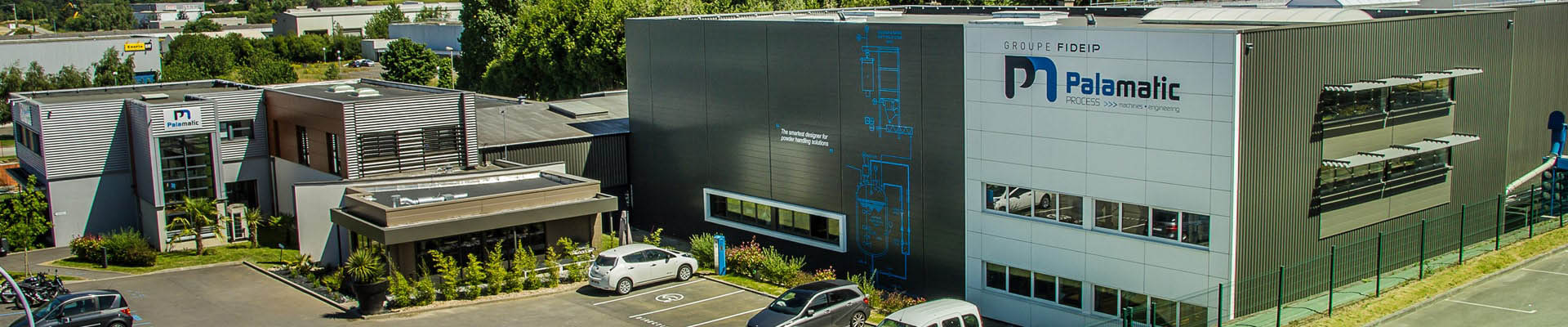
Case studies - Cement and plastering
Palamatic Process has proven expertise in the treatment, extraction, crushing, grinding, dosing, homogenization or conveying of bulk materials, such as quicklime, silica, alumina and iron oxides. Also, the use of admixtures in the manufacture of concrete makes it possible to attribute certain properties to it, particularly for high-performance concretes (technological innovation).
Nos applications chez nos clients
Optimizing Sensitive Powder Processing with a Custom Solution
Powders Handled: Lithium, NMC compounds (Nickel, Manganese, Cobalt), and anode/cathode materials (graphite, LiFePO4), requiring secure handling due to their toxicity, hygroscopic nature, and...
Chemical
Decompacting cement big bags
Minerals and building
Semi-automatic bulk bag unloading
Minerals and building
Automated Bulk Bag Unloading and Conveying
Minerals and building
Double deconditioning station and pneumatic dense phase cement transfer
Minerals and building
Process for the manufacture of plasterboard
Minerals and building
Big bag filling station Flowmatic 07
Minerals and building
Discharge of big bags of plaster for re-packaging into containers
Minerals and building
Automatic opening and emptying of bags of plaster, cement and starch
Minerals and building
Discharge of big bags of cement for truck loading
Minerals and building
The experience of Palamatic Process engineers and the powerful software packages used make it possible to design and implement these specific production processes. Palamatic Process offers a complete service from the definition of the requirement to the commissioning.
The steps of the process for the manufacture of cement:
- Raw material extraction
- Grinding and storage of raw materials
- Cooking of raw materials
- Storage, crushing and screening
- Cement conditioning and transport
The pneumatic conveying of cement with specific bulk handling equipment allows you to achieve a long service life of the installations by minimizing maintenance as much as possible.