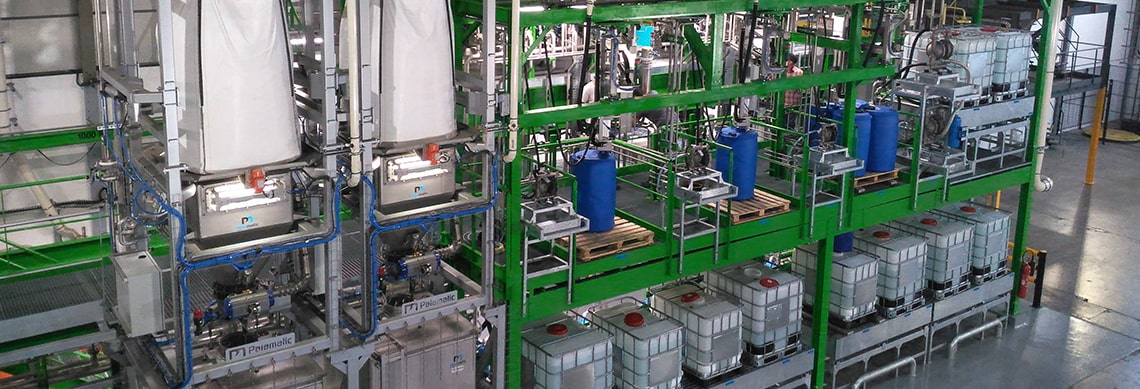
De implementatie van een nieuwe productielijn of apparatuur vereist een voorafgaande studie van uw poeders en bulkmaterialen, alsmede van uw behoeften en bedrijfsbeperkingen.
Onze experts komen terug op de 4 belangrijkste criteria om uw poederverwerkingsproject tot een goed einde te brengen.
1. Bepaal de kenmerken van uw poeders
Het is belangrijk de eigenschappen van uw poeders en bulkmaterialen te kennen wanneer u uw productieapparatuur plant en aanschaft.
De bulkdichtheid speelt een sleutelrol in hoe een poeder zich gedraagt op productielijnen, vooral bij opslag, transport en mengen.
Lichtere poeders zullen meer volume innemen wanneer gestreefd wordt naar een specifiek gewicht voor verpakking, terwijl voor zwaardere poeders een hogere snelheid nodig kan zijn om in transportbuizen te worden gebracht.
De deeltjesgrootteverdeling is ook belangrijk om de houding van uw poeder te begrijpen. Er zijn vele methoden om de deeltjesgrootte van uw product te meten, zoals laserinbreuk, zeven, vloeibare suspensie... Deze methoden leveren het bovenste, middelste en onderste bereik van de deeltjessamenstelling. PSD (particle size distribution) wordt vaak gemeten aan de hand van de waarden D90, D50 en D10, waarbij het getal overeenkomt met het percentage materiaal dat door een bepaalde zeef of maaswijdte gaat.
De reposehoek is een andere belangrijke indicator van hoe uw bulkmateriaal in een proces zal presteren. Dit is vooral belangrijk bij het ontwerp van de hellingshoek voor trechters en bakken.
Andere sleutelfactoren voor poeders zijn toxiciteit (vermijden van blootstelling van de operator), abrasiviteit (speciale coatings op apparatuur), hygroscopiciteit (vermogen van poeder om te klonteren in vochtige omgevingen), temperatuur (mate van gevoeligheid voor hoge temperaturen) en vochtgehalte.
Alle functionele eigenschappen van poeders moeten zorgvuldig worden geanalyseerd bij het ontwerpen van uw proces om de resulterende productiviteit te maximaliseren. Lees ons artikel over de 7 eigenschappen van poeders die je moet weten.
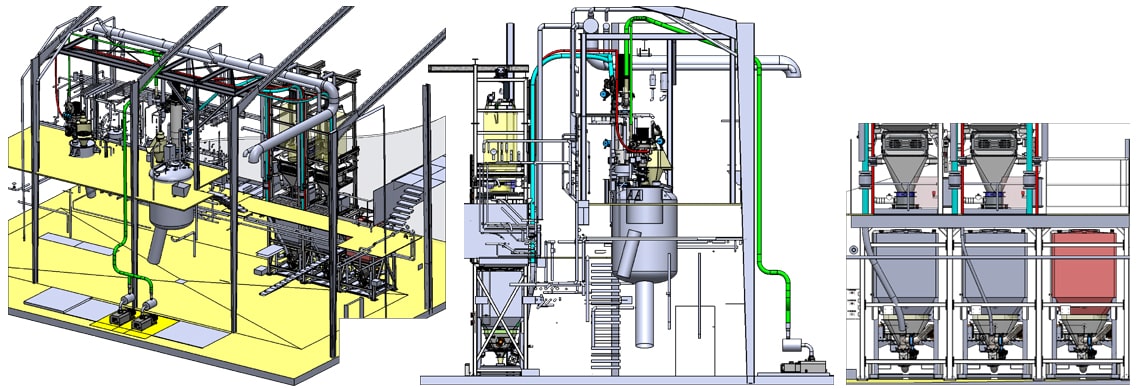
2. Bepaal uw gewenste productiedoelstelling
Of u nu een dagelijkse, wekelijkse, maandelijkse of jaarlijkse productiedoelstelling hebt, u moet apparatuur kiezen (zeefmachines, transportbanden, shredders, enz.) met de capaciteit om die doelstelling te halen.
De apparatuur kan zo worden ontworpen dat zij in elke fase van het proces precies aan uw productie-eisen voldoet. Het is echter raadzaam een speelruimte te behouden om onvoorziene behoeften aan te kunnen om de productiecycli te verhogen en zo extra capaciteit aan uw lijn te bieden.
Palamatic Process heeft verschillende modellen binnen zijn gamma van apparatuur die kunnen inspelen op verschillende productietempo's naargelang de behoeften van industriëlen.
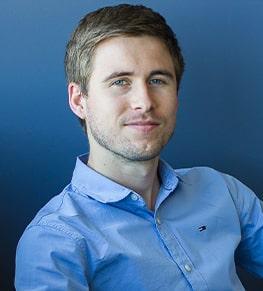
Heb je meer informatie nodig?
Ik sta tot uw beschikking om u te helpen.
Guillaume, expert in poeders
3. Rekening houden met de specifieke kenmerken van het ontwerp van de apparatuur naar gelang van het verwerkte poeder
De productie-uitrusting wordt gewoonlijk aangeboden in koolstofstaal, 304 of 316 roestvrij staal. Afhankelijk van de kenmerken van het te verwerken poeder zal de keuze van het constructiemateriaal verschillen.
In de chemische industrie en de mijnbouw kunnen leveranciers van apparatuur gelakt koolstofstaal gebruiken als het primaire fabricagemiddel. In de levensmiddelenindustrie wordt gewoonlijk roestvrij staal 304 gebruikt om redenen van reinheid. De farmaceutische, cosmetische of zuivelindustrie hebben zeer strenge hygiënische normen en gebruiken bijna altijd 316L roestvrij staal.
Naast het fabricage-element van een apparaat moet u ook kijken naar de polijstingen waaraan het oppervlak moet voldoen. Als uw poeder een kleverige substantie is, wat betekent dat het zich vastklampt aan alles waarmee het in contact komt, en moeilijk stroomt, dan zijn spiegelglansafwerkingen het meest effectief om te voorkomen dat het materiaal zich vastklampt aan de zijkanten van de productielijn. Korrelafwerkingen vallen over het algemeen in de volgende categorieën: 120, 150, 180 en 240, want hoe hoger het getal, hoe fijner de polijsting. Parelstralen, of 120 grit, is de typische standaardafwerking indien geen speciale overwegingen vereist zijn.
Andere factoren waarmee rekening kan worden gehouden, zijn elektrolytisch polijsten en passiveren, waardoor onzuiverheden worden verwijderd en het polijst- en hygiënische ontwerp van de apparatuur verder wordt verbeterd.
4. Classificeer uw gebied volgens de mate van gevaar
Rekening houden met de explosieve aard van uw poeder en de verwerkingsruimte is van cruciaal belang voor uw poederbehandelingsproject.
Classificaties van gevaarlijke gebieden hebben vaak betrekking op explosieve stoffen, dampen/gassen en vezels op basis van hoe vaak deze aanwezig zijn tijdens normale bedrijfscycli. Aan deze veiligheidsmaatregel moet de grootst mogelijke aandacht worden besteed. Ernstige verwondingen en ongevallen kunnen worden vermeden indien passende maatregelen worden genomen om het fabricageproces naar behoren te ontwerpen overeenkomstig de toepasselijke classificaties.
Sinds 1 juli 2003 zijn ATEX-normen van kracht voor de classificatie van gevaarlijke zones en locaties ter bescherming van werknemers. Een explosieve atmosfeer wordt gedefinieerd als "een mengsel van ontvlambare stoffen in de vorm van gas, damp, nevel of stof met lucht, onder atmosferische omstandigheden, waarin de verbranding zich na ontsteking uitbreidt tot het gehele niet verbrande mengsel". ATEX kan bestaan in een open omgeving (thermisch effect) of in een gesloten omgeving (overdrukeffect).
Naar gelang van de aard van de ontvlambare atmosfeer en de waarschijnlijkheid dat deze zich voordoet, zijn verschillende zones gedefinieerd, zowel voor stof (zone 20, 21, 22) als voor gas (zone 0, 1, 2).
Meer informatie over de classificatie van uw ATEX-zone.
Met meer dan 30 jaar ervaring kan Palamatic Process u helpen bij alle stappen van uw productieproces, of het nu gaat om het legen, vullen, overbrengen, mengen, doseren, zeven, ontstoffen, verkleinen, opslaan of automatiseren van uw poeders.
Neem vandaag nog contact op met een van onze poederexperts om uw project te analyseren en u te helpen uw productiedoelen te bereiken.