Description
DrumFlow® Liquid - Drum tipper for liquid or viscous products
The drum tipping DrumFlow® Liquid, manufactured in stainless steel, operates automatically by remote control to minimize and eliminate the need for heavy manual work by production operators. The operator does not have to hold the barrel during tilting, or remove the inner liner for cutting and opening.
The drum vacuum is equipped with a bag and drum clamping system (top of the drum) with a retaining rod (bottom of the bag) mounted on a pneumatic cylinder.
Operating mode:
- Placement of the full barrel on the clamping table.
- Opening of the bag and attachment to the collar of the barrel, by the operator.
- Startup of the automatic emptying cycle, once the operator has left the enclosure.
- Descent of the bag and drum clamping rod.
- Tilting of the drum in position 1: 150° - Most of the product is drained.
- Progressive tilting up to 180°. Complete draining of material.
- Return to the starting position of the empty drum.
- Lifting of the clamping rod.
- Release of the empty drum and installation of the new drum.
- Recovery of the discharge bag from the 1st drum for disposal through the rollers, while the second barrel empties.
DrumFlow® Liquid is available in 3 models: DrumFlow® Liquid 50, DrumFlow® Liquid 150 and DrumFlow® Liquid 300 with tilt differences ranging from 90 ° to 180 °.
DrumFlow® Liquid 50 | DrumFlow® Liquid 150 | DrumFlow® Liquid 300 | |
---|---|---|---|
Capacity - keg weight | 110 lbs | 330 lbs | 660 lbs |
Barrel height | 23.5" | 31.5" | 39.25" |
Diameter | 15.75" | 19.5" | 23.5" |
The drum discharging station consists of:
- A tilting cradle with electric motor
- A clamping system for the bag and barrel
- A receiving hopper
- Rolling mill
- A transfer pump
-
Rate4
Equipment advantages
- Tilting cradle with electric motor
- Bag and drum clamping system
- Equipment cleanability (CIP system possible)
- Minimized operator intervention
Media
View our equipment in videos
Basculeur fût liquide
View our equipment in photos
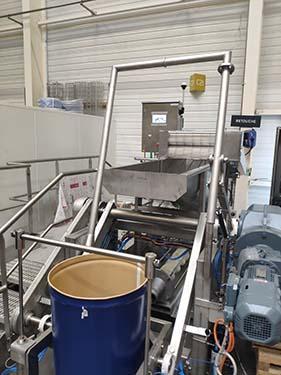
Raising the barrel for unloading.
Start of the automatic discharging cycle, once the operator has left the enclosure.
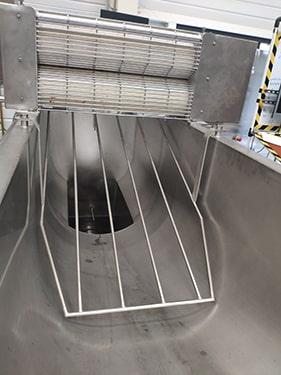
Roller Mill Empty Drum Hopper
Integration of a roller mill for complete emptying of the bag.
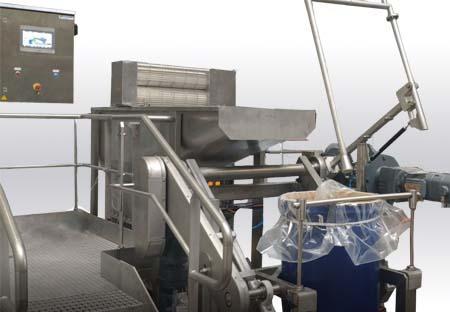
Automated drum discharge platform
Operator access platform to the drum tipper equipped with a railing.
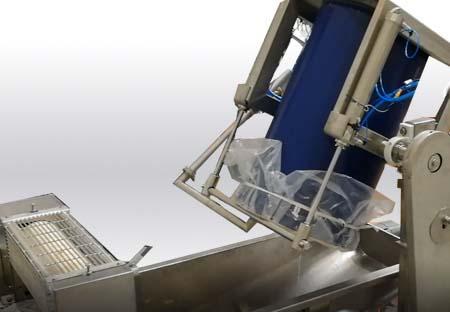
180 degree tilt of the barrel
Tilting the drum 180° to finish the emptying cycle.
Features
Technical specification
Transfer rate on viscous product: 7m³ / h
Transfer rate for non-viscous products: 15m³ / h
Product discharge pressure : 12 to 15 bars
Drum tipper with integrated:
- Completely removable bag holding bar
- Foot pedal with stainless steel protection
- Installation of a stainless steel protective cover to prevent access to the discharge hopper during the Cleaning In Place phase.
Safety enclosure:
- 304 stainless steel safety grid
- Light curtain
Case studies
CASE STUDIES WITH THIS EQUIPMENT
Packing of olives
Treated products: olives in brine - Packing of olives - The objective is the automatic emptying of the drums by turning the drums over.Food and Animal Feed