Manufacturer’s dealing with dry bulk materials can face a lot of challenges during the packaging phase. It is critical for an equipment supplier to understand production challenges and requirements when a client is sourcing powder filling equipment for their specific application.
There are a few basic questions you can ask yourself to help select the right powder filling machine or powder filler that fulfills both production goals and your customer expectations. Let us look at a few key aspects that are important to know regarding bag filling machines pertaining to their functionality and overall design.
1. What are the characteristics of the material?
Bag fillers are essential in filling a wide variety of both free-flowing and non-free-flowing powdered or granulated products. Bulk solids that are not cohesive, like granulated sugar or salt, are considered to be free-flowing. They are not easily compressed when pressure is applied and are typically very easy to handle and process. By contrast, powder products with poor flow properties, such as brown sugar or powdered milk, can be compressed (agglomeration) and can keep their shape when manipulated.
Besides the flowability of the dry material, another factor to take into consideration is the bulk density, especially pertaining to what equipment is being used in the upstream process. A production facility should avoid packaging material when it is aerated, as the bulk density is not truly representative of the material after it has had time to rest.
A common packaging system, particularly in the food industry, is to have a large industrial blender that mixes ingredients prior to the powder being packaged (spice blends, instant food mixes). Once a powder is done being mixed, it will be fully aerated meaning that in between each particle of powder exists air gaps. If an operator attempts to fill a 50 lb. sack with this aerated material, the air will take up more volume then is necessary and the production loses cost efficiency on the package product.
Integrating features such as a vibrating densification table underneath the bag helps shake the material during the filling phase. The vibration causes air between the particles to escape, densifying the particles and increasing the fill efficacy of the container. The air volume and material flow can be balanced by using a degassing cylinder on the filling head of the station. This can then be either connected to a simple filter sock, or even better, a central dust network to keep the surrounding environment clean and safe.
2. What is the type of container to be filled?
Some bag and container types can be more easily implemented in an automated system while others do not. For example, equipment needed to close or seal bags can change both in design and price. Poly-woven bags, paper bags, plastic type bags, lined paper bags, etc.: the construction material of the bag, how it is to be placed on a bag filler, how it is sealed and handled through the packaging process all need to be taken into consideration. The type of bag and how it is made can have an impact on what type of bagging solution and auxiliary equipment you production process will need.
Some bag types will use either an inflatable seal to secure the open top bag in place, as well as contain any potential dust leads.
Boxes and buckets on the other hand may use an adaptable dust cover plate to gently rest over the container to accomplish the same previously mentioned task.
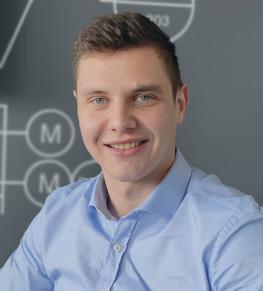
Do you need personal advice on sack filling units?
I am at your disposal.
Loïc, powder expert
3. What degree of automation is needed?
There is no doubt that in recent years the needs of manufacturer’s have rapidly evolved towards automation as they struggle to source manual labor. As technology becomes more cost-effective and efficient, automation has become the industry buzz word for solving current economic woes. However, automation is not always the solution as production facilities must consider the potential ROI on such systems, and if other parts of their process will still remain dependent on the needs and critical thinking skills only a labor force can deliver.
Obviously, machine and system design are the key drivers in what level of automation a production process requires. Powder filling machinery can be grouped into three distinct classes based on the machine’s automation level: manual, semi-automatic, and fully-automatic powder filling machines.
In manual powder fillers, the operators need to be always alert and take a very active part in the powder filling process. They need to perform most of the tasks including the following:
- Weighing of the filled containers
- Determining the exact fill quantity
- Starting and stopping the machine
In semi-automated setups, some parts of the process are automated while other parts are still manually done. Depending on the manufacturer, it may be possible to upgrade them to a fully-automatic machine with a few modifications.
Semi-automatic powder fillers can have a PLC control system for performing a series of tasks such as quantitative filling and measuring dosing adjustments. Finally, semi-automatic systems allow the operator to have more control over the filling process. Operators can even use weight-based or volumetric filling limits.
Full automation makes use of the latest technology which results in less or no labor input and an efficiently controlled process. The majority of the process’s tasks are done automatically via the PLC system sequences. These tasks include feeding of the powder product into the hopper/tank, product weighing/measuring, and filling. Also, automated container fillers can handle both powder and granulated products, which results in an easy to use and flexible packaging process.
4. Other considerations?
Some other important features to consider are:
- Production rates (bags per hour)
- Dosing accuracy
- Hazardous area rating
A small to mid-size manufacturer may be able to use a manual or semi-automated filling system to handle 1 to 2 bags per minute. However, large manufacturers with daily production output goals measured in tons may need a very efficient and fully automated system with a PLC that controls all functionality as well as a robotic palletizing arm for loading and shrink wrapping the bags once packed on a pallet for shipping.
Some manufacturers may have less concern about precise filling weights if they are more concerned about selling a less expensive material by bulk. But materials with high input costs will need very precise dosing mechanisms as to not over pack the bags of material. By using load cells on the filling hopper and integrating a screw feeder, it is possible to achieve a dosing accuracy within +/- 1 to 2 grams in some instances.
Finally, and probably most importantly, one must take into consideration the potential explosivity of the powder material. With current NFPA 70 NEC regulations, it is imperative a manufacturer understand the necessary OSHA regulations for what the equipment should be designed and rated for to avoid workplace accidents and serous operator injuries. You can read more on this topic: What are the differences between nfpa 70 nec, atex and iec ex rated equipment for hazardous locations?
Palamatic Process has been supplying the powder and bulk solids industry with bulk bag and sack filling equipment since 1992. In order to determine what solution is best for your project, contact one of our sales engineers. Together, our team of experts can provide the right kind of powder filling equipment that will fulfil your every production goal.