Processed powders: soy flour, brewer yeast, corn starch, dried whey...
Manufacturing line for petfood industry
The customer, located in the U.S. Midwest, is a manufacturer of dry and liquid flavor enhancers for the pet food industry. Due to increasing demand of their products, our client evaluated their current production capacities and the need to increase daily output rates to meet a growing market.
The main challenge they faced was a manual and labor intensive feed system for their main mixer. The old setup was a traditional bag dump station for unloading 50 lbs. bags of dry ingredients into a pneumatic conveying line which filled the mixing and blending station.
This method resulted in several production barriers:
- Operator fatigue and risk of injury
- Slower mixer load rates
- Restrictive installation area due to existing equipment and structures
Our team of experts helped the client develop a system that would meet all three concerns. Initially, the design stage went through many changes and alterations. Our focus was to develop the best solution with the customer’s input to boost their confidence in the final solution. Therefore, our team designed an automated bag unloading solution with respect to the minimal floor space available for the installation.
Minislit® – Automated Bag Splitter
The core component of the material feed system is the Minislit® automatic bag dump station. This equipment is an industrial bag splitter that is capable of opening, unloading and removing bag waste at much higher rates then manual sack tip trays are capable of. By utilizing a system of sensors and automatons, the operator can load 5-6 sacks of material per minute into the bag tipping device.
Once the bag enters the cutting chamber, a sensor activates the band saw that cuts the bag down 3 sides. Inversion discs grab the bag material and pull it away from the powder. The powder is dumped into the discharge hopper below. The bag waste is caught by an integrated sack compactor that utilizes an auger to compact it into a polyethylene sheath. The sack tipping machine can be designed to tie into an existing dust filter system, or utilize an integrated independent filter of its own.
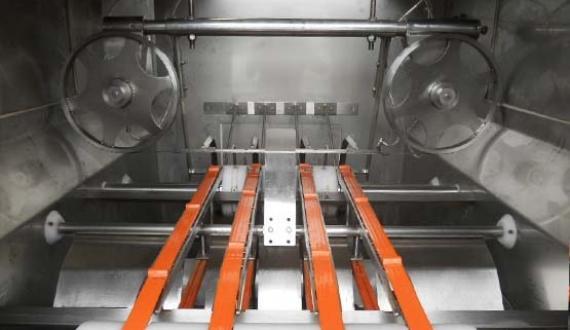
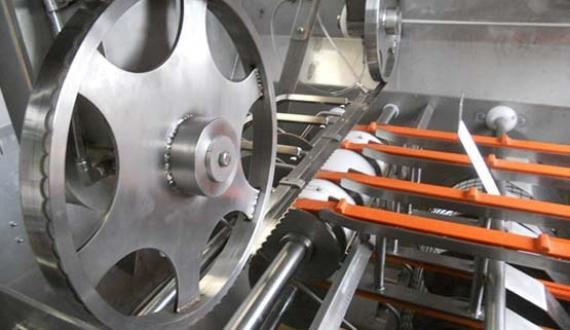
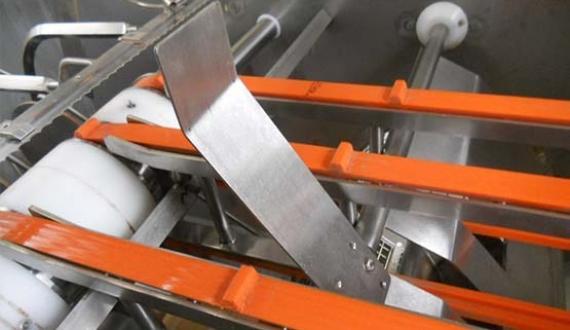
Vertical Conveyor
Common feeding methods for the automated sack discharging unit involve either a manual roller conveyor, or an inclined motorized belt conveyor. However, our team had to meet the challenge of the restrictive space available. Therefore, our team of engineers integrated a vertical bag lift. Combined with compact, vertical belt conveyors, the equipment automated the lifting and feeding of the bags to the elevated location of the Minislit.
Vacuum Bag Lift
Another component that made up this process was the Palamatic Sack Manipulator Manis 160-1700. Also known as bag manipulators, the equipment utilizes a vacuum that helps grip and lift the 50 lb sacks of powder. The bag gripper provides improved ergonomics of the work station, as well as preventing operator injury from repetitive heavy lifting. A simple level mechanism allows the operator complete control over the amount of vacuum being used to lift and lower the bag. By increasing the suction power, the bag is lifted with ease, and by lower the suction the bag is lowered and released. Industrial manipulators for sacks are usually comprised of a vacuum pump, jib crane or gantry, vacuum lifting tube system, and a vacuum boot.
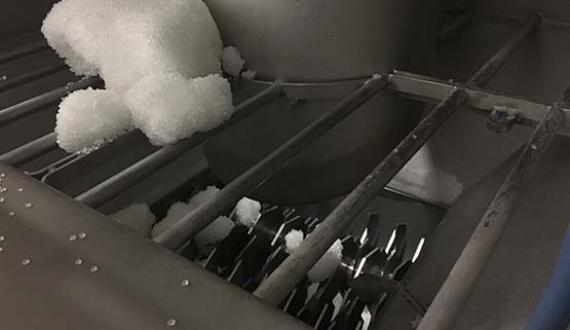
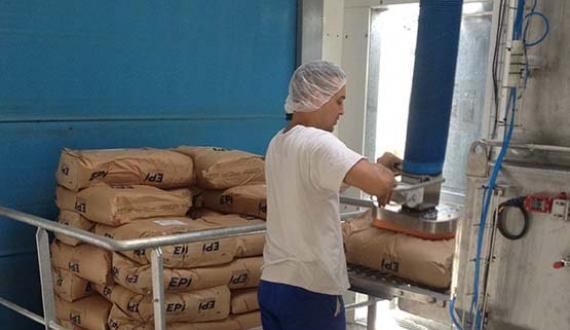
The EC35 Lump breaker and Cone Mill
Due to the client’s need to feed dozens of different materials through this system, they had concerns about the more difficult powders. Some of the materials have poor flow properties and tend to agglomerate when stored in the bags. The solution, a two-stage size reduction equipment setup.
First, the Palamatic EC35 Lump Breaker is a robust machine to help pre-break any solid lumps of powder that may be present after the bag is split and dumped from the Minislit located above. The powder lump breaker (also known as lump crushers, pre-breakers, flakers and industrial crushers) is often used with powders that have been in storage for long periods or were exposed to moisture. Powders coming from these conditions tend to form either compression lumps (soft agglomerates) or hard lumps of material related to humidity and moisture. The lump breaker uses a direct drive motor that spins two rotating knives surrounded by a coarse grid. When lumps hit the lump breaker, the grinding medium uses impact forces via the cutting knives and the grid to help break them up and return the powder to its original granular state.
The cone mill is then used to control the top end of the particle size range by ensuring all granules are 100% passing through a 1200 micron sieve. This provides the right amount of impact energy to shatter over size particles and improve the consistency of the blended batches at the end of the process.
Rotary Airlock Valve
The final piece of the system install is the necessary rotary airlock valve to help isolate the gravity discharge of the cone mill into the pneumatic conveying line below. Standard design rotary valve with 304 stainless steel construction and a rotary with fixed blades was all that was needed to help meter the milled powders into the dilute phase conveying system.
System controls
Finally, tying in all components, sensors, motors and automation is the Palamatic Pal’ Touch industrial control system. Palamatic Process has its own electrical design team to meet the needs of your project’s automation and control requirements. The electrical department was involved in the final design of our client’s project to help define the needs and technical control requirements.
Our control system can provide stamping of raw material feed, batch traceability, operator identification and automation reliability. We are able to work with several PLC brands including Allen-Bradley, Schneider Electric and Siemens to suit the client’s plant standards.
Since 1992, Palamatic Process has provided equipment to over 2000+ installations in over 30 countries. We offer knowledge and expertise in all manner of powder and bulk automated material handling needs.
Examples of our equipment solution offerings include: conveyor systems, handling equipment, screw conveyors, material handling equipment, vacuum conveying, dust collection, pneumatic conveying system (dense phase and dilute phase) and feeders. Contact one of our experts today for assistance with needed material handling solutions and to request a quote.