IBC container discharge: why do industries choose IBCs for powders and bulk materials?

In industries dealing with powders and granular bulk materials, choosing the right container is critical to ensure efficient material flow, minimize losses, and protect operator safety. Bulk bags, drums, sacks, octabins, or IBC containers—each option has its advantages and limitations depending on containment, dosing, and ergonomic needs.
Among these solutions, IBC containers (Intermediate Bulk Containers) are increasingly preferred for their ability to optimize flow, limit dust emissions, and enhance process flexibility. Why are Canadian industries choosing them over other alternatives? What benefits do they offer in terms of cleanliness, efficiency, and traceability? This article covers best practices for IBC filling and discharge, along with the equipment required for a safe and sealed transfer.
1. Comparison of storage and discharge solutions for bulk powders
Each storage and discharge system comes with its own set of benefits and limitations depending on the type of material, quantity, and process requirements. Below is a comparison of the most common options used by Canadian industries when handling bulk powders and granular materials.
1.1. Bulk bags: a cost-effective but limiting option
Bulk bags are widely used across industries for the storage and transfer of powders and granulates. They are affordable and flexible, but also present several challenges. Product may clump or bridge, making flow inconsistent. In addition, opening a bulk bag often releases significant dust, which can cause hygiene and safety issues. Handling also requires special equipment such as hoists or forklifts, which complicates operations.
1.2. Drums and bags: suitable for small quantities, but restricted
Drums and sacks are ideal for small-batch applications, especially in labs or small production units. They are easy to move and manipulate but require repeated opening, which increases the risk of dust and contamination. Additionally, packaging waste management is more demanding than with larger-volume bulk solutions.
1.3. Octabins: a compromise between volume and product protection
Octabins offer high-volume storage with improved protection for materials thanks to their rigid structure. However, their limited flexibility in dosing and the need for specialized discharge systems can be a drawback in some industrial processes. Learn more about bulk powder handling equipment.
1.4. IBC containers: the optimized solution for safe and controlled discharge
IBC containers are becoming the go-to choice for manufacturers seeking a balance of safety, control, and process flexibility. Their rigid frame ensures clog-free, consistent discharge. Unlike bulk bags or octabins, IBCs allow users to discharge only the required amount, helping to reduce material loss and streamline inventory. Their sealed design significantly reduces dust emissions, offering ideal containment for sensitive environments. Automated cleaning systems further ensure high hygiene standards, even in demanding sectors.
2. Why choose an IBC container for discharging powders and bulk materials ?
2.1. Cleaner and contained discharge
Powder discharge is a critical stage in any industrial process. Dust emissions can lead to material loss and pose health and safety risks for operators. IBC containers provide precise and even flow while significantly reducing dust release. They are also compatible with containment and dust extraction systems, ensuring a cleaner and safer working environment.
2.2. More flexible handling of raw materials
One of the key benefits of IBC containers is their ability to release and dose only the necessary amount of product. This flexibility allows manufacturers to better control inventory and adapt production to demand. Unlike bulk bags or octabins, IBCs enable efficient product changeovers with reduced cross-contamination risk, making them ideal for multi-product environments.
2.3. Ergonomics designed for operators
Ergonomics plays a crucial role in equipment selection. IBC containers are easy to handle, helping to reduce physical strain on operators. Their compatibility with dosing and transfer systems also allows for automated processes, limiting manual operations and minimizing human error.
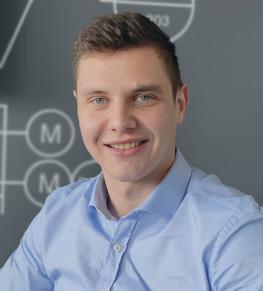
Do you have a project involving IBC container discharge for powders or bulk solids ?
I’m available to support you and guide your process review.
Loïc, expert in IBC discharge systems
3. How to fill an IBC container ?
3.1. Gravity filling
Gravity filling is the simplest and most economical method for loading an IBC container. The container is placed beneath a silo or hopper fitted with a downpipe. When the silo valve is opened, the powder or granulate flows freely by gravity. This method works well with free-flowing, low-density products, but it can generate dust emissions if no containment solution is implemented.
3.2. Manual sealed system filling
When external contamination must be avoided, a manual sealed filling system can be used. This system uses a movable cover or false plate that lowers to seal the IBC inlet. It prevents foreign particles from entering and stops dust from escaping during filling. Although semi-automated, this method requires an operator to lower and remove the plate before and after the filling cycle.
3.3. Fully sealed system filling
For industries where total containment is required, a sealed inflatable seal system is recommended. This setup hermetically seals the IBC inlet during filling. An inflatable seal presses down into the container opening, ensuring zero dust leakage. A pressure balancing system is often integrated to prevent volume surges and to ensure smooth, uniform filling. This solution is ideal for volatile, toxic, or moisture-sensitive powders.
4. How to discharge an IBC container ?
4.1. Standard gravity discharge
The most common method involves placing the IBC container above a receiving system and opening the bottom outlet valve. The product flows down naturally by gravity. This technique is easy to implement, but may result in dust emissions unless a proper containment solution is used downstream.
4.2. Tulip seal discharge connection
To ensure a dust-tight discharge, a tulip-shaped connection seal can be used. The IBC container is placed on a discharge station where a flexible tulip seal connects hermetically to the container outlet. Once sealed, the butterfly or slide gate valve can be safely opened, allowing a clean and controlled transfer. This is a popular method in advanced bulk powder handling systems.
4.3. Discharge with flow-assist system
Some powders tend to clump or block at the outlet, making discharge difficult. In such cases, the IBC can be fitted to a vibrating discharge station. Gentle vibrations loosen compacted material and help maintain a steady flow. This system is ideal for fine powders, sticky products, or dense granulates.
4.4. Transfer with split butterfly valve
The cleanest and most secure method is using a split butterfly valve system, where one half is attached to the container and the other to the discharge station. When connected, the two halves join to form a sealed interface, ensuring that no product escapes and no contaminants enter. This solution is particularly suited for pharmaceutical, chemical, and food-grade environments requiring maximum hygiene and containment.
5. Frequently Asked Questions
5.1. Is an IBC more expensive than a bulk bag?
Yes, the initial cost of an IBC container is higher than that of a single-use bulk bag. However, IBCs are much more durable and reusable. They also improve process cleanliness and help reduce handling and cleaning costs. Over time, they are a more cost-effective investment for manufacturers.
5.2. How can I ensure safe and contained discharge?
The best solution is to use IBC containers with a dedicated discharge station. Combining this with a tulip seal system or a split butterfly valve ensures dust-free and sealed transfer. Additional options like vibrating platforms or fluidization devices can be integrated to enhance flow, without compromising containment. Learn more about contained powder handling solutions.
5.3. Can IBC discharge be automated?
Yes. There are fully automated discharge systems that manage valve control, flow rate, and containment levels. These systems often include sensors to monitor fill levels and automatically adjust flow according to production needs. Automation reduces manual intervention and enhances operator safety.
5.4. What is the maximum capacity of an IBC?
IBC containers typically range from 500 to 1,500 litres, but custom models can exceed this depending on process requirements. Capacity choice depends on storage space, handling constraints, and production volume.
Conclusion
Selecting an IBC container for managing powders and bulk materials is a smart choice for manufacturers looking to optimize their process. Thanks to their rigid structure and sealed discharge options, IBCs provide enhanced cleanliness, improved operator safety, and greater flexibility for handling various materials.
Palamatic Process offers solutions tailored to different automation levels:
- IBCFlow® 01: a simple, reliable solution for IBC discharge.
- IBCFlow® 02: an advanced version with integrated control systems.
- Custom-built solutions: designed to meet your industry’s specific needs.
Contact us today for a customized assessment and discover how our innovative systems can optimize your bulk material handling operations.