Produis traités : graines (lin brun, jaune, tournesol, pavot, courges, sarrazin), fruits secs (amandes, noisette poudre, pistache poudre), fruits séchés, sucres...
Production de fruits secs et graines
Notre client, fabricant français de mélange de fruits secs et de graines pour l’industrie agroalimentaire (pâtisserie et boulangeries industrielles) souhaite implémenter une nouvelle ligne de mélange et de conditionnement liée à la croissance de son entreprise.
Les matières premières livrées en big bags et sacs sont déconditionnées sur des postes mixtes dédiés au déconditionnement de sacs et de big bags Duopal®. Ces postes de vidange sont pesés. Les matières sont ensuite dosées dans la conduite de transfert par des couloirs vibrants sans dégradation des produits.
Le transfert des matières premières est réalisé par aspiration avec un cyclofiltre modèle VF04 à un débit de 2 000 kg/h. Le transfert en phase dense aspiré évite toute altération du produit.
La matière est alors introduite dans un mélangeur horizontal monorotor à pales MRS2000 travaillant des batchs de 1400L utiles. La vitesse ainsi que le temps de mélange sont adaptés à chaque recette en cas de présence de produits fragiles. Une fois terminé, l’intégralité du mélange est vidangée dans une trémie tampon qui permet de libérer le mélangeur pour le batch suivant.
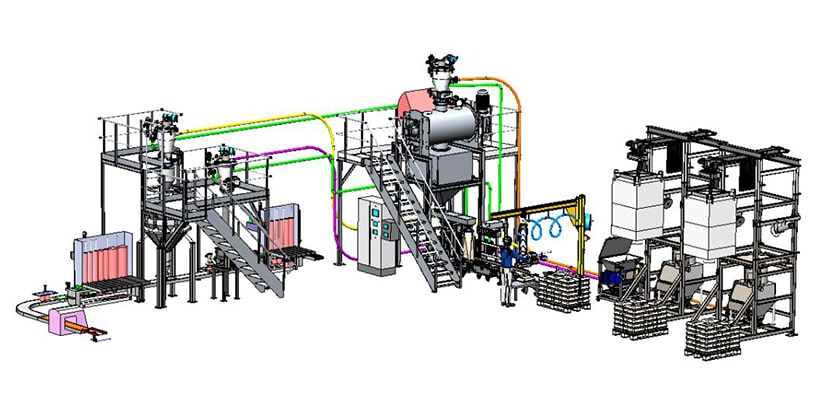
Pour la suite du process, un système de conditionnement en seaux de capacité maximale de 8 litres a été mis place (station PalDrum® 03).
Pour cela, la conditionneuse de seaux a été rendue mobile et déplaçable de façon à intégrer une boite de mise en vitesse sous le volume tampon en sortie de mélangeur pour convoyer le mélange par aspiration (Cyclofiltre VF04) vers une peseuse associative.
La peseuse associative prépare la dose par combinaison de plusieurs têtes et la relâche par gravité vers le seau. Un système de dépilage automatique de fût permet d’amener le contenant vide via un convoyeur à bande sur le poste de conditionnement. De même, un convoyeur à bande achemine le contenant rempli vers le poste de dépose automatique du couvercle. Le seau rempli et fermé est ensuite transféré vers le poste de palettisation automatique via un nouveau convoyeur à bande muni d’un détecteur de particules métalliques. Une formeuse de caisse carton prépare la caisse carton dans lequel un robot 5 axes muni d’une ventouse de préhension va y introduire le nombre de seaux souhaité. Le carton est ensuite dirigé vers une scotcheuse automatique pour être fermé. Les cartons fermés sont repris par le robot et positionnés sur une palette. L’évacuation de la palette est faite par chariot élévateur.
La mise en place d’un dispositif de conditionnement en sacs de 25kg directement en sortie de ce volume tampon via un doseur vibrant aurait également pu être envisagée. Le conditionnement se serait alors effectué sur un poste de vide sacs PalSack® 01 muni d’un joint gonflant et d’une bascule. Les sacs auraient ensuite été acheminés vers le poste de palettisation manuel par un convoyeur à bande muni d’un détecteur de particules métalliques. En fin de ligne, un manipulateur de sacs permettrait la palettisation manuelle sans effort par l’opérateur des sacs tout juste fermés par un banc de couture.
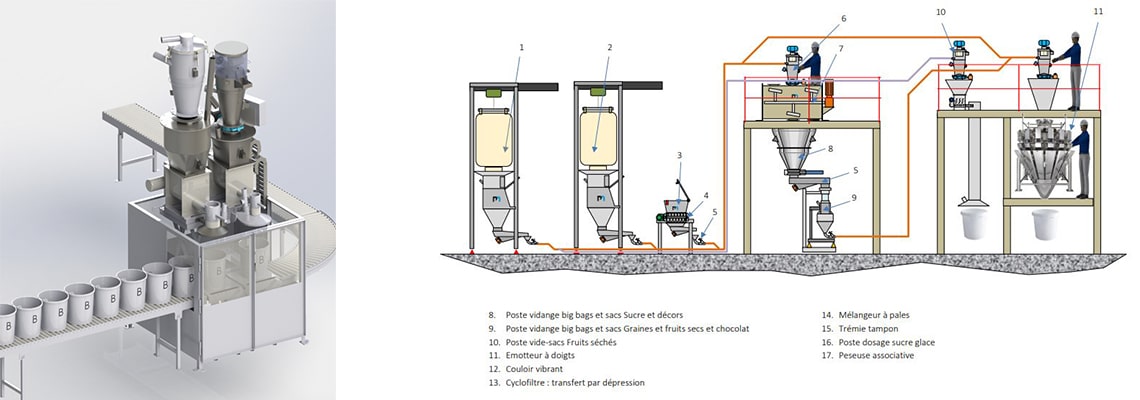