Description
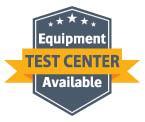
Standard manual bag dump station for a reduction of dust emissions
Bag dump stations are designed to minimize dust emissions during the manual process of bag opening and dumping.
Our range of standard manual bag dump station
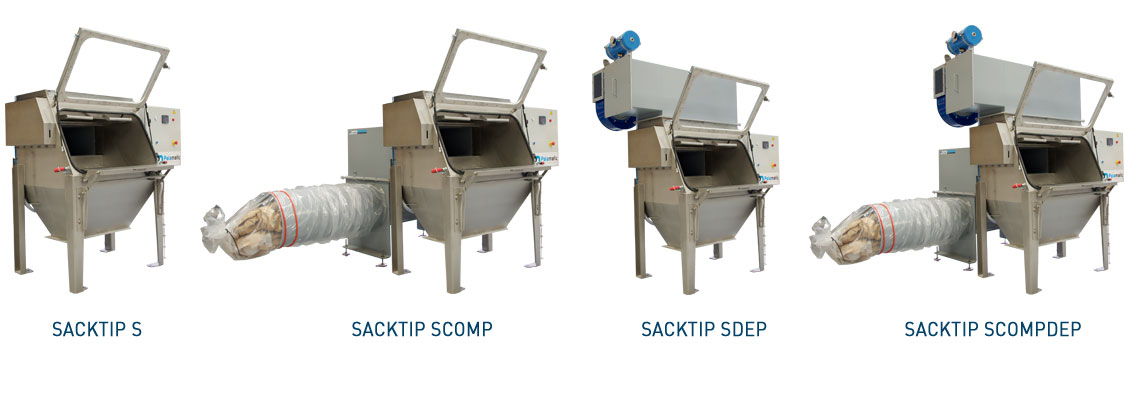
Manual and ergonomic unloading:
The Sacktip® S bag dump stations ensure the manual deconditioning of bulk materials that are delivered in bags at the production sites.
These bag dump stations, manufactured in steel or stainless steel and with an ergonomic design, allow the bulk materials to be stored and transferred to the production line without air contamination by dust emissions during the bag opening and discharge process. All cabins are equipped with dust extraction nozzles or integrated filters..
Operating mode:
The operator places his bag on a shelf, manually or using a vacuum manipulator, and positions it on the screen placed above the powder evacuation hopper.
Once the cutting operation has been performed, the operator opens the door and shakes the empty bag. The bag is evacuated via the compactor which limits the volume of waste in a polyethylene sheath and eliminates the rejection in the workshop of any residual dust in the bags.
-
Rate2
-
Automation1
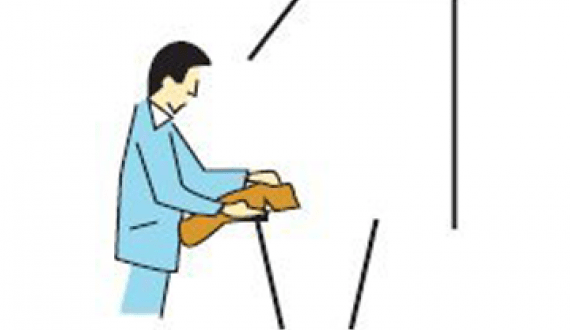
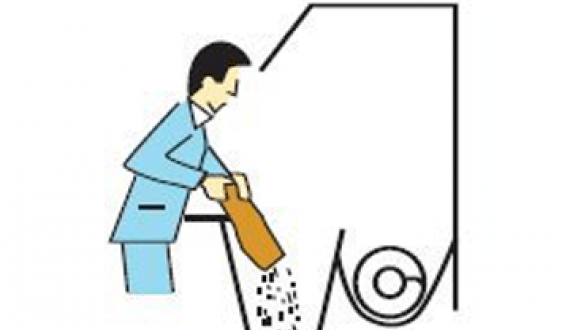
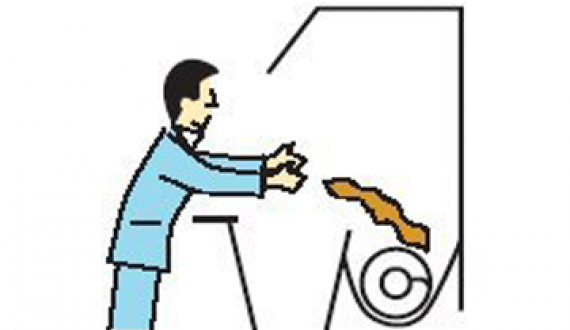
The access door is equipped with a gas spring for secure holding in both open and closed positions as well as assistance in lifting and closing the door safely.
A removable mesh screen with a 50 x 50 mm aperture and a 2 mm diameter wire is placed above the receiving hopper.
Equipment advantages
- Perfect ergonomics: the working position of the operator is efficient and safe
- Healthy working atmosphere
- Optional installation of nozzles or rotating washing heads for cleaning in place (CIP)
- Access door mounted on a gas cylinder
- Retractable bag removal tray
- Inner screen for supporting bags with sliding bar
- Product outlet chute adapted to each particular case
Media
View our equipment in videos
Sack discharging with bag manipulator
Optional integrated dust collection. Made of steel or stainless steel.
View our equipment in photos
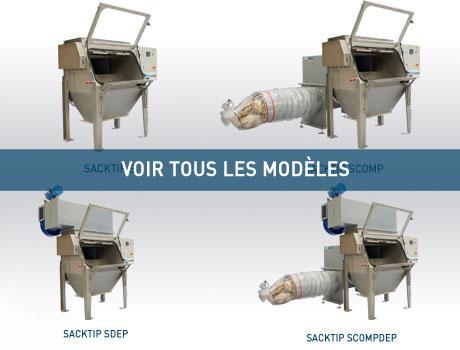
Standard bag dump station range
Our range of manual and ergonomic sack tip trays.
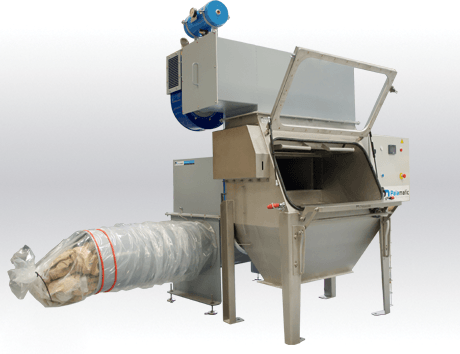
Bag dump station dedusting
Standard manual bag dump station with integrated compactor and dust extraction system.
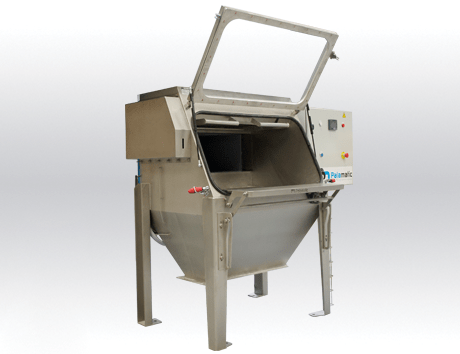
Ergonomic bag dump station
Access door mounted on a gas spring for assistance when opening and closing.
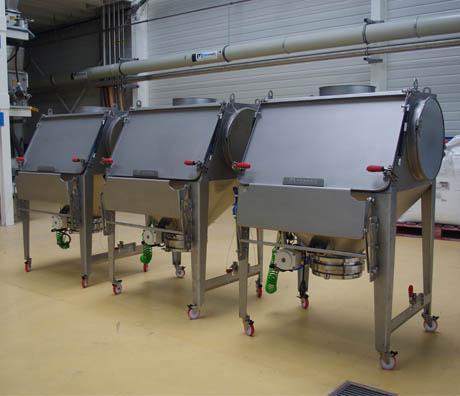
Sack emtying system
Bag dump stations manufactured in stainless steel.
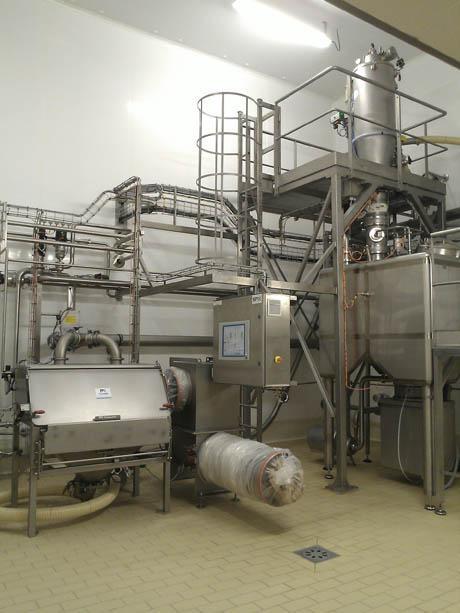
Bag opening system with integrated compactor
Bag dump station designed with ergonomic access door on gas cylinders and built-in bag compactor.
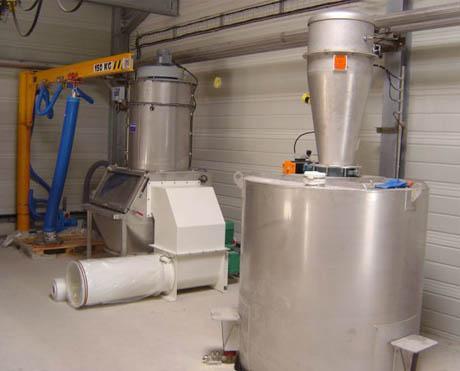
Bag discharging system with compactor
Removal of the empty bag to the compactor for safe waste containment.
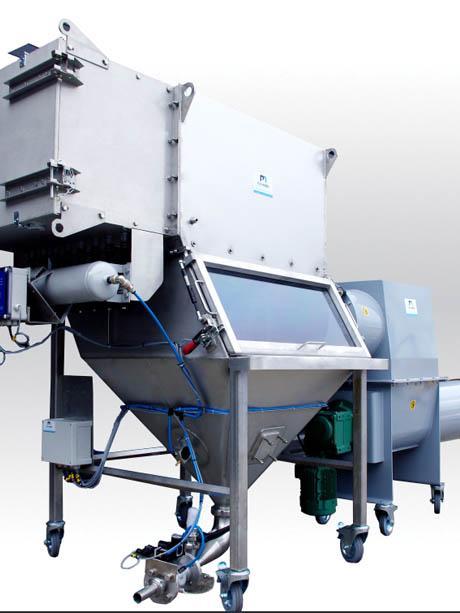
Manual bag discharging system
Bag dump station fitted with a dust control system and a sack compactor.
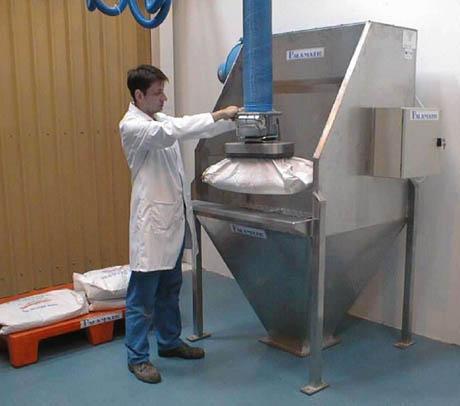
Bag dump station with vacuum bag lifting
The bag manipulator helps your operators lift and load heavy sacks of powder onto the bag dump station without risk of strain or injury.
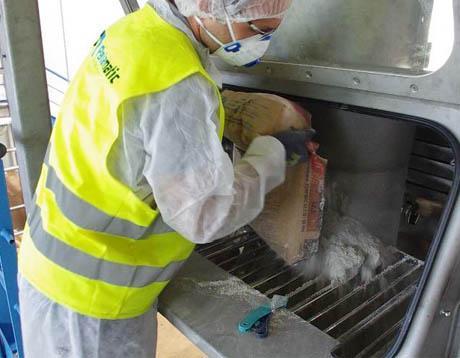
Sack Tip tray Palamatic Process
Internal safety grid for assistance in loading and holding the heavy bag during opening and emptying operations.
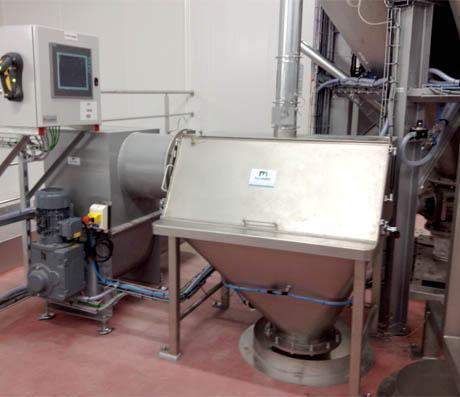
Sack discharging system
Bag dump station with compactor for empty sacks.
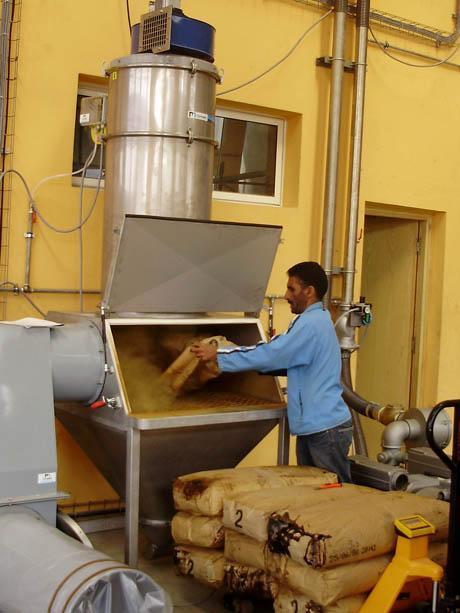
Bag dump station palamatic process
Bag dump station with dust-tight door.
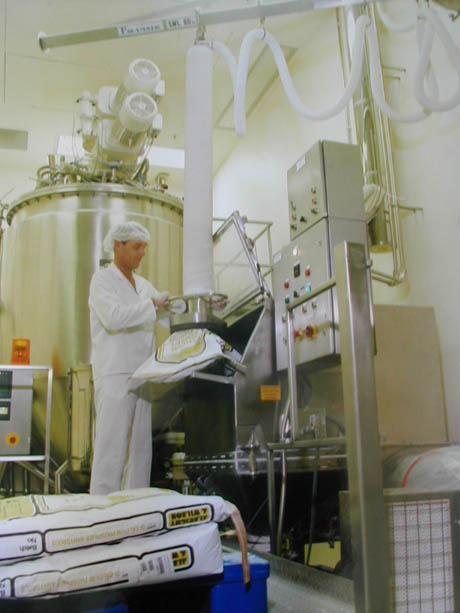
Sacktip - bag dump station
Bag tube lifter to load the bag dumper.
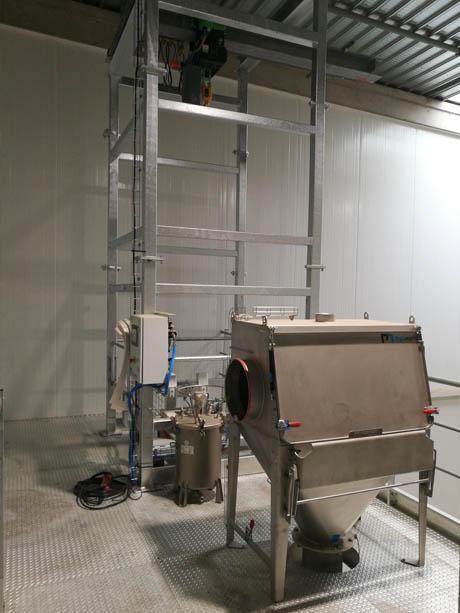
Bulk bag and sack unloading units for feeding materials into a mixer
Manual bag dump and bulk bag emptying stations for mixer feeding.
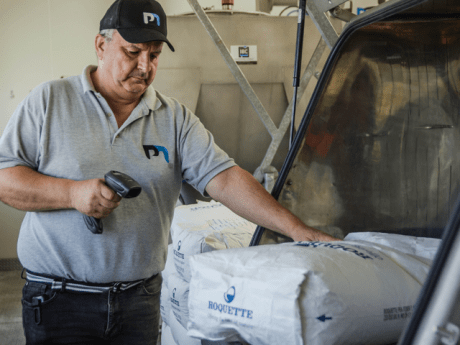
Tracking bags
Monitoring of production batches to ensure process safety.
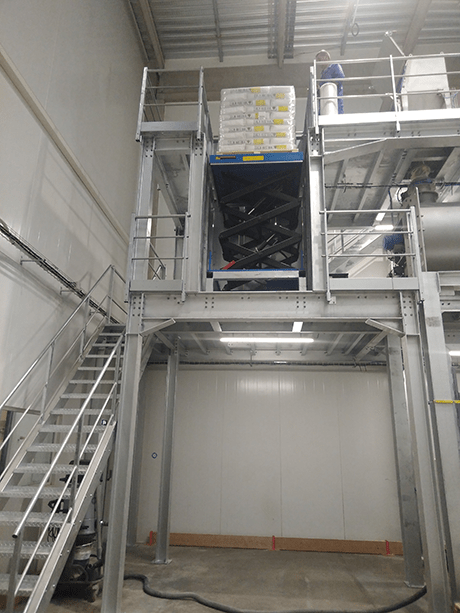
Lifting table sack discharging
Lifting table for manual bag discharging.
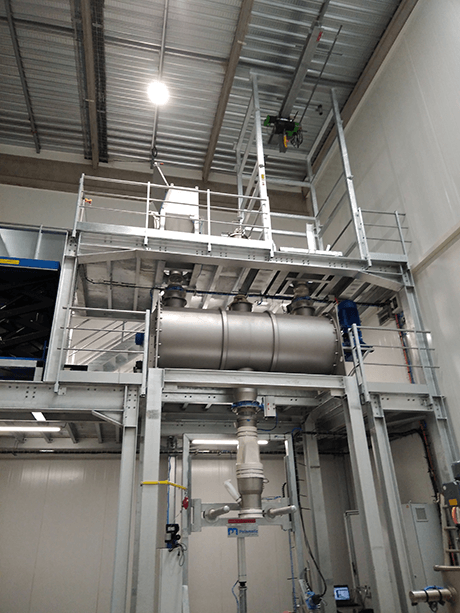
Sack tip tray for industrial mixer feeding
The bag is emptied into a standard bag dump station. The bulk material is then dropped into the industrial mixer using gravity discharge and flanged connections.
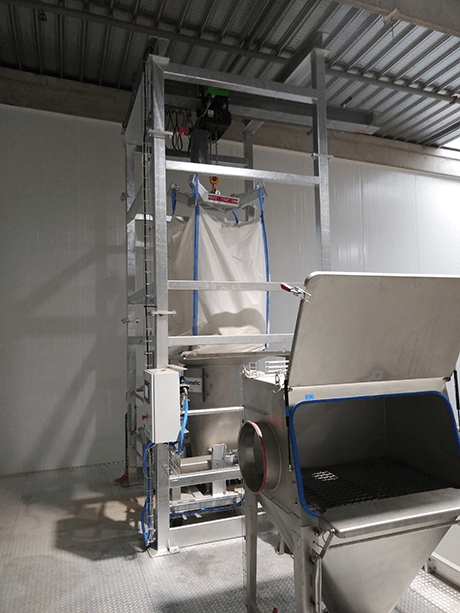
Bulk bag unloading station and bag dump station for feeding an industrial mixer
The operator places the bag on the safety grid, either manually or with a vacuum manipulator, positioned above the bulk material discharge hopper.
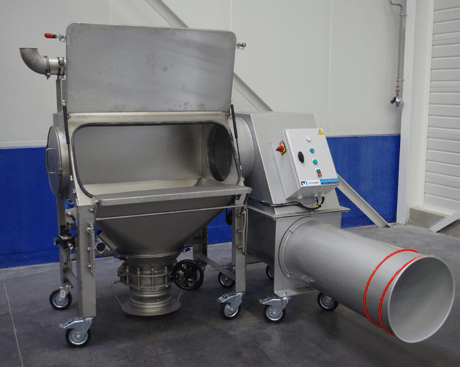
Customized sack discharging
Customized sack discharging with compactor for bulk materials handling. The bag compactor reduce waste volume and keep an healthy dust-free atmosphere.
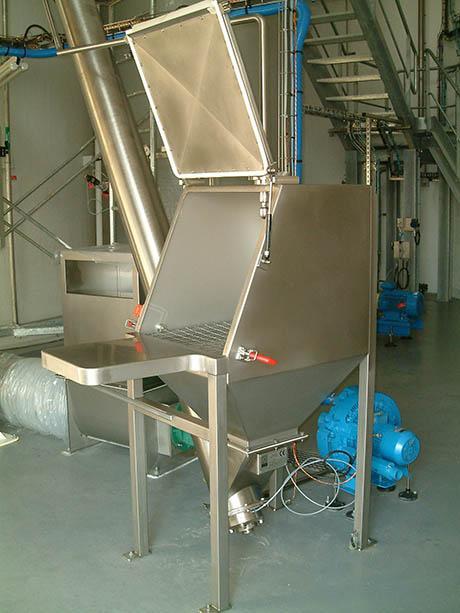
Bag dump station
Bag dump system with CIP cleaning system.
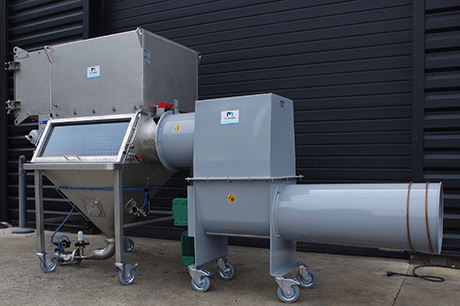
Mobile bag dump station
The bag dump station with dust collection and bag compaction assembly is installed on heavy duty casters for station mobility.
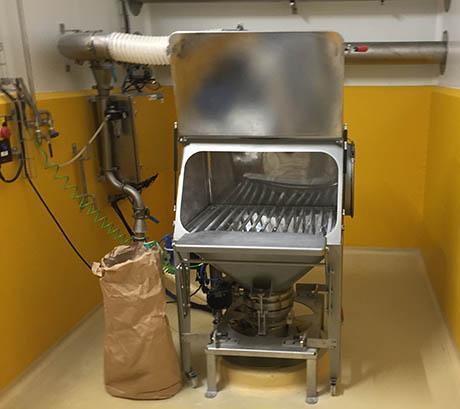
Sack unloading system for powder and bulk materials
Bag dump station - bulk solids handling.
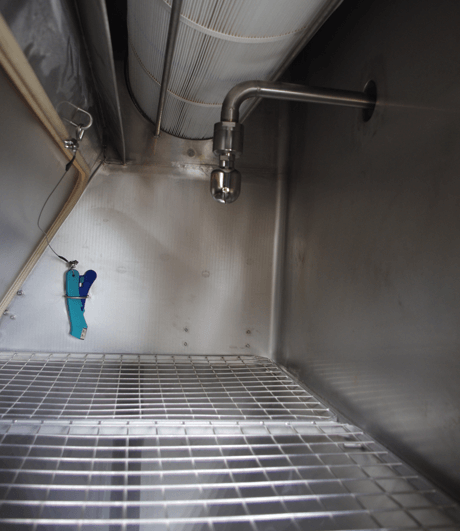
Washing head
Rotating washing nozzle/head for clean-in-place processing.
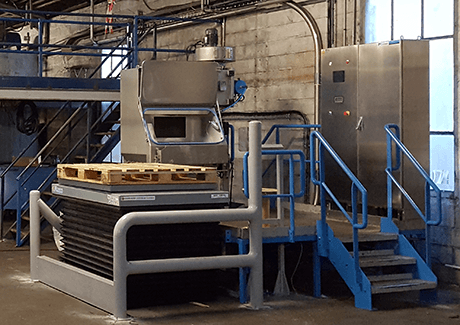
Bag dump station with dust collector for bulk materials handling
The bag dump station uses an integrated dust collector for a safe and clean work environment. The hinged door uses gas cylinders for safe and ergonomic opening and closing for access to the inside of the station. The access door is designed to be dust tight for full material containment.
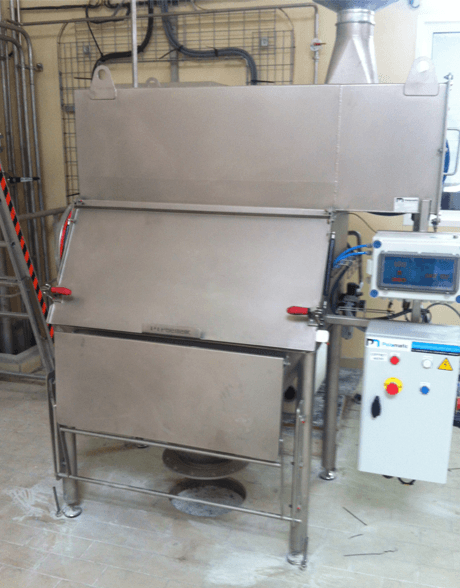
Bulk materials handling sack dump station dust collector
Work in a healthy atmosphere without pollution and without loss of bulk material.
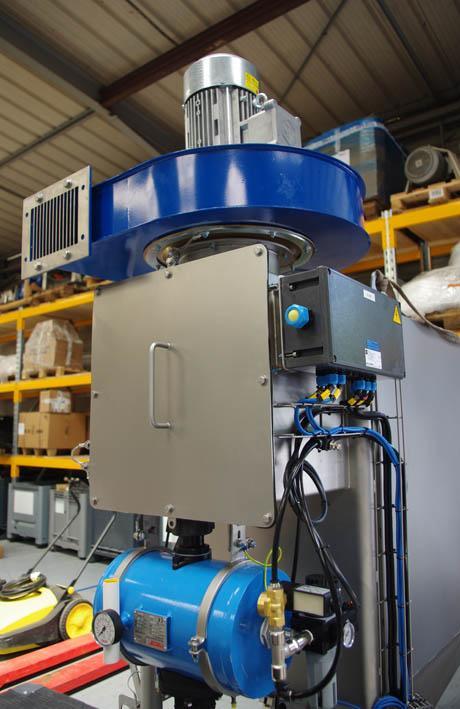
Integrated dust collector on a standard manual sack dump station
Healthy atmosphere without pollution and without loss of bulk material.
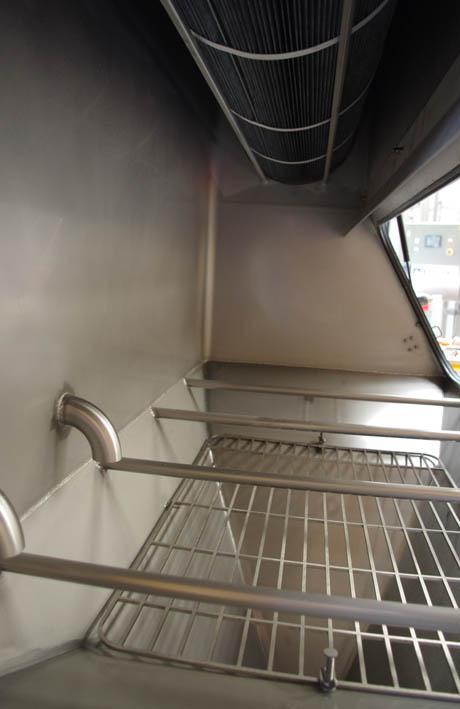
Manual sack tip tray
Internal safety grid with sliding bars for bag support and operator ergonomics.
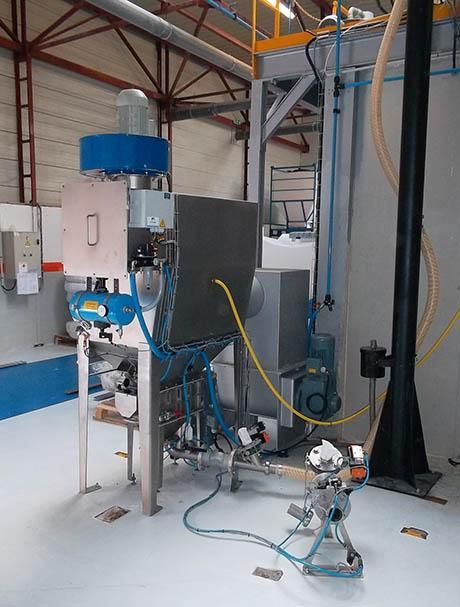
Bag dump station for the chemical industry
This sack tip tray is connected to a pneumatic vacuum conveying system that supplies a storage container for the production of detergent powder.
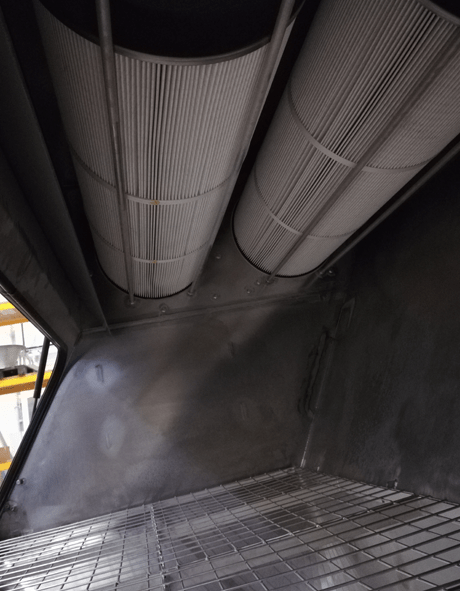
Bag dump station dust collection
Optional installation of an air filtration system to maintain a healthy working atmosphere.
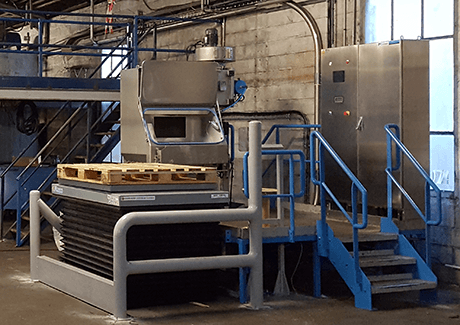
Bag dump station dust collection
Bag opening station with loss in weight hopper to prepare the correct quantities of powders. The bulk material transfer is conducted by a pneumatic vacuum conveying system.
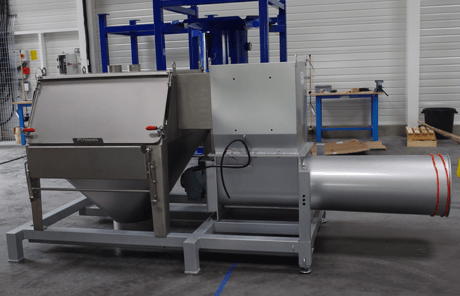
Standard bag dump station for dust containment
The manual sack tip tray station is the ideal solution for opening and emptying bags of dry bulk materials. The equipment provides a dust-free work area with an integrated sack compactor solution for full containment.
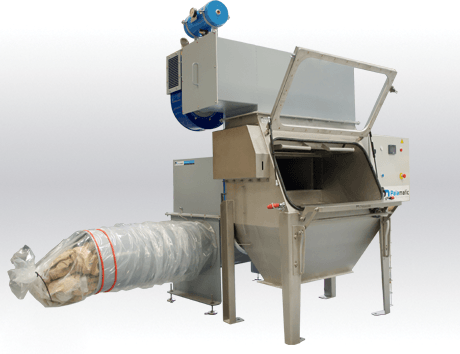
Bag dump station with integrated dust filter and bag compactor
The bag compactor helps reduce the volume of bag waste and contain any residual dust, preventing operator exposure to potentially hazardous health conditions.

Bag dump system with compactor
The bag compactor reduces the volume of waste and keeps the atmosphere healthy and dust-free.
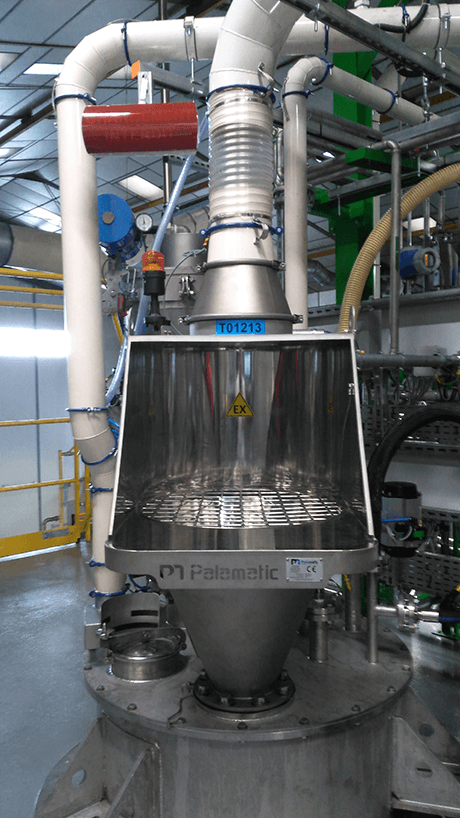
Custom manual bag emptying
Palamatic Process provides custom-made solutions for your bag dump station according to your implementation constraints and throughput rates.
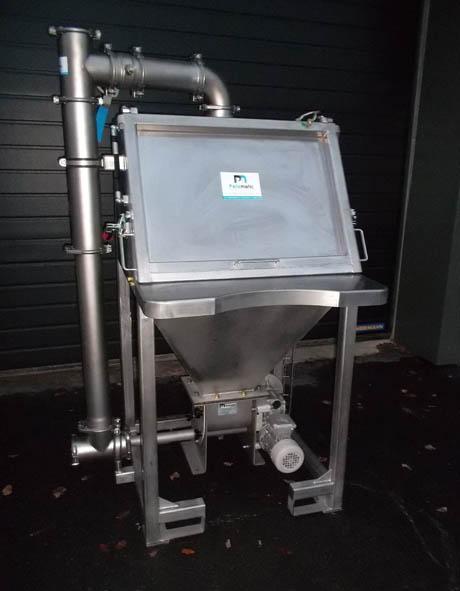
Manual bag emptying with screw feeder
Integrated dosing and weighing system to control the quantity of bulk solid materials introduced into the industrial processing line.
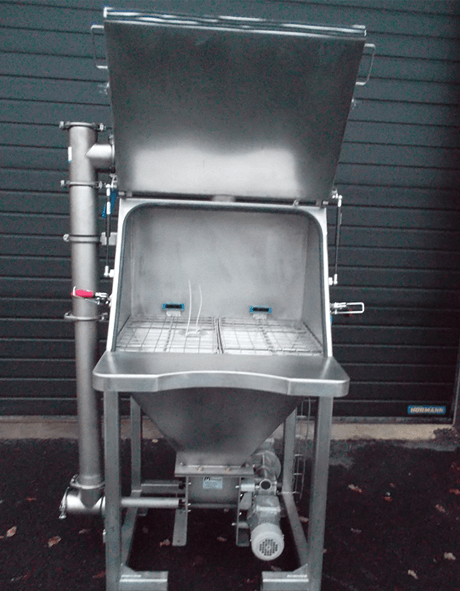
Manual sack discharging with screw feeder
Integrated dosing and weighing system to control the quantity of bulk solid materials introduced into the industrial processing line.
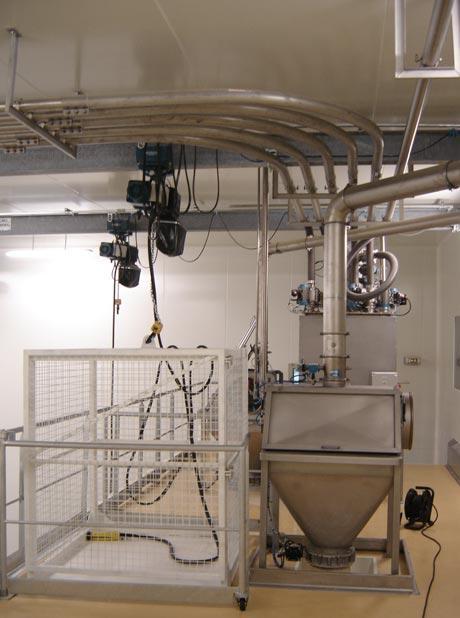
Bag emptying with pneumatic conveying
For bulk materials with difficult flow, we recommend the installation of a pneumatic vibrator installed in the lower part of the cyclone on a dedicated plate.
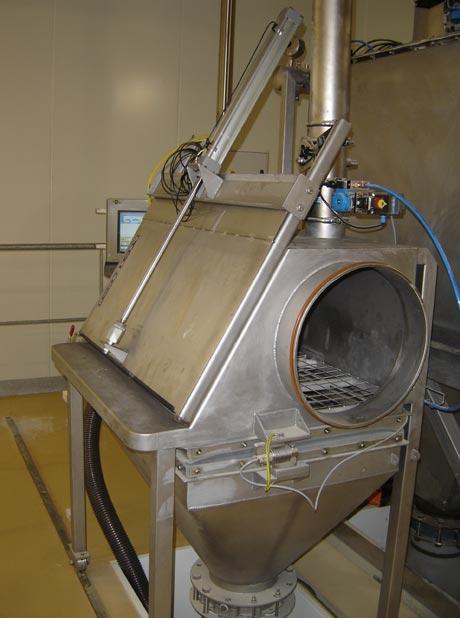
Bag dump station powder processing
All equipment can be configured according to your bulk materials handling requirements. The Palamatic Process design office is able to offer you very specific solutions.
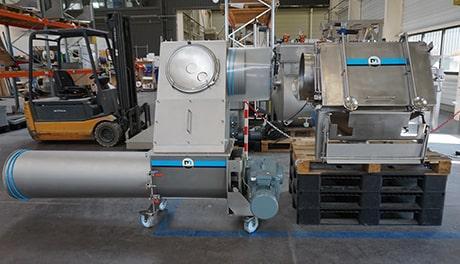
Bag dump station
Manual bag dump station equipped with a dustproof door.
Features
Technical specification
Flow rate | 2 to 6 sacks/min. |
---|---|
Manufacturing materials | Painted steel, 316L stainless steel |
Surface finishes | Customized RAL, bead-blasting, electropolishing |
Sealing: EPDM, NBR, natural rubber, silicone
Equipment integrated into the Sacktip® S model:
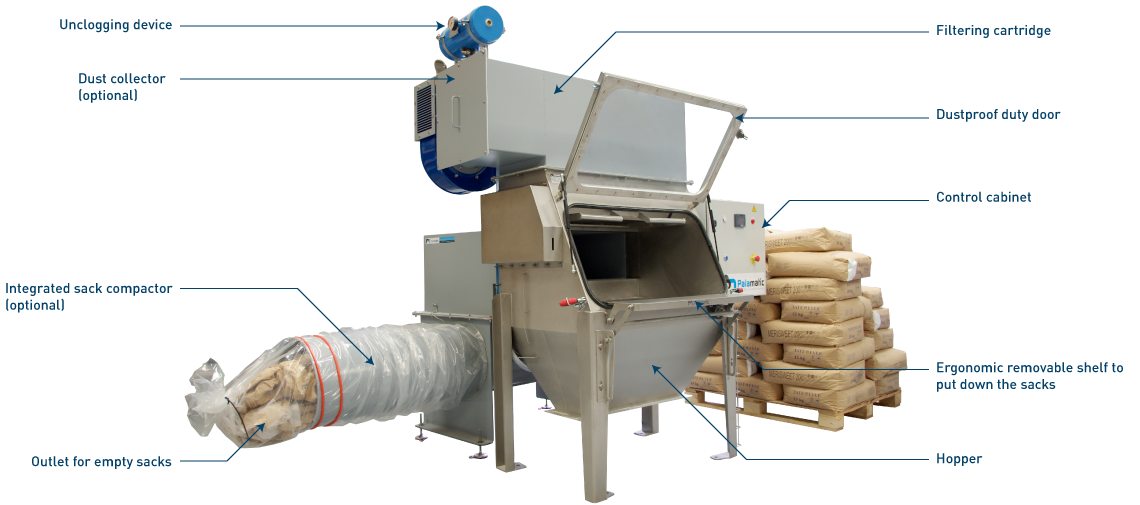
Standard models of the range:
Models | Bag dimension length | Flow rate for dust extraction (CFM) | Hopper water volume (Liters) | Outlet diameter | Height from floor to outlet diameter |
---|---|---|---|---|---|
S 800 | 650 | 800 | 180 | 250 | 285 |
S 1000 | 850 | 1,000 | 225 | 250 | 285 |
S 1200 | 1,050 | 1,200 | 265 | 250 | 285 |
S 1400 | 1,250 | 1,400 | 300 | 250 | 285 |
Options
Case studies
CASE STUDIES WITH THIS EQUIPMENT
Sugar dissolution for beverages
Processed powder: crystal sugar - Sugar dissolution for beverages - Company dedicated to the design of artisanal lemonade and artisanal syrup.Food and Animal Feed
Manufacture of food flavours
Processed powder: maltodextrin with a bulk density of 500 kg/m³ - Manufacturing of food flavours - Company specialized in mushroom extraction - Maltodextrin is packed in 20 and 25 kg bags. The...Food and Animal Feed
Blowing agent for PVC flooring
Powder processed: azobul - Blowing agent for PVC flooring - Continuous dosing supply of a PVC powder mixing reactor. The industrial metering system is fed by a vacuum pneumatic conveying system...Chemical
Masterbatch and additives
Processed powders: cobalt, calcium carbonate CaCo3, titanium dioxide TIO2 - Masterbatch and additives - Discharge of raw materials while maintaining a healthy atmosphere without pollution and without...Chemical
Resin formulation
Processed powder: resin - Resin formulation - This company in the petrochemical sector provides adhesive solutions.Chemical
Shampoo production
Processed powders: flake soda, lime powder, potash, magnesia - Shampoo production - This company in the cosmetics industry is involved in the implementation of industrial installations.Fine chemical
Resin and gel coat manufacturing
Processed powders: maleic anhydride, Epo Kukdo - Resin and gel coat manufacturing - The customer is one of the world leaders in the production of structural resins for the building, automotive, water...Chemical
Cake mix
Processed powders: modified starch, sodium bicarbonate, fat powder, whipping base, gelatin, milled sugar - Cake mix - Company based in Saudi Arabia that manufactures and distributes dry food materials...Food and Animal Feed
Animal nutrition food supplements
Processed powders: silica, clay, calcium carbonate, lithothamnium - Animal nutrition food supplements - This customer is a producer of specific mixtures of botanical extracts. In order to ensure its...Food and Animal Feed
Truck loading with amino acids
Processed powder: amino acids - Truck loading with amino acids - This facility concerns a major player in the production and marketing of amino acids for animal feed.Food and Animal Feed
Aromatic herbs conditioning
Processed powder: dried grass seeds - Seeds conditioning - Installation of a double discharge station: big bag emptying and container emptying for mixer feeding as well as a double filling station...Food and Animal Feed
Handling of veterinary bulk solids
Processed bulk solids: veterinary powders - Loading of veterinary powders - Company specialized in animal nutrition and health: workshop for the preparation and mixing of bulk materialFood and Animal Feed
Disperser feeding
Processed bulk materials: pyrogenic silica, calcium carbonates, expanded graphite, aerosil, imersil - Disperser feeding - The facility consists of a bag dump station fitted with a dedusting device and...Chemical
Loading of ingredients for the production of beverage
Processed materials: citric acid, potassium sorbate, sodium benzoate... - Loading of ingredients for the production of beverage - This installation concerns a new production line in a new building of...Food and Animal Feed
Deconditioning of food powders
Processed powders: wheat starch, potato starch, salt, egg white and sugar - Deconditioning of food powders - The customer is a Breton cannery specialized in the manufacture of surimi.Food and Animal Feed
Manufacturing of engine additives
Treated powder: diatomaceous earth - Manufacture of engine additives - Safe incorporation of powders with nitrogen inerting sluice in a sensitive environment, ATEX gas zone, zero retention.Chemical
Foundation production line
Processed powders: silica and iron oxide - Foundation manufacturing line - The aim of the installation is the mixing and homogenization of the different ingredients.Fine chemical
Milk powder mixing line
Processed powder: infant milk powder - Milk powder mixing line - The mixing line is totally cleanable with the complete dismantling of the equipment with our Palamatic-EasyClean range of equipment.Food and Animal Feed
Ingredient loading
Processed powder: sugar - Ingredient loading - This installation concerns a French company manufacturing spirits.Food and Animal Feed
Sugar grinding unit
Processed powders: icing sugar from white granulated sugar and starch - Sugar milling unit - The installation consists of feeding the mill with granulated sugar and then packaging the resulting icing...Food and Animal Feed
Glue production unit
Processed powders: polyester powders - The powder is delivered in big bags or sacks for storage in a weighed buffer hopper.Chemical
Automation of the feeding of zinc powder to the process
Processed powders: zinc powder and additives. The aim is to improve the manual loading of the powders and to implement a complete automated system for accurate dosing of the ingredients into the...Energy
Process for the production of chocolate
Process materials: granulated Sugar, whey, skim milk powder, and various other minor additives - Process for the production of chocolate - Objectives: unloading, transfer, storage and dosing of...Food and Animal Feed
Ergonomically designed bag dump station for the safe and contained handling of bags of sugar
Processed powder: granulated sugar - Bag opener for dust containment and operator ergonomics.Food and Animal Feed
Automation of the feeding process
Products processed: gluten flour, ascorbic acid, emulsifiers, enzymes, seeds and yeasts - Automation of the feeding process - Improvement of the preparation of premixes, quality and production...Food and Animal Feed
FlexMix® is a safe and flexible mixing solution for animal nutrition
Processed powders:sugar, sorbitol, locust bean gum, yeast derivatives, sodium chlorines Enhancing the safety and quality of feed supplements for livestock farmsFood and Animal Feed
Safe preparation of pyrotechnic powders: automated dosing and mixing line
Treated powders: ammonium perchlorate Safe preparation of pyrotechnic powders: automated dosing and mixing lineDefense