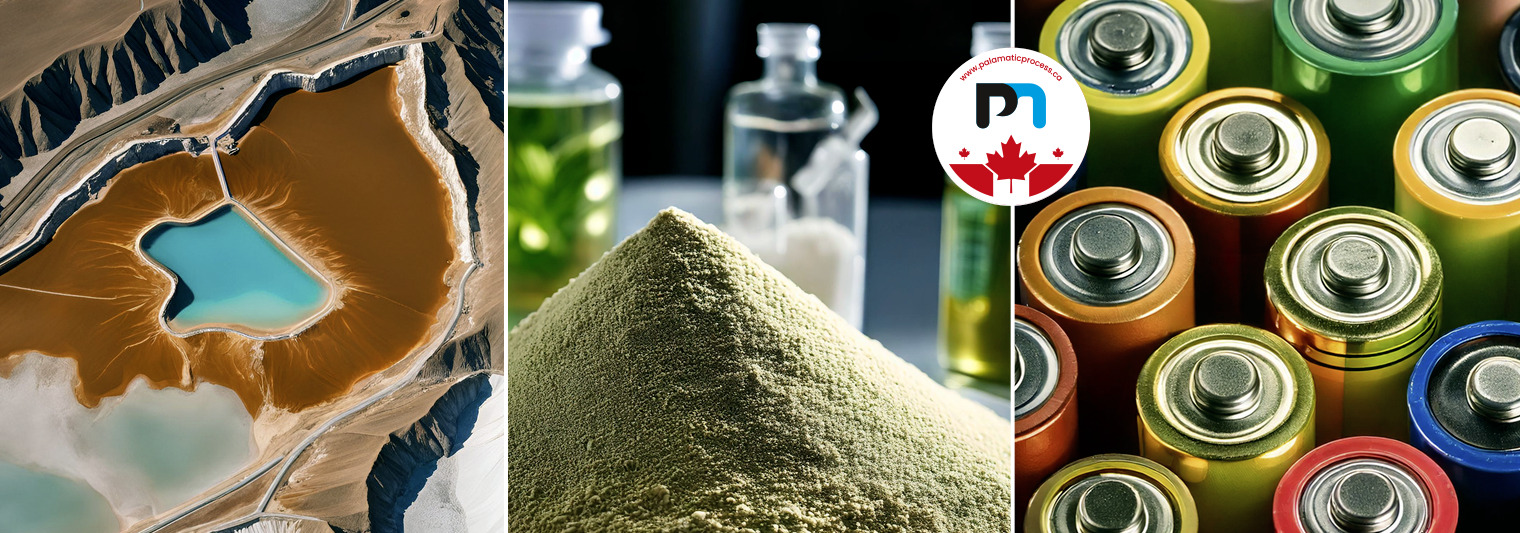
- 1. Addressing geopolitical and economic challenges in strategic raw material sourcing.
- 2. Producing high-purity sulphates: a meticulous and rigorous process.
- 3. Mastering filtration and filter cake extraction to optimise production.
- 4. Converting sulphates into hydroxides: a key step for high-performance batteries.
- 5. Blending hydroxides for PCAM: ensuring uniformity for high-performance batteries.
- 6. From PCAM to CAM: the importance of thermal calcination.
An industrial revolution driven by innovation
Lithium-ion batteries have become indispensable across various applications, including electric vehicles, renewable energy storage, and electronic devices. Their success is built on a smart combination of cutting-edge technology and highly optimized industrial processes.
Each stage of production — from raw material extraction to their final transformation into active electrode materials — is critical to ensuring the quality, performance, and longevity of batteries. These steps involve logistical, chemical, and technical challenges that require advanced expertise.
Gigafactories are at the heart of this energy revolution, managing sophisticated operations that start with the strategic sourcing of raw materials. Reliable partnerships with suppliers ensure a steady supply of lithium, cobalt, manganese, and nickel — essential elements in lithium-ion battery production.
Addressing geopolitical and economic challenges in strategic raw material sourcing
The geopolitical and economic context
Sourcing raw materials for lithium-ion battery production is a complex task marked by significant geopolitical and economic challenges. Critical materials like lithium, cobalt, nickel, and manganese are concentrated in specific regions, making their extraction and availability particularly challenging.
Key materials and the role of major players
- Cobalt: The Democratic Republic of Congo (DRC) produces approximately 70% of the world’s cobalt. Political and social stability in the DRC is critical to maintaining a steady supply.
- Lithium: Known as the "white gold" of the energy transition, lithium is primarily sourced from South American salt flats (Chile and Argentina) and Australian mines, which together control over three-quarters of the world’s known reserves.
- Manganese: South Africa and Gabon are major suppliers, requiring strong collaboration to ensure consistent deliveries.
- Nickel: Indonesia, now the leading global producer of nickel, introduces additional complexity to the supply chain.
Industrial strategies
Manufacturers address these challenges through several approaches:
- Diversifying supply sources to reduce dependency on specific regions.
- Establishing direct partnerships with producers to secure resources and minimize geopolitical risks.
- Investing in recycling: Advanced recycling technologies decrease reliance on virgin resources while reducing environmental impact.
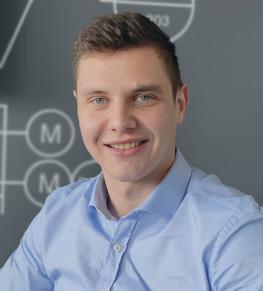
Do you work in the battery industry and have a powder handling project?
I'm available to discuss the subject with you.
Loïc, powder expert
Producing high-purity sulphates: a meticulous and rigorous process
After extraction, raw materials must be refined into intermediate compounds like nickel, cobalt, and manganese sulfates: essential precursors for electrode manufacturing.
The chemical process
In specialized reactors, ores are dissolved in sulfuric acid, often with oxidants to enhance reactivity. Temperature and pressure are meticulously controlled to maximize conversion efficiency.
Why purity matters
Sulfates must achieve a purity of over 99% to prevent parasitic reactions in subsequent stages. Impurities can degrade battery performance, reducing energy efficiency and lifespan.
Mastering filtration and filter cake extraction to optimise production
Filtration separates solid impurities from the solution and recovers sulfates in the form of a homogeneous "filter cake."
Technologies in use
Advanced filter presses enable rapid and effective separation, while hermetically sealed systems minimize contamination risks.
Advantages
A consistent "filter cake" facilitates transport and subsequent transformations, ensuring optimal quality while protecting workers from potential hazards.
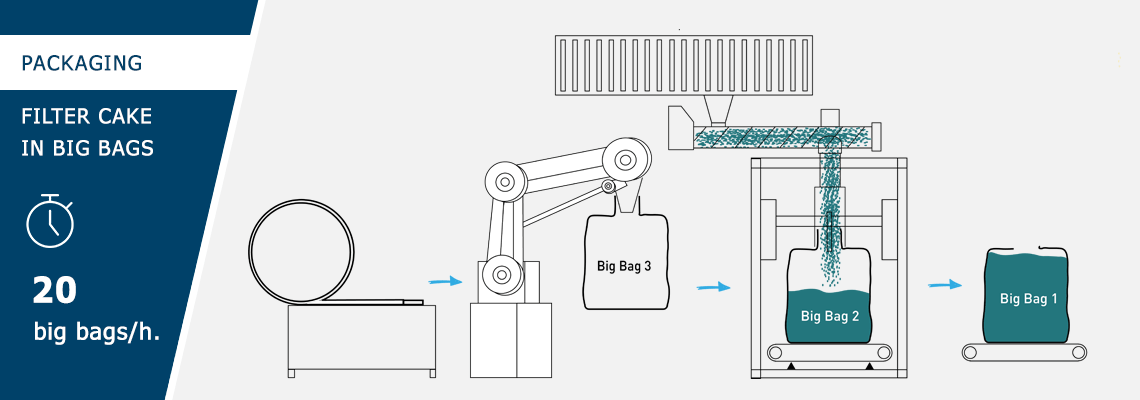
Automated packaging process for filter cake in big bags with Palamatic Process
Converting sulphates into hydroxides: a key step for high-performance batteries
Sulphates are converted into hydroxides, such as nickel and manganese hydroxides, which are vital for producing active cathode materials.
Rigorous process
This reaction, using sodium hydroxide, requires precise control of temperature, pH, and reactant concentrations to avoid impurities and ensure complete conversion.
Impact on batteries
The quality of hydroxides directly affects battery performance, including stability, capacity, and longevity.
Blending hydroxides for PCAM: ensuring uniformity for high-performance batteries
Hydroxides are mixed to create PCAM (Precursors Cathode Active Material), the foundational material for positive electrodes.
Industrial process
Specialized equipment ensures uniform particle distribution and precise chemical composition to meet the stringent requirements of battery cells.
Results
High-quality PCAM ensures consistent charge distribution, minimizing energy losses and enhancing chemical stability.
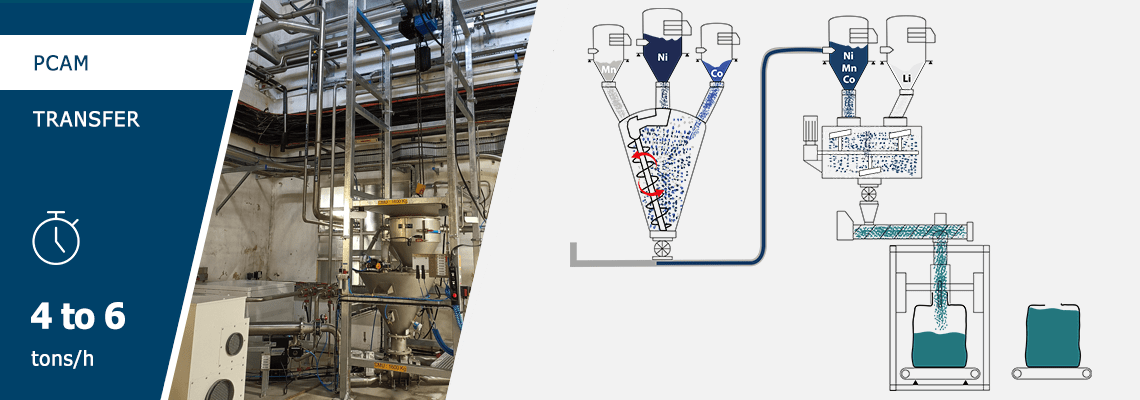
Automated preparation of CPTED with your Lithium, Nickel, Manganese and Cobalt hydroxides products
From PCAM to CAM: the importance of thermal calcination
The final step involves calcination, where PCAM is exposed to approximately 700°C to transform it into CAM (Cathode Active Material).
Effects of calcination
- Optimized crystallization enhances electrochemical properties.
- Additives like lithium hydroxide are evenly integrated to stabilize cathodes.
Impact
High-quality CAM ensures greater energy density, extended lifespan, and improved cycling performance.
Conclusion
Producing lithium-ion batteries requires technical expertise at every stage, from raw material sourcing to final calcination. Innovative solutions, like those offered by Palamatic Process, support manufacturers in achieving sustainability and performance goals, driving the energy transition forward.