Processed powder: Powdered sugar
Powdered sugar packaging
Our client specializes in sugar manufacturing and had a need to increase production capacity to meet the rising demand by global supply chains. Palamatic Process responded by integrating a FlowMatic® 06 automatic bulk bag filling system.
Design requirements:
- Ergonomics: workstation adapted to the operator and designed to promote better handling and improved efficiency.
- Rate and Accuracy: minimum of 40 bulk bags / hour with dosing accuracy provided by either a 4-20mA butterfly valve or screw feeder specially designed for this application.
- Flexibility: The installation allows packaging of various raw materials (particle size and bulk density) and is configurable with its acceptance module.
- Pallet System: automatic distribution of pallets by a pallet feeder (also called a pallet unstacker) that can store up to 20 pallets simultaneously.
- Conveying and storage: a motorized roller conveyor line allows the super sacks to be transferred to a buffer storage / pick-up location via forklift.
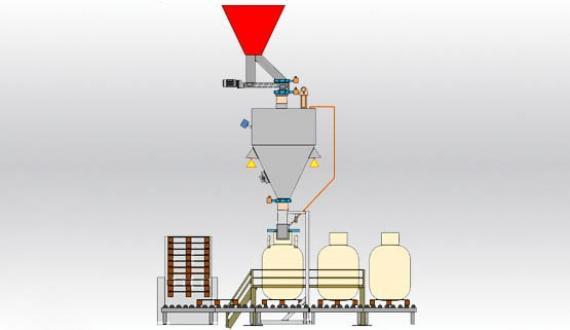
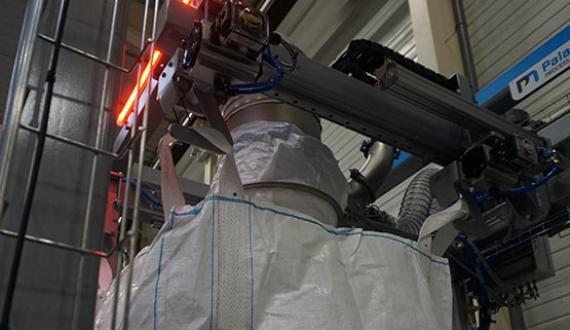
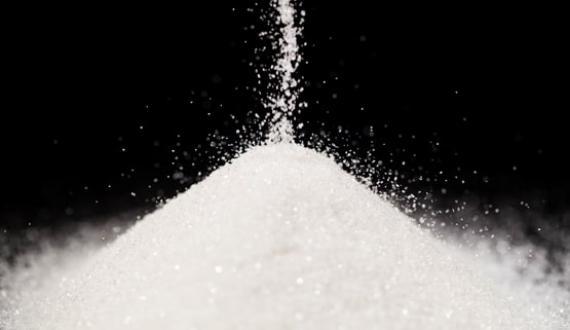
The installation consists of a weighed buffer hopper with the same storage capacity as one bulk bag, which provides production efficiency with the FlowMatic® 06 bulk bag filling station. After the bulk bag filling cycle is complete, the bulk bag is transferred down the line and the next one is prepared. During the next bulk bag preparation, the buffer hopper is being filled with the raw sugar powder material.
This super sack system is also equipped with a volumetric screw feeder, allowing precise weight control of the hopper contents.
This material dosing equipment is available in hygienic Easy Clean Design (ECD). Its assembly and disassembly makes cleaning and washdown fast and efficient for your industrial maintenance crew.
The FIBC filling station is equipped with automatic hooks, two of which move forward on linear tracks to optimize operator ergonomics. This allows easy loading of the next bulk bag to be filled.
A bulk bag welding station is also available to assist the operator in sealing the inlet spout and minimize operator / powder contact.
The entire installation is controlled by a PalTouch® Technology touch screen interface. The PLC and its tactile interface offer the operator simple and flexible use of the machine while ensuring traceability (batch number, PO number, customer, packaged weight, date, time, bar code).