Description
The rotary lump breaker, also known as a de-lumping valve or circular lump breaker, separates loose materials which tend to agglomerate and form friable lumps during production and storage process phases. It was designed for medium sized agglomerates and promotes smooth pre-breaking of your materials, even working on harder lumps.
Ideal for crushing snowball shaped clumps, as well as hygroscopic powders and compacted materials. It is suitable for materials such as salt, sugar, silicates and various food and chemical ingredients. The circular lump breaker can be installed in loading and / or unloading ducts (such as drums tippers and fillers), screw conveyors and small containers.
This type of lump breaker consists of a solid cylindrical body with inlet and outlet flange, an integrated grinding tool (electric motor), a rigid blade grid and a seal. The grid and the blades are removable and therefore adaptable according to the material handled. It is easy to disassemble and clean which makes its operation efficient and cost effective.
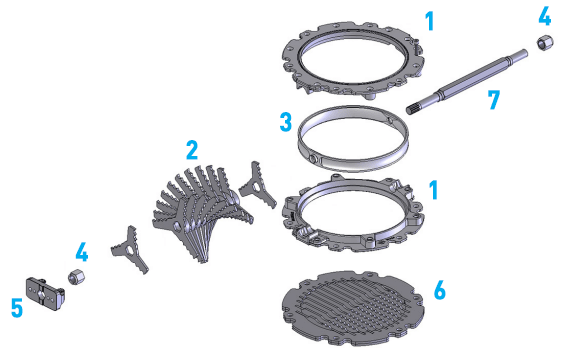
Operating mode:
- Upper and lower flanges
- Rotary blades
- Seal
- Sleeves
- Actuator mounting bracket
- Gate
- Robor shaft
A version of the rotary lump breaker dedicated to the food industry is available with stainless steel blades and a special integral seal.
Discover the Palamatic knife lump breaker, which is ideal for compact, fibrous, fatty or moist products.
-
Rate5
Equipment advantages
- Compact design
- Efficient and cost-effective deagglomeration
- Improved quality of your material
- Easy disassembly and cleaning
- No product degradation
- Removable screen and blades
- Version dedicated to the food industry
Media
View our equipment in videos
Rotary lump breaker - EDR®
Compact rotary lump breaker with removable comb.
Compact lump breaker
Compact lump breaker for gentle shredding of your bulk materials.
View our equipment in photos
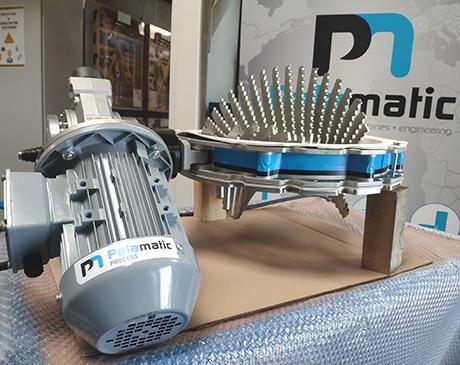
Rotary lump breaker
The screen and the blades are removable and therefore adaptable to the material handled.
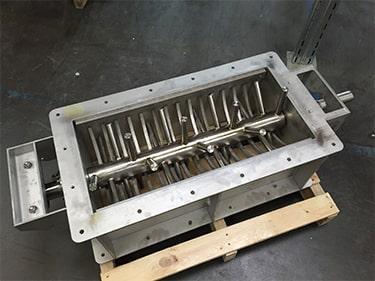
Rotary circular lump breaker
The rotary lump breaker or bar crusher is ideal for crushing your bulk materials. This equipment is made of high quality stainless steel.
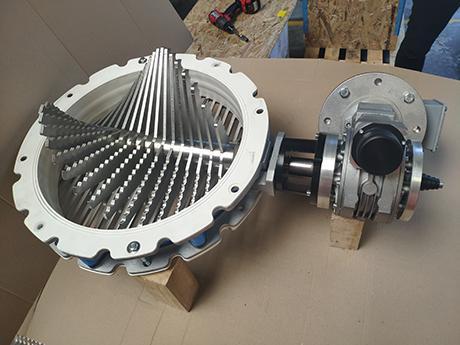
Clod breaker valve
Palamatic rotating feeder for the separation of bulk materials that tend to agglomerate.
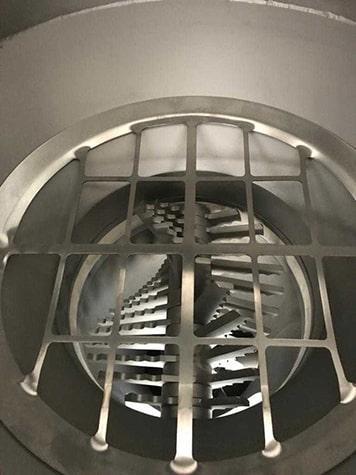
Palamatic compact lump breaker grid
The Palamatic compact lump breaker has a grid and removable rotating blades making it easy for production operators to maintain and service.
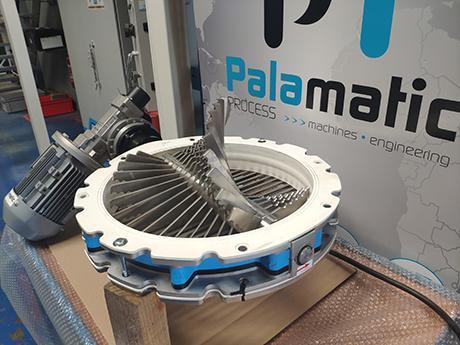
Lump breaker with removable comb
Compact crusher with removable comb, available in food processing version.
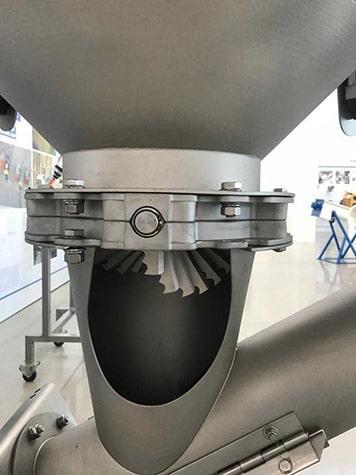
Lump breaker and screw conveyor
Example of installation with a lump breaker valve and a screw conveyor. The lump breaker is easily connected to existing piping or equipment in production plants.
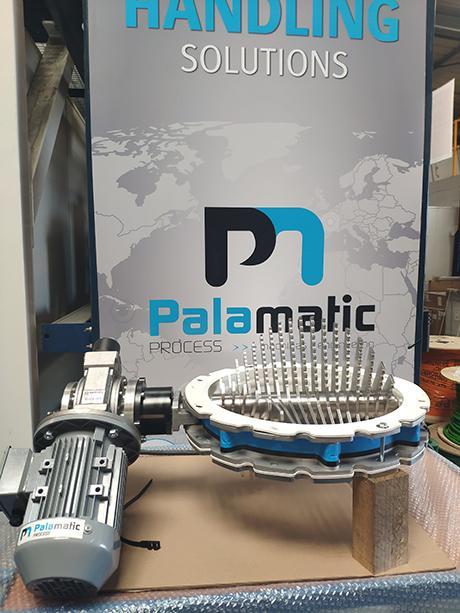
Compact circular feeder
The circular crusher ensures separation of bulk materials that tend to agglomerate.
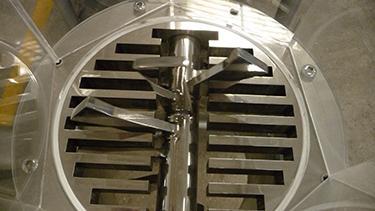
Chemical and food lump breaker
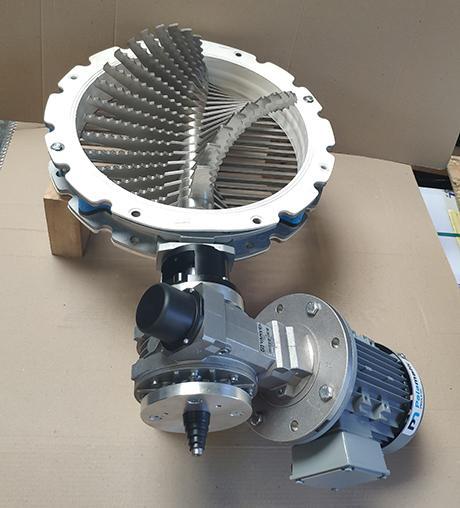
Clod breaker
The circular lump breaker can be installed in loading and/or unloading chutes, for emptying or filling drums, screw conveyors or small containers.
Features
Technical specification
Fabrication :
- Body : Aluminium
- Rotor and grid : Stainless steel 304
- Seal : White NBR
- Geared motor : Painted steel
Dimensions :
- Ø of passage : 150 to 400mm
- Thickness : 68 mm to 80 mm
- Possibility of specific dimensioning
- Height between flanges : 80mm
- Shaft with knives with product passage comb (comb removable from the outside)
- Width of passage between bars: 15mm
- Width of passage between rotating blade and bars: 4,5mm
- Thickness of bars: 6mm
(without motorization)
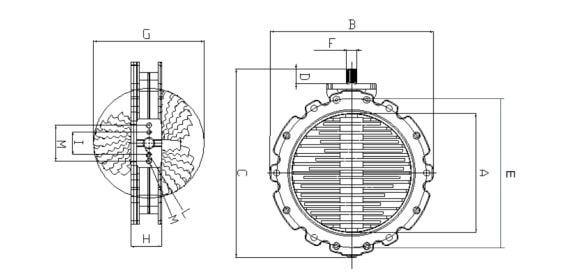
Modèle | A | B | C | D | E | F | G | H | I | L | M | kg |
---|---|---|---|---|---|---|---|---|---|---|---|---|
EDR150 | 164 | 255 | 306 | 31 | 225 | DIN482 | 146,5 | 66 | 50 | 2xM10 | 80 | 9 |
EDR200 | 213 | 310 | 367 | 33 | 280 | DIN5482 | 199 | 68 | 50 | 2xM10 | 80 | 13 |
EDR250 | 267 | 365 | 422 | 33 | 335 | DIN5482 | 248 | 68 | 50 | 2xM10 | 80 | 18 |
EDR300 | 318 | 425 | 488 | 33 | 395 | DIN5482 | 299 | 68 | 50 | 2xM10 | 80 | 21 |
EDR350 | 374 | 475 | 552 | 48 | 445 | DIN5482 | 358 | 80 | * | * | 80 | 35 |
EDR400 | 424 | 525 | 603 | 48 | 495 | DIN5482 | 410 | 80 | * | * | 80 | 40 |
Case studies
CASE STUDIES WITH THIS EQUIPMENT
Déconditionnement et alimentation de cuves de préparation
Processed powders : Frying batter (flours, starches, spices, colourings...) - The installation concerns a pre-mixing line of ingredients for the food industry.Food and Animal Feed