Il y a souvent confusion entre les termes convoyeur à vis, doseur à vis, convoyeur vibrant et doseur vibrant. Dans le cadre de cet article, nous définirons ce qu'est exactement un équipement de dosage de poudre et comment choisir le meilleur type d'équipement en fonction de vos matériaux entre un doseur à vis et un doseur vibrant.
1. Fonctions principales d’un équipement de dosage
L'équipement d'alimentation n'est pas un système de convoyage. Les convoyeurs mécaniques, tels que les convoyeurs à vis (également appelés convoyeurs à vis sans fin) et les convoyeurs vibrants, se composent généralement d'une entrée et d'une sortie dans le seul but de déplacer des matériaux d'un point A à un point B sur de longues distances. Ils fonctionnent généralement à un rythme fixe et déplacent le matériau en aval à un débit constant mesuré en tonnes ou en kilogrammes par heure.
Les équipements de dosage sont, eux, utilisés dans les situations où un contrôle et une précision accrus du débit de matériau sont nécessaires. Les doseurs à vis et les doseurs vibrants ne servent pas à déplacer les matériaux sur de longues distances, mais plutôt à doser les matériaux d'une trémie ou d'un conteneur IBC vers une ligne de conditionnement ou vers un broyeur industriel. Ils sont beaucoup plus petits que les convoyeurs mécaniques et se composent d'une trémie intégrée, d'un agitateur, d'un petit tube ou d'un socle plat et d'un entraînement à fréquence variable.
La trémie intégrée est nécessaire pour les équipements de dosage car une charge de tête constante doit être maintenue pour un bon fonctionnement. La vitesse peut être contrôlée sur l'équipement d'alimentation via un VFD pour permettre des vitesses d'alimentation plus lentes ou plus rapides.
Si votre processus nécessite le reconditionnement du matériau traité dans des sacs en papier de 25 à 50 kg et que vous devez être certain de ne pas surcharger ou sous-charger le conteneur, un doseur est la solution. De la même façon, les broyeurs de poudre sont plus performants lorsqu'ils fonctionnent avec un taux d'alimentation régulier et constant.
2. Prendre en considération les caractéristiques de votre matière
Les poudres et les granulés peuvent avoir des propriétés différentes qui affecteront grandement leur comportement dans un processus de fabrication. Il est donc important, au préalable, d’étudier ces caractéristiques avant de sélectionner votre équipement industriel. De façon générale, voici les attributs communs à analyser concernant les matières vrac :
- Hygroscopicité : Le sucre, le sel et certains types de poudres chimiques peuvent facilement et aisément absorber l'humidité de l'atmosphère qui les entoure ce qui peut peut provoquer une agglomération et un durcissement de la matière pendant des périodes prolongées de stockage et de repos.
- Aération : Les perles de verre, la farine et les résines ont souvent un faible angle de repos et se comportent comme un fluide lorsqu'elles sont aérées. Ce matériau peut facilement inonder (flux incontrôlable) les processus en aval s'il n'est pas contrôlé.
- Formation de mottes : La farine de bois ou les fibres de biomasse et autres contiennent de longues particules qui s'emboîtent et forment des masses qui peuvent bloquer les canaux d'écoulement.
- Adhésion : Les matériaux tels que les pigments en poudre peuvent être adhésifs, c’est-à-dire coller et s'accrocher à toutes les surfaces imaginables, ce qui peut rendre ce type de produit très difficile à manipuler.
- Friabilité : Les pâtes, les flocons ou certains produits granulaires peuvent être facilement cassés (ce que l'on appelle l'attrition) s'ils sont manipulés trop brutalement. C'est pourquoi, il est nécessaire de disposer d'un équipement capable de manipuler et de transférer délicatement le matériau afin de préserver l'intégrité du produit.
- Facilité d’écoulement : Les granulés plastiques s'écoulent facilement par gravité, avec peu ou pas d'aide à l'écoulement ou d'un équipement spécialement conçu.
- Abrasivité : Les poudres de verre, le ciment Portland, etc. peuvent avoir des propriétés qui usent rapidement les composants de l'équipement si votre procédé n'est pas conçu en tenant compte de cette caractéristique. Cela peut entraîner une maintenance fréquente et coûteuse.
Anticiper comment votre poudre se comportera représente donc une étape clé dans le choix de votre équipement de dosage.
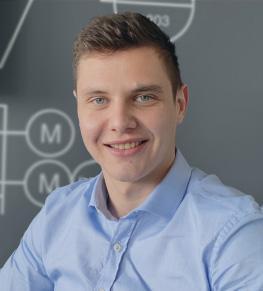
Vous hésitez sur le type de doseur à sélectionner ?
Je suis disponible pour échanger et vous conseiller.
Loïc, expert poudre
3. Différences de performance et de conception
Les doseurs à vis utilisent une trémie intégrée avec un agitateur qui alimente un canal tubulaire. À l'intérieur du tube se trouve une petite vis qui pousse le produit à travers une sortie vers le processus en aval. Il existe plusieurs conceptions pour la petite vis dans les alimentateurs à vis : les vis à queue de cochon, les vis à ruban et les vis avec un arbre d'entraînement.
- Les vis à queue de cochon n'ont pas d'arbre central et sont souvent utilisées pour les matériaux qui ont les caractéristiques suivantes : une densité légère et/ou sont collants ou cohésifs. Exemples : farine, poudre de cacao et oxydes.
- Les vis à ruban ont un arbre central mais les ailettes sont ouvertes et reliées en un point à l'arbre. Les vis à ruban sont utilisées sur des matériaux légers et granuleux tels que le PVC et les granulés de polymère.
- Les vis à arbre central sont utilisées pour les matériaux plus denses ou fluides comme les poudres métalliques par exemple.
Les doseurs à vis offrent une bonne précision. Dans certains cas, le dosage est d'une exactitude de -/+ 1-2 grammes. Il s'agit du type de doseur le plus utilisé car il convient à la plupart des applications sauf dans le cas de matériaux friables ou sensibles à la chaleur.
Les doseurs vibrants ont une structure similaire (trémie et unité de structure tubulaire) mais au lieu d'une vis, des moteurs de secouage sont fixés à l'unité et la structure est soutenue par des ressorts, pour permettre à l'unité de vibrer. Un angle très minime permet à l'unité de déplacer le matériau le long du banc d'alimentation vers le processus en aval. La vitesse d'alimentation peut être contrôlée en augmentant ou en diminuant l'amplitude et la fréquence des vibrations. Le brassage permet de préserver l'intégrité des matériaux ou d'éviter une usure inutile dans le cas de matériaux abrasifs. Par conséquent, lorsqu'il s'agit de matériaux friables, sensibles à la température ou abrasifs, les doseurs vibrants constituent la solution idéale.
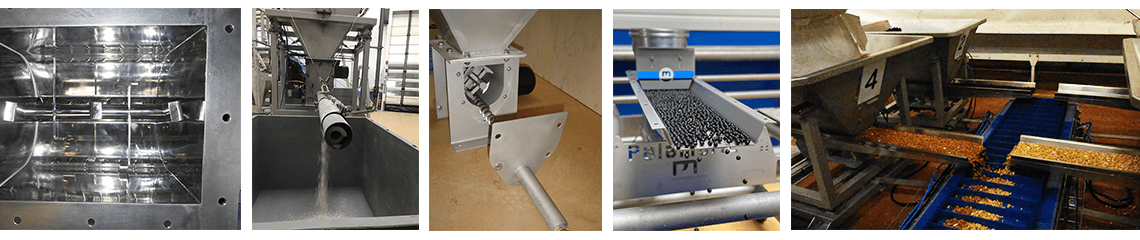
4. Avantages et inconvénients des doseurs à vis et doseurs vibrants
Doseur à vis
Principaux avantages d'un doseur à vis :
- Les types de vis peuvent varier et être facilement interchangés pour répondre à une grande variété de poudres
- La vis assure une extraction positive (traction) de la trémie
- Elle peut être conçue pour des applications faciles à nettoyer, sans avoir à retirer l'unité entière de la ligne
Principaux inconvénients d'un doseur à vis :
- Les matériaux adhésifs et les fines peuvent s'accumuler à l'intérieur du matériau, ce qui limite le débit
- Les pièces mobiles peuvent provoquer une usure supplémentaire de l'équipement, ce qui entraîne des besoins en maintenance plus importants
- Consomme plus d'énergie qu’un doseur vibrant
Doseur vibrant
Principaux avantages d'un doseur vibrant :
- Ce doseur gère des débits d'alimentation faibles et élevés
- Il produit un flux de matériau uniforme qui permet une manipulation en douceur
- Pratiquement aucune pièce mobile, ce qui réduit les besoins en maintenance
- Faible consommation d'énergie
Principaux inconvénients d'un alimentateur vibrant :
- L'action vibrante peut générer de la poussière avec certaines poudres fines
- La vibration peut éventuellement séparer des matériaux qui ont été mélangés
- Ne fournit pas une extraction positive (un moyen de tirer le matériau de la trémie)
- Une matière à tendance adhésive ou des fins peuvent s'accumuler sur le plateau d'alimentation, limitant le débit