1. Basic Principles of Bulk Bag Handling Equipment
What is Bulk Bag Handling Equipment?
Industrial equipment that lifts, moves, fills or unloads FIBCs (flexible intermediate bulk containers) is known as bulk bag handling equipment. This bulk bag equipment (also called super sacks) is typically used at the start or end of the production process to either feed bulk materials to the pneumatic conveying system, or to be packaged and palletized for shipping.
Bulk bags are commercially produced fabric bags for storing and moving dry, flowable materials. Examples include sand, grain, fertilizer, and granulated sugar. Various industries use them for many applications, including some pneumatic conveying operations which heavily rely on bulk bag handling.
Bulk bag equipment is used in a variety of establishments, such as construction, industrial manufacturing plants, commercial agriculture facilities, food & beverage facilities, pharmaceutical production, and many more!
2. Material Handling Logistics
In the supply chain, the purpose and location of bulk material handling equipment determines the categories and processes into which it is applies. Transportation, storage, loading, and retrieval are among the various operations. Various highly constructed and well-designed control systems are used as material handling instruments in modern material handling.
In bulk material handling, a wide variety and methods of instruments and apparatuses are used to move items, supplies, and materials effectively. Hoists, cranes, and conveyors that transfer materials and bulk containers inside a facility between processing applications, production zones, and packing facilities are a part of this group.
Forklifts, hand trucks, and pallet jacks, which have closer contact with material transportation, also assist in these procedures. The speed that bulk materials and raw ingredients are metered into the processing facility can greatly impact the quality of a production or manufacturing process.
The goods being manufactured, as well as the location to which the necessary goods must be delivered, will dictate the method deployed. The use of technical instruments in modern production includes automated systems and processes and numerous feeder types designed to precisely deliver bulk materials into the super sack or production process.
The warehouses, where products are received and prepared for shipping, is typically what comes to mind when people define or think of material handling. One of the more important sections of material handling, such as components and tools, machinery, and control panels help to streamline and simplify different parts of the industrial process.
Weighed hoppers, screw feeders, pallet stackers, roller conveyors, sensors, and access platforms are all essential for bulk bag handling. Truck loading and unloading are done with the help of mobile roller conveyors, which can be moved around and placed in various locations.
The process of moving bulk materials that need equipment to transport such as cement, cereals, gravel, sand, and other kinds of granular or powdered bulk materials is known as material handling.
Each type of bulk material handling equipment, such as screw conveyors, hoppers, lump breakers, bag dump stations, and rotary airlock valves are all made to handle a particular material.
Every manufacturing, industrial, and commercial organization has a technique for keeping track of what is available and what is needed while storing its raw materials. Warehousing, a crucial component of storage, is a carefully managed and controlled component of bulk production systems.
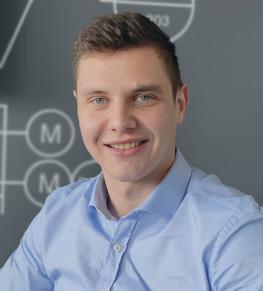
Looking for a bulk bag handling equipment? I am
available to advise you in your study.
Loïc, powder expert
3. Methods of Bulk Bag Handling
Bulk bag fillers, bulk bag unloaders, and bulk bag conditioners are a few of the several types of bulk bag machinery.
Bulk Bag Unloaders (or Bulk Bag Dischargers)
Bulk bag unloaders, also called bulk bag dischargers, efficiently discharge powders or other dry bulk materials from super sacks that were used to store or facilitate the transportation of various manufactured bulk solids (sugar, cement, salt, titanium dioxide, etc.). A mechanism known as a bulk bag unloader is designed to efficiently and safely unload jumbo bags of bulk materials. Bulk bag unloading systems are widely used in industries handling ingredients in the form of powders and bulk solids. These emptying installations make it possible to considerably reduce the number of manipulations by production operators.
The bulk bag unloading system is also the initial point of contact between the operating staff and the raw ingredients. Therefore, bulk material handling safety begins with the bulk bag unloader regarding the industrial operation. When bags are removed from storage, bulk bag unloaders are useful because the material may have become packed and agglomerated over time, causing challenging flow and unloading issues.
Due to their enclosed, tubular construction, bulk bag emptying stations provide dust-free material handling and are frequently used for feeding material, including polymers, cement, soda ash, magnesium oxide, and hydrated lime, into a production process. Bulk bag unloaders are beneficial for a variety of materials and can be designed to accommodate a variety of FIBC sizes and types, including lined, unlined, polypropylene, mesh, gusseted, and valve bags.
Bulk bag unloaders are frequently used in the construction, commercial, foundry, mining, and pharmaceutical sectors as a safe and affordable method of unloading bulk bags.
Depending on the application, production rates and design requirements, several accessories can be added to bulk bag dischargers. These bulk handling stations typically are made of a frame, a hopper, bulk bag support tray, hanger connecting to the bags handles, and an outlet chute. Although there are numerous frame designs for bulk bag unloaders, the most prevalent are forklift and chain hoist styles.
Forklift-style Bulk Bag Unloader/Discharger
Bulk bag unloaders that can accommodate forklift loading and unloading contain pockets that make it simple for a forklift to put bulk bags into the bulk bag unloader. Because it does not require an upper framework for placement, this form of a super sack unloader is often shorter than a chain hoist-style design.
Hoist-style Bulk Bag Unloader
Hoist-style bulk bag unloaders are a popular option amongst many production facilities. Much like a forklift would be used to load bulk bags, a hoist-style bulk bag unloader operates in the same fashion. The material can be efficiently discharged for additional processing or longer-term storage with the added safety of the hoist method. By integrating an electrical hoist that enables an operator to lift, position, and support the super sack for loading, a chain hoist-style bulk bag unloader makes it possible to load the bags without using a forklift. Large bags of bulk material can be swiftly and effectively unloaded with bulk bag unloaders. These goods are used in numerous industries, including mining, chemical, and food production.
Food and Pharmaceutical Bulk Bag Unloaders
Several bulk bag unloader equipment suppliers have developed a new design, primarily for the packaging and processing operations of the food and pharmaceutical industries. These unloaders meet most national and international hygiene standards.
Automated systems, which maximize uptime availability in the food and pharmaceutical processing and packaging centers, is used to achieve this. These devices use a touch screen controls for system-wide processing, communication, reporting, sensing, and monitoring. Instant connections with UL panels are possible because of high-speed Ethernet connections. Because of this we improve the unloader's efficiency and avoid costly errors.
The design and sophisticated controls work in sequenced time to allow factories to unload their materials in a clean environment with minimal operator intervention. This streamlines the manufacturing process and can help factory owners save time and money. A food production facility can increase production rates and reduce expenses by using this style of super sack unloader.
Rail Car Unloading
A rail car unloading system typically uses a pneumatic conveying line to unload and convey material to a storage vessel. The system typically uses a vacuum cylcone filter with a vacuum pump. A rotary valve feeds product into the conveying line to provide a crucial balance between conveying air and material load. The rail cars can have a holding capacity of 3,500 to 5,500 cubic feet in volume. They can typically transport bulk material up to 120 tons at a time.
Depending on the rail car type, the unloading system must be cost-effective and efficient to balance out the high operating costs of these rail cars. The high operating costs are due to the very large blower packages used when pneumatically unloading. This high cost would also include ongoing maintenance.
Bulk Bag Fillers
These devices are made to weigh and fill bulk bags. Manufacturers can add vibrating trays to filling systems to promote material densification and stability of the bulk bag. To improve flow, they can also set up conveyors, pallet dispensers, and automatic hooks.
Bulk bag fillers for companies like Palamatic Process, can provide various configurations to satisfy the price point and capacity demands of each customer's application. Each of these configurations can offer the best performance within particular capacity ranges at the lowest possible cost. They are intended for low to high production applications, placing the fill head close to the operator at floor level for quicker, safer, and simpler bag hookups.
Each of these designs fulfills a particular range of bulk bag filling applications and may be customized with performance upgrades to precisely meet any needs at the lowest possible cost. Successful bulk bag filling can be sourced according to basic, low-cost fillers to automated, high-capacity systems.
Palamatic Process has developed a range of bulk bag filling equipment and FIBC loading machines.
The FlowMatic® big bag filler series is offered in several different types of configurations and allows you to easily load and store your powders and bulk materials. Whatever the demands of your process, from manual to automated loading and storing requirements, Palamatic Process can offer the right equipment for every application.
Bulk Bag Filler Systems
Regardless of the properties of the process material, bulk bag filler systems are designed for high-performance operation in bulk material processing and packaging applications. These applications often involve repeatable and consistent cycles, rates, accuracy, and equipment effectiveness. Integrating the controls and automation systems throughout the equipment creates a unified construction and controls infrastructure. The operator's experience with the system is improved because of this, which also offers more thorough and useful performance data and lowers the total cost of ownership.
Construction materials and design requirements allow bulk material processing operations to run production at intended rates. When designed properly, the plant can run these systems without worrying about unscheduled downtime, inaccurate filling, or additional labor costs that come with underperforming big bag filling systems.
When filling bulk bags, drums, cartons, totes, or other bulk containers, bulk material filling systems allow processing and packaging operations to run at, or beyond, planned uptime, throughput, and quality standards. Bulk filling systems can be made to withstand harsh process conditions and handle extended run time cycles. Additionally, integrated automation controls capabilities deeper into equipment operations to give more thorough data reporting. Process-integrated dry bulk filling systems offer a whole process advantage by producing precisely filled, stable bulk bags and containers, eliminating material loss, and enhancing worker safety and productivity.
Bulk packing operations benefit from the performance and precision of bulk bag fillers. Because of their robust design and automation, bulk bag fillers assure processors that their packaging operation is an integrated system of their upstream process, while also delivering dependable and repeatable packaged quantities. While maintaining accurate fill volume and weight accuracy, a filling station can be designed to accommodate a variety of container types, including totes, cartons, and even bulk bags.
4. Bulk Bag Equipment Applications
Feeding a production line, filling a silo, loading a mixer or truck, packaging for resell, weighing, batching, and dosing systems are a few examples of big bag unloading applications. May industrial applications, including pneumatic conveying operations, heavily rely on bulk bag handling operations.
Advantages of Bulk Bag Handling Equipment
The advantages of bulk bag handling equipment include:
Minimized operator intervention
Less labor is required to do this activity because bulk bag handling equipment can collect and distribute material into processing lines, which is a big advantage for facilities with limited worker resources.
Reduces Dust and Product Loss
Bulk bag handling equipment provides dust-free discharge that seals in powder ingredients, reducing product loss during dispensing and improving worker safety and comfort.
Improves Sanitation
Bulk bag handling equipment is also intended to enhance hygiene. For example, the bulk bag unloaders from Palamatic Process have a special design that allows a telescopic tube to clamp onto the bulk bag discharge spout. This allows a secure connection while also promoting flow from the bulk bag. All contact surfaces can be made from food grade materials.
Boosts Productivity
Since bulk bag unloaders handle the heavy lifting, operators may effortlessly load, tie, untie, and remove bags without having to reach into awkward or hard-to-reach spaces. Unloaders also include user-friendly control screens that are simple to understand by the operator.
Customizable Designs
Bulk bag handling equipment has a modular design that makes it simple for the OEM to customize to unique requirements.
Equipment Durability
The stainless steel and carbon steel designs of bulk bag unloaders offer a robust, long-lasting solution for discharging bulk items.
Other advantages:
- Prevents product waste and spills
- Gathers product dust
- Effective and secure handling of bulk bags
- Prevents product tampering
- Automated product management
- Formed of stainless steel and mild steel
Palamatic Process has been supplying the powder and bulk solids industry with bulk bag handling equipment since 1992. In order to determine what solution is best for your project, contact one of our sales engineers. Together, our team of experts can provide the right kind of powder filling equipment that will fulfil your every production goal.
Contact one of our experts today for assistance with needed material handling solutions and to request a quote.