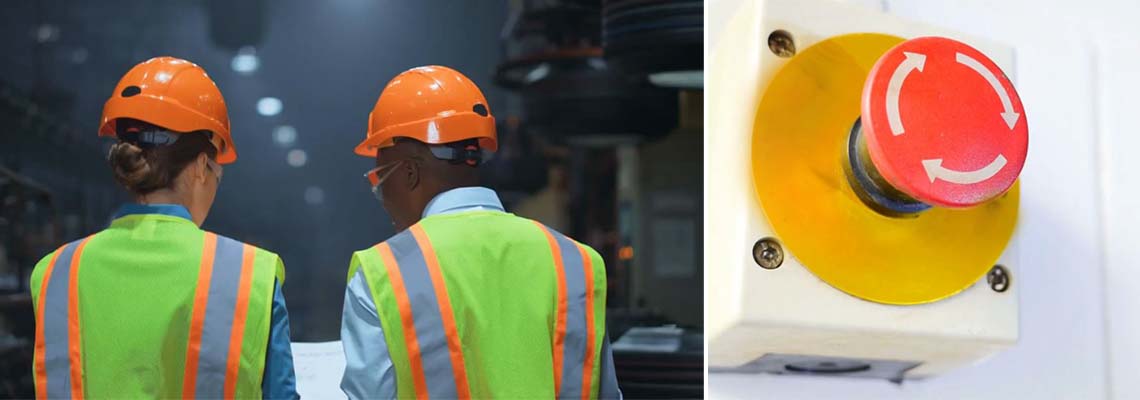
The safety of your workforce and the industrial equipment they use requires preventive measures aimed at reducing risks and eliminating dangerous situations linked to the use of machines. These risks involve the exposure to the mechanical components and are linked to the energy sources or even to nuisances such as noise, lighting and the state of the work area.
Most of the risks associated with mechanical hazards can be avoided by having risk reduction strategies, such as: adequate signage, suitable working methods, an emergency stop button, protection devices, etc.
In all cases, as stipulated in the Occupational Safety and Health Act of 1970 “To assure safe and healthful working conditions for working men and women; by authorizing enforcement of the standards developed under the Act; by assisting and encouraging the States in their efforts to assure safe and healthful working conditions; by providing for research, information, education, and training in the field of occupational safety and health.”
Examples of OSHA standards include requirements to:
- Provide fall protection, such as a safety harness and lifeline
- Prevent trenching cave-ins
- Ensure the safety of workers who enter confined spaces such as manholes or grain bins
- Prevent exposure to high levels of noise that can damage hearing
- Put guards on machines
- Prevent exposure to harmful levels of substances like asbestos and lead
- Provide workers with respirators and other needed safety equipment (in almost all cases, free of charge)
1. Risk analysis and commissioning
Above all, securing the machines through a preliminary analysis (fixed, mobile, production line, etc.) and the present risks within the industrial site (noise pollution, vibrations, lighting, dangerous substances, restricted space, etc.).
The machine manufacturer and production plant both have an obligation to comply with OSHA laws and regulations (Standards – 29 CFR) Part 1910 – occupational safety and health regulations, to guarantee the safety of operators on its machines. The certification is carried out either by the designer himself in the form of a self-certification or it is an approved third-party which certifies the conformity of the machine and issues the certificate.
Upon receipt and commissioning of the machine, specifications and a procedure guaranteeing its compliance with the regulations must be given to plant personnel. These documents define the operator’s intervention procedures and proper use of the equipment. The instruction manual gives recommendations concerning the compatibility of a machine within a specific working environment and therefore must be respected.
In order to provide ergonomics and safety for production operators, an occupational risk assessment must be conducted by the employer before the machine is put into service. Define the "limits" of the machine - such as the users, its duration of use, the type of materials used, etc. Also define examples of dangerous mechanical phenomena that can occur - cutting, sectioning, shock, projection, crushing, etc. These elements are also an important step in the analysis of occupational risks.
Depending on the indications given by the manufacturer, personal protective equipment (PPE) may be necessary.
2. Signage
Each industrial machine must include signals, warnings and alarms to warn operators of the risks associated with use of the machine and dangerous zones. They must be clearly visible and easily understandable.
This signaling is carried out via visual pictograms with standardized colors relating to machine safety.
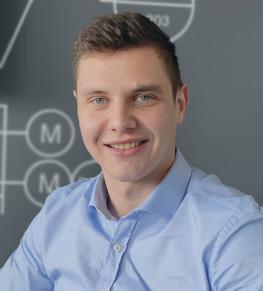
Are you looking for secure machines?
I can assist you in your process.
Loïc, powder expert
3. Machine guards
There are several means of mechanical and electrical protection of machines.
Mechanical guards of industrial machines:
- Operator protection screens
- Closures and partitions for the protection of machine tools
- Padlocking with isolation devices (circuit breaker) and accessories (hasps, padlocks)
- Locking and interlocking systems preventing the opening of sliding, pivoting or removable guards during dangerous movements
- Frames, mesh enclosures and machine protection casings
- Soundproofing hood, sound insulation, anti-vibration blocks, etc. to keep noise emissions from machines to a minimum.
Electrical protectors of industrial machines:
- Machine emergency stop switches in case of danger. This action interrupts the energy supply to industrial pumps, motors, etc.
- Safety switches (particularly explosive atmospheres)
- Sensitive devices and safety light curtains which cause the machine, or one of its elements, to stop when a person enters a dangerous zone (opto-electronic safety devices for presence or movement detection, safety mats, etc.)
- Control circuits (electrical, hydraulic or pneumatic in nature)
4. Servicing, maintenance and improvement of machinery
In addition to machine guards, it is essential to maintain machines regularly and to perform periodic checks to detect any possible failures that could trigger an accident and to ensure that they are kept in compliance. If defects are detected, corrective action should be taken and employees should be informed. Maintenance of machines must be carried out by qualified personnel trained in this type of operation in order to minimize any occupational risk. Safety instructions must be kept available for the operators and updated if necessary.
Machine maintenance (checking, inspection, cleaning, deburring, lubrication, adjustment, troubleshooting, repair, etc.) requires a specific organization that takes into account the technological, material and organizational constraints of the company. It is, in fact, a stage where workers are particularly exposed to occupational diseases and accidents. The priority in connection with the maintenance service of a machine remains the control of energy. Each maintenance operation must be carried out on a de-energized machine with a lockout of the energy sources beforehand. When a machine requires energy maintenance, all technical safety measures must be put in place (reduced speed, maintained action...) as well as clear instructions.
If a machine is modified for new needs/new functions, the employer must ensure that its safety level does not deteriorate. Machine improvements can be carried out by the manufacturer, specialized companies or users if they have the required skills. A new risk assessment must be carried out and the workers handling the machine must be informed.
Finally, particular attention must be paid to the layout of the workplace and workstations as well as to the training given to operators to guarantee their safety throughout the production process.
Palamatic accompanies you in the installation of industrial machines secured in adequacy with your trade constraints that it is for operations of conditioning, emptying, mixing, sifting, dosing, etc.
You can come to our test station to test your products directly on our machines. Contact our experts to make an appointment.