Description
Jumbot 1000 – The Benchmark in Automated Big Bag Emptying
The Jumbot 1000 is a fully automated big bag emptying station, designed to handle everything from loading the big bag to its removal after emptying without human intervention.
Unlike the semi-automatic solutions on the market, our system is based on a high-capacity industrial robot, capable of handling big bags of different sizes completely autonomously.
Its modular design allows for the integration of various adaptation options according to the needs of the industry, whether in plastics, chemicals, food processing or any other sector requiring the handling of powdered materials.
Thanks to its precision and speed, the Jumbot 1000 guarantees an optimized production flow, while ensuring maximum safety and perfect control of dust emissions.
-
Efficiency5
High-capacity gripper, secure big bag grip
The key element of the Jumbot 1000 is its hydraulic big bag gripper, specially designed to handle heavy loads and guarantee optimal support throughout the emptying cycle.
- Initial gripping of the big bag: The clamp closes around the full big bag with controlled force, allowing stable handling without the risk of the container falling or tearing.
- Progressive opening during emptying: Once the big bag is cracked on the emptying hopper, the main clamp opens to release the product from the big bag.
- Claws to hold the empty big bag: To prevent the empty big bag from falling back into the hopper, a second gripping system with metal claws or hooks perforates the upper part of the big bag to keep it suspended until it is removed.
A high-performance industrial robot
The Jumbot 1000 is based on a FANUC M-2000iA/2300 robot, designed to meet the requirements of the most demanding industrial environments.
- Load capacity: 2,300 kg, allowing the handling of big bags up to 750 kg and even 1,000 kg under certain conditions.
- Operating radius: 3,734 mm, ensuring extensive coverage of the work area.
- Speed of execution: Fast and smooth movement thanks to the 6-axis robot.
- Intuitive programming: User-friendly interface compatible with the main industrial standards (Profinet, Modbus, Ethernet/IP), facilitating integration into existing automated lines.
- Built-in safety: DCS (Dual Check Safety) system guarantees completely safe operation in a restricted environment.
Using this robot offers greater flexibility than an overhead crane, eliminating space constraints and ensuring a much higher production rate.
Optimized oil change: adaptable hopper and cracking systems
The big bag is emptied through a receiving hopper equipped with a custom-made big bag perforation system, designed to adapt to the characteristics of the transported product.
Available cracking systems:
- U-blades: For big bags with outlet sleeve and pointed for big bags with open bottoms.
- Water jet cutting: For applications requiring an opening without particle release.
- Massage systems: Supplementary to facilitate the flow of dense or compact products.
Dust emission management:
- Pouyes rings: Can be integrated for efficient collection of fines and dust.
- Connection to existing suction networks: Compatibility with the site's dust extraction systems.
Automated management of empty big bags
Once the big bag has been emptied, its disposal is fully automated thanks to the various possible configurations:
- Deposit in box: For manual management by the operator or subsequent reuse.
- Waterproof big bag compactor: Allows for volume reduction and hygienic disposal of residues.
- Big bag shredder: For immediate destruction and optimized recycling of materials.
This system avoids any manual handling of empty big bags, thus reducing the risk of environmental contamination and operator risk. This improves the cleanliness of the production site.
The Jumbot 1000, a standard of excellence for the industry
With its fully automated design, the Jumbot 1000 represents a major breakthrough in the field of big bag emptying. It allows for:
- Optimized productivity, thanks to smooth and fast big bag management.
- Enhanced safety, by eliminating any human intervention in the critical stages of the process.
- Complete adaptability, with tailor-made options to meet the specific needs of each industry.
At Palamatic Process, we develop integrated solutions for powder handling and processing, and the Jumbot 1000 is the perfect example. Advanced technology, robust design and total automation for a more efficient industry.
Contact our experts for a personalized study and a demonstration in real conditions.
How the Jumbot 1000 works – automated emptying of big bags
How the Jumbot 1000 works – Automated emptying of big bags
The Jumbot 1000 ensures 100% automatic emptying of big bags, from loading to removal of the empty bag, without human intervention. Thanks to its high-capacity FANUC robot, hydraulic gripper and optimized perforation system, each stage is carried out with precision, speed and safety.
1. Gripping and positioning of the big bag
- The robot identifies the big bag using its intelligent sensors and automatically adjusts its grip.
- The high-capacity hydraulic gripper firmly grasps the big bag, ensuring stable handling.
- The robot orients and lowers the big bag above the hopper, with precise dynamic positioning.
- Option: automatic removal of plastic covers before emptying.
2. Controlled emptying via the perforation hopper
- The big bag is pressed against a perforation system (cross, U or V blades or water jet) adapted to the product being handled.
- The product flows out immediately, optimised by integrated pneumatic massage systems.
- A dust extraction system (Pouyes rings) guarantees a clean working atmosphere free of volatile emissions.
3. Automated management of the empty big bag
- Once emptying is complete, the main gripper opens, releasing the big bag.
- An upper gripper with perforating claws takes over, keeping the big bag suspended without risk of it falling.
- The robot transports the empty big bag to one of the evacuation systems:
- Deposited in a box for temporary storage.
- Waterproof big bag compactor for volume reduction.
- Big bag shredder for immediate destruction and recycling.
4. Supervision and industrial integration
- The Jumbot 1000 is compatible with all industrial control systems:
- Intuitive touch interface for real-time management.
- Advanced connectivity (Profinet, Modbus, Ethernet/IP) for smooth integration into industrial automation.
- Control sensors for precise detection of production flow.
With its fully autonomous and secure process, the Jumbot 1000 guarantees maximum productivity and optimized management of big bags, meeting the strictest requirements of the chemical, plastics and food industries.
Equipment advantages
- 100% automated: Loading, emptying and evacuation without human intervention.
- Precision and speed: FANUC robot, hydraulic gripper and perforating gripper.
- Optimized emptying: Custom hopper, adapted perforation and dust removal.
- Management of empty big bags: Automated removal, compaction or shredding.
Media
View our equipment in photos
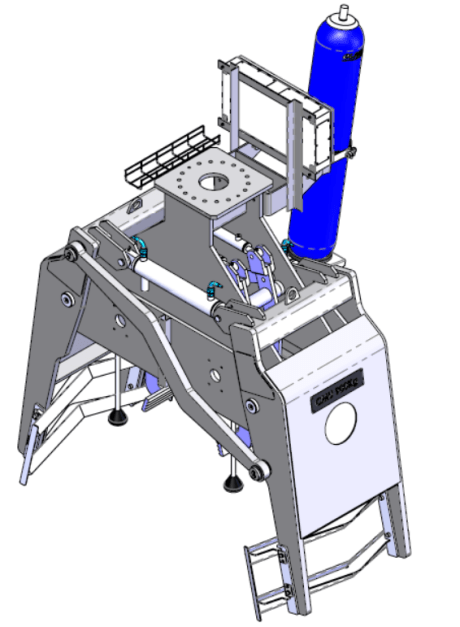
JUMBOT 1000 - hydraulic gripper for the safe lifting of drums or big bags
Hydraulic clamp designed for the JUMBOT 1000 for handling heavy loads
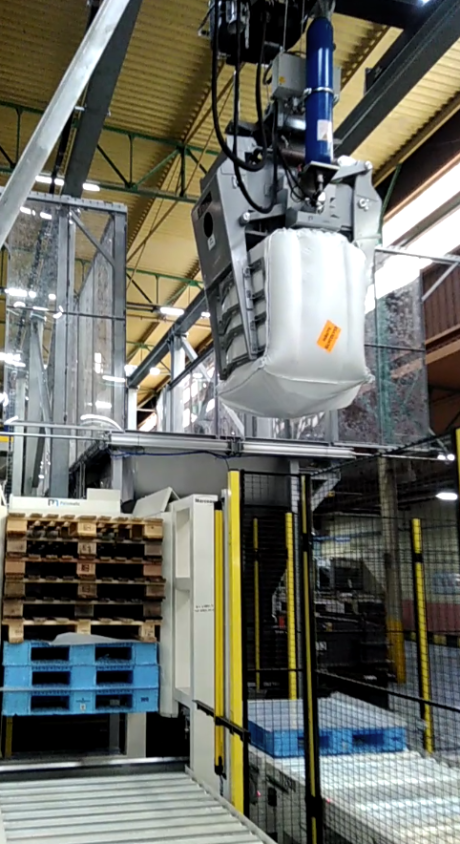
JUMBOT 1000 equipment with robotic gripper for automated handling
High-strength hydraulic clutch mounted on the JUMBOT 1000
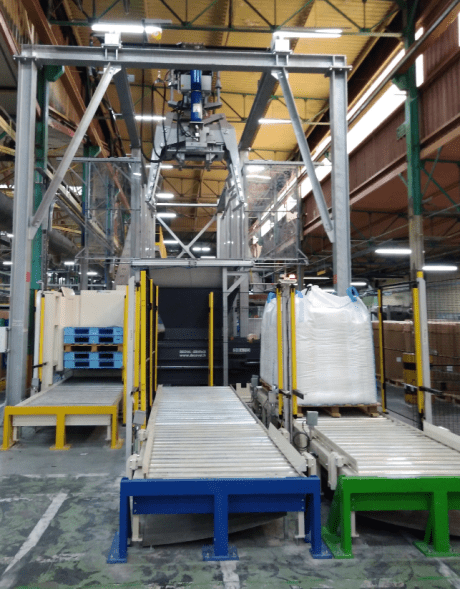
JUMBOT 1000 with hydraulic gripper
Close-up of the JUMBOT 1000 gripper in big bag lifting position
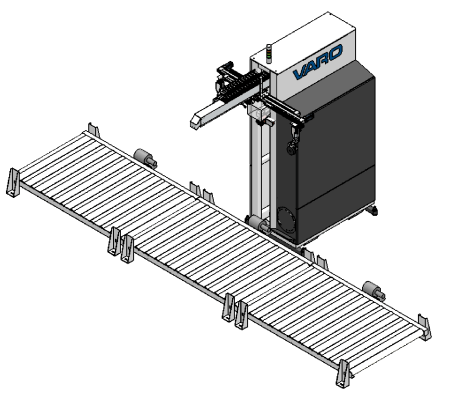
JUMBOT 1000 – safe plastic film cutting system
Automatic shrink film cutting module - integrated into the JUMBOT 1000
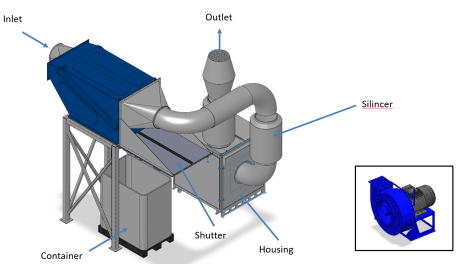
JUMBOT 1000 – robotic arm with equipment for automated removal of packaging film
Shrink-wrapping system controlled by the robot JUMBOT 1000
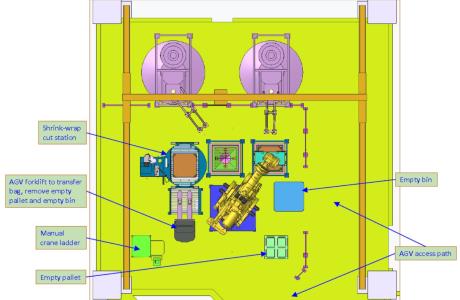
Layout of the JUMBOT 1000
Plan view of the JUMBOT 1000 station with robot, big bags, conveyors and AGV zones
Features
Technical specification
Criteria | JUMBOT 1000-500S (Single Pickup) |
JUMBOT 1000-500M (Multi-Pickup) |
JUMBOT 1000-1000S (Single Pickup) |
JUMBOT 1000-1000M (Multi-Pickup) |
---|---|---|---|---|
Robot type | FANUC M-2000iA/2300 | FANUC M-2000iA/2300 | FANUC M-2000iA/1700L | FANUC M-2000iA/1700L |
Robot payload capacity (kg) | 2300 | 2300 | 1700 | 1700 |
Big bag handling capacity | Up to 500 kg | Up to 500 kg | Up to 1000 kg | Up to 1000 kg |
Gripping system | Hydraulic clamp | |||
Safety system | "Chignon" clamp | Upper BB hook | ||
Number of pickup points | 1 (standard) | Up to 2 (multi-pickup) | 1 (standard) | Up to 2 (multi-pickup) |
Number of discharge zones | 1 (standard) | Up to 2 (multi-zone) | 1 (standard) | Up to 2 (multi-zone) |
Big bag cutting system | Options: U-blades, cross blades, or water jet cutting. | |||
Discharge hopper | Stainless steel 304 or 316; options: dust extraction, flow aid by pneumatic massage | |||
Empty big bag handling | Optional: CompactR / SchreddR / RollR | |||
Dust extraction | Optional (Pouyes rings) | Integrated with advanced filtration | Optional (Pouyes rings) | Integrated with advanced filtration |
Industrial connectivity | Standard (Profinet/Modbus) or full Industry 4.0 integration (Ethernet, IoLink) |