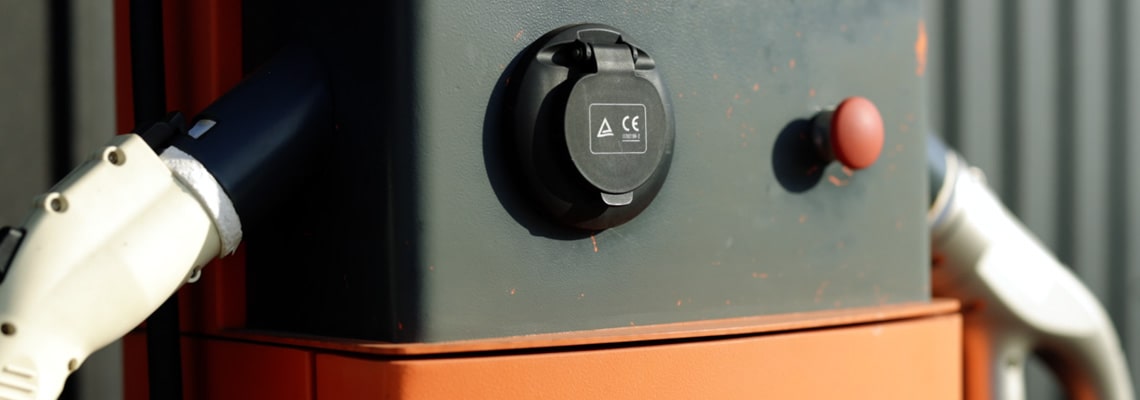
- 1. Nickel's essential properties for high-performance batteries
- 2. Lithium's unique properties: optimize your batteries' performance
- 3. Aluminum: an essential material for high-performance batteries
- 4. Maximize battery performance with the benefits of cobalt
- 5. Manganese: a vital ally for high-performance batteries
- 6. Palamatic Process: tailor-made support to maximize battery performance
In the battery manufacturing industry, nickel, lithium, aluminum, cobalt and manganese powders play an essential role. Understanding the key characteristics of these powders is crucial to ensuring high-quality batteries. In this article, we explore in detail the behavior, flow, density, castability, impact of moisture and particle size of each powder.
Whether you're a battery manufacturer or simply interested in the subject, discover the unique properties of these powders.
1. Nickel's essential properties for high-performance batteries
Nickel plays a crucial role in the manufacture of lithium-ion batteries. In powder form, it is widely used in the positive electrodes of batteries. Understanding the key characteristics of nickel is essential to optimize its handling and use in the battery manufacturing process.
As a major component of positive electrodes, nickel is often used in powder form.
- Behavior and flow: it's important to note that nickel powders have a natural tendency to agglomerate and form clumps, which can impede their smooth flow. To remedy this, proper grinding and sieving are required to improve their fluidity.
- Bulk Density: it is generally around 8.9 g/cm³, which gives this powder specific characteristics when used in batteries.
- Castability: it depends on their particle size, shape and particle size distribution. Appropriate treatment, such as sieving, can considerably improve their flowability.
- Humidity and its impact: nickel powders have the ability to absorb moisture from the air, which can lead to corrosion and affect battery performance. To preserve powder quality and guarantee battery performance, it is imperative to control humidity and store nickel powders in a dry environment.
- Particle size: nickel powders generally have a particle size of between 1 and 100 micrometers, making them suitable for various applications in the battery industry.
2. Lithium's unique properties: optimize your batteries' performance
Often used in the form of lithium oxide powder or lithium salts, lithium plays a crucial role in the composition of battery electrodes and electrolytes.
- Behavior and flow: lithium powders have a low density and viscosity, which greatly facilitates their flow. Nevertheless, it is important to note that these powders can form agglomerates when exposed to moisture, which can impair their performance.
- Bulk density: it is estimated at around 0.534 g/cm³, giving it specific properties when used in batteries.
- Castability: it is highly dependent on their particle size and particle size distribution. Appropriate treatment, such as sieving, can considerably improve their flowability, guaranteeing efficient handling during battery manufacturing.
- Humidity and its impact: it is a crucial factor to consider when handling and storing lithium powders. Lithium powders are sensitive to humidity and can react with water to form lithium hydroxide, which can lead to undesirable reactions and compromise battery quality. Therefore, it is essential to strictly control the surrounding humidity to prevent any negative impact.
- Particle size: lithium powders generally have a particle size of between 1 and 50 micrometers, making them remarkably adaptable to a variety of battery applications.
3. Aluminum: an essential material for high-performance batteries
Aluminium plays a crucial role in the manufacture of batteries thanks to its light density and conductivity. It is commonly used as a current collector for positive electrodes, guaranteeing optimum performance.
- Behavior and flow: aluminum powders are characterized by their excellent flowability. However, in the presence of moisture or contaminants, they can tend to agglomerate. To maintain optimum flow, we recommend appropriate treatment, such as sieving, to improve particle dispersion.
- Bulk Density: around 2.7 g/cm³, aluminum is characterized by its lightness, making it a preferred choice for reducing the overall weight of batteries.
- Castability: the flow characteristics of aluminum powders depend on factors such as particle size, shape and particle size distribution. Appropriate treatment, such as sieving, optimizes the flowability of aluminum powders, making them easier to use in battery manufacture.
- Humidity and its impact: it is crucial to control humidity when handling and storing aluminum powders. Aluminum powders can react to form aluminum hydroxide and hydrogen, which can have a negative impact on battery performance and durability. Proper handling and storage in a dry environment are therefore recommended to preserve battery quality.
- Particle size: aluminum powders are generally characterized by a particle size between 1 and 100 micrometers, making them suitable for many battery manufacturing applications.
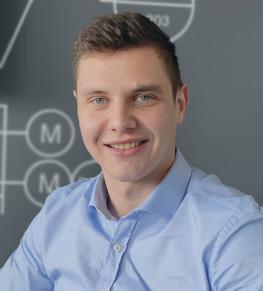
You work in the battery sector and you have a project?
I am available to advise you.
Loïc, powder expert
4. Maximize battery performance with the benefits of cobalt
Cobalt is commonly used in the form of cobalt oxide or cobalt salts, conferring essential electrochemical properties.
- Behavior and flow: cobalt powders have a propensity to agglomerate, which can impair their flowability. Proper grinding and sieving to improve dispersion of cobalt particles is crucial to ensure optimum flow.
- Bulk Density: around 8.9 g/cm³, cobalt is characterized by its robustness and superior electrical conductivity, contributing to optimal battery performance.
- Castability: the flow characteristics of cobalt powders depends on several factors, such as particle size, shape and particle size distribution. The proper processing techniques, such as precise control of these parameters and the use of sieving, can improve the flowability of cobalt powders and optimize their use in battery production.
- Humidity and its impact: cobalt powders have an affinity for absorbing moisture from the air, which can induce corrosion and impair battery performance. It is therefore essential to control humidity and store cobalt powders in a dry environment, thus preserving their integrity and battery reliability.
- Particle size: cobalt powders generally have a particle size between 1 and 100 micrometers, making them versatile for use in battery manufacturing processes.
5. Manganese: a vital ally for high-performance batteries
Manganese is frequently used in the form of manganese oxide or manganese salts, conferring crucial electrochemical properties.
- Behavior and flow: manganese powders generally flow well, but can agglomerate in the presence of moisture or contaminants. For optimal flow, appropriate treatment such as sieving is required to improve the dispersion of manganese particles.
- Bulk Density: with a density of around 7.3 g/cm³, manganese stands out for its robustness and ability to provide optimal electrical conductivity, contributing to superior battery performance.
- Castability: the flowability of manganese powders depends on various factors, such as particle size, shape and particle size distribution. Proper processing, such as accurate sieving, can improve the flowability of manganese powders, facilitating their use in battery manufacture.
- Humidity and its impact: manganese powders have the capacity to absorb moisture from the air, which can lead to corrosion and impair battery performance. It is therefore essential to strictly control humidity and store manganese powders in a dry environment, thus preserving their quality and battery reliability.
- Particle size: manganese powders generally have a particle size between 1 and 100 micrometers, offering versatility in battery manufacturing processes.
6. Palamatic Process: Tailor-made support to maximize battery performance
Each powder (nickel, lithium, aluminum, cobalt and manganese) has specific properties in terms of behavior, flow, density, castability, moisture and particle size, which must be taken into account during handling, storage and use in the battery manufacturing process.
If you are a battery manufacturer looking for tailor-made solutions to optimize your manufacturing processes, we strongly encourage you to contact our solutions managers. Thanks to their in-depth expertise in the field of battery powders, they will be able to guide you in improving the efficiency and performance of your batteries.