High speed disperser loading station
Paster feeder / disperser / mixer for viscous products
The PaintFlow® loading stations are designed for the supply of any type of viscous product mixer such as disperser (flag, butterfly, grinder, etc.), homogenizer, agitator. A sack emptying hopper ergonomically feeds the process from the ground. An air conveyor conveys the loads, pigments or additives to the macerator.
- Ease of use
- Reliability
- Very low retention
- Dust confinement
PaintFlow® loaders allow manufacturers to feed their paint processes and other viscous products easily and ergonomically.
Models
PaintFlow® 10 | PaintFlow® 20 | PaintFlow® 30 | |
---|---|---|---|
Flow m³/h | 10 m³/h | 10 m³/h | 15 m³/h |
Mobile station | No | Yes | Option |
Integrated dust collection | No / option | No / option | Yes |
Integrated Bag Compactor | No | No | Yes |
Mobile outlet height | Yes | No | Yes |
Feed height | 3,30 - 1,70 m | 2,30 m | 3,30 - 1,70 m |
Retention | < 1% | < 1% | < 1% |
Safety Screen | Yes | Yes | Yes |
Bag opening station:
The operator places the bags to be unloaded in the autonomous bag emptying station. The bag is cut and emptied of its material. The product passes through the screener to provide quality control of the pasters.
The bag emptying station is designed for manual opening of all types of bags, limiting dust emissions by integrating a dust collection unit and an empty bag compactor. Its ergonomic design provides the operator with an efficient and reliable workstation.
Once empty, the bag is compacted in a waterproof plastic sheath by the bag compactor. Dust associated with product residue in the bags remains trapped. As for the operator's station, it is continuously de-dusted by an independent filter that captures fines during unloading.
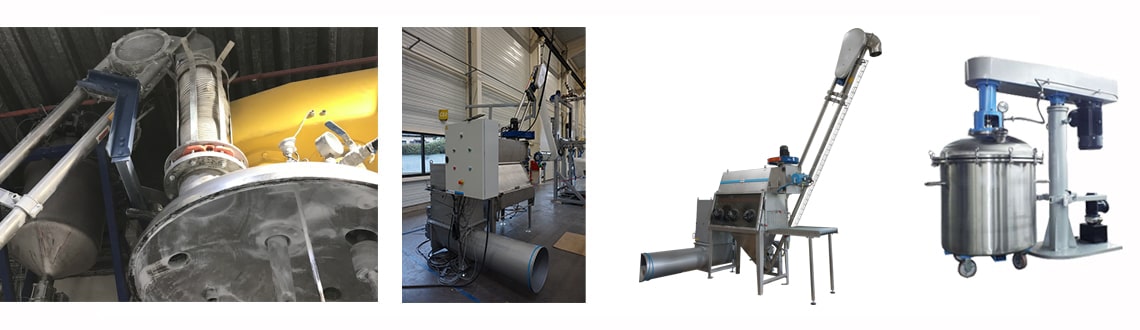
Aeromechanical conveyor:
The aeromechanical conveyor transports the loads and other additives from the bag dump to the disperser at a maximum rate of 15m³ / h.
The air conveyor uses air to convey a product with molded discs on a cable moving at high speed in a steel tube. This high speed movement of the discs is what creates the air flow which transfers the materials.
This mechanical conveyor is multi-product compatible and does not require any adjustment between the different production steps.
Its sleek design gives it excellent cleanability with almost zero retention for the conveyed products.
Connection to the macerator:
A retractable flexible cuff for dust tight sealing is connected to the disperser. A simple DN150 flange on the tank roof allows a clean connection. A butterfly valve can be added to prevent the grinding, finishing and colorimetry steps from being polluted.
Standard applications:
PaintFlow® loaders are suitable for manufacturers who want easy and ergonomic feeding of their paint process and other viscous products, in particular for:
- Feeding the pasters with load and pigment for the manufacture of paints
- Loading of additives (preservatives, wetting agents, crosslinking agents, stabilizers, anti-bubbles, coalescing agent, etc.)
- Loading of mixers in the manufacture of silicones and sealants
- Loading of the pasters on the glue production line upstream of the dispersion / adjustment
- Loading of hot melt powder compounds, control is carried out by an on-board control unit.
The piloting is done as close as possible to the loading. Many standard options are available: food design, ATEX certification, etc.
Options:
- Dusting
- Flow aid
- Operation delay to follow the recipe
- Larger capacity loading hopper
- ATEX certification
- Food certification
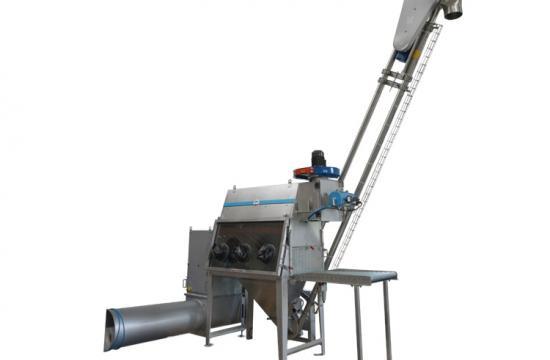
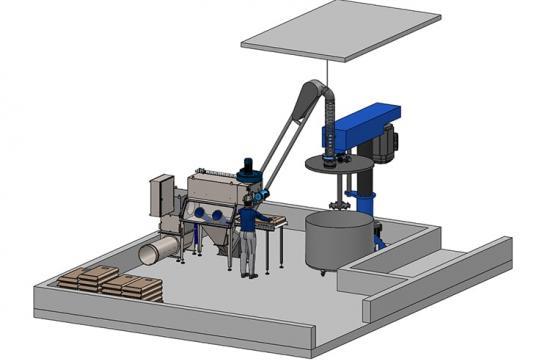
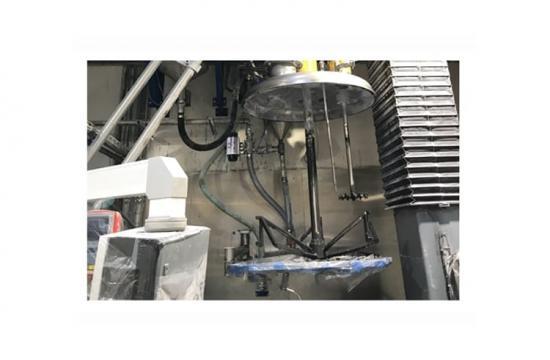
Discover the facilities of our customers using the PaintFlow® paster loading line.
All the equipment integrated into the PaintFlow® process line is available below.