Description
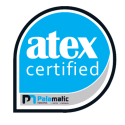
Bulk bag filling - Containment, densification and bulk weighing
The filling station 's structure is easily adjustable to condition big bags of various heights. The tensioning cylinder, the fan and the vibrating table give an optimal shape to the big bag. The vibrating table , on the other hand, ensures the deaeration of low-density products.
The FlowMatic® 03 filling system has a filling rate ranging from 10 to 20 big bags per hour.
-
Automation3
-
Rate3
-
Overall dimensions5
Operating mode :
1. Installation of the big bag on the packaging station
2. The big bag spout is fixed to the filling head by means of an inflatable seal which ensures dust containment during operation.
3. Tensioning of the big bag with the pneumatic cylinder
4. The pre-forming fan inflates and shapes the big bag (FIBC)
5. Inflating fan is deactivated and another fan used for reverse jet filtration of the big bag is switched on
6. Big bag filling starts with high flow rate capability
7. Big bag comes to rest on its pallet and the vibrating table ensures stability of the big bag during filling and handling
8. Vibrating table further ensures densification of material with intermittent operation throughout the filling process
9. Load cells allow for weight management via a low speed switch to adjust the flow rate for final dosing
10. End of the filling process, the forks lower and the seal deflates. The big bag is ready to be unloaded
11. Removal of the big bag can commence by forklift, pallet truck or by the bag straps
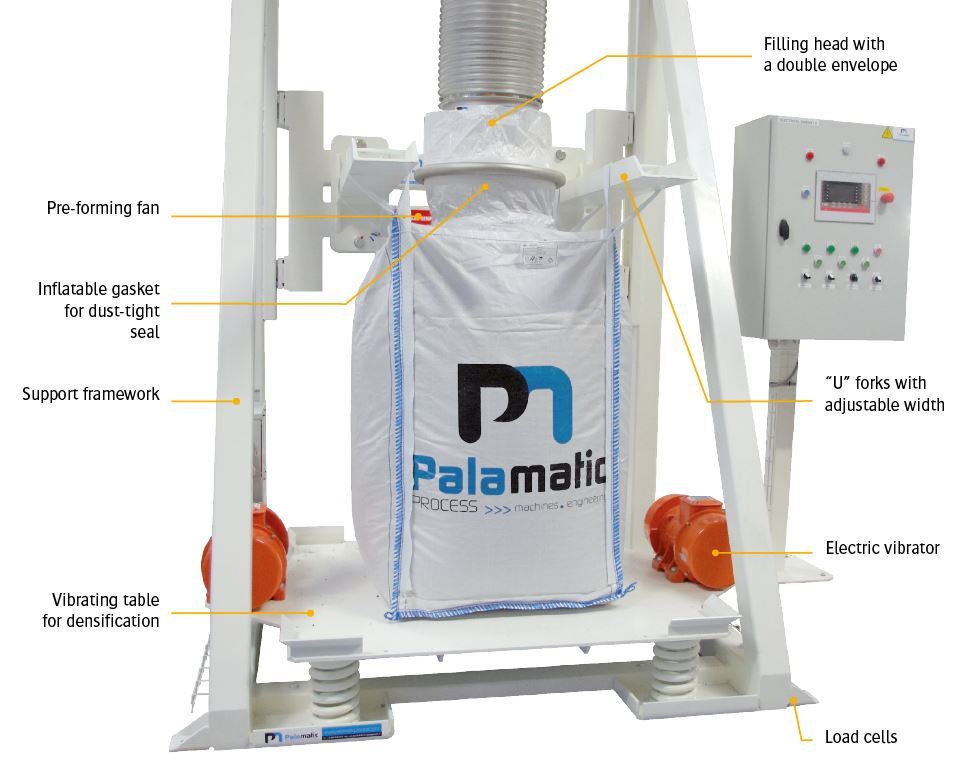
The FlowMatic® 03 big bag filling station incorporates all the necessary options for an efficient filling and dust containment operation. These features include the inflatable containment seal, big bag hanging deck with pneumatic cylinder height adjustment, big bag shaping fan, big bag weighing system (dosing), optional commercial weighing and vibrating densification table. The adjustable structure enables the conditioning of big bags of various heights and dimensions. The filling head is designed with a double casing to relieve back pressure during filling as well as containment of dust emissions into the atmosphere. The tension cylinder and the fan allow the big bag to be pre-formed for optimal filling.Finally, the vibrating table also ensures that the handling of the packed big bag is safe by avoiding the risk of tipping.
The FlowMatic®03 big bag filling station has a filling rate ranging from 10 to 20 big bags per hour.
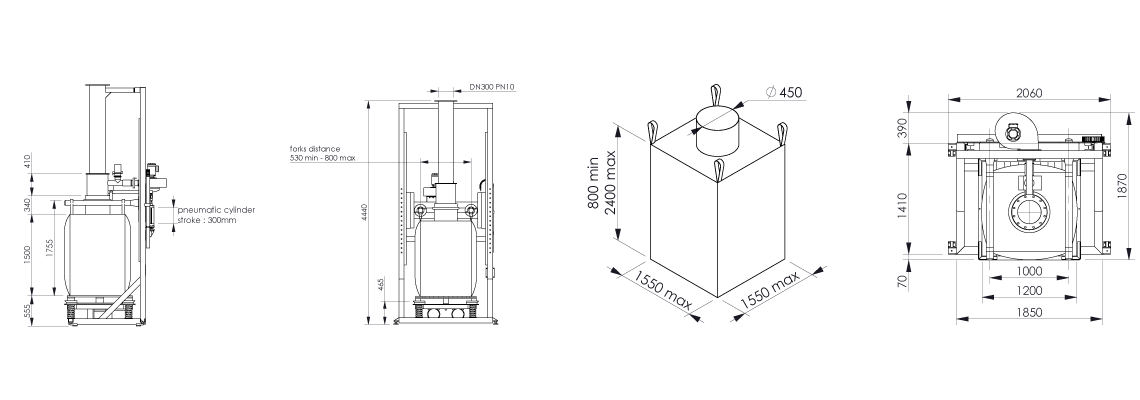
Equipment advantages
- Dosing and weighing for commercial transactions of your products
- Fan and tension cylinder to ensure the shaping of the big bag and of the internal pocket
- Vibrating table to ensure the densification of the product and to obtain a stable big bag
- U-shaped forks to remove the big bag by the handles without a pallet
Media
View our equipment in videos
Bulk bag filling unit - FlowMatic®03
Big bag filling system - Flowmatic 03
Containment, densification and gross weighing
The FlowMatic® 03 filling station is easily adjustable to pack big bags of different heights. The tension cylinder, fan and vibrating table ensure that the big bag is optimally shaped. The vibrating table ensures the deaeration of low-density bulk materials.
Bulk bag filling range
View our equipment in photos
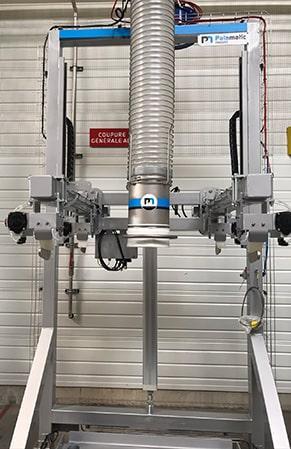
FlowMatic® 03 filling bulk bag - Palamatic Process
Flowmatic 03® is a bulk bag filling solution suitable for a wide variety of business sectors.
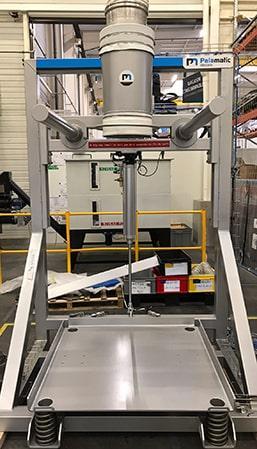
Big bag filling Flowmatic® 03
Complete process line for the preparation and management of premixes.
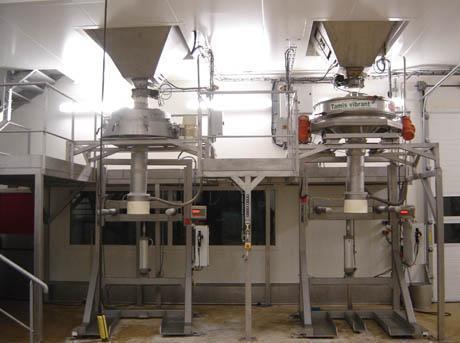
Super sack filling Flowmatic 03
Pictured: A turnkey process line integrating super sack filling stations for the preparation and management of premixed recipes.
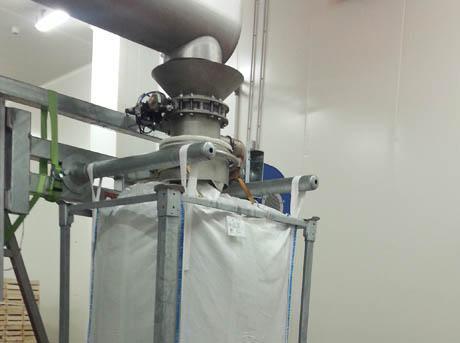
Big bag filling station under screw conveyor
The filling station is fitted with a weighing system to enable commercial transactions of the processed powders.
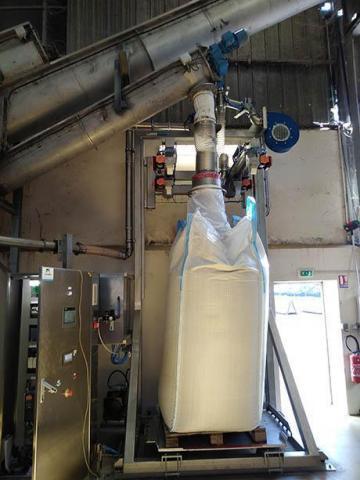
Big bag filling station under screw conveyor
The filling station is fitted with a weighing system to enable commercial transactions of the processed powders.
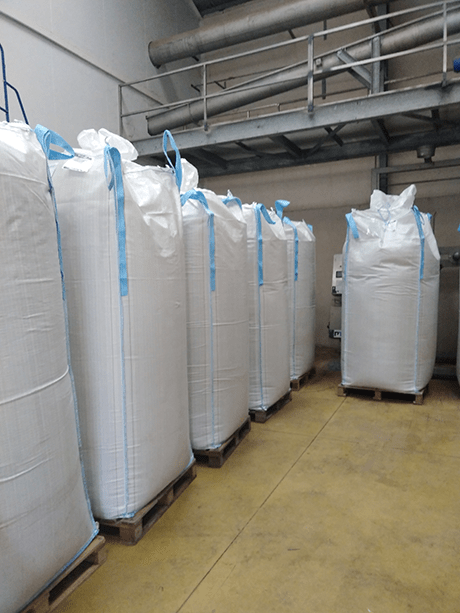
Bulk bag filling on packaging line
The super sack filler has an integrated mechanical roller conveyor that automates and increases the production rate of the packaging line.
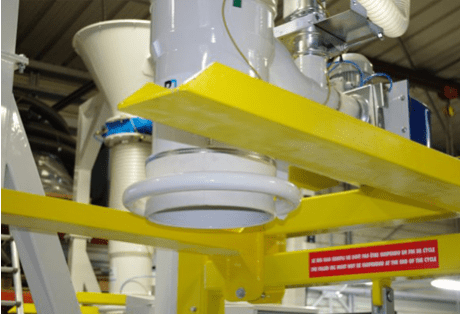
Inflatable seal on bulk bag filling station
The inflatable seal provides a dust tight connection to the spout inlet on the bulk bag. The filling head of the bulk bag packing structure is designed as a double jacketed tube allowing the material to air volume balancing as well as the capture and filtration of dust particules.
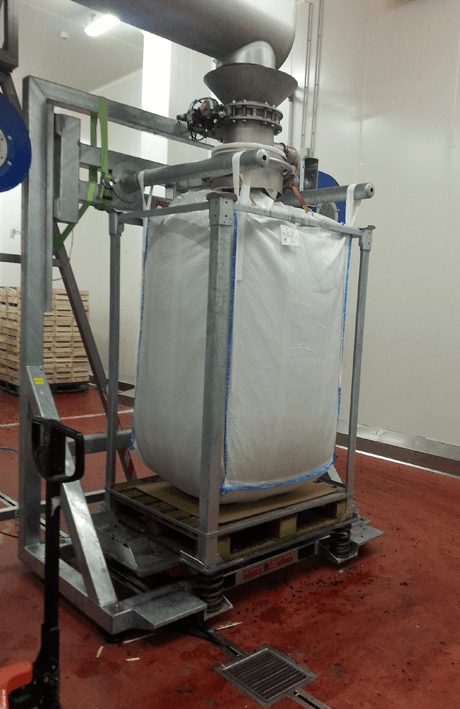
Bulk bag loading for a powder handling application
The vibrating table provides material densification for optimal filling and stability of the bulk bag.
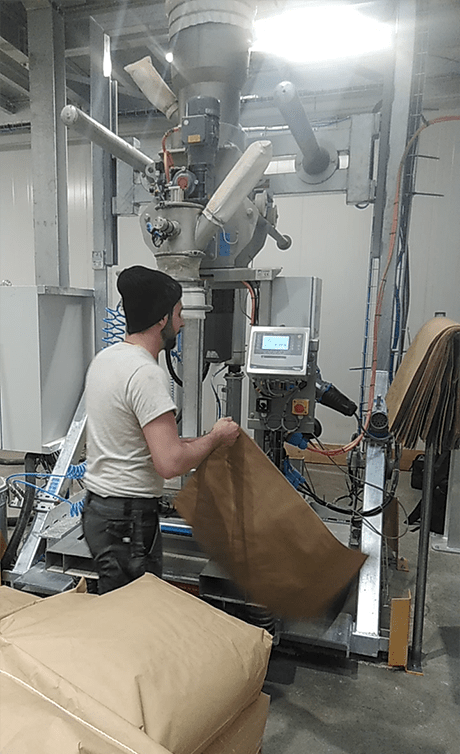
Dual bulk bag and sack filling station
Installed at the outlet of a mixer, the material filling station combines the packing of super sacks and open mouth sacks.
The bulk bags are filled with a FlowMatic 03 station equipped with: inflatable seal for a dust tight connection, pneumatic tension cylinder and a vibrating table for the densification of powders and granules during the packing process.
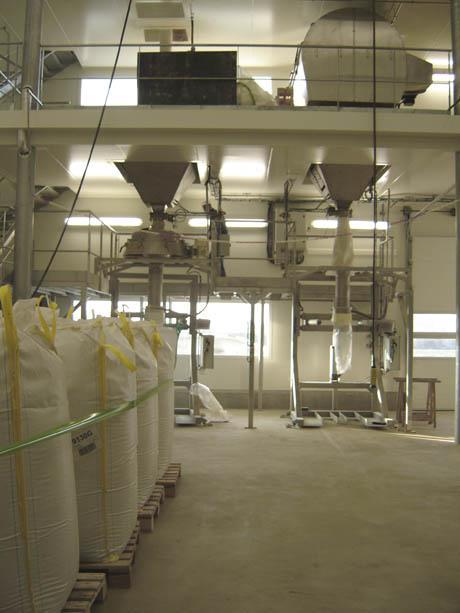
Animal feed industry project for bulk bag filling operation
A complete industrial production line for the manufacture of additives in the animal nutrition industry.
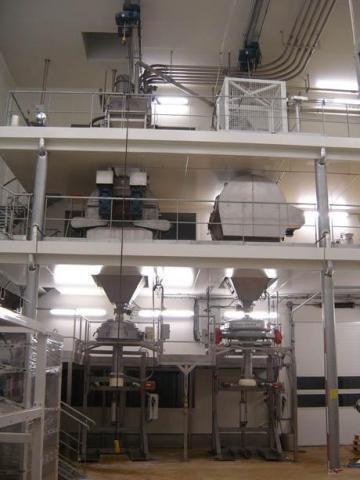
Animal feed application bulk bag filling
Process for the manufacture of additives for the animal nutrition sector, dog and cat food.
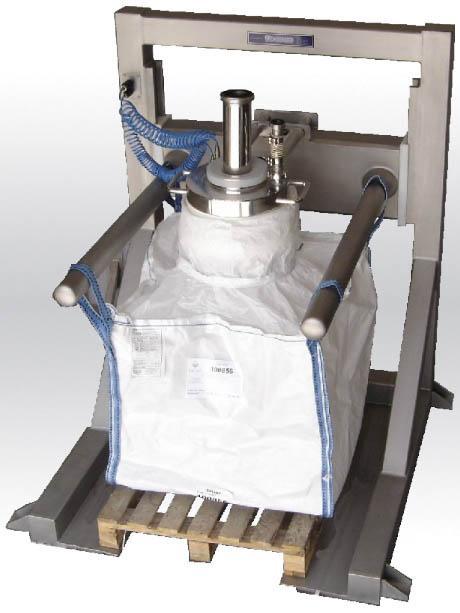
Drum and bulk bag filling station
Animal flour packing station on an industrial production line.
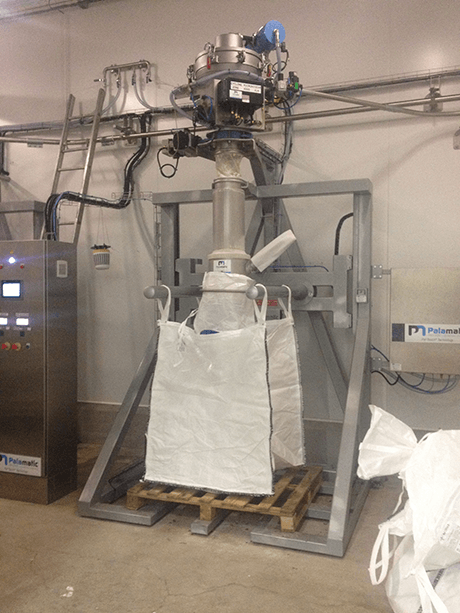
Pneumatic conveying on a big bag filling station
Integrated pneumatic conveying on a big bag filling station. It is used to convey the bulk materials or powders without deterioration.
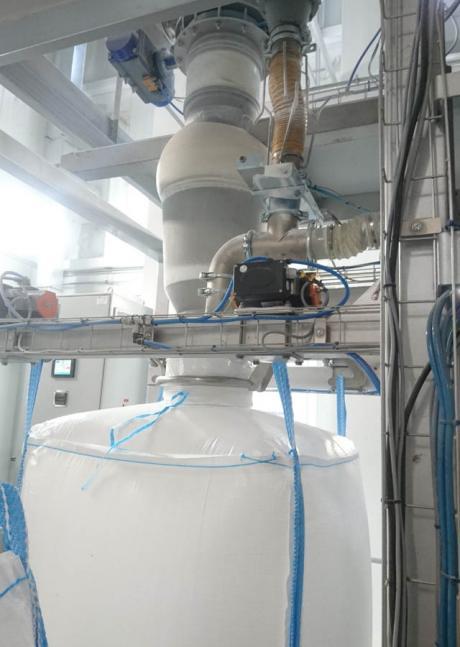
Powder handling bulk bag filler
FlowMatic® 03 filling line of barite in big bags.
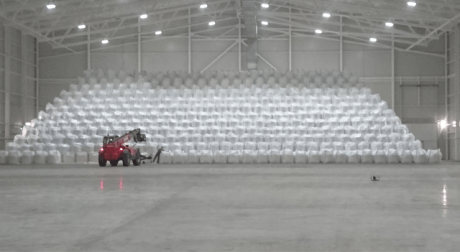
Sugar handling
Powdered sugar packaging line in big bag.
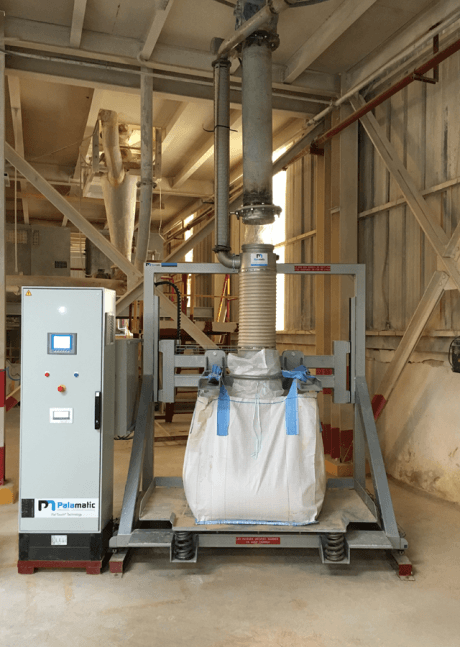
Bulk bag filling for the building and minerals industry
The repacking of prepared powders from a storage silo for the production of plaster.
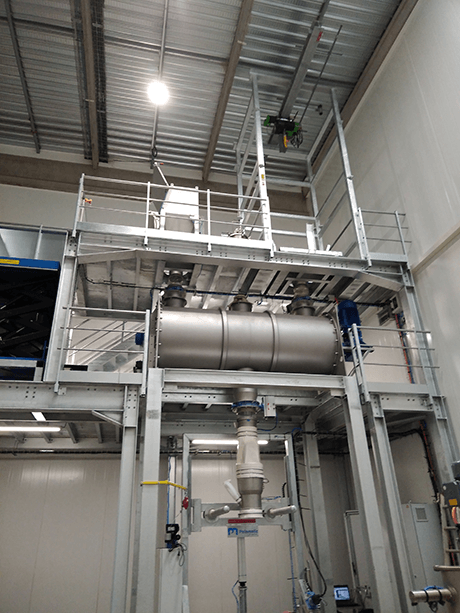
Plow mixer feeding a bulk bag filling station
This three tiered turnkey installation involves a bulk bag unloader and bag dump station, which both fill a plow mixer. Once the mixing is finished the powder blend discharges into a bulk bag filling station.
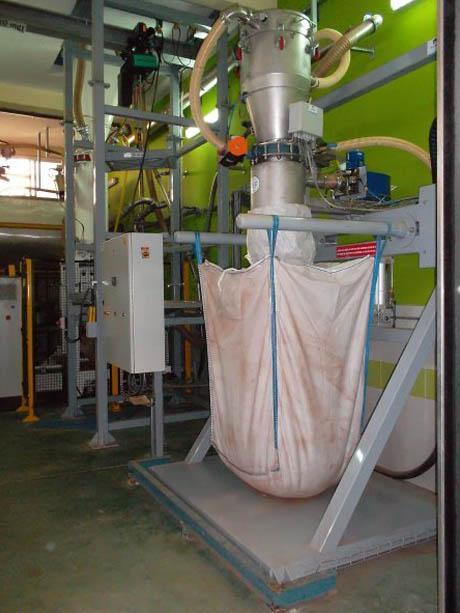
Dust-tight bulk bag charger
Spice preparation line for the food industry.
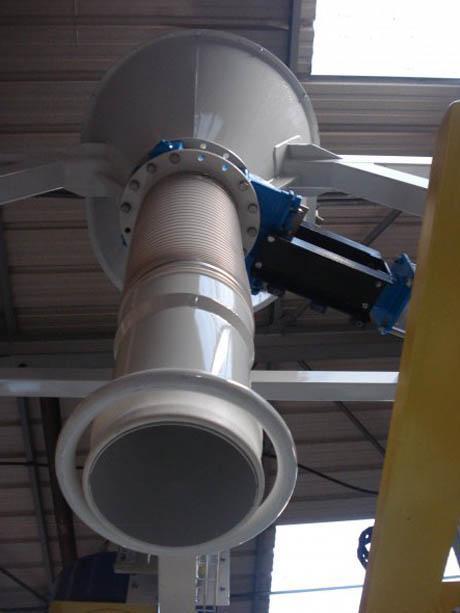
Filling head
Double jacket big bag filling head with inflatable seal and clamping ring.
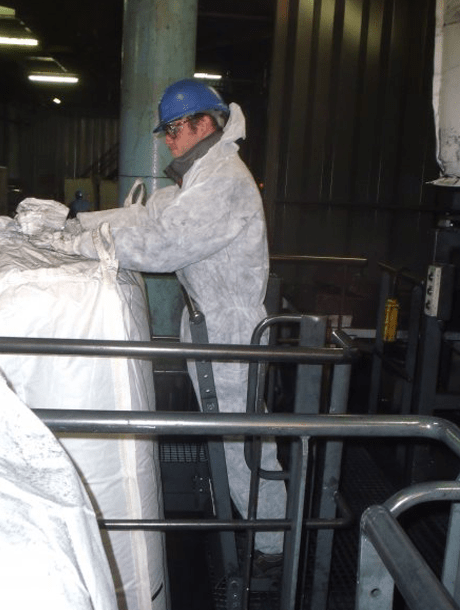
Ergonomic design for access to the spout inlet of the bulk bag
An operator access platform provides safe and ergonomic access to the big bag filling spout.
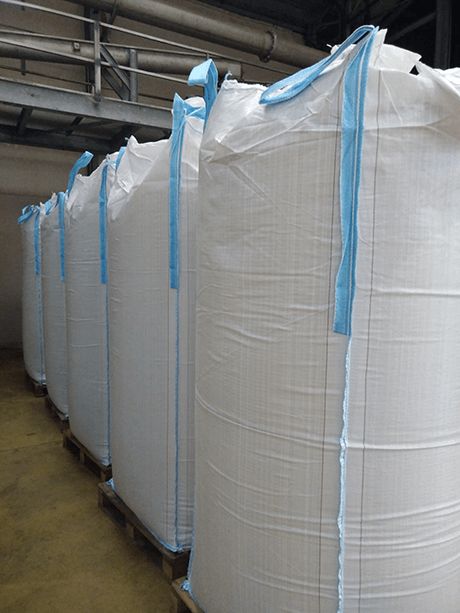
Bulk bag in manufacturing production line
Industrial production line with filling station for big bags of sugar.
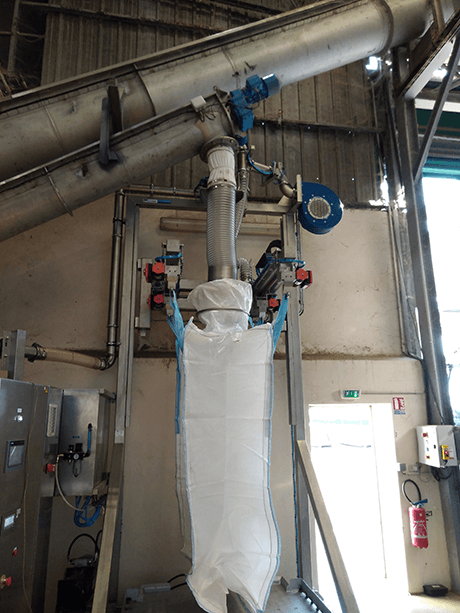
Screw conveyor feeding a bulk bag filling station
A process system involving the fine milling, transfer and bulk bag filling of seaweed powder for the food industry.
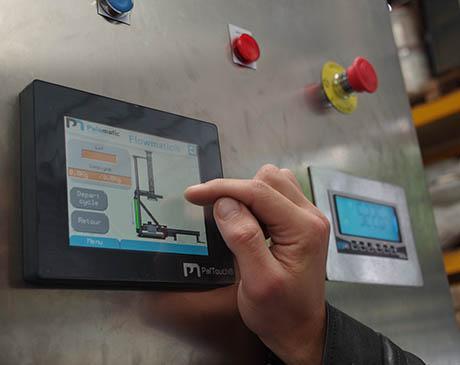
Pal'Touch control cabinet for bulk bag filling application
Pal'Touch industrial automation: The control cabinet is integrated into our Flowmatic 03 bulk bag filling station.
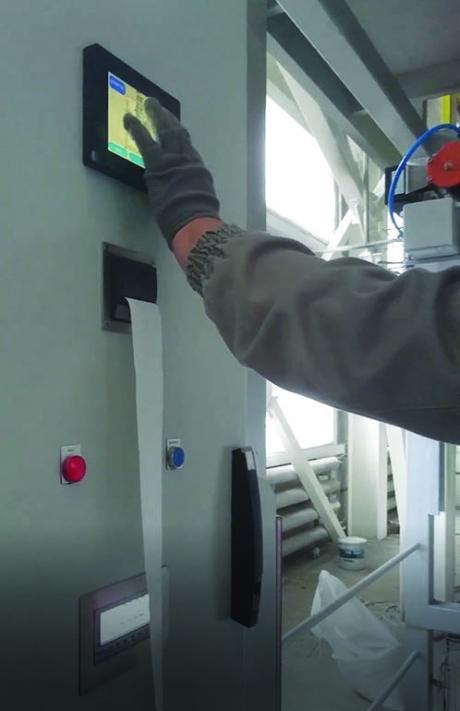
Palamatic Process industrial automation
A Pal'Touch control panel automatically manages the dosing and weighing systems integrated into the bulk bag filling station. This features make it possible to conduct commercial transactions of the packed bulk solids.
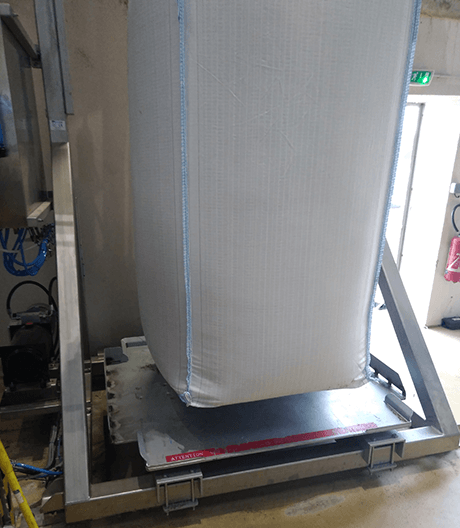
Suspended big bag on filling station
Bulk solids mixing and conditioning line.
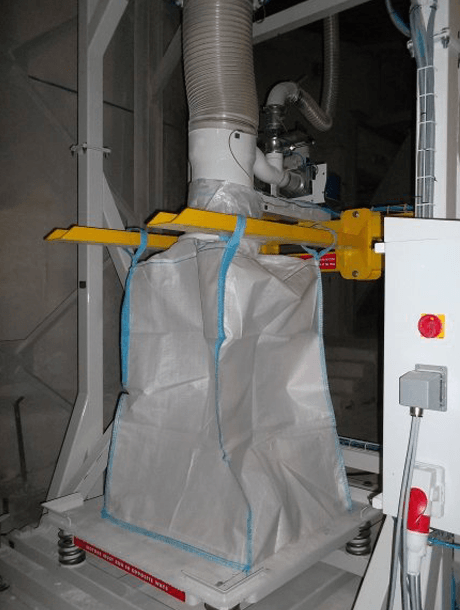
Building industry bulk bag filling application
The entire structure is adjustable to handle big bags of different heights.
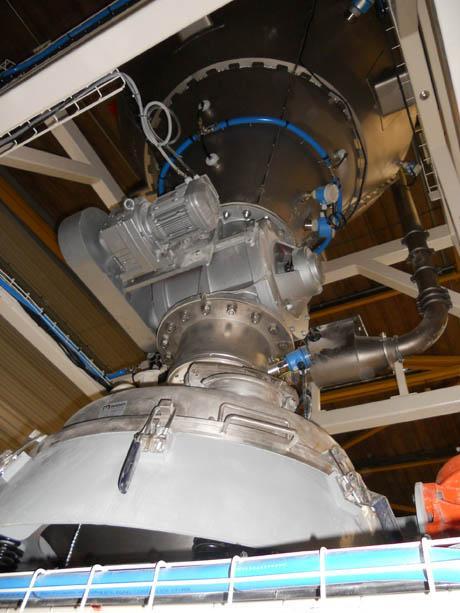
Feed hopper on bulk bag filling station
The bulk bag filling station is fed upstream by feed hopper and vibrating screener.
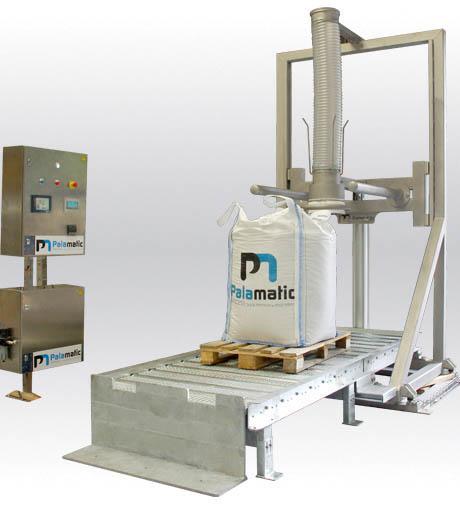
Big bag filler FlowMatic®03
This big bag filling system is fitted with a roller conveyor.
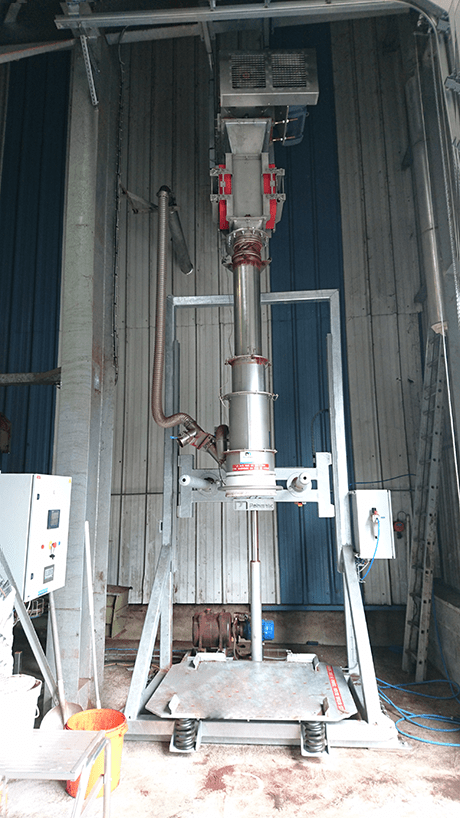
FIBC filling station
Integrated on the back of the FIBC bulk solids loading station is a pneumatic jack that helps adjust the tension of the FIBC during the filling cycle.
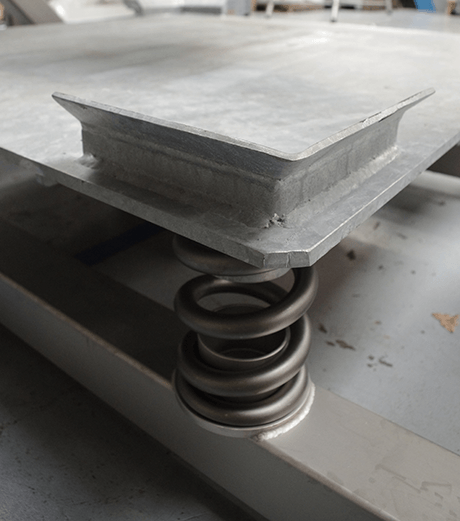
Vibratory table
The vibrating table integrated into the filling station for big bags with calcium carbonate enable the raw bulk material to be deaerated and ensures the stability of the big bag.
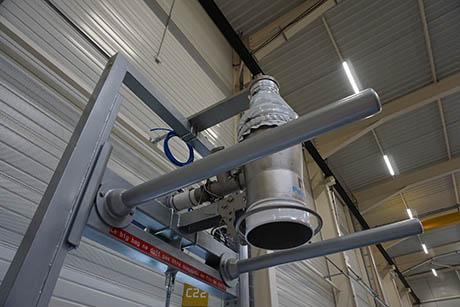
Filling head
Big bag filling head on mobile salt conditioning station.
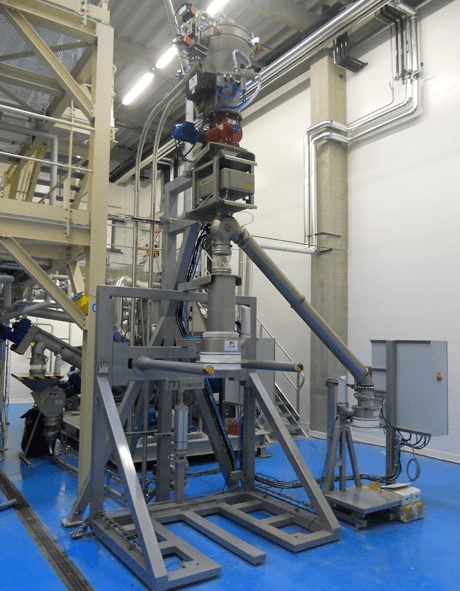
Big bag filler on industrial production line
Integrated equipment:
- FlowMatic® 03 - Big bag filling station
- Clamping ring
- PalSack® - Sack filling station
- Drop through rotary airlock valve
- Magnetic detector
- Industrial automation
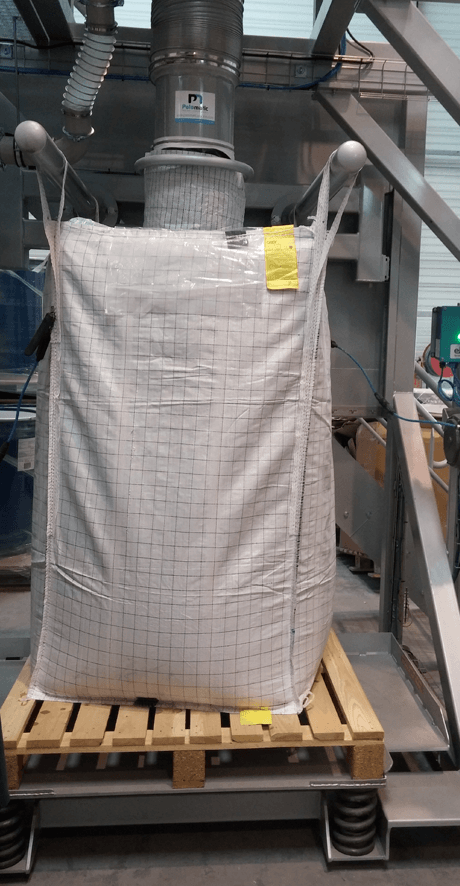
Industrial big bag filling station
Big bags are packed with ingredients for the food industry.
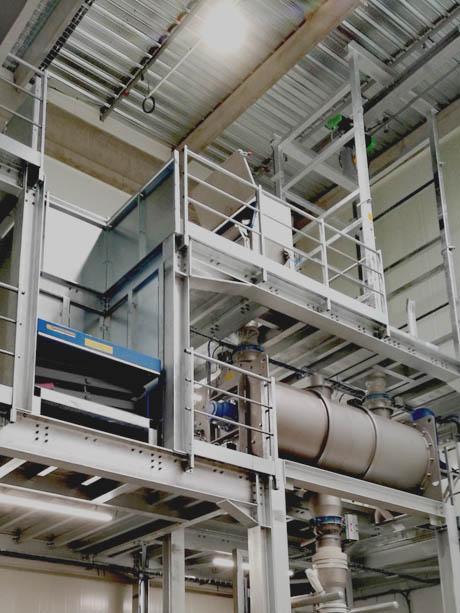
Big bag filler in the food feed industry
The big bag filling station is positioned on handling wheels.
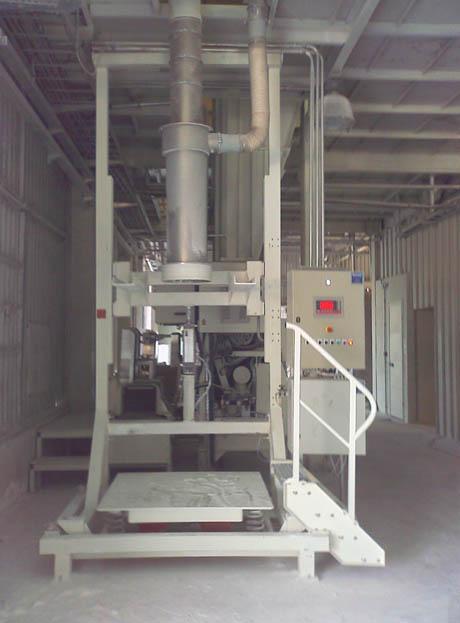
FlowMatic® 03 - Minerals and building industry
The big bag is filled with barite from quarries.
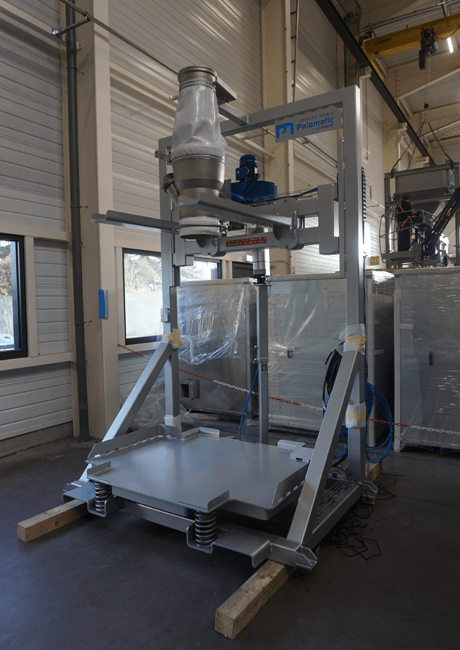
Big bag filler for fishmeal powder
Dosing, mixing and packing line for animal feed in big bags.
Features
Technical specification
Rate | 10 to 20 big bags/h. |
---|---|
Capacity | 2 ton/big bag |
Manufacturing materials | Mild steel, 304L stainless steel |
Installed power | 3 kW |
Compressed air consumption | 0.9 Nm³/h. |
Dust removal rate | 300 m³/h. |
Finishing touches: RAL 9006, micro-blasted, electropolishing
Average power consumption: 0.2kW
Operating pressure: 6 bar
Digital input: 6
Digital output: 6
Accuracy of the weighing chain: ± 500 grams
Maximum size of big bags: 1,550 (l ) x 1,550 (L) x 2,400 (H) mm
U-shaped forks: allow the removal of the big bag by the handles (optional)
Equipment integrated into the FLOWMATIC 03 model:
- Round hooking forks of the big bag: offers easier sliding of the big bag handles.
- U-shaped forks for attaching the big bag handles: allow the big bag to be evacuated directly through the handles using a forklift truck (no pallet is used).
- Support structure: the structure is manually adjustable in height to fit all types of big bags- Width adjustment: the spacing of the hooking forks is adjustable in width to optimize the filling operation but provides a greater stability of the flexible container on its pallet.
- Inflatable seal: the inflatable seal ensures a tight connection between the filling head and the big bag during the filling operation.
- Filling head: the filling head is designed in a double casing for volume balancing. The charged air is evacuated through the degassing line which can be connected to the dedusting network.
- Tension cylinder: the pneumatic cylinder is located on the deck of the suspension forks. It allows to bring the system for attaching the handles of the big bag to ergonomic height, to adjust to the different big bag heights and to give an optimal shape to the big bag thanks to the permanent tensioning during the whole conditioning phase. The big bag is perfectly filled without any risk of pocketing and can be handled safely, without any risk of it tipping over.
- Pre-inflation fan: implanted on the station, the fan ensures the shaping of the big bag equipped with an internal bag to facilitate its filling. A by-pass valve makes it possible to degas the fines that are captured by the double-cased tube during the conditioning phase.
Options
Case studies
CASE STUDIES WITH THIS EQUIPMENT
Paint formulation
Processed powder: paint powder (polyester resin + fillers + additives + pigments) - Paint formulation - A manual container emptying station feeds a big bag filling system. The container unloading...Chemical
Animal flour loading
Powders processed: feather flour, animal flour - Animal flour loading - Palamatic Process has set up a bulk bag packaging station with vibration and automatic releaseof the bulk bag.Food and Animal Feed
Mineral packing
Processed powder: barite - Mineral conditioning - FlowMatic® 03: sealed filling of big bags with barite with automatic weighing.Minerals and building
Process for food supplements
Processed products: Vitamin A, Vitamin E, Metasmart dry - Process for food supplements - Big Bag filling station with integrated weighing and vibrating densification table.Food and Animal Feed
Premix compound packing
Treated powder: premix compound - Premix compound packing - Our customer, a specialist in PVC compounds and polymer composite materials, required the packing of its finished product - polymer...Chemical
Packaging process optimization
Processed powder : fish meal - Big bags packaging - Output of 50 big bags/hFood and Animal Feed
Filling bulk bags with fly ash
Processed powder: fly ash - Filling of big bags for building materials via gravity discharge from a silo.Minerals and building
Bulk bag filling equipment for semi-automatic process in the fish food industry
Processed powders: meat meal and bone meal - Semi-automatic bulk bag filling stations - The installation consists in loading big bags under mixers without emitting dust.Food and Animal Feed
Reconditioning of nickel hydroxide in battery manufacture
Processed powders: nickel hydroxide, nickel sulphate and sodium hydroxide Recovery of nickel hydroxide cake for reconditioning in super sacksEnergy
Receive your quotation in 3 clicks!