Description
FlowMatic® 06 Bulk bag filling - 100% Automation for Net Weighing at High Rate Capacities
The complete system solution for automatic conditioning of bulk bags in gross weighing operations. This station is ideal for continuous filling operations at high rates (30-60 bulk bags/hour) and significantly minimizing direct intervention of operators.
The FlowMatic® 06 automatic bulk bag filling station is equipped with all the necessary options for fast packaging of big bags: a pre-dosing weigh hopper, inflatable containment seal, automatic handle release system, a height adjustable deck via pneumatic cylinder, big bag pre-forming fan, commercial weighing machine, densification vibrating table, pallet unstacker and a big bag motorized conveyor.
-
Automation5
-
Rate5
-
Overall dimensions4
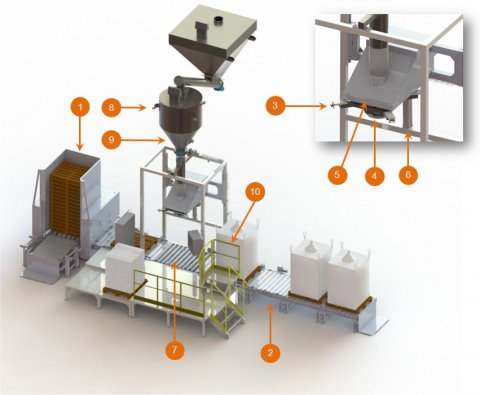
1 - Pallet unstacker
2 - Motorized conveyors
3 - Automatic release
4 - Inflatable seal
5 - Head
6 - Tension cylinder
7 - Vibrating table
8 - Load cells
9 - Pre-dosing hopper
10 - Platform
Rates from 30 to 60 bulk bags/hr.
The FlowMatic®06 bulk bag filling system model represents the complete solution for automatic gross weighing systems for big bags, FIBCs, super sacks, jumbo bags, bulk bags (dosing/packaging/conveying). This model is designed for continuous use at high rates while integrating automatic operation features to minimizing the need for human intervention.
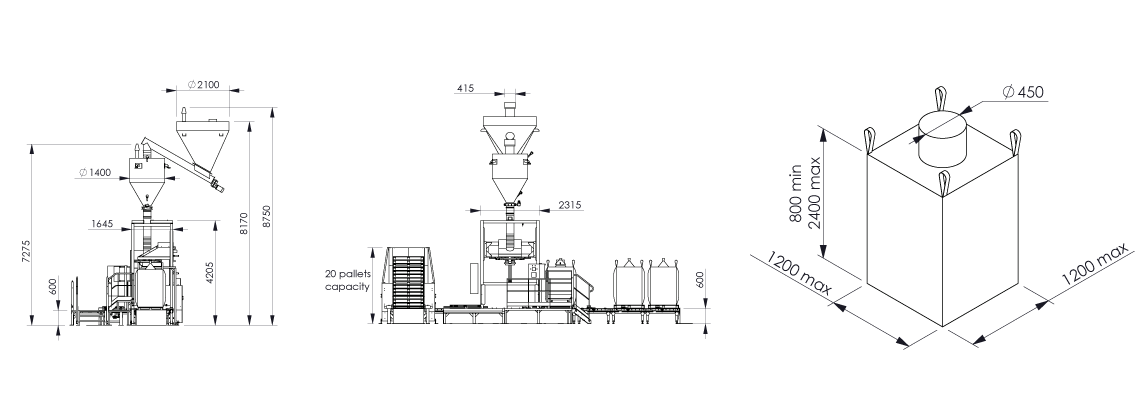
FlowMatic® 06 operation procedure:
- The pallet unstacker places an empty pallet on the roller conveyor to supply the bulk bag filling station automatically.
- The handles of the bulk bag are automatically hung by the operator thanks to the automatic rear hook feed system
- The spout of the bulk bag connects to the filling head through a dust containment inflatable seal.
- The big bag is tensioned and adjusted by a pneumatic cylinder to optimize the filling volume of the big bag.
- A pre-forming fan inflates the big bag to prevent wrinkles and optimize the filling capacity.
- The inflation fan switches to the dust collection system to ensure a dust free atmosphere.
- The dose of product, prepared in masked time, flows into the big bag while another dose is prepared.
- A vibrating table, positioned under the big bag, packs and densifies the material during the filling operation.
- When the filling operation is complete, the seal is deflated and the auto hooks release the FIBC straps.
- The bulk bag is transferred automatically by means of a motorized roller conveyor.
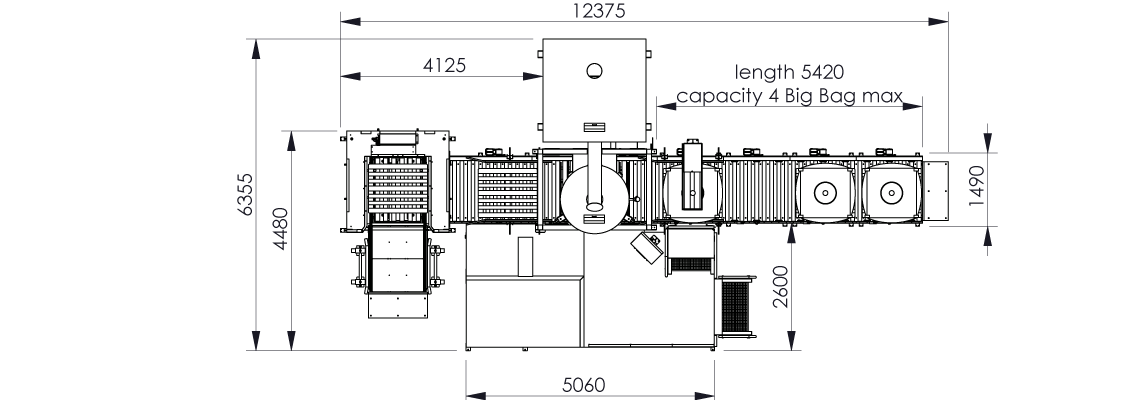
Equipment advantages
- Handling conveyor for automatic high rate filling
- Pallet unstackers with a capacity of 15 multi-format pallets
- Net weighing dosing hopper for containment and automation
- Simple unloading operation of filled bulk bags by forklift
Media
View our equipment in videos
Automatic big bag filler
Application client : Conditionnement automatique de big bags et dosage de sucre.
Semi-automatic big bag packaging line for fish meal
Mise en big bag semi-automatique de farine de poisson
Big bag filling - Flowmatic 06
Big bag filling - Flowmatic 06 100% automated bulk bag loader with net weighing for high rate loading
Bulk bag filling range
View our equipment in photos
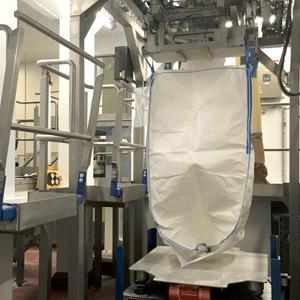
Automated line for bulk bag filling
The big bag filler is provided with a belt conveyor to ensure high filling rates.
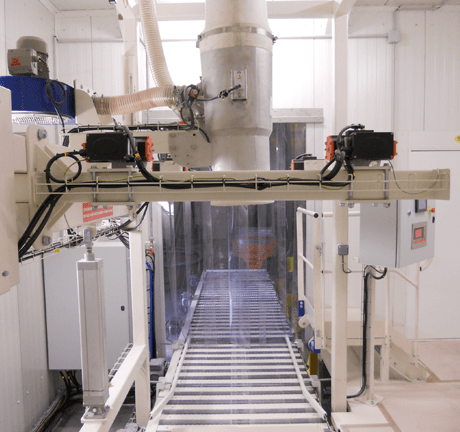
Bulk bag filling Palamatic Process
Motorized roller conveyor on big bag filling station.
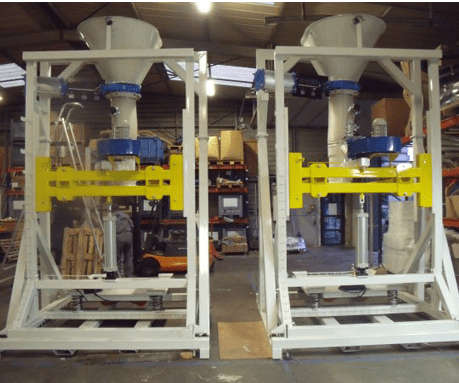
Bulk bag conditioner - Bulk materials handling
The complete solution for automatic super sack loading with net weighing. This bulk bag filler is perfect for a continuous use with high flow rate (30 to 60 big bag/hour) and to limit the operators intervention.
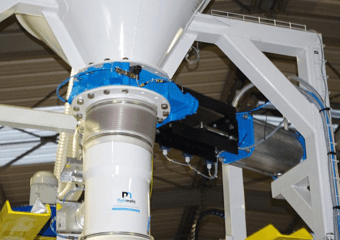
Big bag packing production line
The dosing hopper for feeding the big bag filling station is equipped with load cells.
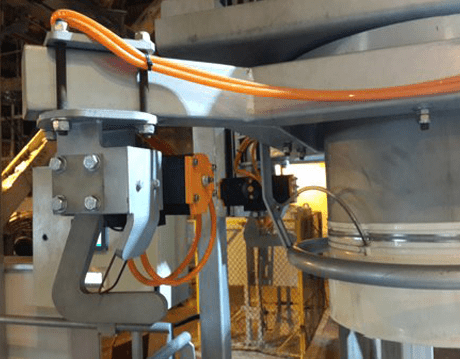
Big bag loading
The big bag unhooking system is automatic.
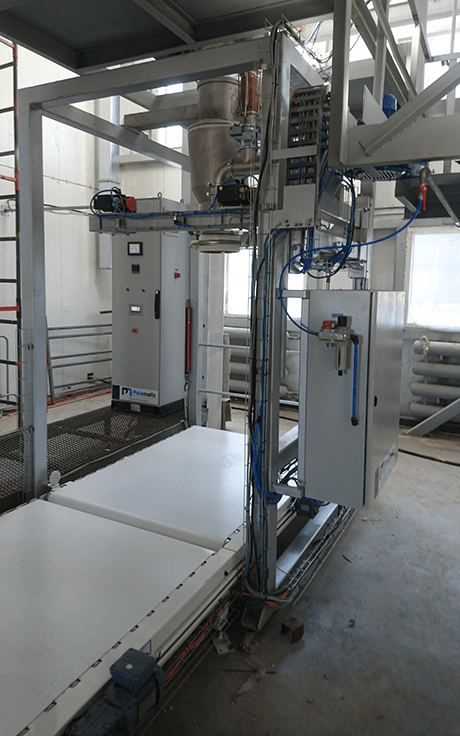
Big bag filling head
The belt conveyor provides motorized evacuation of the big bag once it is filled.
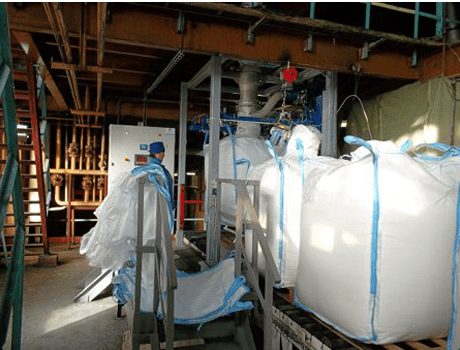
FIBC loading
Loading of big bags on industrial production lines processing bulk materials.
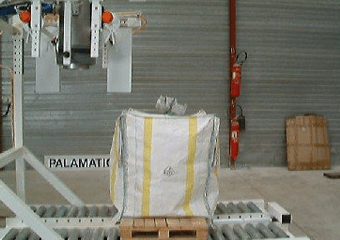
Big bag evacuation
The motorized roller evacuation conveyor allows the big bag to be filled at high speeds.
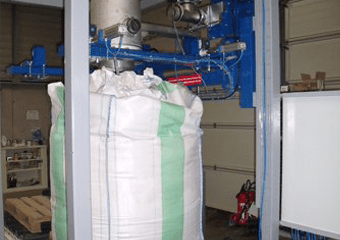
FIBC handling
Net weighing and commercial transaction are the benefits of the FlowMatic® 06 big bag conditioner.
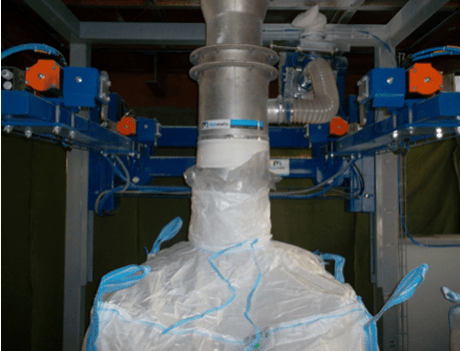
Bulk bag loading
Very high efficiency and station ergonomics are the benefits of the FlowMatic® 06 big bag packaging station.
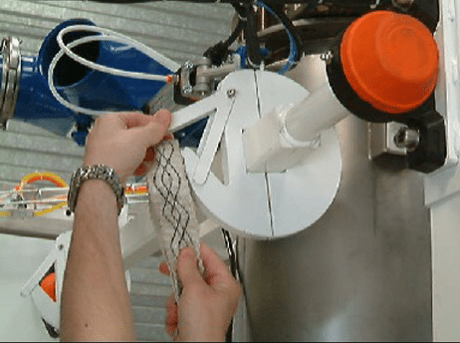
Big bag filling raw material packaging
The big bag is unhooked automatically once filled.
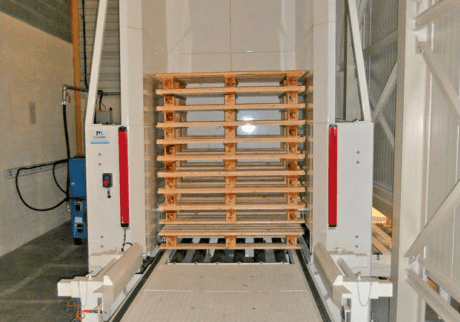
Pallet unstacker
The pallet unstacker has a capacity of 15 multi-format pallets.
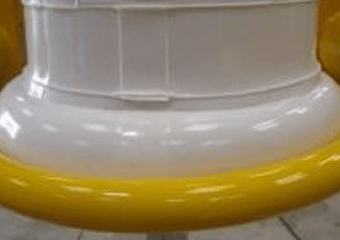
Big bag filling system powder handling equipment inflatable seal
The inflatable containment seal makes it possible to fill the big bag without powder emanating into the atmosphere.
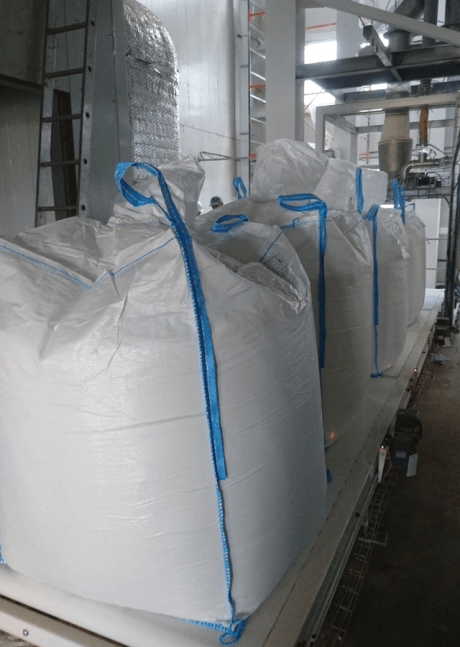
Handling conveyor on bulk bag filling line
Conditioning of minerals in big bags.
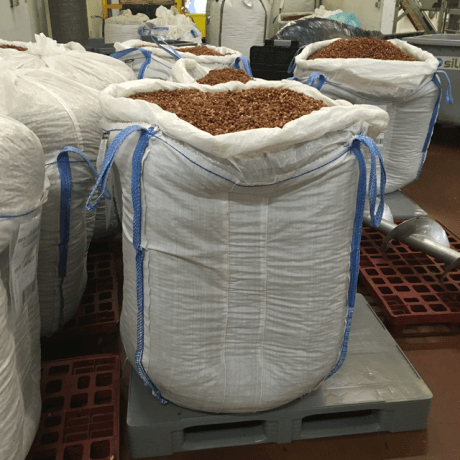
Bulk materials handling
Packing station for big bags of seeds.
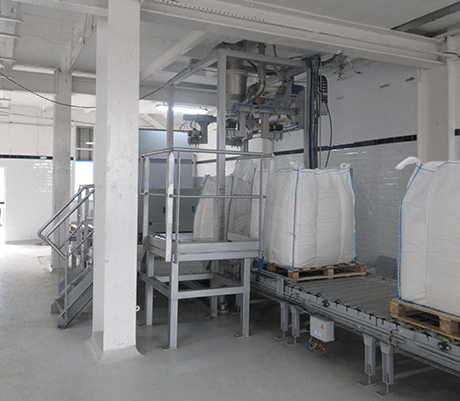
Big bag filling line conveyor
The big bags of sugar, once filled, are moved using a roller conveyor.
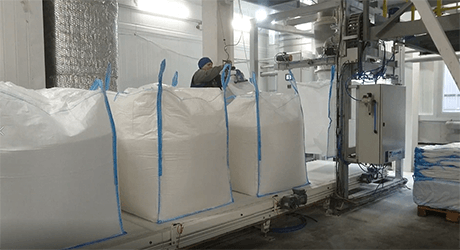
Big bag sewing after filling
Welding of the inner bag: the thermo-welding system permits a tight closure of the big bag after filling.
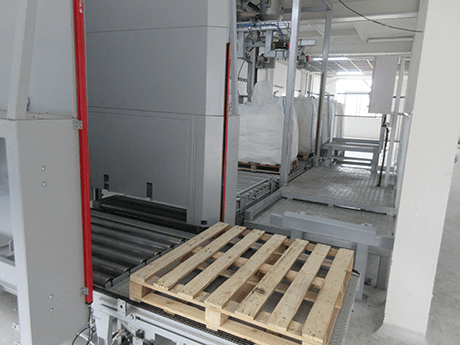
Big bag filling on pallet
The stacked pallets are stored in the warehouse and then feed one by one the big bag packing station via a motorized conveyor.
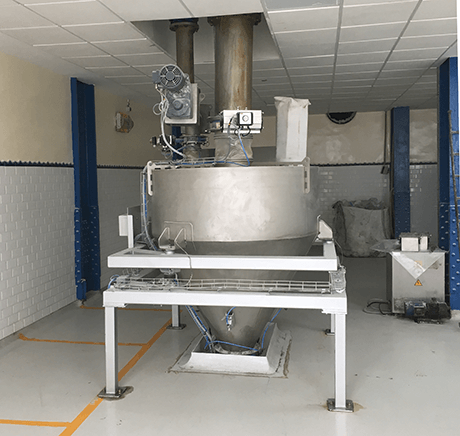
Hopper on bulk bag filling processing line
Dosing hopper upstream of the big bag filling machine for a biscuit processing line.
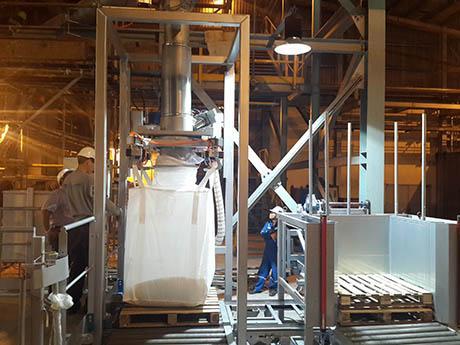
Bulk bag packing
This installation removes the finished material from the existing silo through a conveying screw (without an intermediate level to limit Atex risks as much as possible) in order to convey it to the big bag filling station.
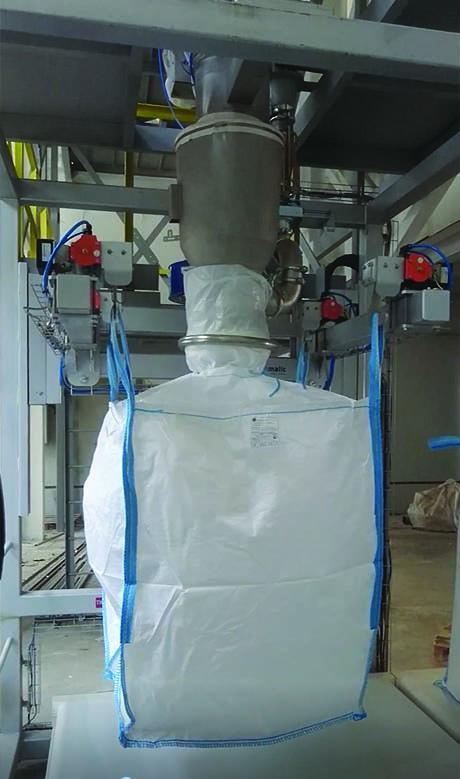
Big bag filling
The big bag is pre-inflated to facilitate filling.
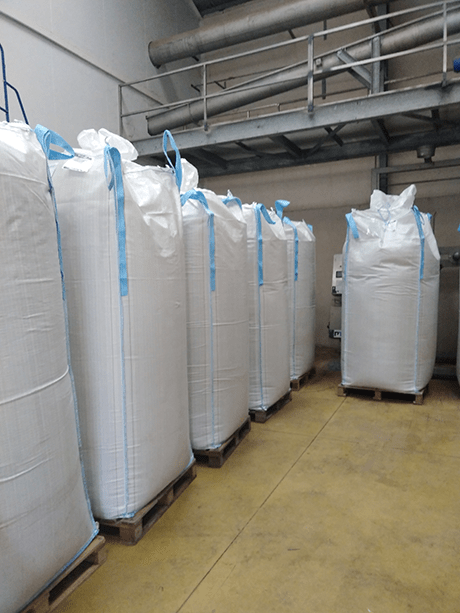
Bulk bag packing
The automatic removal of the big bag to the storage area is carried out via a roller conveyor.
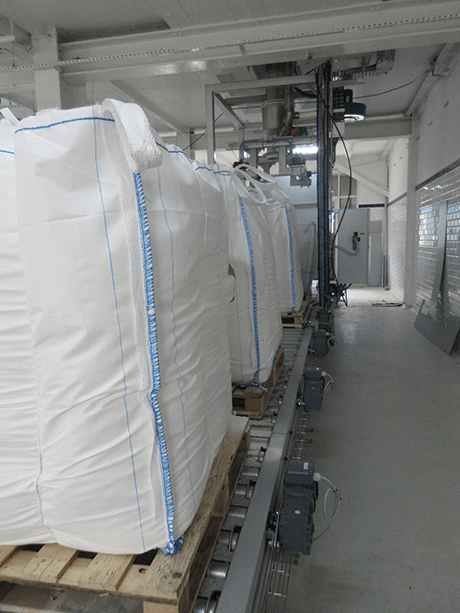
Big bag filling with sugar
The installation of a roller conveyor provides high filling rates.
Features
Technical specification
Rate | 30 to 60 big bags/h. |
---|---|
Capacity | 2 tons/big bag |
Manufacturing materials | Painted steel, 304L stainless steel |
Installed power | 8.7 kW |
Compressed air consumption | 10.2 Nm³/h. |
Dust removal rate | 600 m³/h. |
Finishing touches: RAL 9006, micro-blasted, electropolishing
Average power consumption: 1.5 kW
Operating pressure: 6 bar
Input 4 - 20 mA: 1
Digital input: 15
Digital output: 13
Accuracy of the weighing chain: ± 500 grams
Maximum dimensions of big bags: 1,200 (W) x 1,200 (W) x 2,400 (H) mm
Equipment integrated into the FlowMatic® 06 model:
- Pre-weighed dosing hopper
- Motorized roller conveyor
- Pre-inflation fan
- Automatic big bag unhooking
- Tension cylinder
- Vibrating table for densification
- Pallet unstacker
Options
Case studies
CASE STUDIES WITH THIS EQUIPMENT
Packing of white sugar and crystal sugar in big bag
Processed powders: white refined sugar, surfine caster sugar, crystal sugar - Packing in big bag of white sugar and crystal sugar - This big bag installation is designed to achieve a minimum flow rate...Food and Animal Feed
Powdered sugar packaging
Processes powder: powdered sugar - Powdered sugar bagging - Our client is a company specializing in sugar manufacturing with a need to increase production capacity to meet the rising demand by global...Food and Animal Feed
Loading bulk bags of soda ash
Treated powder : Natural soda ash - Automatic bulk bag filling line with buffer hoppers. Remote control system ensuring traceability and safety of the process.Chemical
Your quotation in 3 clicks!