Powder processed: wet ground powder
Automated drum dumper
Dumping and discharging of drums of wet ground powder at a rate of 40 drums/hour.
The full drums are conveyed on pallets of 4 to an unloading dock directly from the truck. The objective of the installation is to unload all the drums from the truck (300 units) to a workstation (maximum duration of the operation 8 hours).
An Atex certified drum manipulator with a capacity of 100 kg is mounted on a pivoting jib and is used to lift the drums from the pallet and position them on the dumper' infeed conveyor.
Once the full drum is positioned on the atex 22 motorized roller conveyor, the removal of the cover is done manually by the operator. An anti-slip system on the rollers prevents the drum from rotating when the cover is unscrewed.
An Atex certified rotating table controlled by a pneumatic cylinder in the mid-point of the conveying line makes it possible to carry out the 90° angle drive and rolls the drum towards the dumping station.
The installation of the drums on the dumping system is carried out automatically by the motorized conveyor chain. Photoelectric sensors located along the powered roller conveyor relay the position of empty and full drums to the system controller and ensure the right positioning of the drum.
The tilting movement being perpendicular to the conveyor chain, the tilter is equipped with a pickup device that permits the drum to be gripped from below through the rollers of the conveyor. The drum is placed above the device thanks to a cylinder that pushes it to the stop on the dumping system. The comb itself is mounted on a rail which allows its translation thanks to the piloting of an Atex cylinder; this system is intended to rim the drum against an upper capping cone and thus guarantee the tightness of the discharge chute on the drum during the dumping operation.
STARTING POSITION |
TILTED POSITION |
![]() |
![]() |
Position initiale
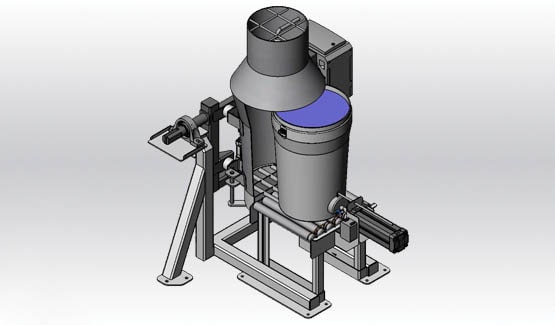
Position basculée
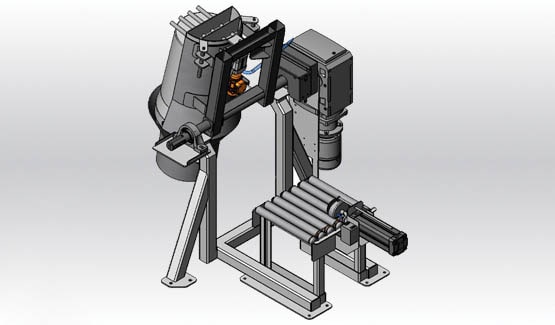
The system is fitted with sensors and positioning stops. Once the drum has been positioned and capped by the cone, the dumping cycle begins. The drum automatically tips over and the wet ground powder flows into the customer's tank. The tipping of the drum is automated and is carried out in complete safety, preventing the operator from coming into contact with the bulk solid. The dumping cycle consists of rotating the drum and the tipping platform. This tipping operation is carried out by a high-torque geared motor. The mobile assembly comes into contact with the rubber blocks provided for this purpose.
The drum rinsing by spray-ramp with clean in place nozzle is carried out above the customer's tank while the drum is always tilted to ensure that there is no powder left inside the drum. The tipper is then returned to the starting position. The empty container is then returned to its upright position by performing a reverse tilting movement.
The empty container is returned to its upright position on the motorized roller conveyor by means of a cylinder fitted with a pusher for extracting the empty container at the end of the conveyor.
The entire drum tipper is installed inside a safety enclosure that prevents any cycle start as long as the door of the enclosure is open. The containment option is required for hazardous materials. If necessary, it can be connected to a dust collection network.
The electrical control cabinet is located out of the Atex area.