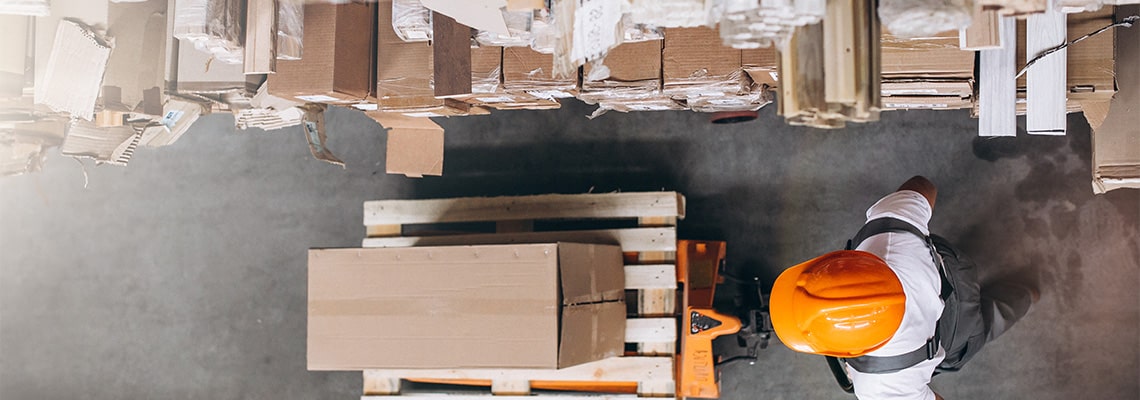
Musculoskeletal disorders (MSDs) account for 80% of work-related diseases. Almost all of these illnesses are due to working conditions, particularly manual handling. This is why it is essential to know the regulations in force in this area in order to avoid any risk for production operators and to enable them to work in the best possible conditions.
1. Definition of manual handling
Manual handling is defined as "any operation of transport or support of a load, including lifting, placing, pushing, pulling, carrying or moving, which requires the physical effort of one or more workers".
There are several types and rates of manual handling.
Types of manual handling :
- Carrying loads
- Lifting and setting down loads
- Carrying loads
Paces of manual handling:
- Isolated load carrying
- Occasional load carrying
- Repetitive load carrying
2. Thresholds that should not be exceeded
The AFNOR NF X35 - 109 standard on manual handling of loads indicates the thresholds not to be exceeded according to age and sex in the 18 - 65 age group. This standard, which is a recommendation of the CNAMTS (Caisse Nationale de l'Assurance Maladie des Travailleurs Salariés - National Health Insurance Fund for Salaried Workers), is not valid for situations involving risks such as slopes, stairs, etc.
According to standard X35-109, loads :
- weighing less than 5 kg are not at risk.
- between 5 kg and 15 kg are "acceptable
- over 15 kg are at risk
- over 25 kg are in the unacceptable zone.
For women, the limit is 25 kg and for men it is 55 kg maximum. An opinion from the occupational physician is required for carrying loads above this threshold. For young workers, there are specific loads defined by the Labour Code (male staff aged 14-15 years: 15 kg, 16-17 years: 20 kg / female staff aged 14-15 years: 8 kg, 16-17 years: 10 kg).
Under no circumstances may the loads carried exceed 105 kg.
The maximum cumulative weight per day that an operator can carry is defined as 7.5 tonnes over 8 working hours with an application height for the hand position between 0.75 and 1.10 m.
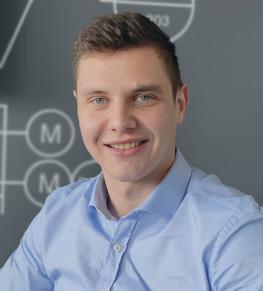
Do you have a handling project?
I am available to discuss the subject.
Loïc, powder expert
3. Prevent MSDs by avoiding painful factors
Several elements can increase the difficulty of manual handling. It is therefore important to anticipate them in order to avoid any risk of MSD. Among these aggravating factors, we find in particular the factors :
- Related to the manual load itself: its weight, size, shape, height, distance travelled, etc.
- Organizational: high production rate, speed of execution, repetitive movements, night work, stress, etc.
- Workplace: surface area of the manual handling activity, slippery, cluttered floor, poor condition (e.g., fall hazard)...
- Ambience: cold or hot environment, lighting, etc.
An upstream analysis of the risks linked to manual handling, training of personnel in the movement of loads, the provision of personal protective equipment (PPE) or the use of mechanical handling equipment are all measures to be applied to improve the working conditions of operators.
4. Ergonomic equipment for carrying loads in industrial environments
Palamatic Process offers many solutions to reduce the risks of injuries and occupational diseases thanks to handling equipment adapted to different industries.
The industrial manipulators designed by Palamatic are intended for the handling of bags, drums, pallets, gum blocks, cartons... They work with a vacuum lifting system which allows to handle heavy loads (from 5 to 200 kg) without effort, thus minimizing muscular fatigue. This equipment optimizes working time and reduces the risk of RSI for production operators.
For filling and discharging stations of big bags, sacks and drums, Palamatic also has a range of ergonomic equipment ensuring a minimum of intervention from the operator and a safety throughout the process. The use of an electric hoist, a forklift or a low structure is also an integral part of our installations for the loading of the containers.
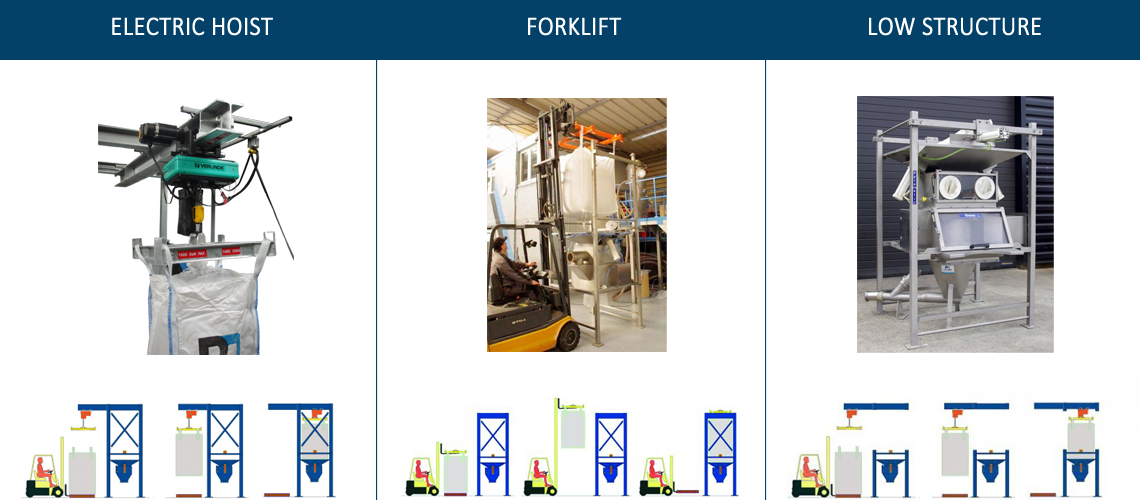
Discover our articles related to this topic: