Processed Powders: Skim Milk Powder (SMP) and Whole Milk Powder (WMP)
Connecting the upstream powder process to downstream bulk packaging equipment
The client, located in Africa, is a manufacturer of dairy powders. The project goal was to upgrade their system for higher production outputs of skim milk and whole milk powders.
The main objective was to connect their fluidized bed and atomization tower process to their bulk packaging line while reducing the need for operator intervention.
The Palamatic Process solution
Our team of engineers provided a means of vacuum conveying from the fluid bed dryer to downstream bulk bag and sack fillers. This was conducted over the following stages: buffer storage with high and low-level probes, powder vacuum conveyor to cyclone collection, by-pass split valve to feed two filling stations. A second material loading station is added to the conveying line for product recycling.
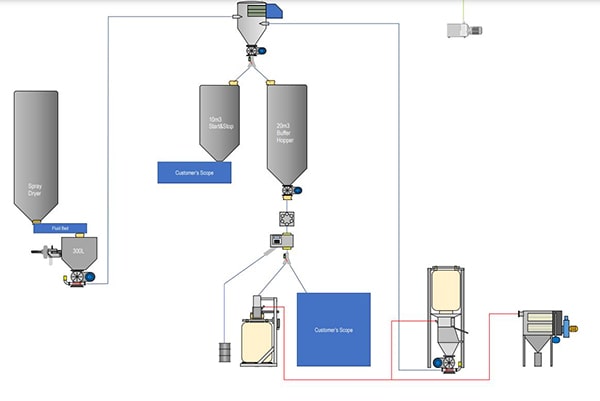
Buffer Hopper – 300 Liters
At the start of our process is the client’s fluid bed dryer. Our engineers designed a 300 liter buffer hopper in 304 stainless steel to provide a constant supply of SMP or WMP to the vacuum conveying system. The buffer hopper is outfitted with high level and low-level probes to send signals to the upstream process for automated filling of the hopper. Load cells are also incorporated to allow dosing by weight into the conveying system. An automatic powder sampler is fitted onto the buffer hopper to allow the operators to take real time production samples for quality control purposes. Flow aids are also fitted onto the hopper to promote the flow of the dairy powders into the vacuum system. A blow through rotary airlock valve completes this stage of the install for isolation of vacuum and a controlled feed of the powder into the vacuum conveying line.
Vacuum Cyclo-Splitter – Vacuum Pneumatic Conveyor
Once the milk powder is introduced into the pneumatic conveying line, it is transferred to a 200 liter cyclo-splitter (cyclone) for the necessary separation of the powder from the conveying air. The unit is fitted with a dust filtration unit that utilizes a timed jet pulse cleaning for maximum product retention. The vacuum transfer rate of the system is capable of 2.4 tons / hr. Also fitted to the cyclone are high and low-level probes, along with flow aid devices to allow automation of the filling and unloading of the cyclo-splitter. A high-pressure vacuum pump is responsible for the material transfer from the fluid bed dryer to the cyclone. A gravity rotary valve allows for the extraction and metered control of the milk powders from the cyclone, and a pneumatic by-pass directs the material to the customer’s existing sack filling line or the Palamatic Process supplied bulk bag filling station.
Magnetic Rotary Drum
In order to ensure that no metal particles are present in the packaged dairy powders, a magnetic rotary drum is installed just above the pneumatic by pass valve. The magnetic bars are situation on an easy to clean sliding rail system. The operator only needs to slide the magnetic bars out of the housing to clean between production runs.
FIBC Filling Unit – Flowmatic® 01
Palamatic Process offers a series of bulk bag filling systems to meet almost any bulk packaging production process. For this client’s project, the Flowmatic® 01 was selected for its minimalistic design and simple operation. The bulk bag operator hangs the handles on the rounded forks which can be manually adjusted to accommodate various FIBC heights and handle widths. An inflatable seal with clamping ring helps secure the filling spout of the jumbo bag in a dust tight connection. A BFM® flexible fitting provides isolation of the weight of the super sack filler, as load cells have also been integrated into the base of the structure. The filling head consists of a double jacket design with the inner tube providing the material filling and the outer tube allowing for air/material volume balancing and connection to a dust collector. Our team has extensive experience with supplying solutions for big bag handling systems.
FIBC and Sack Unloading Unit – Duopal® 125
The Duopal® 125 is a station combining the unloading operations of 50 lb sacks of powder and 1 ton bulk bags. An electrical hoist allows for the staging, lifting and loading of the bulk bag on the unloading station. The bulk bag discharge spout is secured via an unlacing cabinet that can be accessed from inside the integrated bag dump station. An anti-overflow gravity chute isolates the material being discharged from the bulk bag from the sack tip tray. A metal grid helps the operator rest the smaller sacks of minor ingredients while they cut the bag for material unloading. The system is connected to a central dust filter. The station outlet is fitted with another rotary airlock valve to control the flow of powder into the vacuum conveying system. The solution is perfect for production facilities requiring both big bag unloading and sack discharging stations.
Electricity & Automation
To further support the client, a functional analysis and PID is supplied to allow the installation team to connect the equipment supplied by Palamatic Process to an existing central control system.
Since 1992, Palamatic Process has provided equipment to over 2000+ installations in over 30 countries. We offer knowledge and expertise in all manner of bulk powder handling equipment solutions. Examples of our equipment offerings include: conveyor systems, bulk process equipment, pneumatic conveyor system material transfer systems, dust collection, sack tipping machine and food processing equipment. Contact one of our experts today for assistance with needed material handling solutions and to request a quote.
Palamatic Process has developed a turnkey process line, DairyBagging®, for packaging at the exit of the spray tower.