Processed powder : Sugar
Ingredient loading
The installation consists of loading and mixing sugar in white wine at 59°F alcohol. The feeding rate of the sugar into the wine is 3 t/hr.
The sugar is delivered in 25 kg bags. The operator positions the bag on the shelf of the Sacktip® 800 manual bag dump station using a vacuum manipulator. The sack is then positioned on the screen above the powder discharge hopper. The volume of water in the hopper is approximately 100 liters. The operator cuts the bag and empties the product into the hopper.
The empty bag is evacuated through the compactor, which limits the volume of waste in a polyethylene sheath and contains any residual dust from escaping into the workshop.
This bag unloading station is equipped with a dedusting system which is clamped onto the structure. The dust collector is made of stainless steel and is integrated into the equipment. It allows the operator to work in a healthy atmosphere without dust pollution and loss of product.
This sack tip tray is designed to be mobile, so the electrical and pneumatic connections use quick clamps. The equipment is positioned on a frame fitted with sheaths to allow the assembly to be handled by a forklift.
Once poured into the hopper, the sugar is vacuumed into a powder incorporator which provides the in-line mixing of the sugar into the white wine tank, made of 316L stainless steel.
The liquid (wine) is then conveyed at a high rate from the bottom of the tank. Its passage through the body of the incorporator creates a venturi effect which allows the sugar to be vacuumed up. The specific technology of the wheel in the body of the device allows the shearing of the sugar for rapid mixing with optimal dissolution. The liquid obtained (mixture of wine and sugar) is then delivered to the head of the storage tank. The cycle continues until the sugar is completely aspirated.
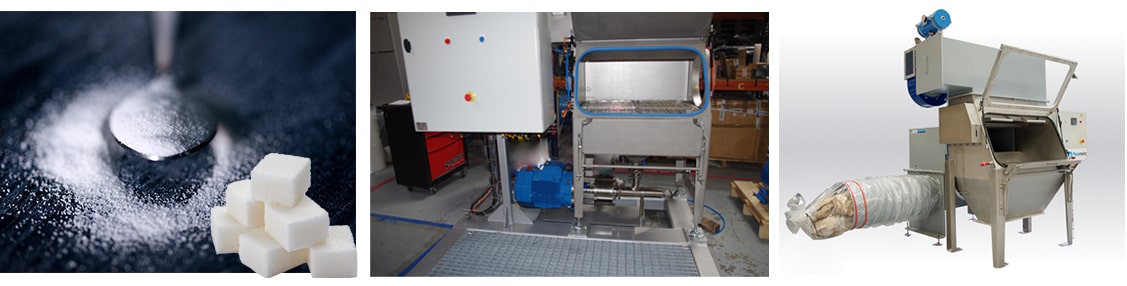