Poudres traitées : facteurs d’appétence, arômes destinés aux aliments pour chiens et chats
Fabrication croquettes petfood
Entreprise SPF. Pour faire face à son développement, la société française SPF, branche « petfood » du Groupe international DIANA-Ingrédients, s’est dotée d’un nouvel atelier de mélange de poudres.
La réalisation de cet atelier a été confiée à Palamatic Process pour l’ensemble des lignes de vidange de big bags, de transfert pneumatique, de tamisage et de dosage, incluant l’intégration de mélangeurs industriels existants (cinq transferts pneumatiques, deux mélangeurs industriels, stations de remplissage de big bags pour les produits frais).
Objectifs de l'installation :
Concevoir et installer un atelier permettant d'améliorer les mélanges et d'augmenter la productivité.
La société Palamatic Process a été choisie pour la conception, la fourniture et le montage des lignes de vidange de GRVS, de transfert pneumatique, de dosage, de tamisage et de remplissage. Palamatic Process a également assuré le déplacement et l’adaptation des mélangeurs industriels existants.
Un process opératoire sans poussière
Les différentes lignes mises en place par Palamatic Process sont destinées à préparer un premix dans une trémie pré-pesée à partir de différentes poudres conditionnées en big bags, à alimenter le mélangeur industriel, puis à conditionner le mélange en big bags. Elles intègrent cinq stations de vidange big bags, un transport pneumatique aspiré phase dense VFlow® assurant le transfert des poudres, implanté sur pesons au débit de 6 500 litres/heure, un tamis vibrant, un châssis de support pour les big bags à remplir, un ensemble de dépoussiérage industriel avec son réseau de tuyauterie et une trémie sous mélangeur.
Une fois le big bag mis en place sur le plateau de dépose, l’opérateur ouvre la boîte de délaçage et défait le chignon afin de procéder à la vidange du big bag. Celle-ci peut être optimisée par la mise en marche du système de massage. Grâce à l’implantation optionnelle d’une vanne d’interruption de vidange, l’opérateur peut arrêter ou réguler à tout moment la vidange du big bag. Une fois la vidange terminée, le retrait du big bag s’effectue à l’aide du palan et de la croix de manutention. Afin de minimiser les émissions de poussières, la boîte de délaçage est reliée à l’unité de dépoussiérage industriel.
Pour réaliser un dosage précis, un cyclone de transfert pneumatique est implanté sur une trémie de 1 300 litres, le tout monté sur pesons. L’automatisme permet de déterminer le poids souhaité. Une fois le poids choisi, le cyclone de transfert aspire la quantité de poudre nécessaire dans la trémie pré-pesée, en amont du mélangeur.
Lorsque le poids est atteint, l’automate coupe l’alimentation du transfert pneumatique et ferme la vanne d’arrivée produit correspondante. Le premix est alors prêt à être introduit dans le mélangeur industriel.
Les stations de vidange big bag et leurs équipements :
Le corps de chaque station de vidange big bag fournie par Palamatic Process est construit en inox 304. Toutes ses soudures sont décapées et passivées pour les parties en contact direct avec le produit et la station est équipée d’une porte d’accès articulée en lexan transparent. L’étanchéité est assurée par un montage par brides avec joint FDA.
La goulotte d’évacuation statique des poudres (trémie tampon) est fabriquée à partir d’inox 304. Son diamètre de sortie correspond aux dimensions de la boîte de mise en vitesse du transfert pneumatique.
La structure autoportée est renforcée pour permettre de supporter le poids du big bag.
Afin d’optimiser la vidange du big bag, un système autonome de tension des flancs permet d’éviter les poches de rétention et garantit ainsi une vidange optimale du big bag sans perte de produit.
De manière à favoriser l’écoulement des produits, toutes les pentes du système ont été déterminées en fonction de l’angle du talus du produit s’écoulant le plus difficilement.
Le système d’extraction des poussières, conçu par Palamatic Process est composé d’un bâti en inox dans lequel sont installées les cartouches filtrantes ; un moto-ventilateur de 3 kW fournit le débit d’air nécessaire. Des registres de réglage sont implantés sur la tuyauterie afin d’ajuster le débit d’aspiration sur chaque station de vidange big bag. De façon à sélectionner l’appareil à dépoussiérer, un clapet de commande pneumatique est installé sur chacune des tuyauteries de vidange de big bags. La commande du clapet s’effectue par l’armoire de commande.
Un système de décolmatage par buses a été installé sur chaque cartouche. Le décolmatage est piloté par un séquenceur électronique qui permet de régler les intervalles de décolmatage ainsi que les durées des impulsions d’air comprimé. Un cycle de décolmatage à l’arrêt est programmable pour assurer la récupération des fines avant le changement de produit. Les fines sont récupérées dans un seau clampé sous le dépoussiéreur.
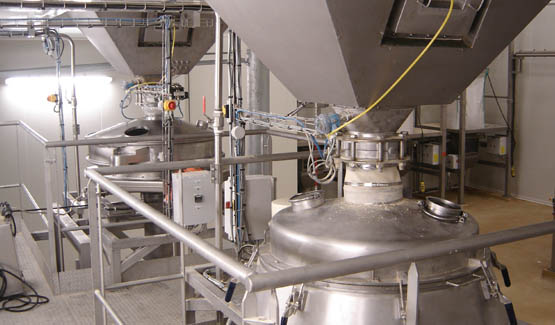
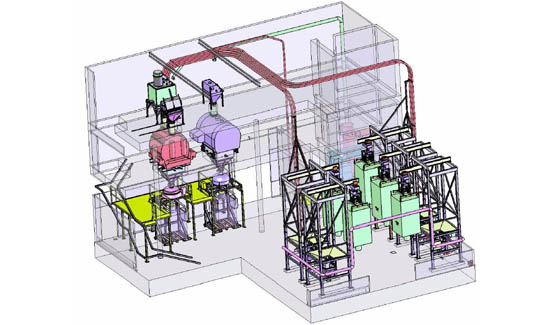
Le transfert pneumatique en phase dense :
Pouvant assurer un débit de 6 500 litres/heure, le transfert pneumatique est implanté directement sur la trémie de pré-pesée de 1 300 litres en amont du mélangeur industriel. L’ensemble cyclone + trémie a été installé sur trois pesons.
Le cyclone séparateur, avec son système de décolmatage automatique par air comprimé, est connecté aux stations de vidange de big bag. Les tuyauteries sont regroupées sur le corps de la trémie tampon et la sélection est réalisée par des vannes pilotées.
La pompe à vide est équipée de deux filtres supplémentaires permettant d’assurer la non-contamination de l’atelier.
Toutes les parties en contact avec le produit sont réalisées en inox 304 avec des soudures décapées, passivées et polies, et un microbillage à 500 microns intérieur et extérieur.
Résultats obtenus :
Possibilités de mélange multipliées, diversité des produits améliorée, qualité des mélanges optimisée, productivité de l’usine accrue, capacité doublée, traçabilité assurée.
Grâce à cette nouvelle installation, les possibilités de mélange industriel ont été multipliées permettant une amélioration de la diversité des produits, la qualité des mélanges a été optimisée par une meilleure précision des dosages industriels, la productivité de l’usine a été accrue, la capacité doublée et la traçabilité assurée dans les meilleures conditions de sécurité.
Après quelques mois de fonctionnement, Philippe FONTENAY, responsable du projet chez SPF, peut déjà faire un premier bilan. Il déclare : « L’esprit d’équipe qui a animé ce projet a permis de réaliser cette installation de façon très satisfaisante dans un délai de huit mois. L’ensemble des objectifs, tant quantitatifs que qualitatifs, ont été atteints. La productivité a pu être augmentée et la capacité a été multipliée par deux. De plus, l’enregistrement des paramètres a été automatisé permettant une gestion zéro papier et une traçabilité du système absolument sans faille ».