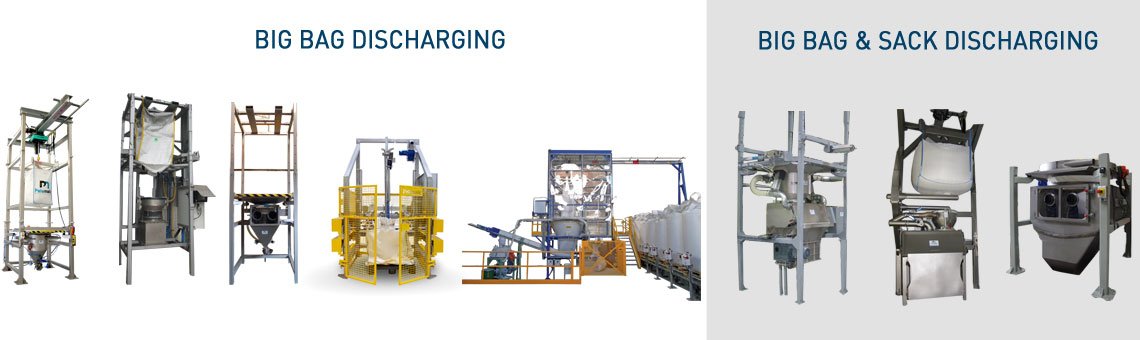
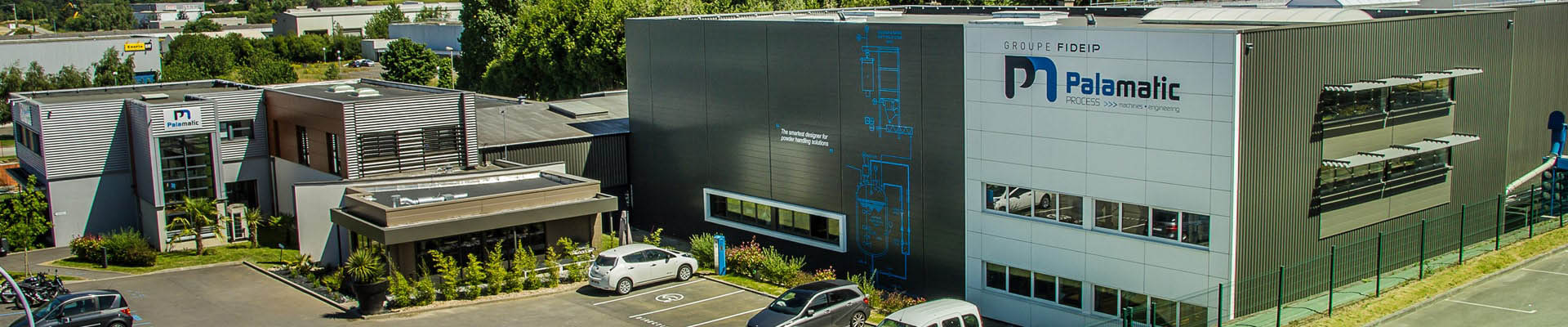
Palamatic Process has developed a wide range of bulk bag emptying stations, including EasyFlow® and Duopal® models, for handling your powders and powders.
Our big bags discharger systems are designed to meet the requirements of different types of deconditioning. They are frequently used for installations requiring slaked lime, activated carbon or polymer dosing.
Bulk bags can be loaded in a number of ways: electric hoist, forklift truck, low structure using an overhead crane.
The big bag discharger can be built in painted steel, hot-dip galvanized steel, 304L stainless steel or 316L stainless steel. The parts in contact with the bulk material and the structure can be made of different materials.
Further options are available for our big bag unloader machines depending on the needs of the operation such as bag massage system, vibrating hopper, load cells, etc...
Our range of big bag discharging stations:
The standard EasyFlow® EF0 big bag unloader with unlacing cabinet has been designed to unpack big bags in an ergonomic way and to facilitate their handling.
The EasyFlow® EF1 big bag unloading station structure with telescopic tube is ideal for ensuring that your bulk bag discharging process is completely dustproof and that your bulk materials flows out easily.
The EasyFlow® EF2 big bag discharger, equipped with a glove box, allows safe handling of toxic products by the operator thanks to total containment.
The EasyFlow® 100-200 big bag discharging station performs cutting, handling and evacuation of big bags in autonomy.
EasyFlow® EF500 is an automatic higjh rate big bag unloader, without operator intervention. This station is based on a big bag gripper, also called hydraulic gripper, and is mounted on an overhead crane. It guarantees the translations above the discharging hoppers. The big bag is then automatically discharged into a bulk bag compactor or a baler.
For partial, multi-product discharging with an integrated weighing device, the EasyFlow® Flex big bag unloading station is the most suitable. Made of a retractable suction tube, this big bag discharger offers the possibility to remove a half-full big bag.
The Duopal® big bag and sack discharging station offers a bigbag discharging system by electric hoist, forklift or overhead crane and is available in a low structure. This big bag dump station offers the possibility of confining the processed powders in an Atex 22 atmosphere. The big bag emptying of the range also ensures a total sealing during the unloading of the bulk materials and guarantees an ergonomic work for the operator.
This big bag unpacking system avoids dust projections and bulk materials contamination. The unloading of raw materials is done in complete safety. The hygiene is maximum. The big bag dump station can also be fitted with a bag dump system, a massaging devis, a commercial dosing and weighing system, a vibrating hopper...
On the production lines, the big bag discharger is generally associated with systems of:
Palamatic Process is equipped with a state-of-the-art test facility and can carry out full-scale tests for big bag unloading, big bag dumping, and big bag discharging concepts. These tests can be combined with a pneumatic or mechanical conveying system, volumetric or weight dosing systems, and dust control filtration.
Our design office is at your disposal to review your process constraints and offer personalized handling solutions tailored to the powders you handle and your industry.
Palamatic Process bulk bag unloading systems are adaptable to all industries: food processing, chemical, fine chemicals, construction, water and flue gas treatment, and nuclear.
Powder handling is feasible in all these sectors, including when dealing with explosive (ATEX-rated) powders.
If your powder has poor flow characteristics, a bulk bag massage cage can be integrated into your setup. Discover the three key benefits of using a bulk bag crusher.
Our project managers can also conduct studies for investment plans aimed at improving industrial efficiency and debottlenecking your site to optimize your product manufacturing.
Big bag emptying stations offer many advantages, particularly in terms of safety, versatility and efficiency. They minimize the risk of spillage and tippings, are adaptable to various materials and applications, and enable rapid and efficient transfer of materials.
Compliant with safety and environmental regulations, they reduce waste, improve product quality and can be automated for complete emptying. In addition, they are flexible, easily integrated into existing installations and are reliable, requiring little maintenance.
Choosing the right big bag emptying station depends on several important factors, such as the nature of the product (physical characteristics, properties, dangerousness), production constraints (emptying rate, volume, integration), the working environment (available space, ATEX conditions, hygiene standards), ergonomics and safety (handling frequency, weight of bulk bags, level of automation), specific options (massage system, total containment, traceability) and budget (initial cost, productivity gains, maintenance costs).
Big bag emptying stations can be compatible with ATEX environments (explosive atmospheres) thanks to appropriate design and equipment. Manufacturers offer ATEX versions incorporating safety features such as grounding, anti-static materials, certified electrical components and containment systems. It is crucial to use suitable big bags, such as types C or D. Consult experts to ensure the equipment meets the required safety standards. By following these precautions, big bag emptying stations can operate safely in ATEX environments.