Description
DrumBot 100 – Automated depalletizing and emptying of drums
The DrumBot 100 is a robotic and fully automated solution for the handling, opening and emptying of industrial drums, guaranteeing safety, precision and increased productivity. This advanced system is based on an ABB IRB 8700 robot, a drum laser cutting station, and automated empty drum management, allowing for complete handling without human intervention.
Thanks to its modular architecture, the DrumBot 100 can be adapted to a wide range of drums and products, whether in chemicals, food processing, plastics or the pharmaceutical industry. It is designed to be easily integrated into automated production lines, thus optimizing ergonomics and production rates.
-
Efficiency5
A high-capacity robot for handling barrels
The DrumBot 100 is based on an ABB IRB 8700-800/3.5 robot, specially designed for the precise and safe handling of 200 kg drums.
- Maximum load: 800 kg, enabling the handling of several barrel sizes.
- Operating radius: 3.5 meters, ensuring extensive coverage of the work area.
- Execution speed: optimized for rapid depalletizing and tipping of barrels.
- Intuitive programming: compatible with Profinet, Modbus, Ethernet/IP, facilitating industrial integration.
- Advanced security: fully enclosed and controlled environment, guaranteeing operation without risk of accident.
The ABB robot handles the drums with intelligent motorized grippers, capable of adapting to different diameters thanks to its rail guides and brushless motors.
An integrated laser cutting station for opening the barrels
The barrels are opened using a high-precision laser cutting station, which guarantees a clean cut without contaminating the product inside.
- Positioning of the barrel: The robot places the barrel on an input conveyor leading to the cutting station.
- Fixing and rotation: A stabilizing roller holds the barrel in place during cutting, ensuring a smooth and seamless cut.
- Automated laser cutting:
- The laser head perfectly follows the contour of the drum, precisely cutting the lid.
- A stabilizing spring support adjusts the pressure to ensure a smooth and controlled cut.
- Removal of the lid: A pneumatic suction cup grabs the cut lid and removes it to a dedicated conveyor leading to a waste management station.
- Removal of the open drum: The drum is removed from the station and picked up by the robot for the emptying phase.
The system can work with different types of drums, and includes a nitrogen blowing system to prevent oxidation of sensitive materials.
Automated emptying of barrels with robotic tipping
After opening, the DrumBot 100 takes care of emptying the drum without human intervention, guaranteeing an optimal flow and drainage without residue.
- Gripping by the robot: The motorized gripper securely grabs the open drum.
- Precise tilting: The rotation of the drum is ensured by the J6 axis of the robot, allowing total control of the tilt angle.
- Emptying into the hopper:
- The product is poured out with a perfectly controlled flow rate.
- Optional vibration or massage systems for materials that do not flow easily.
- Integrated dust extraction with the option of capture by Pouyes rings.
- End of cycle and emptying check: Sensors detect the end of the flow to ensure that there are no residues left in the drum.
The hopper can be custom-designed according to the product to be drained, with different configurations (stainless steel 304/316, reinforced sealing, particle filtration, etc.).
Automatic management and removal of empty barrels
Once emptied, the drum is automatically transported to a compacting station, thus eliminating storage and handling constraints.
- Pick-up by robot: The drum is picked up by the motorized gripper after emptying.
- Placement on evacuation conveyor: A motorized conveyor transports the empty drum to the compaction station.
- Automatic compaction:
- A pneumatic pusher pushes the drum into the press.
- A compaction force of 25 tons optimally reduces the volume of the drum.
- The flattened drum is automatically evacuated to a waste collector.
- Clean and secure management:
- Cycle time: 60 seconds per drum.
- Output conveyor to a collection bin (customizable option according to the customer).
This system completely eliminates the manual handling of empty drums, reducing the risk of accidents and contamination of work areas.
An automated process from A to Z for maximum productivity
The DrumBot 100 is the ideal solution for industries with high depalletizing, opening and emptying of drums needs.
- Total automation: From the handling of the drums to their compaction, without human intervention.
- Enhanced safety: Reduction of risks related to manual handling and cutting operations.
- Optimized productivity: High throughput thanks to a high-performance robot and optimized processes.
- Adaptability: Compatible with different types of drums and can be integrated into existing production lines.
With its advanced technology and robust design, the DrumBot 100 guarantees safe and efficient processing of industrial drums, while optimizing throughput and operating costs.
How the DrumBot 100 works – automated depalletization and emptying of drums
The DrumBot 100 provides fully automated handling of industrial drums, from depalletizing to emptying and disposal of empty drums. Each stage is meticulously optimized thanks to an ABB IRB 8700 robot, a high-precision laser cutting station and fully integrated waste management.
1. Depalletizing and handling of drums
The process begins with the full drums being taken from the infeed pallet.
Identification and handling
- The ABB robot detects the position of the drums on the pallet using positioning sensors.
- The motorized gripper automatically adjusts to the diameter of the drum for secure gripping.
Drum extraction and pallet management
- The drum is lifted and extracted without tipping or instability.
- Once the pallet is empty, it is directed towards an evacuation conveyor or a pallet shredder (optional).
2. Automated drum opening by laser cutting
The DrumBot 100 guarantees a clean and precise opening of the drum without contamination or particle projection.
Positioning in the cutting station
- The robot places the barrel on the infeed conveyor of the laser cutting station.
- A stabilizing roller presses the barrel to ensure even cutting.
High-precision laser cutting
- The barrel is set in synchronized rotation with the laser cutting head.
- The laser head adjusts its position via a stabilizing spring support, guaranteeing homogeneous cutting.
Removal of the lid
- A pneumatic suction cup system lifts the cut lid.
- The lid is placed on a conveyor dedicated to waste management.
Exit of the open drum
- The drum is extracted automatically to the emptying station.
3. Automated emptying and flow control
Once opened, the drum is repositioned and tilted for total emptying.
Gripping and controlled tilting
- The robot grips the drum with its motorized gripper.
- Rotation is provided by axis J6 of the robot, allowing precise and progressive tilting.
Emptying into the hopper
- The drum is tilted over the hopper for optimized flow.
- Optionally, vibration or massage systems ensure discharge without residue.
- A dust extraction system guarantees a clean working environment.
End of cycle and repositioning
- Sensors detect the end of the flow, triggering the robot's return to neutral position.
4. Emptying and compacting of empty drums
Once emptied, the drum is immediately taken over for emptying and automatic compacting.
- Pick up by the robot
-
- The robot picks up the empty drum and directs it to the removal conveyor.
- Transport to the compaction station
-
- A motorized conveyor transports the drum to the hydraulic press.
- Automatic compaction
-
- A pneumatic pusher pushes the drum into the press.
- A force of 25 tons reduces its volume for optimized storage.
The compacted drum is automatically evacuated to a skip for recovery.
5. Supervision and Industrial Integration
The DrumBot 100 is fully compatible with industrial management systems.
- Intuitive touch interface allowing real-time monitoring of the process.
- Advanced connectivity (Profinet, Modbus, Ethernet/IP) for smooth integration.
- Control sensors guaranteeing precise detection of the production flow.
Thanks to its fully automated operation, the DrumBot 100 optimizes productivity, reduces operator risk and ensures the efficient management of industrial drums.
Equipment advantages
- 100% automated: Depalletization, opening, emptying, evacuation.
- Precise laser cutting: Clean opening without contamination.
- Optimized emptying: Controlled tipping, dust collection.
- Management of empty drums: Automatic evacuation and compaction.
Media
View our equipment in photos
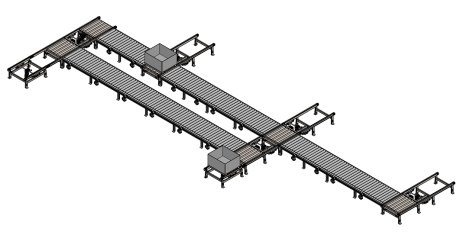
3D view of an automated transfer line incorporating the DrumBot 100
Logistics system with motorized conveyors and DrumBot 100 robot for drum management.
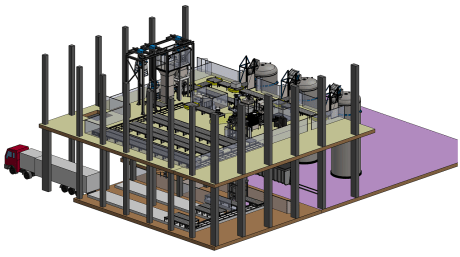
Full integration of the DrumBot 100 in a multi-level installation
Diagram of a multi-level industrial facility with DrumBot 100 for depalletizing and transferring drums.
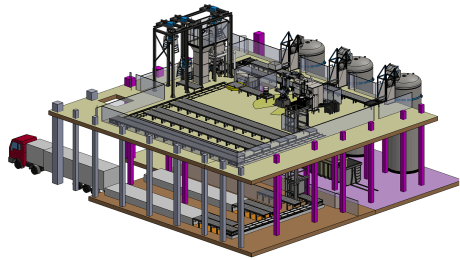
Production line with DrumBot 100, conveyors and storage silos
Factory layout with conveyors and DrumBot 100 robot to ensure a continuous flow of barrels.
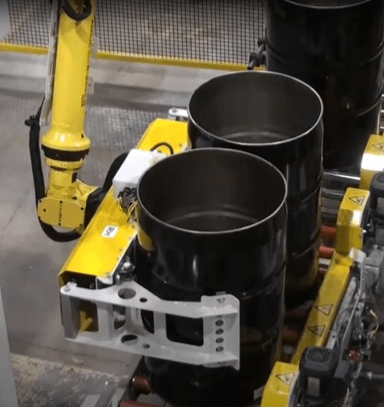
The DrumBot 100, equipped with a double gripper for the simultaneous handling of two drums
Special DrumBot 100 gripper enabling two drums to be picked up in a single operation.
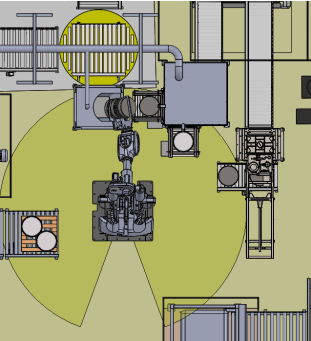
Technical diagram of a complete unit incorporating the DrumBot 100
Robotic zone plan with DrumBot 100 and automated transfer equipment
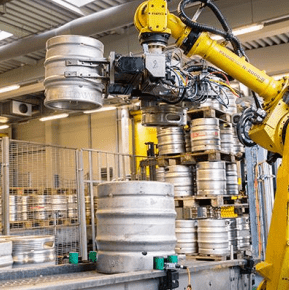
Automatic lifting phase of a barrel by the DrumBot 100
DrumBot 100 in safe lifting operation of an industrial drum
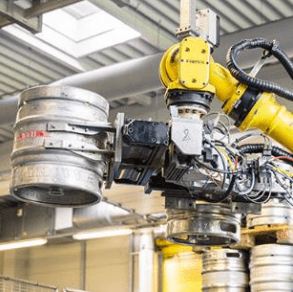
Detail of the single-shaft gripper of the DrumBot 100
Robotic gripper DrumBot 100 grips a metal drum with precision
Features
Technical specification
Criteria | DrumBot 100-S (Standard) | DrumBot 100-M (Multi-Entry) | DrumBot 100-WJ (Water Jet) | DrumBot 100-OEB (Confined) |
---|---|---|---|---|
Robot type | ABB IRB 8700-800/3.5 | ABB IRB 8700-800/3.5 | ABB IRB 8700-800/3.5 | ABB IRB 8700-800/3.5 |
Robot capacity (kg) | 800 | 800 | 800 | 800 |
Drum capacity (kg) | Up to 200 kg | Up to 200 kg | Up to 200 kg | Up to 200 kg |
Drum infeed management | Single conveyor | Multiple conveyors + IRV Vision | Single conveyor | Single conveyor |
Cutting system | Laser | Laser | High-precision water jet | Laser + full containment |
Containment options | Open | Open | Open | Sealed OEB enclosure |
Discharge options | Robotic tilting (DrumFlow 04 option) | Robotic tilting (DrumFlow 04 option) | Robotic tilting (DrumFlow 04 option) | Discharge via DrumFlow 04 |
Empty drum handling | Simple conveyor | Simple conveyor | Simple conveyor | Total compaction |
Drum compaction | Optional | Optional | Optional |