Cardboard box confined packaging station
Powder dosing line at dryer outlet for cardboard box packaging feed.
The objective of the installation is to fill 20 kg boxes in a confined environment.
The process capacity is 260 to 360 kg in one hour with an accuracy of +/-100g.The boxes are then placed on pallets totaling 18 units.
The filling station is powered by a powder pump which vacuums the product directly out of the customer’s dryer. This transfer phase takes 30 minutes to complete. Under the powder pump, a buffer volume of 500 liters provides continuous supply of the box packaging line. Pneumatic vibrators ensure good flow and regularity of the feed rate of the box conditioner.
The hopper is mounted on load cells in addition to the level probe to inform the customer in real time of the quantity of powder stored. An access hatch allows regular inspection of the hopper interior.
Installed under the buffer hopper are magnetic bars and a metal detector, for the capture and detection of ferrous and non-ferrous metals. The metal detector is associated with an ejector, allowing the evacuation of the detected particles. In addition, a security grid with a 10x10 mm mesh helps capture any foreign contaminants.
Capture and detection process safety equipment is easily accessible for cleaning via an access platform.
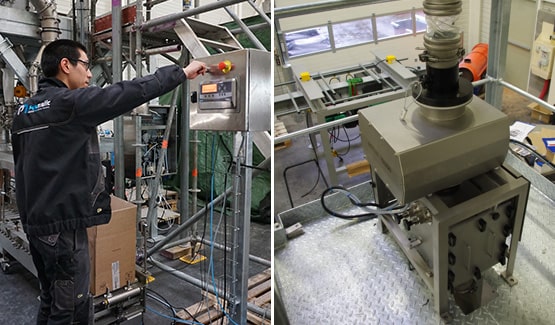
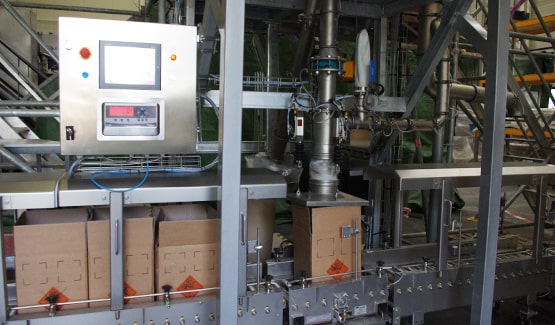
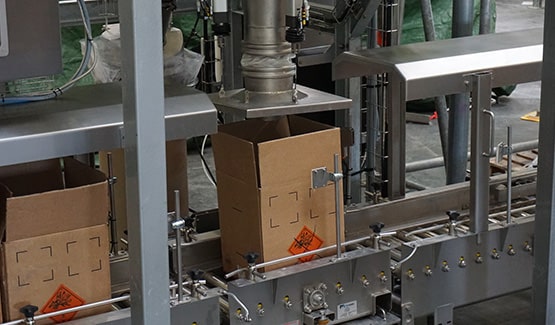
The metering of the powder to the packaging station is carried out by a butterfly valve directly flanged under the hopper. This valve is equipped with a 4-20mA positioner linked to the scale of the packaging station, on which the box is positioned. A flexible sleeve makes it possible to mechanically isolate the weighed packaging station from upstream equipment.
The powder is gravity fed and passes through process safety equipment before passing through the carton filling head.
The connection head makes it possible to seal the product drop tube and cardboard box, preventing dust emissions into the atmosphere. It consists of a telescopic tube, a flexible sleeve and a connection plate. The docking of the plate is driven by 2 pneumatic cylinders which seal against the top of the box. The piloting of the connection system is carried out by the automatic cycle.
A dust removal system collects and treats dust from the packaging and closing station.
A 304L stainless steel suction hood on the closing station, with a flow rate of 1000 m³/hr, prevents any dust emanation during the inner bag closing phase. The dust collector is equipped with a filter medium guaranteeing a particle rejection rate of less than 2 mg/m³.
The supply of empty boxes and the evacuation of full boxes is automatic via the use of one of the motorized roller conveyors. Each conveyor is equipped with a top cover to prevent foreign bodies from the upper floors falling into the boxes. The storage capacity of the boxes is 10 upstream and 4 downstream. All conveyors are mounted on rollers so that they can be moved for cleaning operations in the workshop.
The filling conveyor is positioned on an integrated vibrating table to ensure even filling of the box. The vibration is generated by an electric motor vibrator located on the lower part of the roller conveyor. This vibration makes it possible to break the slope of the product which could have formed during the filling phase.
A first weighing of the box is carried out automatically by the dosing valve with an accuracy of 500g. The vibrating conveyor is positioned on this first scale where the box is filled.
A second weighing of the box is carried out at the level of the closing station to double check the box on a commercial transaction scale.