Processed powder: Potassium Bi-Fluoride
Drum and bag handling in the nuclear sector
French multinational in the energy sector, working mainly in the nuclear sector.
Handled products:
25kg kraft paper bags with an inner liner
90kg drums with an inner liner
The installation consists of a contained sack manual discharging Sacktip® SE and a drum discharging system DrumFlow® 04.
These industrial systems are installed on an operator access platform.
The Sacktip® SE is a bag dumping system suitable for handling toxic and dangerous products. The sealed door with glove box ensures the total containment of the bulk material and the protection of the operators during bag opening operations. The front door is provided with glove rings. An automatic side door allows the bags to be introduced manually and the bag is opened by the operator using a cutting tool.
The ergonomic design of the manual bag emptying station ensures that the operator has an efficient and reliable workstation.
The parts in contact with the raw materials are made of 304L stainless steel.
The contained sack manual discharging Sacktip® SE is fitted with a CBU bag compactor. This empty bag compactor prevents the operator from taking out the empty bag, the first source of pollution in the workshop. Once the bags are emptied, the operator throws the bag into the side chute. it is then extruded into a polyethylene sheath held in tension by elastic rings.
The empty bag compactor is made of all painted steel.
The drums and bags to be unpacked are mounted on the platform via a lifting table. A vacuum lifting tube with a set of suction seals, with quick disconnect system, allows bags and drums to be handled and positioned on the emptying stations.
The bag and drum manipulator is mounted on a wall-hung bracket.
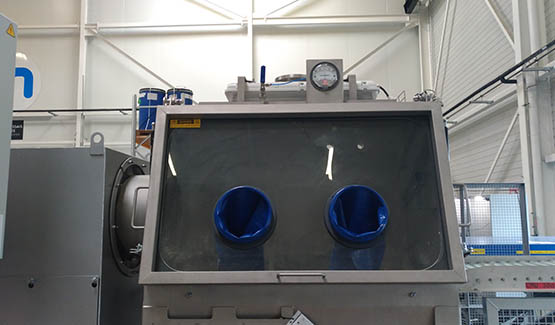
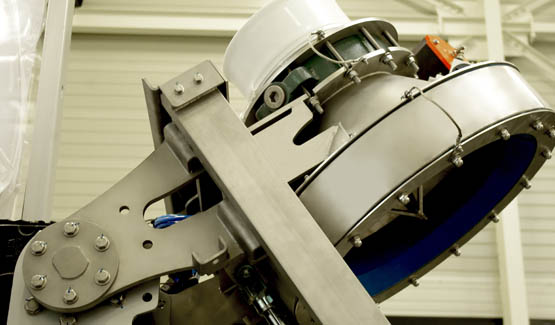
The complete drum tipper is located inside a containment chamber connected to the factory dust collection network.
The drums are dumped on an automatic DrumFlow® 04 drum emptying station. The emptying is carried out by turning it 180°. This DrumFlow® 04 emptying station is positioned in an enclosure made of painted steel with transparent EPDM panels. The drum turning-over cabin has 2 lateral openings on either side of the enclosure as well as a drum entry and exit door with slatted curtain.
The drums are installed by the infeed conveyors. Positioning stops are provided.
Once the drum is positioned, the operator can start the turning cycle. A step-by-step progress first positions the drum in front of the station allowing the cover to be removed. This consists of a glove box allowing the operator to safely remove the cover. The drum is then conveyed to the turning-over station, starting with the capping phase. The capping cycle consists of mounting the barrel as far as it will go on the capping cone. An inflatable seal ensures the tightness on the outside of the drum. The drum is then clamped between the dispensing tray and the capping cone. Bars attached to the cone penetrate into the drum to prevent the internal bag from turning over during turning. An isolation butterfly valve is installed at the outlet of the cone to maintain containment during overturning.
The drum + capping cone assembly can now be rotated 180°. This tilting is ensured by the second cylinder. The mobile assembly comes into contact with the rubber bumpers provided for this purpose.
Once rotated, the drum and its capping cone are vertical. An inflatable seal positioned at the outlet of the capping cone (under the butterfly valve) is placed in the stationary discharge manifold. The seal inflates to ensure a complete tightness before opening the butterfly valve.
Once emptied, the mobile assembly returns to its initial position by performing the 2 reverse tilting and untilting movements. The empty drum can be removed.