The installation is a complete turnkey line allowing the repackaging of dextrose from bulk bags into plastic drums or small, 90 kg big bags.
Initial constraints :
- Legal metrology packaging
- Dosing precision
- Cleanability
- Process safety and quality control
- Flexibility (plastic drums and small big bags)
In order to minimize product retention areas and facilitate cleaning of the equipment between batches, the design utilizes gravity transfer for the powder.
A bulk bag emptying station loading with an EasyFlow® EF1 electric hoist is installed on an extension structure allowing "step over" the packaging line. A maintenance platform with a staircase allows operators to access the big bag unlacing station. It also allows easy access for operators during maintenance operations. The big bag is securely opened using a Palamatic clamping head to minimize operators coming into contact with the product.
Once the big bag is opened, the dextrose flows via gravity through the vibrating screen / dosing units. Pneumatic massage cylinders complete the installation to solve flow problems in the big bag.
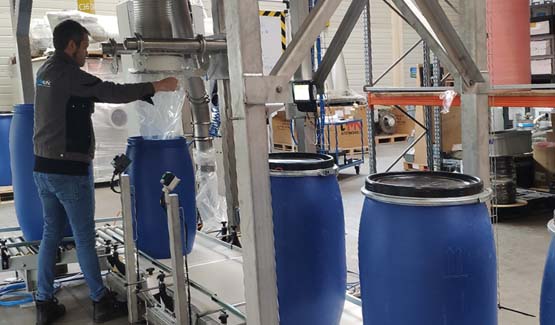
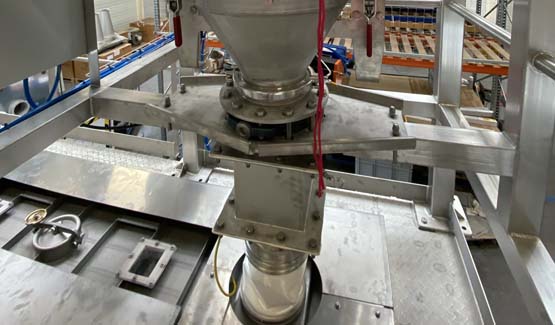
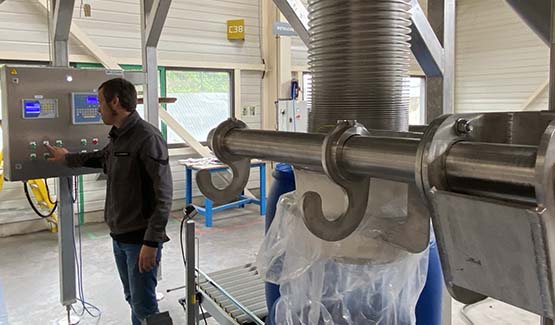
Still in the interest of easy cleaning procedures, Palamatic has pooled the screening and dosing systems. A vibrating feeder equipped with a removable mesh was installed at the outlet of the big bag discharging station. This allows the precise powder dosing (legal metrology) while providing a comfortable flow rate.
Contaminants collected by the mesh of the vibratory feeder are evacuated via an integrated collection bottle. The bottle is accessible from the ground conditioning station.
For the cleaning / maintenance phases, the clamping head as well as the screen and metering unit can be removed using the electric hoist of the big bag empty station. The packaging line, based on the model PalDrum® 03, has been designed with operational flexibility in mind. This process allows the packaging of both 150 kg plastic drums and small 90 kg big bags, in legal metrology.
A simple manipulation by the operator allows the transition from one packaging to another. For big bag packaging campaigns, the operator manually positions the forks in the station.
Since the heights of the containers are different, the station on which the big bag forks and the filling head are fixed, is fitted with a pneumatic cylinder. The filling head is removable and can be replaced by another head depending on the diameter of the container.
Once loaded, the big bag packing station takes on the same functions as a FlowMatic® 02 weighing scale.
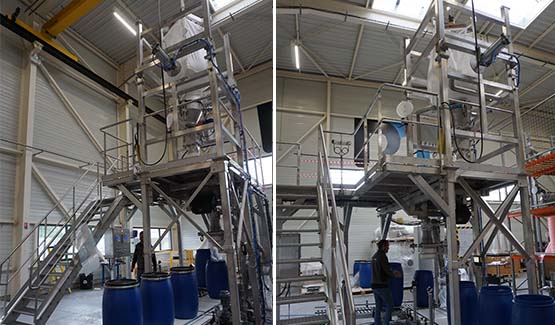
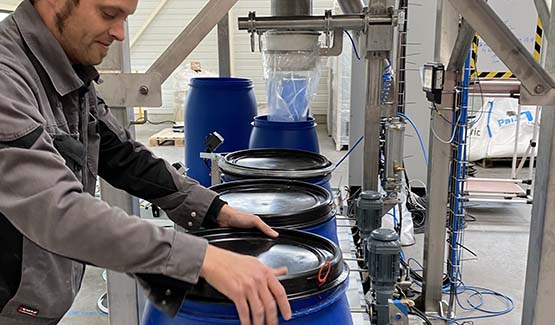
The ground conditioning line consists of 4 conveying portions. The assembly is mounted on casters to facilitate cleaning of the room:
- The first portion is used to supply the packaging station with empty drums.
This section consists of gravity roller conveyors and an automatic stop system. - The second portion is the belt conveyor mounted on the weighed conditioning station.
At this point, the weighing is not commercial. - The 3rd portion is a belt conveyor installed on the weighed control station with legal metrology.
- Finally, the last portion represents the storage area for the filled containers.
It is made up of two belt conveyors.
The entire line is controlled using a Pal'Touch® electrical cabinet fitted with an Allen Bradley PLC.
The whole installation is Atex 20/22.