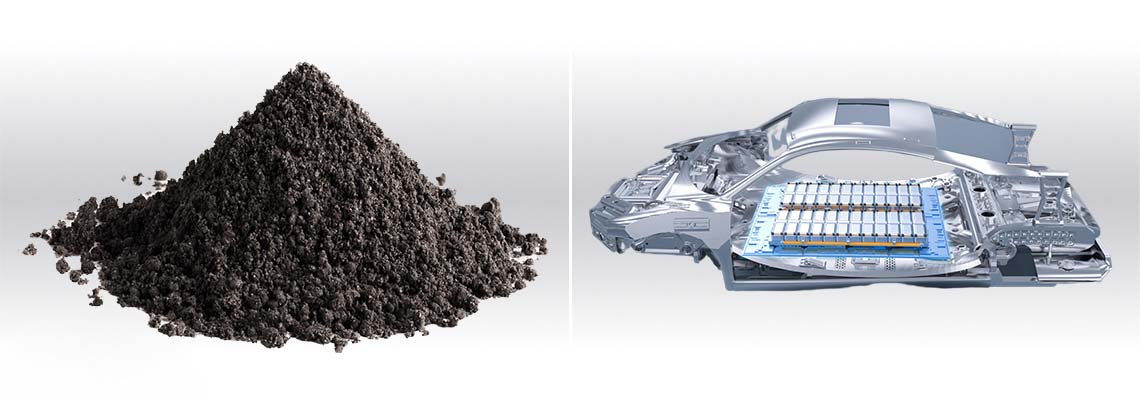
- 1. Explore the ores essential to battery manufacturing.
- 2. The importance of crushing and grinding in battery manufacturing.
- 3. Optimizing battery quality through magnetic separation.
- 4. Key steps in the purification of ores: Flotation, Leaching, Precipitation, Filtration, Calcination.
- 5. Reduction: The critical step in obtaining pure nickel and cobalt metals.
- 6. Electrolytic refining: The quest for ultimate purity for excellent batteries.
- 7. Palamatic Process: High quality batteries through careful mineral purification.
Battery manufacturing is an ever-evolving field, and the quality of the ores used plays a crucial role in their performance and durability. From initial crushing to magnetic separation, and techniques such as flotation, leaching, precipitation, filtration and electrolytic refining, find out how raw ores are transformed into high quality materials.
1. Explore the ores essential to battery manufacturing.
In battery manufacturing, it is essential to understand the types of ores used. The main minerals involved in this process are spodumene for lithium, pentlandite for nickel, cobaltite for cobalt, and hematite for iron.
Each of these minerals plays a crucial role in the composition of batteries, and their purification is a key step in ensuring optimal and sustainable performance.
2. The importance of crushing and grinding in battery manufacturing.
A crucial step in the battery manufacturing process is the crushing and grinding of the extracted ores. This step aims to reduce the size of the ores, making it easier to separate the metals from other elements. Through efficient crushing and grinding, it becomes possible to obtain high quality materials for the production of efficient and durable batteries.
3. Optimizing battery quality through magnetic separation.
Magnetic separation is a fundamental step in the battery manufacturing process. It allows the separation of certain minerals, such as hematite, using a magnetic separator. This device attracts magnetic particles and separates them from other elements present in the ore. Thanks to magnetic separation, it is possible to obtain high quality materials, which are essential for the production of high-performance and durable batteries.
4. Key steps in the purification of ores: Flotation, Leaching, Precipitation, Filtration, Calcination.
For the purification process of ores used for battery manufacturing, several key steps are implemented to obtain high quality metals.
First, flotation is a process that uses air bubbles to separate ore particles, such as spodumene, pentlandite, cobaltite and hematite, from other elements. The ore particles attach themselves to the air bubbles and rise to the surface of the liquid, allowing them to be recovered.
Second, leaching is often used for lithium, nickel and cobalt ores. It involves dissolving the metals in an acid solution, allowing them to be separated from the other elements present in the ore.
Once the metals are dissolved in the solution, the precipitation process takes place by adding specific chemical reagents that react with the metals to form solid precipitates.
The solid precipitates are then separated from the liquid by filtration, where the solid recovered is the purified metal, while the remaining liquid is called "leaching".
Finally, for some metals such as lithium, a calcination step is necessary. This process consists of heating the purified metal at high temperatures to remove remaining impurities and convert it to a more stable form, such as lithium oxide.
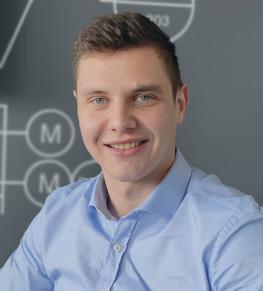
Do you have a project in the battery sector?
I am available to advise you.
Loïc, powder expert
5. Reduction: The critical step in obtaining pure nickel and cobalt metals.
In this crucial purification step, the objective is to remove oxygen from the metal compounds to obtain pure metals of exceptional quality. Reduction is achieved by exposing the metal compounds to specific conditions, such as high temperatures and the addition of reducing substances. The latter act involves capturing the oxygen present in the compounds, promoting the formation of pure metals. The reduction results in highly conductive materials of optimal purity, ensuring superior performance in the manufacture of modern, energy-efficient batteries.
6. Electrolytic refining: The quest for ultimate purity for excellent batteries.
Electrolytic refining is a key step in the purification of metals, achieving unparalleled levels of purity for demanding applications such as battery manufacturing. This sophisticated process relies on the use of an electrolytic solution in which the purified metals are dissolved. By applying a precise electrical current, the metal ions migrate to the opposite electrode, forming pure metal deposits. Electrolytic refining removes residual impurities and ensures the highest quality of metals used in batteries, thus ensuring optimal performance and extended life.
The time required for the purification of ores varies according to the type of ore and the method used. Machines used in the purification process include crushers, mills, magnetic separators, flotation cells, filters, furnaces and electrolytic cells.
7. Palamatic Process Canada: High quality batteries through careful mineral purification.
In conclusion, the purification of ores for battery manufacturing is an essential step to guarantee optimal and sustainable performance. The different techniques used, such as magnetic separation, flotation, leaching, precipitation, filtration, calcination and electrolytic refining, are responsible for obtaining high quality materials of exceptional purity.
Palamatic Process experts master the various stages of the process and use state-of-the-art equipment to meet specific customer needs. If you would like to know more, please contact our solution managers.