Processed powder: polypropylene
Bulk truck loading
This installation concerns a major player in industrial logistics that custom packages the production of a refinery.
This powder handling line is designed to feed granules into trucks at a high rate of 25 t/h. The production requirement is to create neither "angel hair" nor "snake skins" in the pipes and to have a productivity stock of 5 t./h. in order to limit the time of parking trucks in the filling area (target time 45 min.).
Productivity objective: only one operator must be able to operate the production line composed of:
High flow rate automatic bag emptying, big bag emptying station, pneumatic conveying with booster, cyclofilter and truck filling sleeve.
The pallets are placed in line on a motorized roller train. The possibility of accumulating 8 pallets on the conveyor allows the operator to benefit from a convenient buffer in order to be able to work in masked time on other tasks.
A stack separator at the inlet of the actual bag cutting and emptying machine isolates the pallet to be emptied. It is then tilted by means of a hydraulic cylinder and the bags fall into the cutting chamber.
The cutting is carried out by means of circular high-speed steel blades (stainless steel possible) mounted on a transmission that gives them a peripheral speed of about 60 km/h. This speed largely limits the emission of flakes or pieces of bags.
The cutting chamber is directly integrated into the discharge drum which rotates the bag on itself over 5 to 6 revolutions, thus obtaining an excellent discharge coefficient.
The polypropylene powder then falls directly into the intermediate hopper, which is itself clamped on the conveying lock.
The empty bags are conveyed to a baling press (possibility of implementation of a bag compactor).
In this application, the parts in direct contact with the material are made of 304 stainless steel.
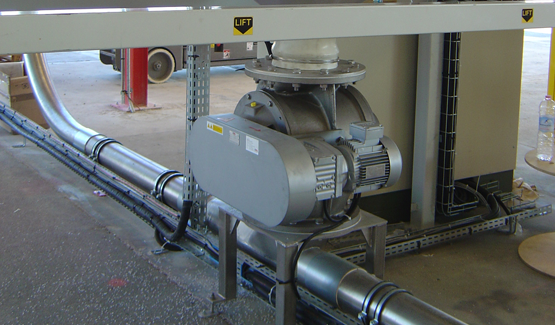
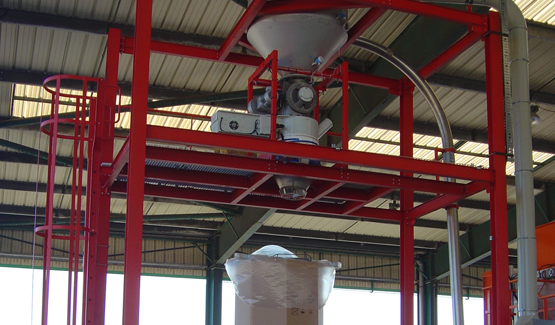
BIG BAG EMPTYING STATION
Polypropylene granules generate only very little dust and are very free-flowing, so Palamatic Process installed a "standard" system for emptying these big bags, namely: loading with forklift, unlacing cabinet, a lock connection, etc…
PNEUMATIC TRANSFER WITH BLOWER
The pneumatic conveying line consists of two full flow locks individually mounted under the bag emptying station and the big bag unloading station.
The length of the circuit is about 40 m. with an elevation of 10 m.
The locks regularly feed the conveyor piping.
This same conveyor is provided by a "Roots" blower whose flow rate and air pressure are calculated in such a way as to ensure the rate of 30 t./h. desired by the operator.
The pipes are made of 304 stainless steel and convey the material to the separation filter.
We do not voluntarily provide more information about the characteristics of this process.
CYCLO-FILTER AND BULK TRUCK FILLING
In order to effectively separate air and material at the pneumatic conveying system outlet, a filter with a dimensioning calculated by Palamatic Process is mounted on the roof of a buffer hopper.
This buffer hopper fitted with a high and low level as well as a bottom valve allows to carry on conveying and therefore to optimize the flow rate when changing the tank inlet openings or when changing the truck.
A telescopic truck loading spout is mounted under the valve of the buffer hopper.
It is equipped with a connection port, a level probe and a vent to ensure a contained filling with perfect pressure balances.
The control of the entire Palamatic Process line is integrated in a control cabinet that includes power and control.
A touch screen allows the user to configure his operating mode while having a user-friendly supervision of the whole system.