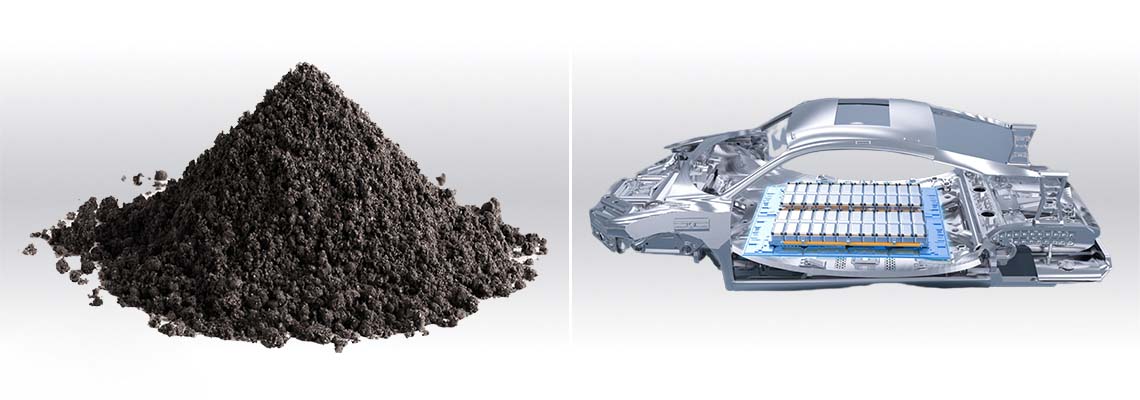
- 1. Explorer les minerais essentiels à la fabrication des batteries.
- 2. L'importance du concassage et du broyage dans la fabrication des batteries.
- 3. Optimiser la qualité des batteries grâce à la séparation magnétique.
- 4. Les étapes clés de purification des minerais : Flottation, Lixiviation, Précipitation, Filtration, Calcination.
- 5. La Réduction : L'étape déterminante pour obtenir des métaux purs de nickel et de cobalt.
- 6. La quête de la pureté ultime pour des batteries d'excellence par l'affinage électrolytique.
- 7. Palamatic Process Canada : Des batteries de qualité supérieure grâce à une purification minutieuse des minerais.
La fabrication des batteries est un domaine en constante évolution et la qualité des minerais utilisés joue un rôle crucial dans la performance et la durabilité de celles-ci. Du concassage initial à la séparation magnétique, en passant par des techniques telles que la flottation, la lixiviation, la précipitation, la filtration et l'affinage électrolytique, découvrez comment les minerais bruts sont transformés en matériaux de haute qualité.
1. Explorer les minerais essentiels à la fabrication des batteries.
Dans le cadre de la fabrication des batteries, il est essentiel de comprendre les types de minerais utilisés.
Les principaux minerais impliqués dans ce processus sont la spodumène pour le lithium, la pentlandite pour le nickel, la cobaltite pour le cobalt, et l' hématite pour le fer.
Chacun de ces minerais joue un rôle crucial dans la composition des batteries, et leur purification est une étape clé pour garantir des performances optimales et durables.
2. L'importance du concassage et du broyage dans la fabrication des batteries.
Le processus de fabrication des batteries implique une étape cruciale : le concassage et le broyage des minerais extraits.
Cette étape vise à réduire la taille des minerais, facilitant ainsi la séparation des métaux des autres éléments. Grâce à un concassage et un broyage efficaces, il devient possible d'obtenir des matériaux de qualité supérieure pour la production de batteries performantes et durables.
3. Optimiser la qualité des batteries grâce à la séparation magnétique
La séparation magnétique est une étape fondamentale du processus de fabrication des batteries. En effet, elle permet de séparer certains minerais, tels que la hématite, en utilisant un séparateur magnétique. Ce dispositif attire les particules magnétiques et les sépare des autres éléments présents dans le minerai. Grâce à la séparation magnétique, il est possible d'obtenir des matériaux de haute qualité, essentiels pour la production de batteries performantes et durables.
4. Les étapes clés de purification des minerais : Flottation, Lixiviation, Précipitation, Filtration, Calcination.
Dans le processus de purification des minerais utilisés pour la fabrication des batteries, plusieurs étapes clés sont mises en œuvre afin d’obtenir des métaux de haute qualité.
La flottation, premièrement, est un procédé qui utilise des bulles d'air pour séparer les particules de minerai, telles que la spodumène, la pentlandite, la cobaltite et l'hématite, des autres éléments. Les particules de minerai se fixent aux bulles d'air et remontent à la surface du liquide, permettant ainsi leur récupération.
Ensuite, la lixiviation est souvent utilisée pour les minerais de lithium, de nickel et de cobalt. Elle implique la dissolution des métaux dans une solution acide, permettant de les séparer des autres éléments présents dans le minerai.
Une fois les métaux dissous dans la solution, le procédé de précipitation intervient en ajoutant des réactifs chimiques spécifiques qui réagissent avec les métaux pour former des précipités solides.
Les précipités solides sont ensuite séparés du liquide par filtration où le solide récupéré correspond au métal purifié, tandis que le liquide restant est appelé "lessivage".
Enfin, pour certains métaux comme le lithium, une étape de calcination est nécessaire. Ce processus consiste à chauffer le métal purifié à des températures élevées afin d'éliminer les impuretés restantes et de le convertir en une forme plus stable, telle que l'oxyde de lithium.
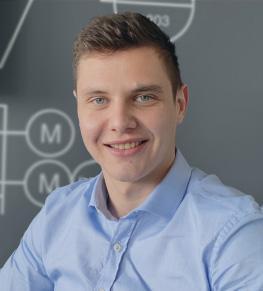
Vous avez un projet dans le secteur de la batterie ?
Je suis disponible pour échanger sur le sujet.
Loïc, expert poudre
5. La Réduction : L'étape déterminante pour obtenir des métaux purs de nickel et de cobalt.
Lors de cette étape cruciale de purification, l'objectif est de débarrasser les composés métalliques de leur oxygène pour obtenir des métaux purs d'une qualité exceptionnelle. La réduction est réalisée en exposant les composés métalliques à des conditions spécifiques, telles que des températures élevées et l'ajout de substances réductrices. Ces dernières agissent en capturant l'oxygène présent dans les composés, favorisant ainsi la formation de métaux purs. La réduction permet d'obtenir des matériaux hautement conducteurs et d'une pureté optimale, garantissant ainsi des performances supérieures dans la fabrication des batteries modernes et écoénergétiques.
6. La quête de la pureté ultime pour des batteries d'excellence par l'affinage électrolytique.
L'affinage électrolytique constitue une étape clé dans la purification des métaux, permettant d'obtenir des niveaux de pureté inégalés pour les applications exigeantes telles que la fabrication de batteries. Ce processus sophistiqué repose sur l'utilisation d'une solution électrolytique dans laquelle les métaux purifiés sont dissous. En appliquant un courant électrique précis, les ions métalliques migrent vers l'électrode opposée, formant ainsi des dépôts de métal pur. L'affinage électrolytique permet d'éliminer les impuretés résiduelles et de garantir une qualité supérieure des métaux utilisés dans les batteries, assurant ainsi des performances optimales et une durée de vie prolongée.
Le temps nécessaire pour la purification des minerais varie en fonction du type de minerai et de la méthode utilisée. Les machines utilisées dans le processus de purification comprennent des concasseurs, des broyeurs, des séparateurs magnétiques, des cellules de flottation, des filtres, des fours et des cellules électrolytiques.
7. Palamatic Process Canada : Des batteries de qualité supérieure grâce à une purification minutieuse des minerais.
En conclusion, la purification des minerais pour la fabrication des batteries est une étape essentielle pour garantir des performances optimales et durables. Les différentes techniques utilisées, telles que la séparation magnétique, la flottation, la lixiviation, la précipitation, la filtration, la calcination et l'affinage électrolytique, permettent d'obtenir des matériaux de haute qualité et de pureté exceptionnelle.
Les experts Palamatic Process maîtrisent les différentes étapes du processus et utilisent des équipements de pointe en mettant tout en œuvre pour répondre aux besoins spécifiques des clients. Si vous souhaitez en savoir plus, n'hésitez pas à contacter nos responsables solutions.