Description
Pneumatic conveying - Dense phase pressure conveying - Pressure vessel
Rate: 2 to 100 t./h.
Conveying of products with high abrasiveness
This dense phase pressure conveying is convenient for very abrasive products. This equipment ensures slow and delicate transport of granules, powders and mixtures, with less compressed air and energy consumption.
High flow, low speed and long distance conveying
The dense phase pneumatic conveying is a system particularly adapted to very abrasive materials.
Palamatic Process offers the procedure Macawber/Mactenn that uses the Inflatek® valve in order to transfer the material to the powder handling manufacturing line. This dense phase pressure conveyor system is suitable for very abrasive product, at all throughput and all temperatures.
Operating mode:
In this type of pneumatic conveying, the valve cuts the product flow below the transfer tank. This tank or transfer sluice is fitted with a double case and a special output elbow that allows to send the product slowly to the pneumatic conveyor piping.
This completely patented thrust dense phase (pneumatic) sluice procedure allows us to ensure the bends for up to two years against abrasion, and to provide a guarantee of 1,000,000 operating valve cycles before general revision. Furthermore, the dispatching valve can be cooled by water circulation, which allows to send products at very high temperature in the process.
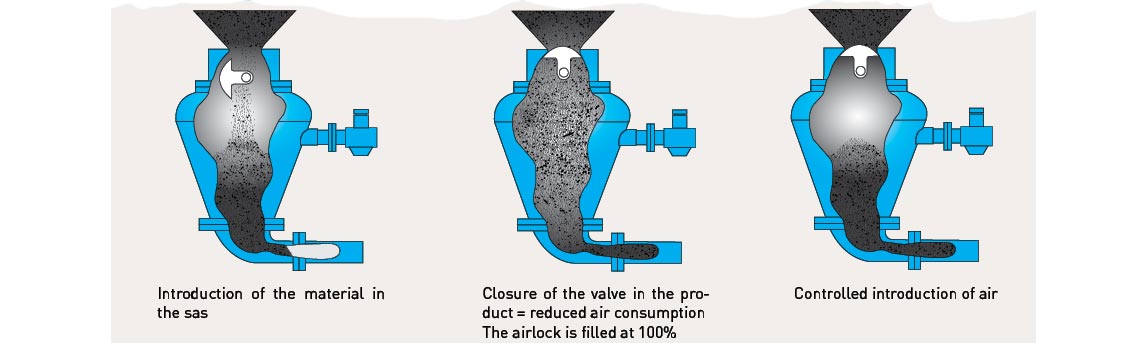
- Product is inserted in the sluice
- The valve closes in the product flow
- Controlled air introduction
- The operation is renewed up to cancellation
-
Rate5
-
Fragile material5
-
Abrasive material5
Example drawing of installation
Realization of an assembly of pneumatic conveying to feed sack filling machines:
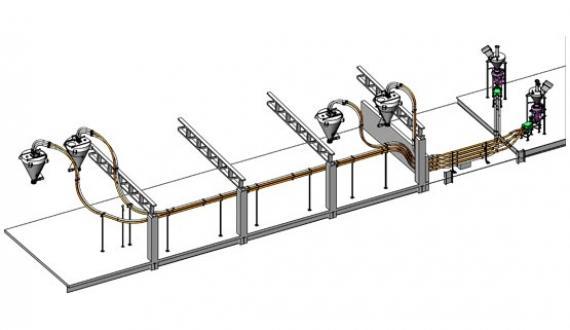
2 fedding silos
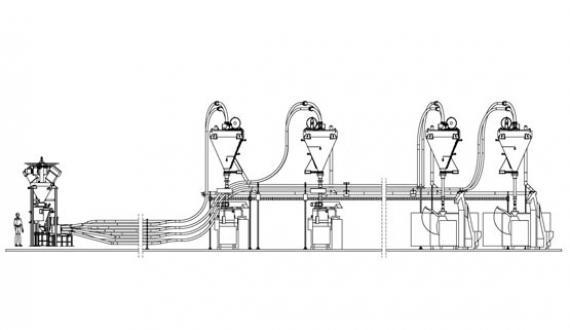
4 packaging lines
Equipment advantages
- Reduce abrasion and segregation
- Long distances conveying
- Important flows
- Optimized design to meet special needs
- All industries
Media
View our equipment in videos
Pressure vessel dense phase pneumatic conveying
The dense phase pneumatic conveying is a system particularly adapted to very abrasive materials.
Palamatic Process offers the procedure Macawber/Mactenn that uses the Inflatek® valve in order to transfer the material to the powder handling manufacturing line. This dense phase pressure conveyor system is suitable for very abrasive product, at all throughput and all temperatures.
View our equipment in photos
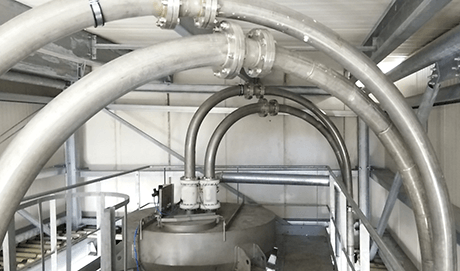
Conveying of refined white sugar and brown sugar
Each conveying airlock is designed to provide 9 t/h. at 12t/h. of sugar conveying rate.
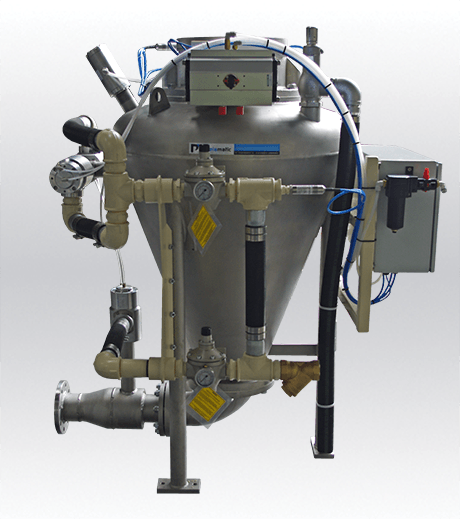
Dense phase pneumatic conveying
Conveying of highly abrasive bulk materials.

Assembly conveying system
Design of a pneumatic conveying system for the feeding of sugar packing machines:
- 2 industrial silos
- 4 packing processing lines
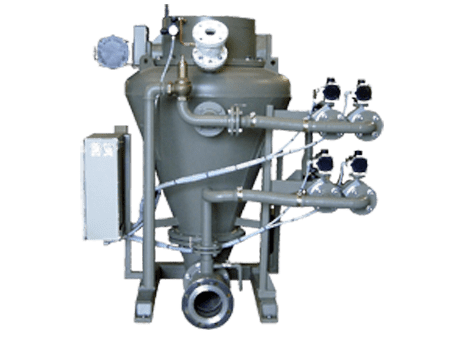
Advanced pneumatic conveying system
Dense phase pressure conveying range.
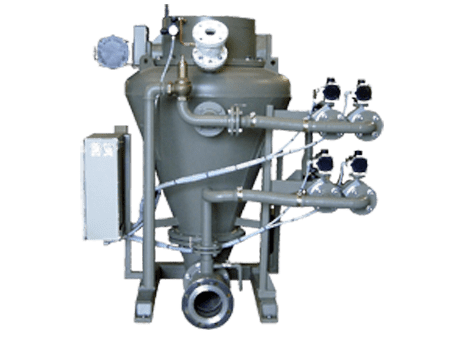
Pneumatic conveying pressure vessel
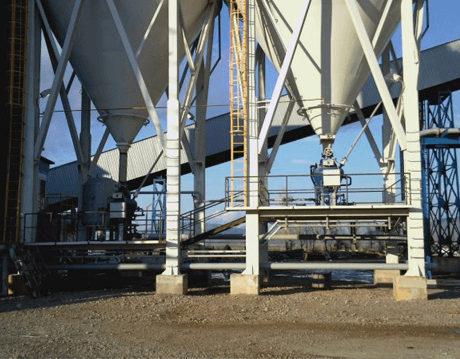
Dense phase pneumatic conveying on processing line
Industrial production lines involving raw ingredients and bulk materials handling.
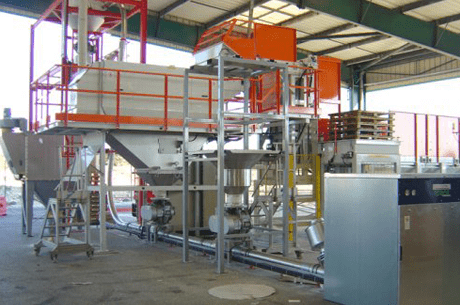
Pneumatic conveying pressure vessel
This high-density pneumatic conveyor is suitable for very abrasive raw ingredients, at all flow rates and temperatures.
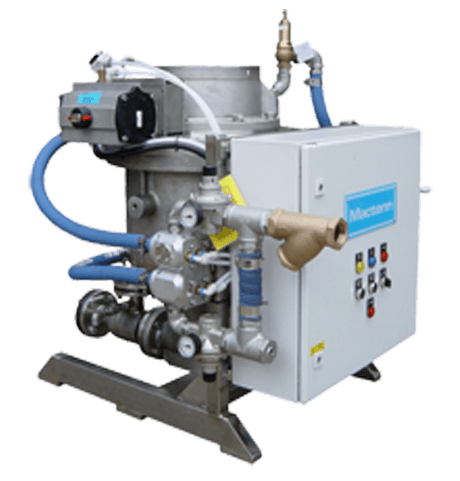
Pneumatic conveying pressure vessel
Pneumatic conveyor for for industrial production lines involving raw ingredients and bulk materials handling.
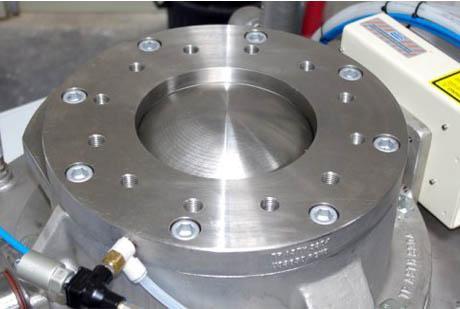
Valve for break in the product stream
Special valve for a cut-off in the flow of the bulk material.
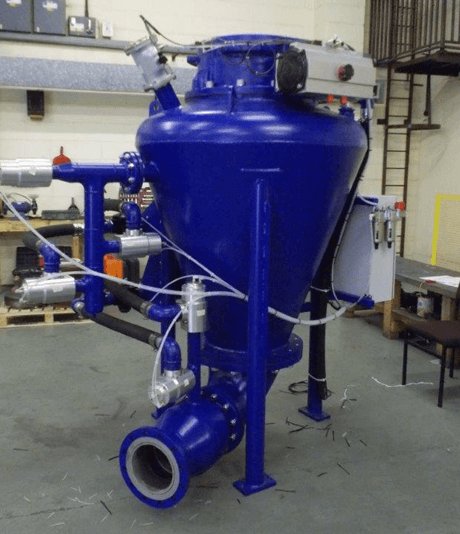
Pneumatic conveying cyclone
Dense phase pneumatic conveying for raw ingredients and bulk materials handling.
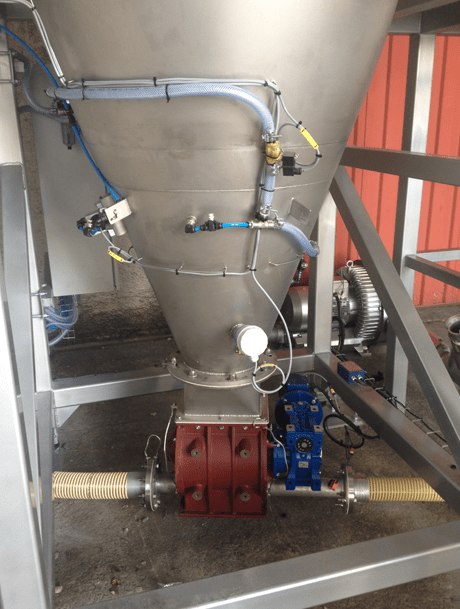
Dense phase pneumatic conveying with integrated stainless steel hopper
This patented high-density pneumatic airlock valve guarantees elbows for up to 2 years against abrasion.

pneumatic sugar conveying
The pressure vessel successively feeds the 8 filling machines at a flow rate of 9t./h. or 12t./h.
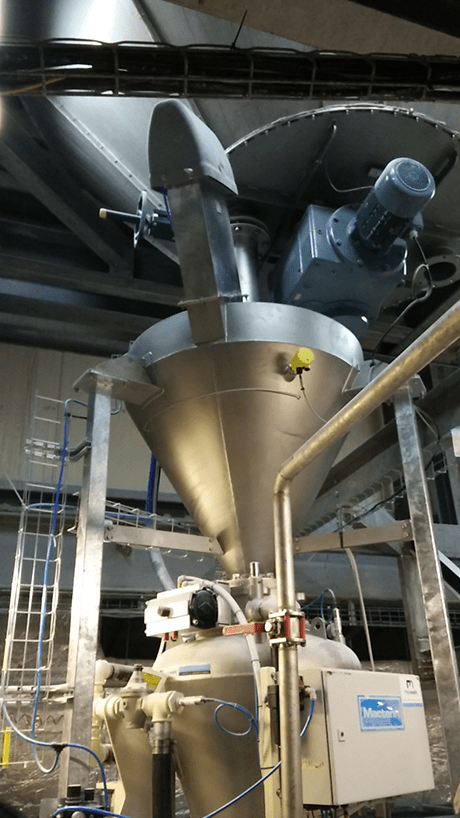
Pressure pneumatic conving
The pressure tank is gravitarily supplied through a specific valve that cuts the bulk material flow at the end of the filling process and ensures a tight seal through its inflatable seal.
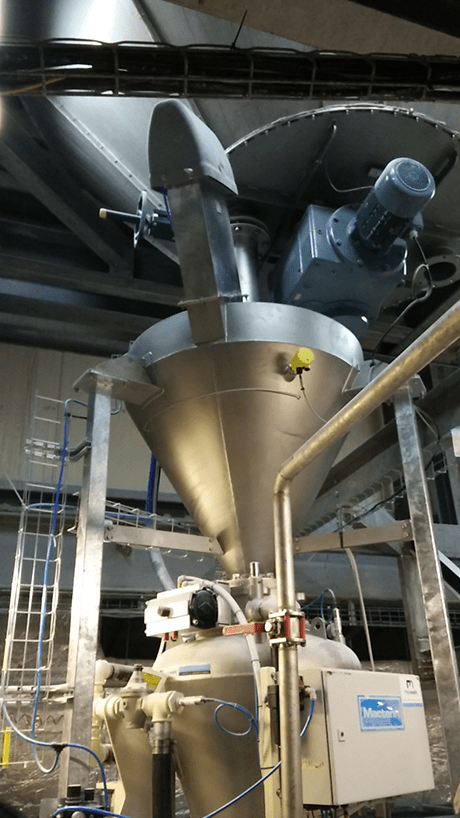
Bulk powder pneumatic conveyor
Airlock for conveying bulk materials into a reactor on a powder storage and conveying line.
Features
Technical specification
MANIMAXFLO® model:
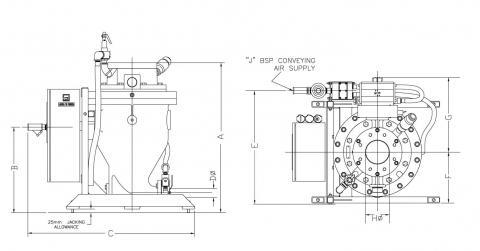
Models |
MINIMAXFLO® dimensions in mm |
Weight in kg |
||||||||
---|---|---|---|---|---|---|---|---|---|---|
|
A |
B |
C |
D |
E |
F |
G |
H |
I |
|
15/4-2 |
718 |
485 |
803 |
25/40/50 |
725 |
330 |
405 |
100 |
20 |
109 |
30/4-2 |
923 |
510 |
835 |
40/50 |
730 |
335 |
428 |
100 |
20 |
130 |
30/6-2 |
908 |
510 |
835 |
40/50 |
730 |
335 |
428 |
150 |
20 |
142 |
60/4-2 |
933 |
545 |
1,081 |
50 |
734 |
330 |
484 |
150 |
20 |
390 |
60/6-2 |
968 |
555 |
1,081 |
50 |
734 |
330 |
484 |
150 |
20 |
390 |
85/8-3 |
1,114 |
769 |
1,290 |
80 |
1,028 |
521 |
600 |
200 |
40 |
415 |
MAXFLO® model:
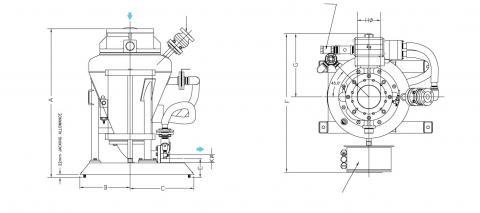
Models |
MAXFLO® dimensions in mm |
Weight in kg |
||||||||
---|---|---|---|---|---|---|---|---|---|---|
|
A |
B |
C |
E |
F |
G |
H |
J |
K |
|
114/4-4 |
1,269 |
400 |
337 |
162 |
1,190 |
543 |
200 |
50 |
102 |
335 |
114/8-8 |
1,279 |
400 |
337 |
162 |
1,190 |
543 |
200 |
50 |
102 |
455 |
228/8-5 |
1,503 |
400 |
337 |
241 |
1,252 |
535 |
200 |
50 |
127 |
525 |
342/8-6 |
1,725 |
400 |
327 |
252 |
1,285 |
533 |
200 |
63 |
152 |
555 |
342/12-6 |
1,807 |
400 |
327 |
235 |
1,131 |
521 |
300 |
63 |
152 |
753 |
570/12-8 |
2,026 |
400 |
400 |
219 |
1,127 |
435 |
300 |
76 |
203 |
1,157 |
857/12-10 |
2,276 |
480 |
502 |
305 |
1,153 |
375 |
300 |
76 |
254 |
1,501 |
1428/12-12 |
2,956 |
480 |
502 |
337 |
1,607 |
781 |
300 |
76 |
305 |
2,019 |
2125/16-12 |
3,680 |
480 |
495 |
305 |
1,607 |
781 |
400 |
101 |
254 |
2,450 |
2825/16-12 |
4,230 |
480 |
502 |
337 |
1,848 |
898 |
400 |
127 |
305 |
3,130 |
3500/16-12 |
4,759 |
480 |
502 |
337 |
2,247 |
1,092 |
400 |
153 |
305 |
3,850 |
Particle size: from very fine (ash) to big (peanuts)
Overpressure average level: 4 bars
Manufacturing: cast iron, 304L and 316L stainless steel
Compressed air consumption: 2 to 114 Nm³/min.
Maximum conveying distance: 700 m.
ATEX Certification: zone II 1,2,3 GD (EMI less to 3 mJ)
Maximum temperature: 280°C
Maximum operating temperature: > 300°C
Inlet Ø: 50 to 600 mm.
Integrated equipment :
- Vent line
- No baffle, nozzles or fluidization jets
- Volume of the sas
- Low and controlled velocity
- Conveying compressed air supply
- Control box
- Valve for break in the product stream
Options
Case studies
CASE STUDIES WITH THIS EQUIPMENT
Packing of white, organic and brown sugar
Processed powders: refined white sugar and brown sugar - Packing of white, organic and brown sugar - Leader in Africa and the Mediterranean Basin in the sugar industry and vegetable oil industry.Food and Animal Feed
Incineration plant
Processed materials: ashes - Incineration plant - Leading company in the supply of waste management and recovery solutions, expert in the whole waste cycle.Water and smoke
Drinking water filtration
Powder processed: activated carbon and lime (with a respective bulk density of 0.5 ton/m³ and 0.6 ton/m³) - Drinking water filtration - The customer requires a pneumatic conveying system, at a rate of...Water and smoke
Cement truck filling
Processed product: cement - Filling of truck with cement - Two EasyFlow® EF100 bulk bag unloading stations for high-speed semi-automatic unpacking .Minerals and building