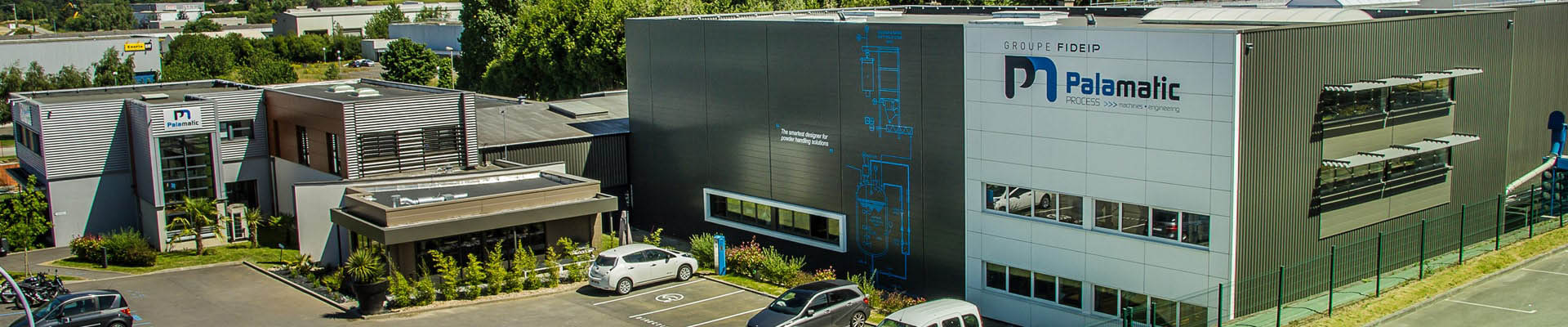
Case studies - Batteries and componants
Nos applications chez nos clients
Automated Bulk Bag Unloading and Conveying System for Lithium
Powders handled: Lithium Carbonate (Li₂CO₃), Iron Oxide (Fe₃O₄), Lithium
Optimizing Automated Bulk Bag Unloading for Lithium Powders
Energy
Optimizing Sensitive Powder Processing with a Custom Solution
Powders Handled: Lithium, NMC compounds (Nickel, Manganese, Cobalt), and anode/cathode materials (graphite, LiFePO4), requiring secure handling due to their toxicity, hygroscopic nature, and...
Chemical
Automating bulk bag decompaction
Powders treated: hygroscopic powders such as metal sulphates
Optimizing the handling and unloading of super bags to improve safety and production
Energy
Complete line for breaking filter cake and bagging in super sacks
Processed powders: nickel hydroxide, nickel sulphate and sodium hydroxide
Recovery of nickel hydroxide cake for reconditioning in super sacks
Energy
Complete automated lines for decompacting and emptying bulk bags
Processed powders: lithium, cadmium and oxides
Decompaction and emptying of bulk bags for battery manufacture
Energy
Sack filling system for the manufacture of batteries
Energy
Turnkey line for the manufacture of battery paste
Energy
Big bag emptying and dosing for the manufacture of copper collectors for electric batteries
Energy
Automated deconditioning of big bags to increase nickel hydroxide production
Energy
Disposal, dosing and pulping system
Energy
Automation of a super bag unloading system
Energy
Discharging station of big bags of cadmium in very high containment
Chemical
Handling big bags of toxic material for a battery manufacturer
Energy
Today the world of batteries is a rapidly evolving industry. For more than 20 years Palamatic Process has been providing this industry with material handling equipment for cadium and silicon, in the creation of winding film and manufacture of batteries. Our experience also lends itself in the knowledgeable design and implementation of screw feeders and dosing equipment for extruders. Furthermore, Palamatic Process is involved in the creation of premixes with the adjustment of product characteristics such as humidity, temperature and granulometry.
The Palamatic Process knowledge in powder management is further represented in the handling of "toxic" products often used in the manufacture of batteries, cells, supercapacitors, etc. Containment and dust removal in bag-in-bag-out are the technologies implemented for the realization of these battery projects.