Description
Dense phase vacuum conveying with detached filter
Dust collector hopper is coupled with a pneumatic conveying cyclone. The separating cyclone is fitted with a reintroduction nozzle for collecting aspirated fines continuously and for using them again in the process.
From a flow rate point of view, the introduction of a separating filter allows to eliminate filter cleaning cycles (10% of a cycle time on average).
Image
![]() |
Main functions : 1 - Cyclonic: air/product separation 2 - Storage: recapture of the material, preservation of expansion volume 3 - Dust collection: separates the fines particles from the air, to prevent the vacuum pump from damages and also to reintroduce the fines into the process, to avoid loss of product 4 - Reintroduction of the fines into the process or fines recovery in a dedicated hopper. |
-
Rate4
-
Fragile material4
-
Fragile material4
Equipment advantages
- No product loss: reintroduction of the powders into the process
- Implementation in harsh environments: loading of reactors in hazardous areas: protection of the filter against emanation of vapors, gas and dust area ATEX certification
- High rate process: optimisation of the cyclonic efficiency, reduction of pressure losses, continuous unloading
- Difficult product conveying: protection of the filtering system, no clogging in the filter
Media
View our equipment in videos
Pneumatic vacuum conveying systems - Powders Pumps - PALAMATIC PROCESS
Vacuum transfer in dense phase for all types of powders and bulk materials
Apple : https://itunes.apple.com/us/app/palam...
Android : https://play.google.com/store/apps/de... http://www.palamaticprocess.com/powde...
Flow rate from 5 to 10.000 l/h.
Steel, 304 and 316L stainless steel construction
The new generation powder pumps developed by the PALAMATIC design office. Provides for dense vacuum transfer and prevents material deterioration continuously and confined in your production processes. Particularly suited to difficult materials (poor flow, fragility, abrasiveness, or explosive materials), this cyclone is easily installed in your environment with unlimited extension options. Suction from several feed points and / or feeding several points in your process. Coupled with weighing systems, it provides for weight-controlled introduction of raw materials. Also provides feeding a pressurized reactor vessel and feeding materials without added air.
3 functions : 1/ Transportation 2/ Dosing 3/ Weighing
Range of vacuum pneumatic conveying systems - Powder pumps - PALAMATIC PROCESS
RANGE OF VACUUM CONVEYING SYSTEMS
http://www.palamaticprocess.com/powde...
The new generation powder pumps developed by the PALAMATIC design office. Provides for dense vacuum transfer and prevents material deterioration continuously and confined in your production processes. Particularly suited to difficult materials (poor flow, fragility, abrasiveness, or explosive materials), this cyclone is easily installed in your environment with unlimited extension options. Suction from several feed points and / or feeding several points in your process. Coupled with weighing systems, it provides for weight-controlled introduction of raw materials. Also provides feeding a pressurized reactor vessel and feeding materials without added air.
The powder pumps are ideal for feeding :
- dust-laying (Triblender Silverson)
- mixers
- tanks
- reactor...
Visualisez nos équipements en réalité augmentée :
Apple : https://itunes.apple.com/us/app/palam...
Android : https://play.google.com/store/apps/de...
Pressure phase pneumatic conveying loading line with integrated dosing - PALAMATIC PROCESS
DILUTE PHASE PNEUMATIC CONVEYING WITH BOOSTER
http://www.palamaticprocess.com/powde...
This pneumatic conveyor in dilute phase, generally thrust, allows to carry pulverulent products at high throughput rate along important distances (not fragile products). This pneumatic conveyor in dilute phase by thrust lies in the use of wheel feeders (rotary valves) allowing to introduce measured doses of product in the piping. Regular application of pneumatic conveyor in dilute phase by thrust: silos emptying and silo filling.
Apple : https://itunes.apple.com/us/app/palam...
Android : https://play.google.com/store/apps/de...
Skid for reactors feeding by doses - PALAMATIC PROCESS
VACUUM PNEUMATIC CONVEYING SYSTEMS - POWDER PUMPS
http://www.palamaticprocess.com/powde...
3 functions : 1/ Transportation 2/ Dosing 3/ Weighing Flow rate from 5 to 10.000 l/h.
Steel, 304 and 316L stainless steel construction, Atex
PALAMATIC offers the vacuum transport system V-Flow running on a dense phase principle.
The product is sucked through a vacuum pump (electric or pneumatic) to a arrival cyclone (cyclo-filter) with tangential arrival (cylindrical). The product is sucked through a pneumatic conveyor gearbox installed at the point of withdrawal (no rotary valve) until the vacuum cyclone that is equipped with filters of small sizes to separate the air from the product. The vacuum cyclone is equipped with a butterfly valve (or other if the process requires) and a level probe allowing the emptying at regular intervals.
The rates obtained by this type of powder pumps are between 5 and 10 000 litres per hour with low energy consumption and extremely simple maintenance.
The other advantage of this powder system is the ease of the implementation of the weight control.
The cyclone vacuum may be located on loading cells allowing the suction and feeding of the conveyed product.
Visualisez nos équipements en réalité augmentée :
Apple : https://itunes.apple.com/us/app/palam...
Android : https://play.google.com/store/apps/de...
Mobil unit - Suction tube for drum and sack discharging
DRUM DISCHARGING SYSTEM - DRUMFLOW® 01 - SUCTION TUBE
The DrumFlow® 01 system was designed by Palamatic Process to perform drum discharging operations through a suction tube. The material contained in the drum will be incorporated in the production process thanks to vacuum suction technology. The emptying of the drums is carried out directly on pallet and without specific handling.
The suction tube allows the suction of the powder by manual operation. This suction tube is ideal for emptying drums.
The vacuum is directly carried out in the drum from the vacuum cyclone.
Transfert pneumatique - Cyclone d'aspiration - Palamatic Process
Débit de 5 à 10 000 l./h. Fabrication acier, inox 304, inox 316 L
http://www.palamaticprocess.fr/machin...
Apple : https://itunes.apple.com/us/app/palam...
Google : https://play.google.com/store/apps/de...
Il permet un transfert dense sous vide et évite la détérioration du produit de façon continue et confinée dans vos process de fabrication. Particulièrement adapté aux produits difficiles (mauvais écoulement, fragilité, abrasivité ou explosivité du produit), ce cyclone s'implante très facilement dans votre environnement avec possibilité d'extension sans limite. L'aspiration se fait à partir de plusieurs points d'alimentation et/ou alimentation de plusieurs points de votre process. Couplé à des systèmes de pesées, il permet l'introduction contrôlée en poids des matières premières. L'alimentation de réacteurs sous pression et l'alimentation du produit sans apport d'air est alors possible.
Dense phase pneumatic conveying
Vacuum transfer in dense phase for all types of powders and bulk materials
Apple : https://itunes.apple.com/us/app/palam...
Android : https://play.google.com/store/apps/de... https://www.palamaticprocess.com/bulk...
Flow rate from 5 to 10.000 l/h.
Steel, 304 and 316L stainless steel construction
The new generation powder pumps developed by the PALAMATIC design office. Provides for dense vacuum transfer and prevents material deterioration continuously and confined in your production processes. Particularly suited to difficult materials (poor flow, fragility, abrasiveness, or explosive materials), this cyclone is easily installed in your environment with unlimited extension options. Suction from several feed points and / or feeding several points in your process. Coupled with weighing systems, it provides for weight-controlled introduction of raw materials. Also provides feeding a pressurized reactor vessel and feeding materials without added air.
3 functions : 1/ Transportation 2/ Dosing 3/ Weighing
View our equipment in photos
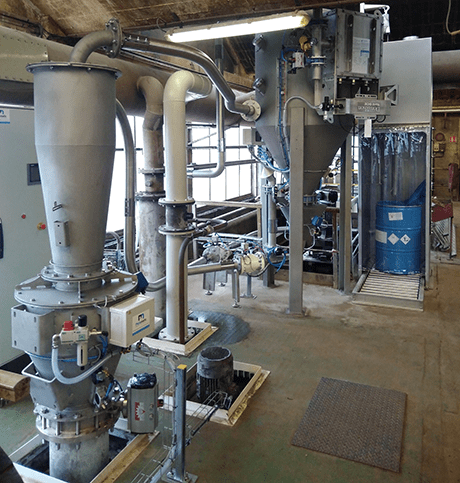
Pneumatic conveying with detached filter
Multi-drain points for a coating reactor. Pneumatic conveyor for resins, polymers, talc and silicas.
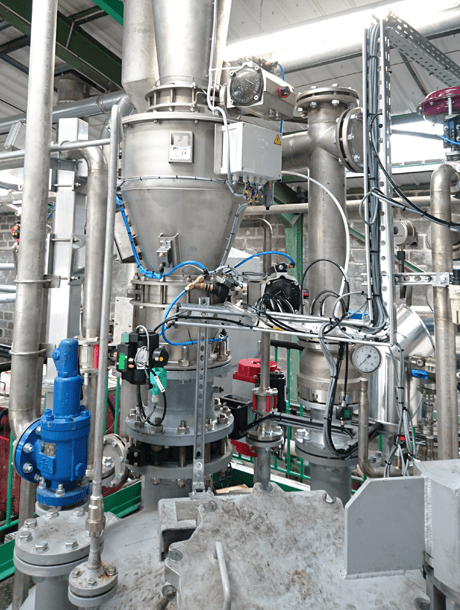
Detached filter on pneumatic conveying
Automatic loading of reactors with raw materials and dosing system.
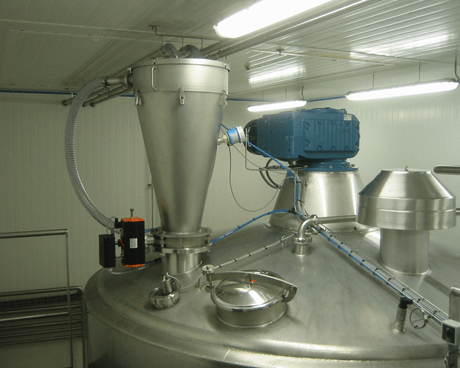
Salt and sugar processing line
High throughput processes: optimization of cyclonic efficiency, reduction of pressure drops, continuous discharging.
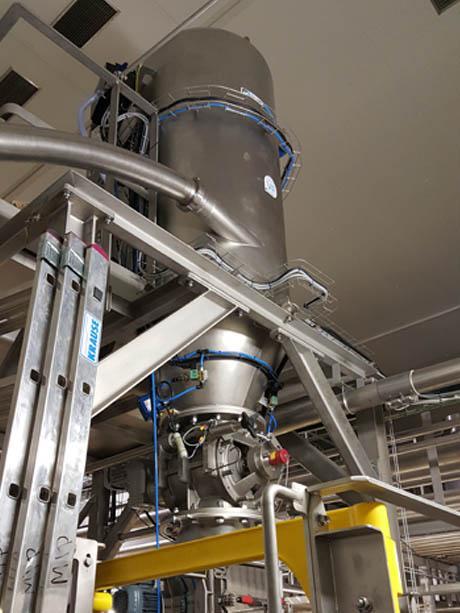
Dense phase vacuum pneumatic conveying
Implementation in difficult environments: supply of reactors in explosive areas (ATEX).
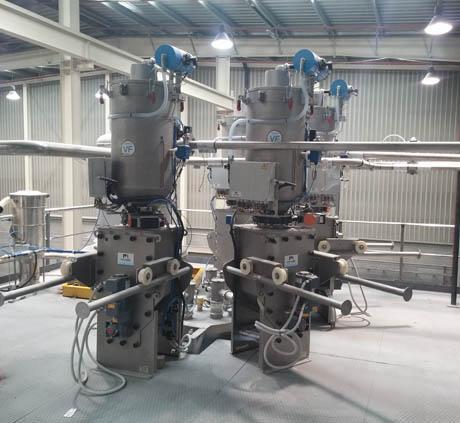
Feeding of an extruder with polymer
Handling of difficult materials: protection of the filtration system, no clogging of the filter.
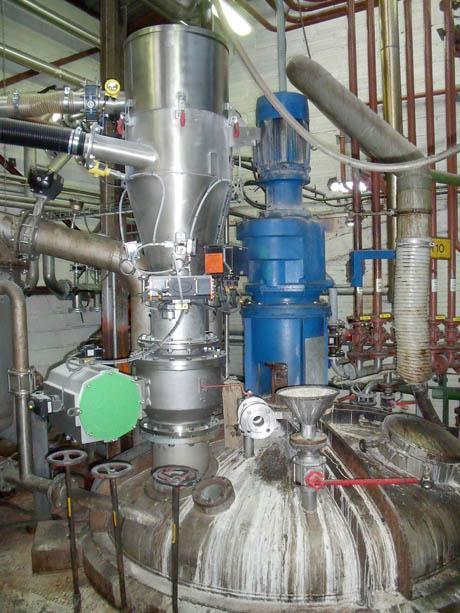
Chemical powder pneumatic conveying
Granules, metallic powders or fats, the VFlow® range ensures the conveying of more than 95% of existing powdery materials.
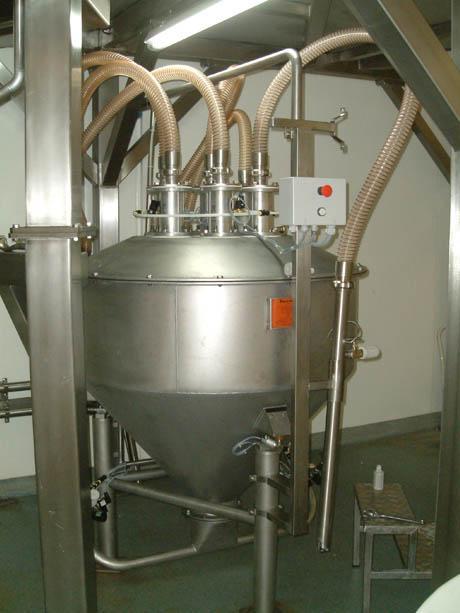
Hopper feeding with pneumatic conveying
Pneumatic conveying performs several functions, thus minimizing the number of equipment required.
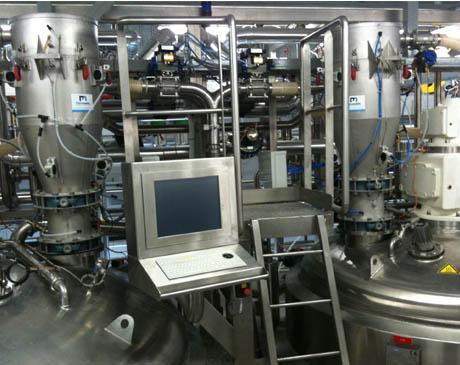
Powder and bulk material pneumatic conveyor
Installation of a big bag emptying station for feeding 3 storage silos in vacuumed pneumatic conveying.
The station is mounted on load cells and is fitted with a conveying screw allowing the material to be dosed.
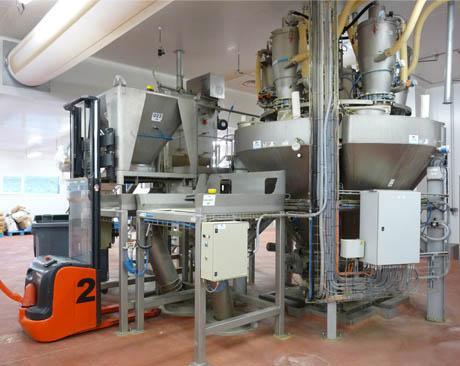
Pneumatic vacuum conveyor of powders and bulk materials
Bulk materials pneumatic conveying at the outlet of an atomization tower.
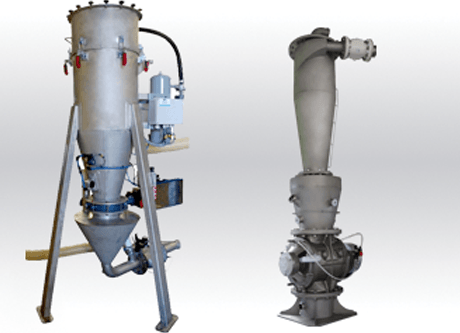
Detached filter on pneumatic conveyor
VFlow® with detached filter. The separator cyclone is coupled to the pneumatic conveying cyclone.
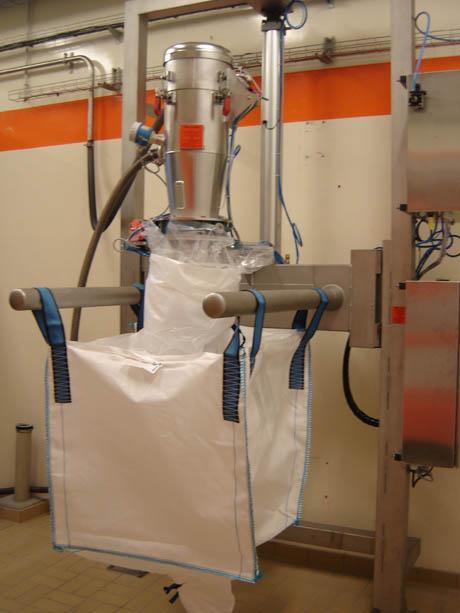
Pneumatic conveying system for big bag filling
Pneumatic conveyor on a big bag filler.
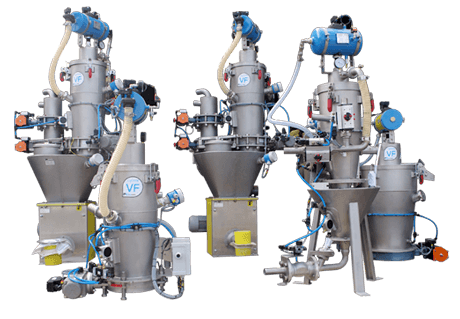
Bulk materials pneumatic conveying
Pneumatic solutions for bulk conveying applications.
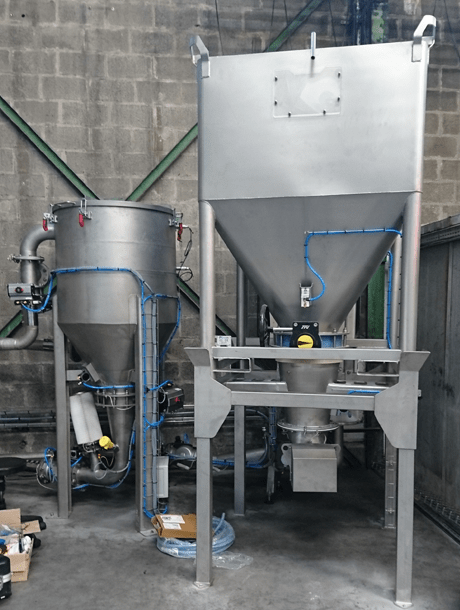
Container discharging with pneumatic conveying
Integrated equipment:
- Pneumatic conveying - Dense phase vacuum conveying - Detached filter
- Dense phase vacuum pneumatic conveying VF05
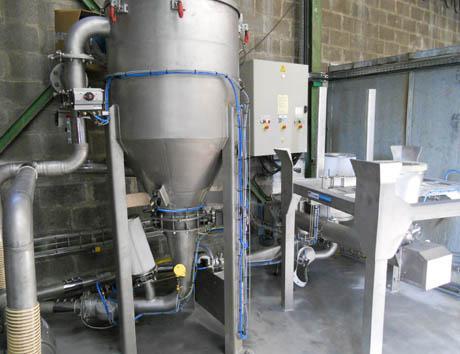
Detached filter pneumatic conveyor
- Securing industrial production lines
- Improvement of operators' working conditions, cleanliness and productivity.
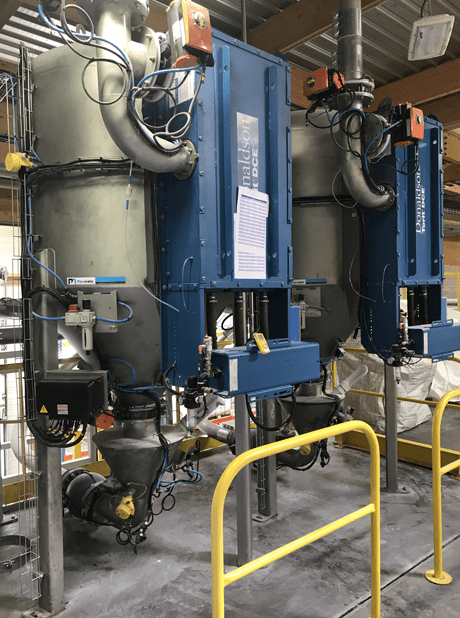
Pneumatic conveyor with detached filter - Manufacture of adhesives
Feeding of raw material processes (granules, food powders...).
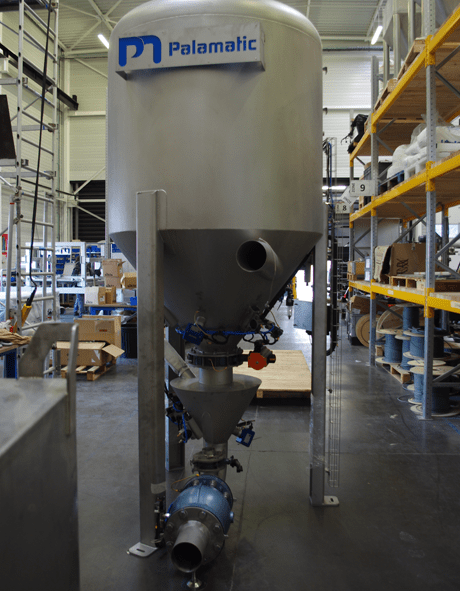
Detached filter on pneumatic conveyor
Pneumatic conveying of dust from filtration systems.
Features
Technical specification
Models | Rate in m³/h | Piping Ø in mm |
Filtering surface in m² |
Cyclone outlet Ø in mm |
Cyclone height in mm |
---|---|---|---|---|---|
VF DEP 02 | 2 | 50 | 5 | 200 | 600 |
VF DEP 04 | 4 | 65 | 8 | 200 | 780 |
VF DEP 06 | 6 | 80 | 12 | 200 | 1,431 |
VF DEP 08 | 8 | 100 | 18 | 250 | 1,850 |
VF DEP 10 | 10 | 125 | 26 | 300 | 2,200 |
Particle sizes: 5 – 3 mm
Average level of vacuum: 500 mbar absolute
Cyclonic efficiency: > 99.5%
Manufacturing materials: 304L stainless steel, 316L stainless steel
Available finishes: outside microblasting, inside electropolishing, inside mirror polishing
Filtering medias: PTFE, antistatic PTFE, FDA certified
ATEX certification: zone II 1,2,3 GD (less than 3 mJ EMI).
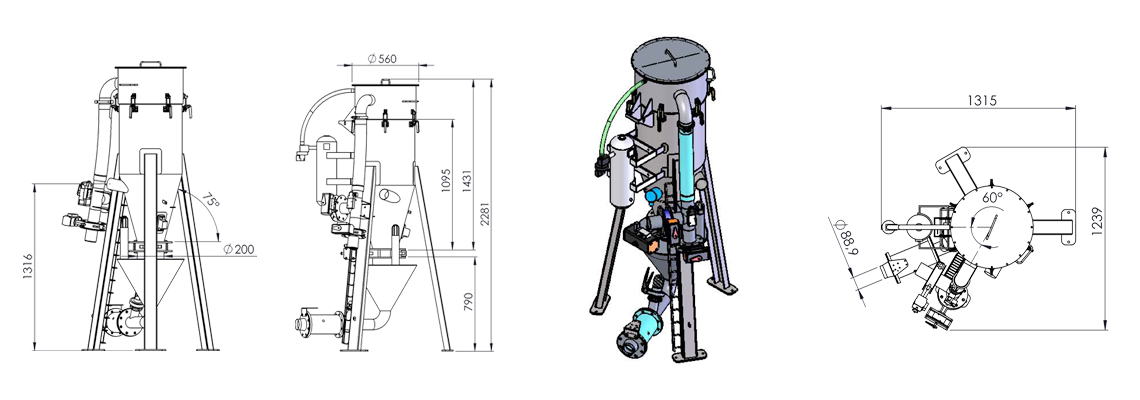
Case studies
CASE STUDIES WITH THIS EQUIPMENT
Reactors loading
Processed bulk material: lithium fluoride - Reactor loading - High performance pneumatic vacuum conveying with dosing container for incorporation into pressurized reactors. Our customer, a Chinese...Chemical
Drum unloading enclosure
Processed product: Triuranium octoxide (U3O8) – Drum tipping station - The installation concerns the installation of a production system that empties, transfers and doses drums of a toxic product...Energy