Description
Bag packing station PalSack®02 - Precision, gentle, containment
The PalSack®02 bag conditioner provides packaging of all your bags and sacks by precisely dosing your powders and fragile bulk products. This bagging machine incorporates a vibrating feeder allowing to dose all bulk products precisely and without causing particle attrition (respect of the granulometry, fragile, friable, dry products, etc.).
The standard bagging capacity of bags and sacks is between 10 and 60 lbs. The packaging rate can vary according to the options selected but can reach up to 100 bags/hour.
This semi-automatic bag filling system offers maximum flexibility for the precise packaging of fine and granular powders with a minimum footprint and a maximum level of containment.
The different possible configurations of the PalSack®02 model:
Ref. | Possible Equipment | Functions | Advantages | |
---|---|---|---|---|
Choice 1 | J | Inflatable seal | Dust tight bag connections | Maximum confinement |
M | Clamping jaws | Quick bag connections | Speed, ergonomic, installation and multi-format bags | |
Choice 2 | P | Support tray | Tension of the bag during filling | Hygiene, height adjustment for adaptability to multi-format bags |
C | Motorized roller conveyor | Holding and evacuation of the bag during filling | Ergonomics, increased speed | |
Choice 3 | Net | Net weighing | Provides accurate amounts of the packaged product | Accelerated rate (dosing in hidden time) / may require a double check weighing system |
Gross | Gross weighing | Weighing of the entire container and contents | Commercial weighing, traceability |
Our PalSack®02 packaging machine is configurable by modulating the possible basic equipment: choice 1 + choice 2 + choice 3.
Example of possible reference: PalSack®02-M-C-Gross.
-
Rate3
-
Fragile material5
-
Dosage accuracy5
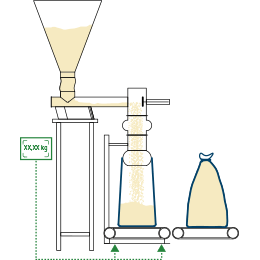
PalSack®02-J-C-Gross
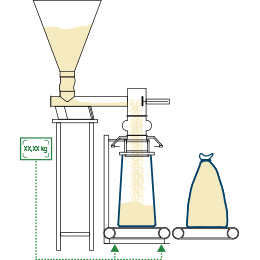
PalSack®02-M-C-Gross
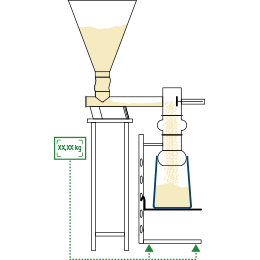
PalSack®02-J-P-Gross
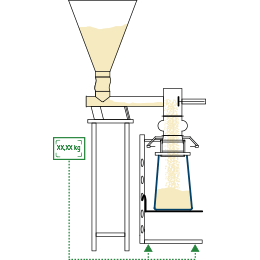
PalSack®02-M-P-Gross
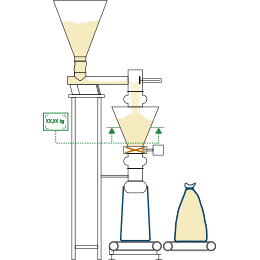
PalSack®02-J-C-Net
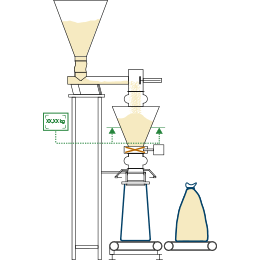
PalSack®02-M-C-Net
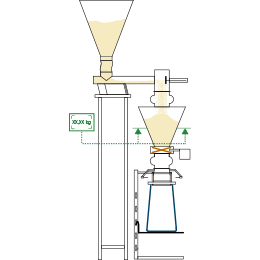
PalSack®02-J-P-Net
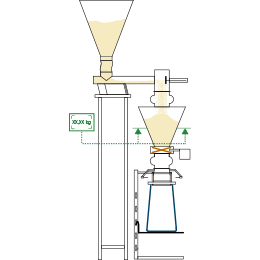
PalSack®02-M-P-Net
The semi-automatic packaging machine can incorporate a variety of options.
The speed of this semi-automatic PalSack®02 filler is perfect for small and medium production operations. It can dose up to 100 bags/hour (depending on the product, the container, the chosen dosing system, etc.).
Batch Labeling: in order to label the products after the filling operation is finished, several automatic and semi-automatic labeling machines can be installed.
- A wide range of available options makes it possible to adapt the semi-automatic filler to all your specific constraints:
- Packaging of products, food or chemical powders.
Example: dried fruits, sugar, semolina, rice, pasta, flour, spices, tea, salt, olives, fine powders, volatile powders, etc. - System management via touch screen
- Batch labeling with printer
- Any type of container: paper bag, plastic bag, multilayer bag, sachets, etc.
- Option for automatic loading of the product directly into the hopper (simplified cleaning version required) and reduced retention zones
- Adjustable and pre-programmed speed
Configurable weight The PalSack®02 bagging machine represents a scalable and modular packaging machine with the possibility to meet production demands requiring hygiene, precision, speed, containers, etc.
Equipment advantages
- Vibrating feeder
- Containment / sealing
- Versatility of the containers to be filled (bags, sacks, buckets, boxes)
- Multiple options: welding / sewing closure, conveyors, vacuum packaging machine, nitrogenization of food, vibration / densification, etc.
Media
View our equipment in photos
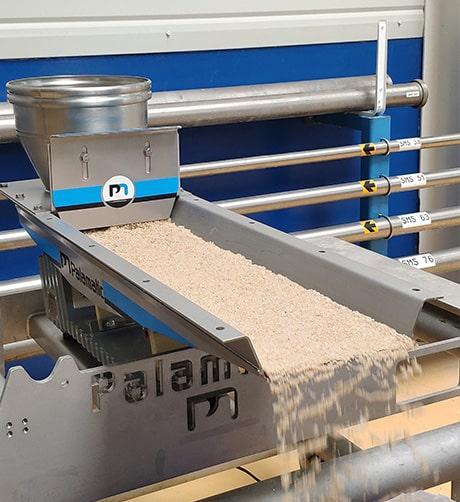
Vibratory feeder adapted to fragile products
The vibrating feeder allows the dosing of powders and granules.
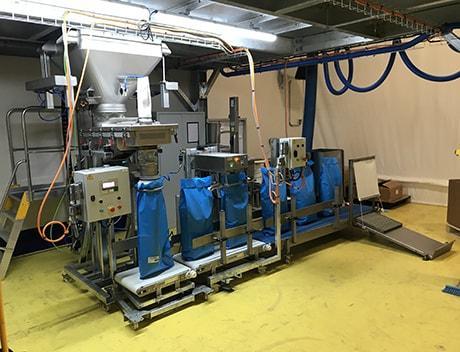
PalSack® 02 complete line
Complete line for packaging bags.
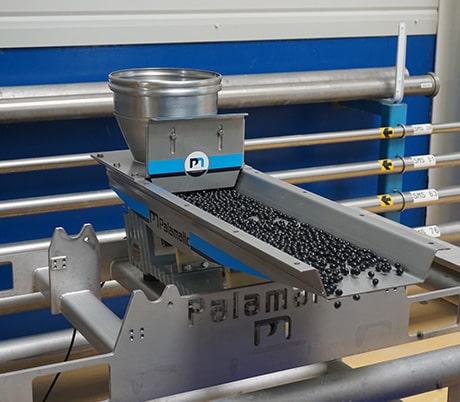
Vibration system for the respect of fragile products
The vibration allows the respect of the product (no moving parts in the vibrating feeder) on the packaging and handling lines of powders.
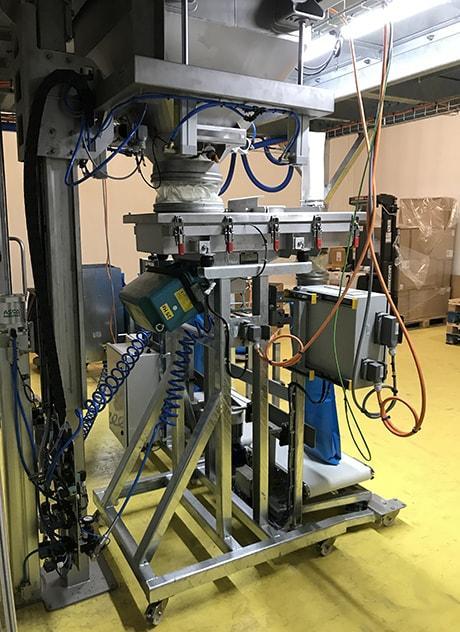
PalSack® 02 bag filling station
Bagging machine fed by a vibrating doser.
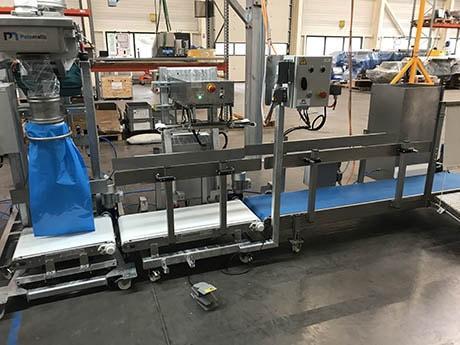
Bag packaging
The bag is held in place by a swelling seal.
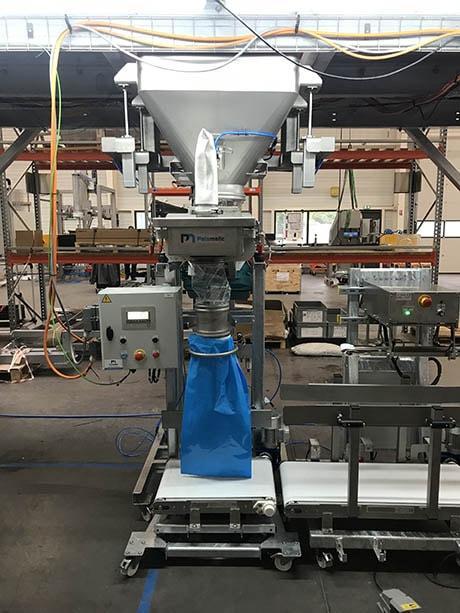
Filling head with a double envelope
Confined bag filling.
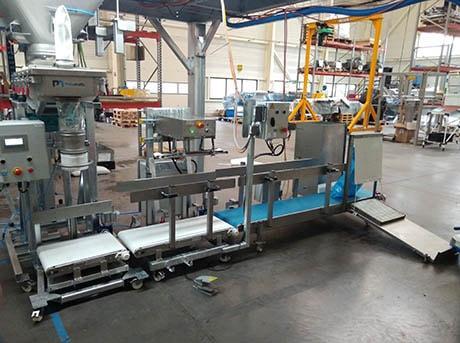
Conveyor on bag filling line
Line with belt conveyor for the evacuation of the bags after the filling phase.
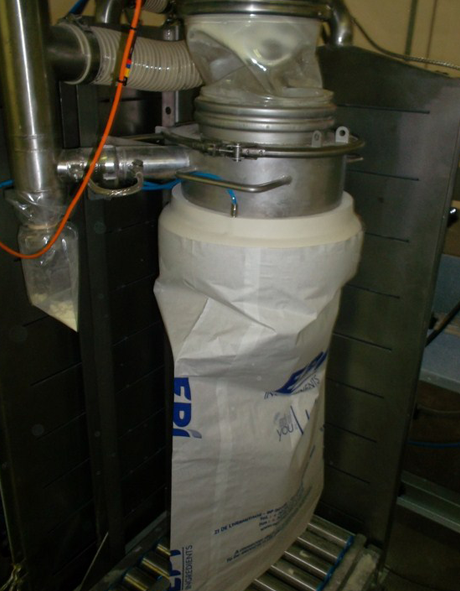
Bagging station for food powders
Bagging of animal meal on an industrial production line.
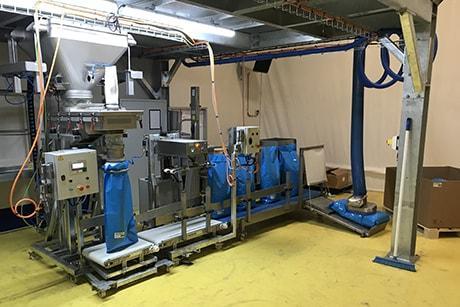
PalSack® 02 bag filler
Ensures the dosing of the products by a vibrating doser.
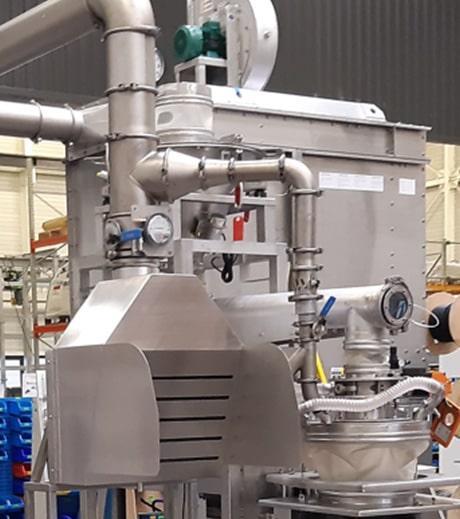
Packaging unit
Vibratory feeder for packaging feeder. The installation is equipped with a suction hood.
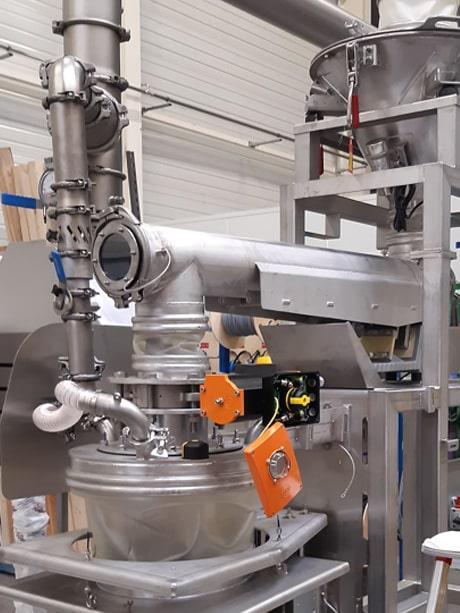
Filling station
The powder is dosed by means of a vibrating dosing unit.
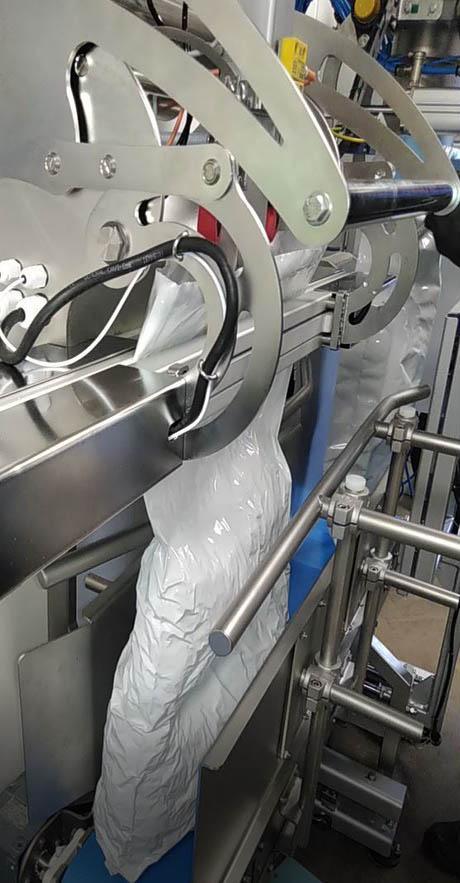
Palamatic Process powder bag sealing machine
The bag packaging line is equipped with a sealing system to ensure the containment of the packaged powder.
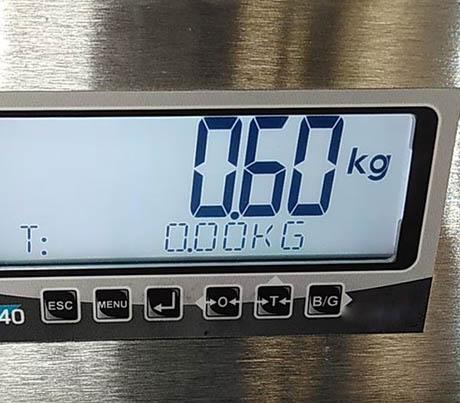
Weighing system on bag filling station
Industrial weighing system on bulk pigment filling line.
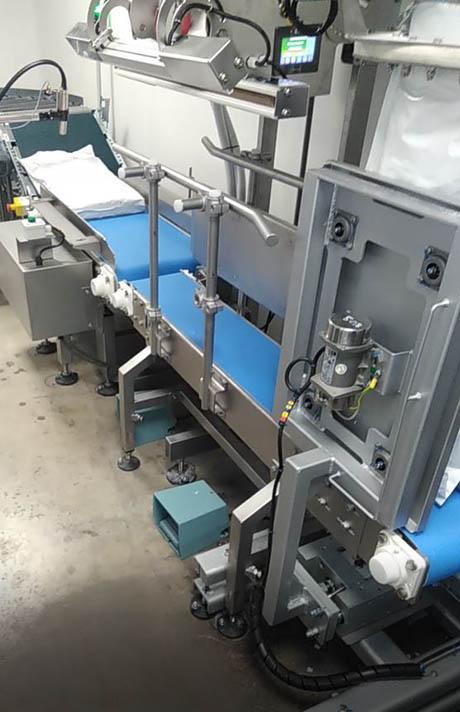
Bag filling line with belt conveyor
Conveyor and packaging line for flakes with sealing machine for bag closing.
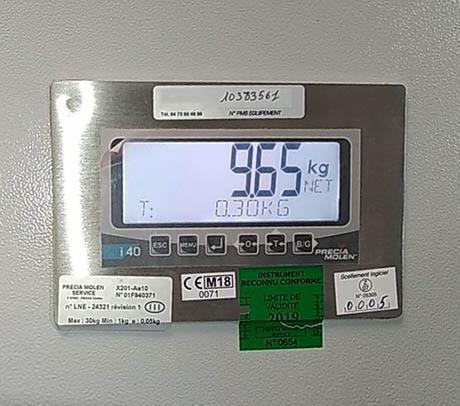
Commercial weighing on bag filling station
The bag filling machine is equipped with a weighing system that allows the gross weighing of the container.
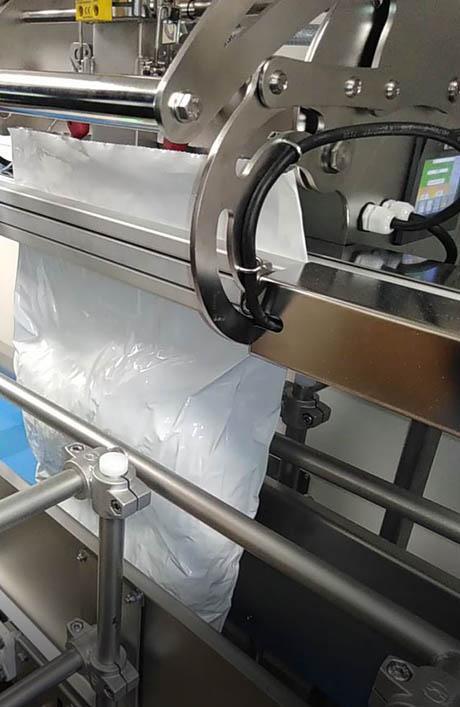
Sealing the top of the bag after filling
Impulse bag sealer for sealing the bag after the packaging phase.
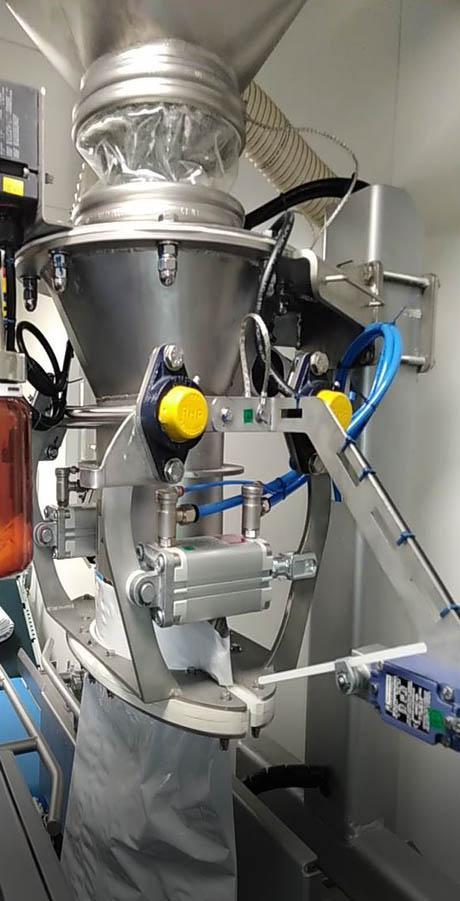
Feeding of the filling head
The bagging machine is fed with flakes via a butterfly valve installed on the buffer hopper.
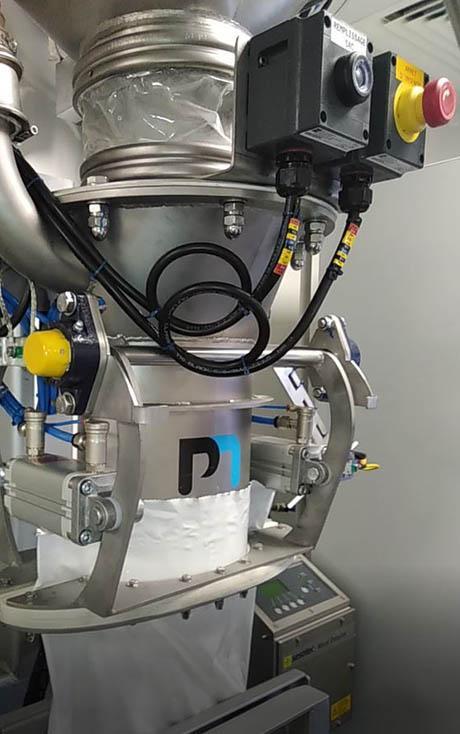
Bagging of powder
The bagging machine is fed via a flexible connection sleeve.
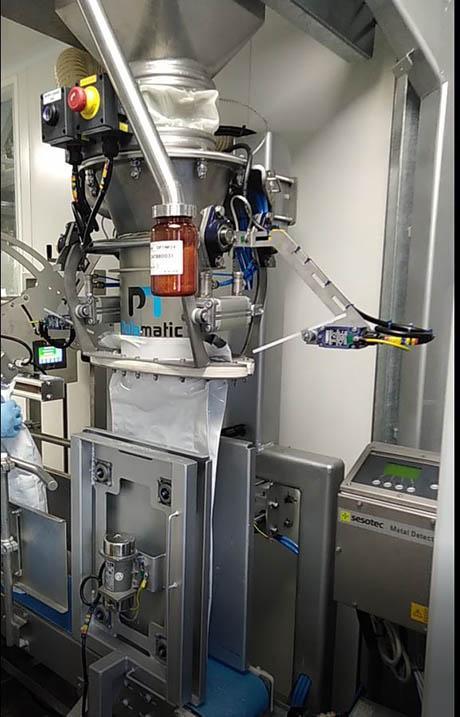
Bag packaging machine
A gravity metal detector guarantees a quality end product.
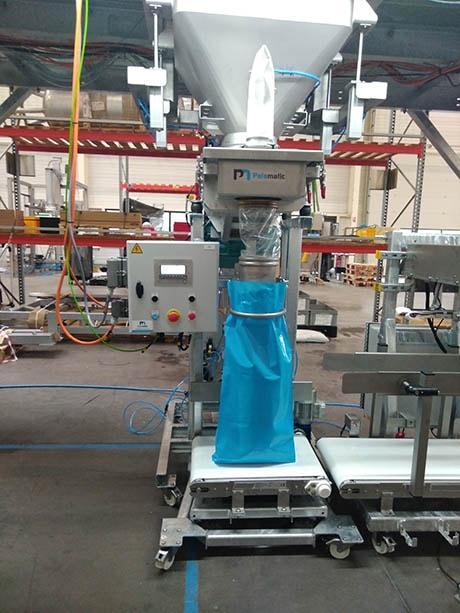
Bag filling head
Bag filling station downstream of a vibrating doser.
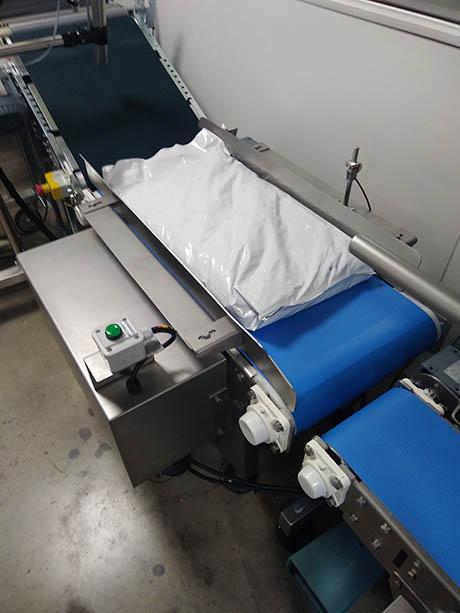
Bag packaging line with weight control
Conveying and packaging process of flakes in the petrochemical sector.
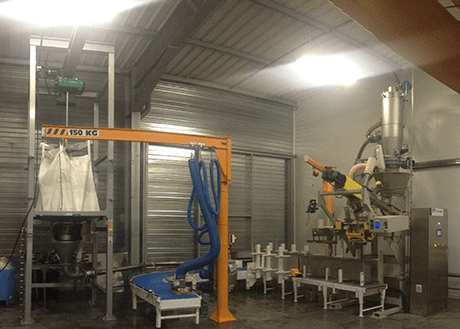
Process line: big bag unloading and bag filling
The bag filling station is fed by a big bag discharge station. Once filled, the bags are evacuated on a conveyor belt to be then palletized with a bag manipulator.
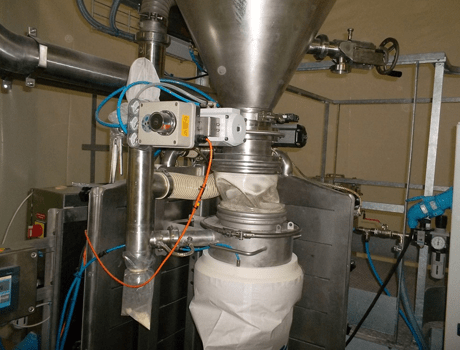
Automatic bagging machine
The upstream dosing device fills the bag. The volumes are balanced by the double envelope filling tube.
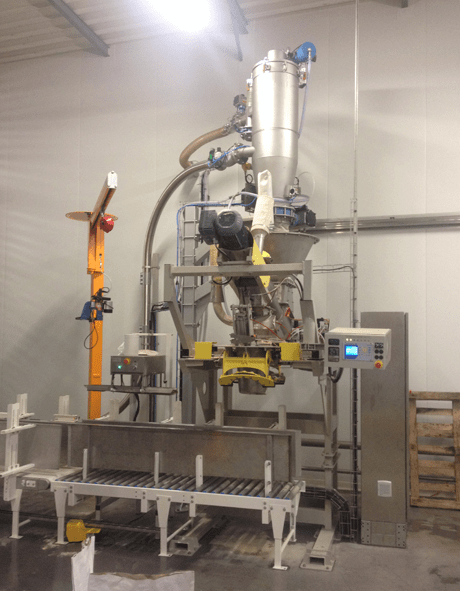
Bag filling station
The bag filling station allows commercial weighing of the bags which are then discharged on a roller conveyor.
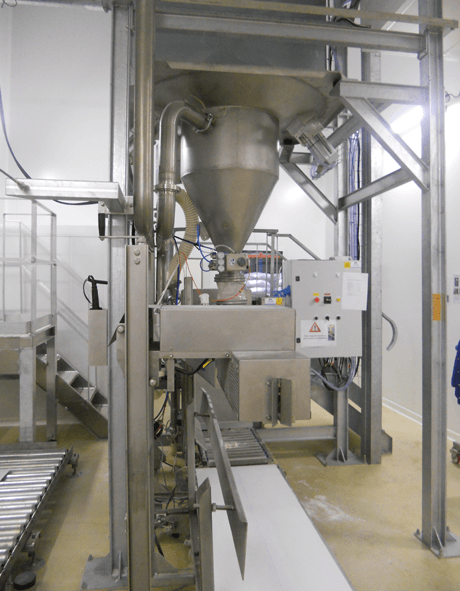
Bagging of food powder
Sugar bag packaging line equipped with a conveyor belt.
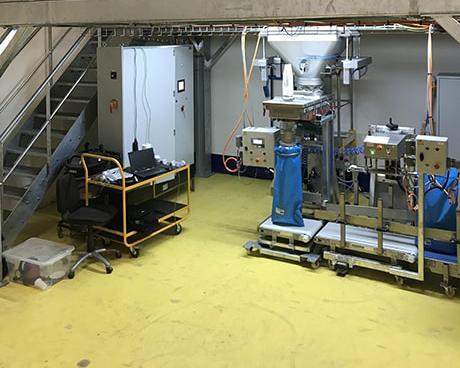
Packaging line for bags
Packaging line for powder bags.
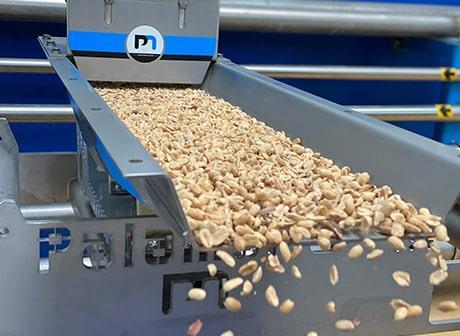
Industrial dosing
Dosing of peanuts on an industrial packaging line. The vibration allows the handling of fragile products.
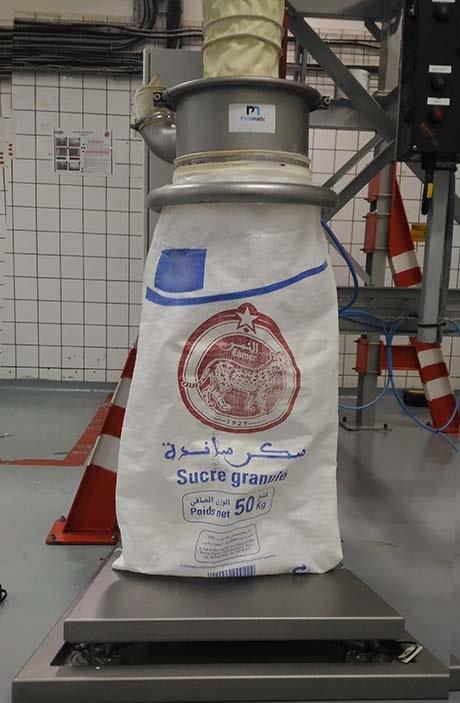
Baking line
Grinding unit for pure powdered sugar with bag packaging.
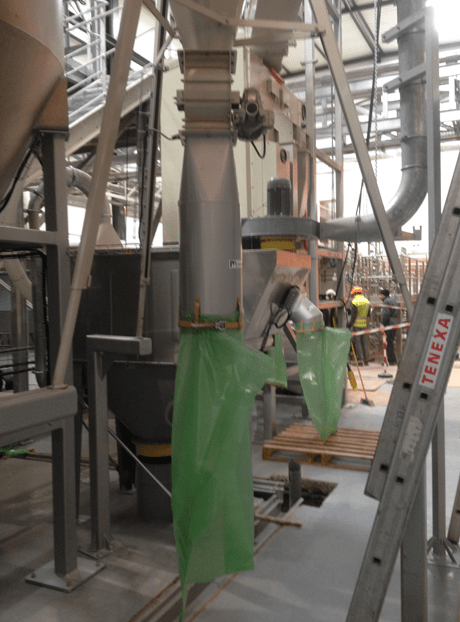
Manual bag filling station
Process line for mixing and packaging products for the petrochemical industry.
Features
The PalSack®02 semi-automatic bag filler incorporates the following features:
- Dosing hopper allowing buffer storage of powders / ingredients to be packaged. This buffer hopper can be automatically replenished by a preparation and production line.
- Vibrating corridor driven by an electromagnetic motor. Geometry of the vibrating corridor adjustable according to the products and the required hygiene constraints: tubular or trough vibrating corridor.
- Automatic closing valve for increased dosing precision. Accuracy less than 5 grams (depending on the type of product packaged). The pneumatic fall tail valve also offers optimized containment and a level of hygiene at the packaging station.
- Bag holding assembly: two standard versions are possible by inflatable seal or pneumatic clamping jaws. Maintaining the bags by an inflatable seal ensures containment for fine products, while the pneumatic jaw system is intended for granular products.
- Product weighing: The PalSack®02 bagging machine incorporates the weighing loop for controlling the vibrating dosing device. The Palsack®02 automatic packaging machine is available in two weighing configurations: net weighing and gross weighing.
- The net weighing version (LIW) integrates an intermediate weighing hopper. This hopper provides dosing of the product/powder before introduction into the container to be filled.
- The gross weighing (GIW) PalSack®02 packer integrates the weighing loop on the base, allowing the bag to be weighed and directly controlling the vibrating feeder.
- The net weighing version (LIW) integrates an intermediate weighing hopper. This hopper provides dosing of the product/powder before introduction into the container to be filled.
Options
Case studies
CASE STUDIES WITH THIS EQUIPMENT
Processing line for biscuit production factory
Processed powder: Crystal sugar - Line for biscuit factory - Food manufacturer that specializes in biscuits, chocolate and cocoa. The customer's process requirements involved the milling of granulated...Food and Animal Feed
Clean room for packing
Processed powder: milk powder - Clean room for packing - A leading dairy and manufacturer of high value-added milk powder for the leaders in the infant market.Food and Animal Feed
Mixing and packing of spices
Processed powders: spice mixtures (curry...), tea and herbal tea blends, fine salt - Spice blending and bagging - Bagging station for packaging spice and powder blends in bags from 1 to 25kg.Food and Animal Feed
Optimization of the processing of agglomerated dried fruit
Products processed: dried fruit and vegetables Disaggregation of a large volume of dried fruitFood and Animal Feed