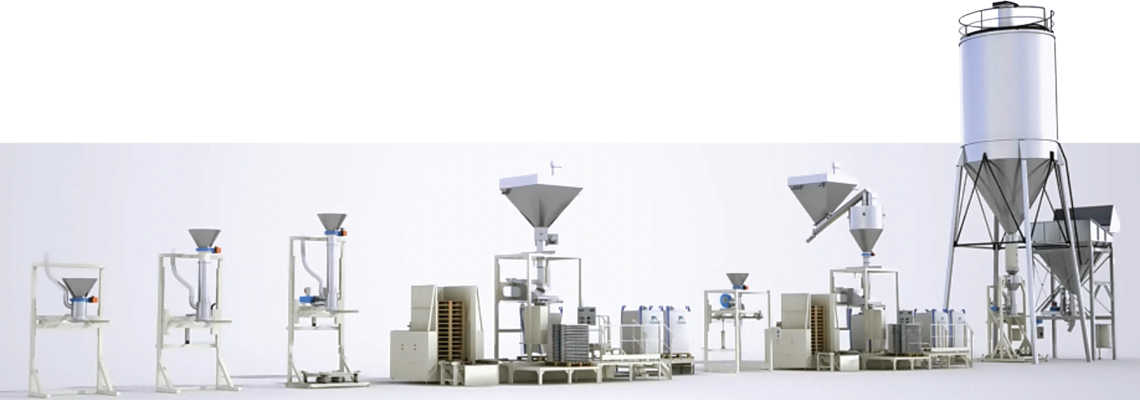
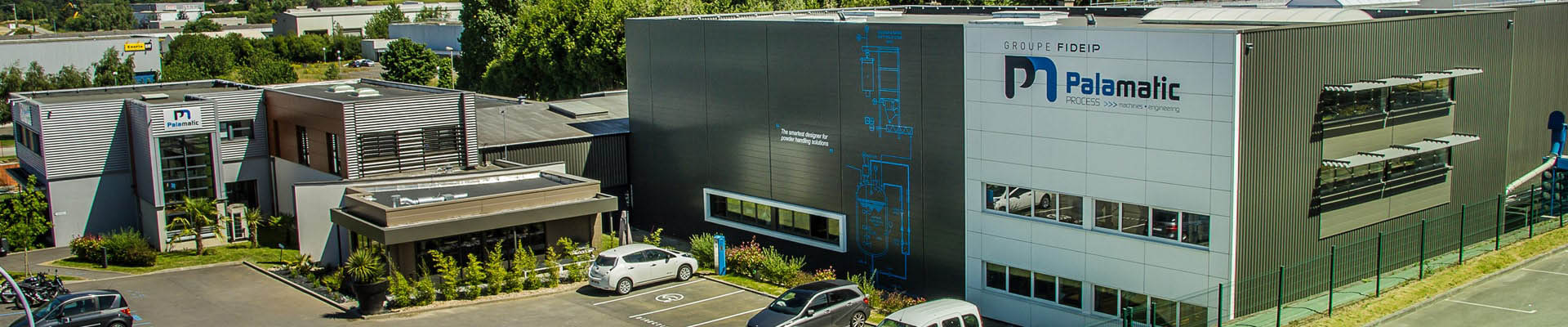
Palamatic Process has developed a range of bulk bag filling stations. The FlowMatic® range enables efficient handling of your powders.
Discover our turnkey solutions for bulk bag conditioning.
Bulk bag filling machines are designed to provide unmatched precision and reliability.
By choosing Palamatic Process bulk bag filling and handling solutions, you benefit from advanced technologies and customized solutions to optimize your production and ensure the quality of your products.
The FlowMatic® 01 bulk bag filling station allows for the conditioning of your bulk bag, with a throughput of 10-20 bulk bags/hour. This bulk bag filler ensures total containment of your powders.
The FlowMatic® 02 provides ergonomic handling of your bulk bags.
The FlowMatic® 02 Ashflow is designed for reconditioning fly ash at thermal power plant sites.
The FlowMatic® 03 bulk bag filling station integrates gross weighing for precise dosing and adapts to the varying characteristics of powders.
The FlowMatic® 04 bulk bag filling station enables high throughput (20-40 bulk bags/hour) and offers operators ergonomic handling for powder processing.
The FlowMatic® 05 filling station offers two bulk bag placement options: the lifting table meets the hygienic requirements of industries, while the hydraulic jack also allows for hygienic powder conditioning with the use of an inflatable seal.
The FlowMatic® 06 provides industries with high throughput and ergonomic workstations, capable of filling 30-60 bulk bags per hour.
The FlowMatic® 07 is a mobile bulk bag handling station, ideal for connecting under truck loading spouts.
The FlowMatic® 08 offers telescopic loading for bulk and powdered products, equipped with an integrated commercial weighing system.
The FlowMatic® 09 automatic bulk bag filling station provides high-speed net weighing for single-loop bulk bags.
The FlowMatic® 10 bulk bag filling station is a hygienic solution for clean rooms, part of our Easy Clean range.
Palamatic Process offers FIBC bulk bag filling solutions ranging from individual equipment to fully automated complete lines.
Automatic evacuation of bulk bags to the storage area is managed with roller conveyors.
Our bulk bag handling solutions are tailored for the food industry, chemicals, fine chemicals, construction, water and smoke treatment, and the nuclear sector.
Looking to fill your bulk bag? Check out our white paper to help you choose: How to select your bulk bag filling machine?
Examples of powders handled include: starch, maltodextrin, dextrose, sugar, salt, spices, flour, alumina, carbonate, sulfate, titanium dioxide, soy, starch, corn starch, wheat starch, TiO2, calcium carbonate, CaCO3, sulfate, animal feed flour, iron oxide and hydroxide, milk powder, re-fattened milk powder, activated carbon, carbon black, dye, pigment...
Our sales engineers can also conduct studies for industrial efficiency improvement and debottlenecking of your site.
Bulk bags, also known as intermediate flexible containers (FIBC), are versatile and robust packaging solutions, suitable for a wide range of products (bulk, food, chemicals, construction materials, etc.).
Bulk bags are particularly appreciated for their ability to transport large quantities of materials efficiently and securely. They are also easy to handle thanks to their lifting straps, making them an ideal solution for storing and transporting bulk products. In summary, bulk bags are a versatile and practical option for a multitude of products in various industrial sectors.
To choose a bulk bag filling station, it is important to consider the type of product to be packaged (powders, granules, liquids or others). The physical properties of the product, such as density, fluidity and sensitivity to humidity or heat are decisive.
The capacity and throughput of the filling station must correspond to the volumes of bulk bags used and production requirements. Filling accuracy is essential to avoid overloading or underloading. Integrated weighing systems ensure increased precision.
Automation enables increased efficiency by reducing filling time and downtime. Automated stations fill bulk bags faster than manual systems. Automation also contributes to cost reduction. By reducing the need for labor, businesses can realize cost savings. Increased accuracy and reduced human error minimize non-conforming batches, thereby increasing production yield.