Introduction
UM Palamatic Process mills offer versatility and ease of operation. Due to the wide variety of raw materials, where every demand for particle reduction requires a tailor-made solution, industrial mills can be equipped with different grinding media. These easily interchangeable grinding tools allow a wide variety of milling applications.
The versatility of industrial grinders makes them very popular in various industrial sectors: pharmaceuticals, food processing, mineral powders, chemicals (fertilizers, pesticides, paints, pigments).
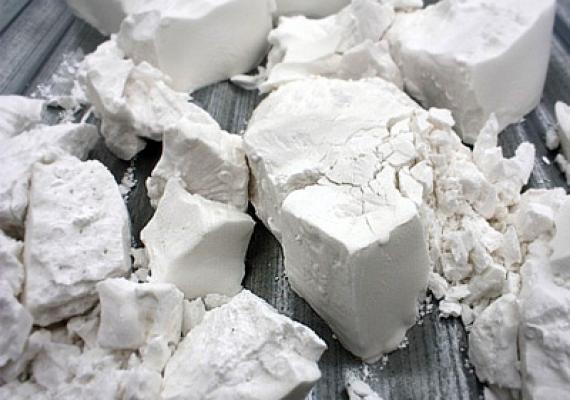
Characteristics of the materials to be milled
The behavior of a product vis-à-vis a grinding process, will be closely linked to the nature of its particles.
The choice of an industrial mill mainly depends on three factors that must be taken into account:
• the nature of the raw material: is it abrasive, oily, hard, brittle, elastic, heat-sensitive, hygroscopic?
• the particle size distribution (average size and variance) of the final product that we are trying to obtain
• the sizing of the industrial unit: quantity and / or flow
Also, the technical characteristics of the product to be ground which must be taken into account are the following: hardness, abrasiveness, adhesiveness, particle shape, angle of repose, toxicity, moisture content, product temperature, fat content, product temperature, bulk density, actual density, grain size, etc.
The following questions should be asked:
Can the product to be milled be extracted with solvents? If yes, which ones?
What is the desired final milled outcome (particle size distribution)?
Danger of explosion? Hazardous zoning?
What equipment is installed upstream of the mill?
What equipment is installed downstream of the mill?
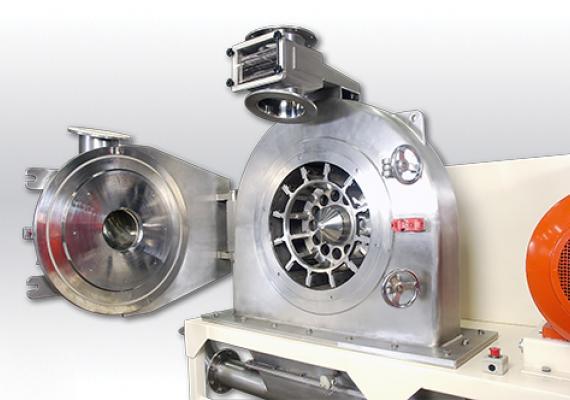
The elements for choosing a milling technology
Should you opt for a hammer or knife mill? The choice of mill will depend on the nature of the material to be milled, its hardness, its size and especially what you will do with it once reduced.
The choice of grinding technology is made in two stages. First, it is necessary to determine the suitable types of grinders taking into account the target particle size and the hardness of the materials to be milled.
Next, it will be necessary to determine which grinding tools are suitable for this same application: pins (with or without screen), hammers (fixed or mobile) or even knives.
The tools available
Pin Mill
The pin mill uses for a grinding chamber a rotating pins disc and stationary pins which enables fine powder grinding. The large grinding chamber can even mill materials that tend to clog. The fineness of grinding can be adjusted by changing the speed of the spindle rotor as well as the feed rate. The centrifugal forces acting on the two discs allow, among other things, to micronize wet, greasy or sticky products.
The use of pin modules with large chambers can also in some cases act as a heat sink, and therefore process temperature sensitive products, such as cocoa powder. The cocoa must be cooled via a "cryogenic" system. The product is then made brittle by injecting liquid nitrogen.
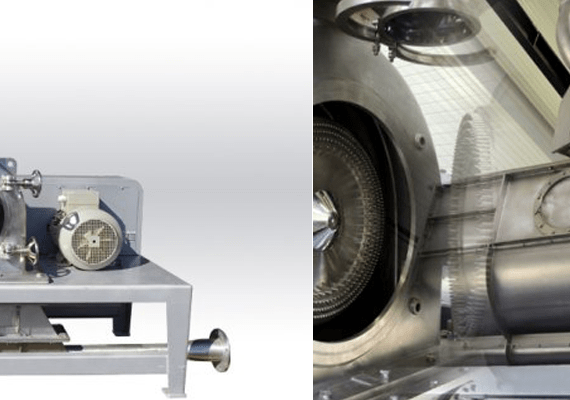
Hammers
The hammer mill allows the grinding of all types of cereals and dry products. Gravity feed into the crusher inlet can be done manually, mechanically or pneumatically.
Robust, easily modular, relatively simple to adjust and maintain, they are often found in the upstream phases of manufacturing processes where they serve as pre-treatment of the raw material.
Knives
The knife mill is used, for example, for soft, fibrous or temperature sensitive materials such as wood chips, cardboard, plastic, hollow bodies, hay, straw, etc.
In a knife mill, the sample is fragmented using the scissor cutting principle, between the rotor blades and the fixed knives of the grinding chamber, into smaller fragments until the final particle size is reached.