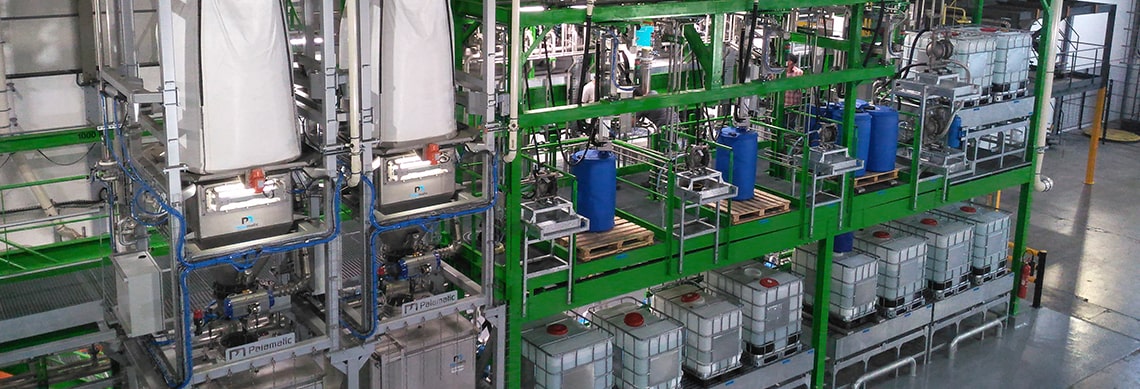
Implementing a new process line or facility can be a serious under taking and must be carefully planned before bringing your powders and bulk materials to market. Many factors go into designing, sourcing and installing a production facility, far too many to cover in detail for one article.
However, when it comes to sourcing the correct powder handling and processing equipment, we can boil down the criteria to five main points. Palamatic Process has 29 years of experience in supplying turnkey engineered solutions for all industries dealing with dry ingredient manufacturing. With our expertise, we can help you define the main objectives for your next bulk material-handling project.
1. Material characteristics
A powder is dry substance composed of many smaller individual particles and is a sub-class of material when dealing with the production of bulk solids. Granules is another form of dry bulk solid and can behave somewhat differently then powders.
It is important to understand the characteristics of your dry materials when planning and sourcing your production equipment.
Unloading, conveying, mixing, milling all require a thorough understanding of the material to successfully implement the manufacturing process.
Bulk Density plays a key role in how a powder behaves in production lines, especially when it comes to storing, conveying and mixing. Lighter powders will take up more volume when targeting a specific weight for packaging, whereas heavier powders may require more velocity to blow through conveying pipes.
Particle Size Distribution is also important to understand of your material. There are many methods to measure the particle sizes of your material, such as: laser infraction, sieve pans, liquid suspension, etc. which provide the high, median and low-end ranges of the particle composition. The PSD (particle size distribution) is often measured by the D90, D50 and D10, the number corresponding to the percentage of material that passes through a certain sieve or mesh size.
Angle of Repose is another key indicator of how material will behave in a process. It is especially important when designing the slope angle on hoppers and bins.
Other key material factors include: toxicity (prevent operator exposure), abrasiveness (special linings or coatings on equipment), hygroscopicity (will the material clump up in humid environments), temperature (is the material hot or is it sensitive to higher temperatures) and moisture content. All these factors must be taken into careful consideration when designing a process line.
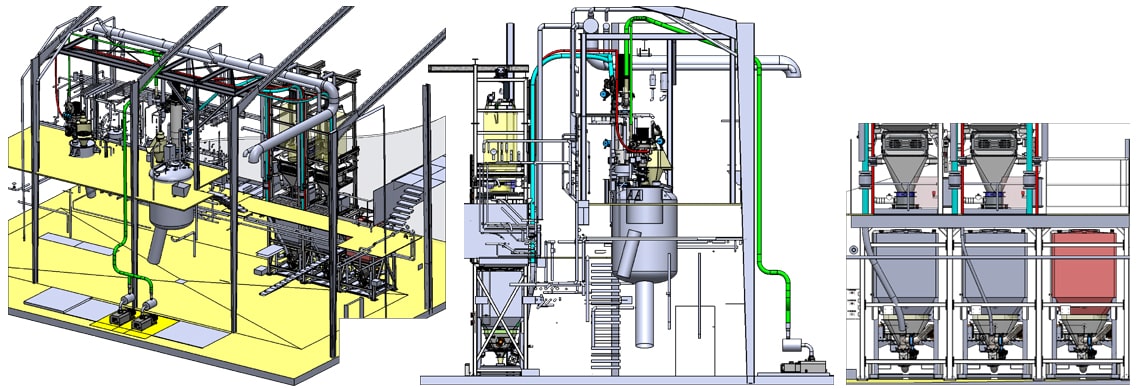
2. Defining production rates
All production processes have daily, weekly, monthly and yearly production goals. Typically, equipment suppliers of conveyor systems, mills, screeners, etc. need to define the capacity of the equipment by having an understanding of your facilities production goals.
Most equipment can be properly sized and designed by simply understanding the per hour production requirements at each stage of the process. For example, let’s say you need a pin mill to process about 10,000 lbs/hr of dry material. The process feeds material via bulk bags at 2,000 lbs each into your process line. Therefore, the bulk bag unloading station should be rated to handle a minimum 5 bulk bags / hr.
All downstream equipment should be designed to handle this capacity, with maybe some extra production increases factored in. That means your feeding equipment (rotary valves) conveying equipment (screw conveyors or pneumatic conveying systems), screeners, etc. should all be able to handle a rate of production at 10,000 lbs / hr. However, it should be noted that it’s never a bad idea to factor in unforeseen needs to increase production runs and allowing some extra capacity in these systems.
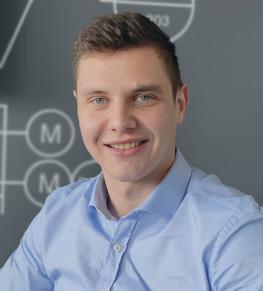
If your require further assistance,
I am at your entire disposal.
Loïc, powder expert
3. Material of Construction and Other Design Factors
Depending on the material being processed, most production equipment is offered in either carbon steel, 304 or 316 stainless steel. Typically, in the chemical and mining industries equipment suppliers can use painted carbon steel as the primary means of fabrication. The food & beverage industry usually goes with 304 stainless for hygienic requirements. Industries like pharmaceutical, cosmetic and dairy need to meet the strictest of hygienic standards and almost always use 316L stainless steel.
Once the main fabrication component is determined we need to then look at what polishes the surface grit needs to meet. You may be dealing with a sticky substance that clings to everything it comes into contact with. In instances of dealing with a powder that has bad flow properties, mirror polishes usually work best to keep the material from clinging to the sides of the process line. Grit finishes typically fall in the following categories: 120, 150, 180 and 240 as the higher the number the finer the polish. Bead blast, or 120 grit, is the typical standard finish if no special considerations are needed.
There are also other factors like electropolishing and passivation in order to take out the impurities and further enhance the polish and hygienic design of the equipment.
4. Know your hazardous area classification
One of the most important factors to consider is the explosivity of your material and process area. According to OSHA, “The National Electrical Code, NFPA 70, contains guidelines for determining the type and design of equipment and installations that will meet this requirement. Those guidelines address electric wiring, equipment, and systems installed in hazardous (classified) locations…
Hazardous Area Classifications often deal in either explosive dusts, vapors / gases and fibers regarding how often they are present during normal operation cycles. This safety measure probably receives the most attention, and rightly so. Serious injuries and accidents can be avoided if the proper measures are taken to correctly design the manufacturing process based on these ratings.
Within the powder processing industry, we are typically dealing with vapors or dusts, let’s define these groupings based on the NEC. Classification defines the explosive substance which is present in the atmosphere. The division deals with the frequency under which those substances are present in the environment, as well as the concentration of the substance. Finally, group specifically defines the physical properties of these substances.
For example, with classification I we are looking at flammable solvents and groups a, b, c and d. With classification II we are looking at explosive dusts and groups e, f, and g.
Learn more on atex certifications
It’s not simply enough to know how to receive, transfer and package your material without first understanding the processing equipment your plant needs in order to get a return on investment. It’s by changing the nature of the raw material that adds value to other potential buyers. For many powder manufacturers, the ability to mill / grind the powder into a finer particulate will add characteristics like solubility, consistency and improved quality.
One common example of adding value using mills is with confectionary plants taking granulated sugar down to an icing grade for the purpose of bakeries and candy producers. The same goes for dairy powder-based products, like infant formula. By grinding the powder to a fine consistency, the formula will more easily dissolve into water. There are many types of mills, such as: pin mills, air classifier mills, granulators, cone mills, ball mills, jet mills, etc.
All have a purpose within powder processes and produce varying results based on the coarseness or fineness required of the milled product. Mixing and blending equipment can be used to bring multiple ingredients together to create instant mix recipes for off the shelf use. There are many types of mixing equipment depending on the raw material and final results desired. Some examples include: ribbon blenders, conical mixers, plow mixers, double cone blenders, etc. Controlling the quality of your material can be achieved with screening equipment such as: centrifugal sifters and vibrating screeners. These sieves can eliminate foreign contaminants and out-of-spec material, generally recycled back to upstream process equipment for reclaiming and avoiding product loss.
With 30 years of experience, the staff at Palamatic Process is well versed in all stages of a powder production process: DISCHARGE - FILL - CONVEY - MIX - REDUCE - DEDUST - STORE - DOSE - CONTROL – SIEVE.
Contact one of our sales engineers today so that together, we can help achieve your manufacturing goals!