Processed product: Powder milk
Packing in a white room environment
Hygienic packing station under an atomization tower for infant powdered milk
International group producing alimentary powders for baby food industrie.
Palamatic Process as devellop an automatic big bags filling station for an international group producing alimentary powders for baby food industrie. In order to meet client hygienic requirements, Palamatic Process design an automatic big bags filling station named FlowMatic10®. Specially develloped for pharmaceutic and food industries, this model is intented for filling big bags in a white room and then store them in a storage area through an airlock and overhead conveyor. This device separate the different areas the big bags get through to avoid any contamination.
All the operations of setting up the big bag, filling, sampling, closing are carried out in strict compliance with the mainteance of absolute hygiene.
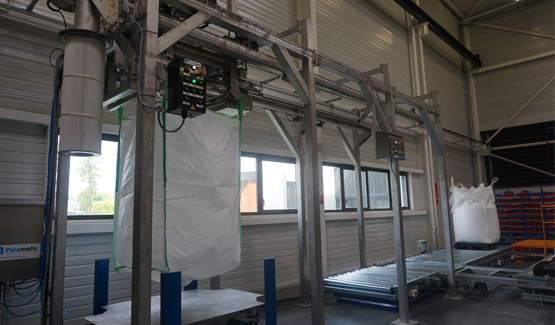
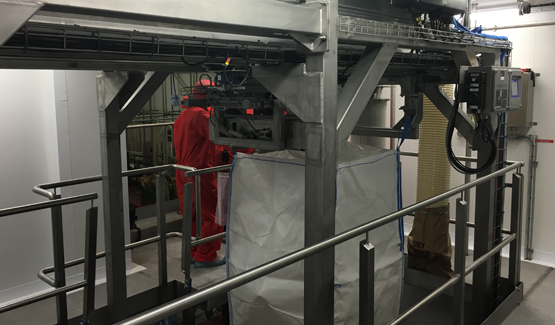
Operating mode :
At first, big bags are placed under the filling pipe and are maintained by a swelling seal system wich confines the passage of product and avoids the emission of dust. The operator starts the production cycle with Pal’Touch PLCs, wich offer great ease in the management of commercial weighing and production control.
Once the big bag has been put in place, the inflation of the big bag is ensured by a fan coupled to a battery of filters to ensure a clean and disinfected air.
The filling operation is carried out by a transfert screw – controlled by a frequency converter – wich doses the product inside the big bag. In order to densify the product at the outlet of the fluidized bed, a vibratory lifting table is provided in the airlock.
Once the densification operation carried out, the big bag is translated by the overhead conveyor to the intermediate zone to be welded and thus ensure a tight closure of the sleeve of the big bag. When sealed, the big bag is transferred to a gray area where the docking is done with the pallet handling. Pallet placemats are removed prior to maintaining an absolute level of hygiene. The big bag and palletized is then supported by a conveyor on the table lift.
All operations are performed by the operators from a platform without any steps, providing ergonomic access to all elements: fastening hooks, connection tube of the big bag spout, welder, sampler, magnetic detector, ...
This design by airlock avoids the introduction of pallets in sensitive area and maintain total hygiene. The double commercial weighing, combined with the filling line and the conveyors, offers high weighing accuracy and guarantees batch traceability.
This bulk bag automatic packing station offers filling rates up to 10 big bags per hour and capacities of 2 tons per big bag. The whole structure can be manufactured in 304L stainless steel or 316L stainless steel.