Processed powders: solid urea, demined water and liquid urea
Adblue - Urea - DeNOx
Supplier of DeNOX solutions for thermal power plants to reduce nitrogen oxide emissions.
The customer wants to obtain a preparation skid for liquid urea , from bulk urea, in order to be supplied in a tanktainer.
The solution offered by Palamatic Process consists of two skids for a global liquid urea flow rate of 24 m³/day:
- The first is a conditioning system for solid urea
- The second is a set for loading solid urea, loading and heating dissolution water, a dissolution tank and tanktainer.
Skid for conditioning solid urea:
The bulk urea is introduced into a steel buffer hopper with a capacity of 1,000 litres. The urea is then conveyed by means of a tubular conveying screw with a volumetric flow rate of 25 m³/hour and is positioned under the loading buffer hopper. The bulk urea ends its flow in a big bag filling station that can support the weight of a 1,600 kg big bag.
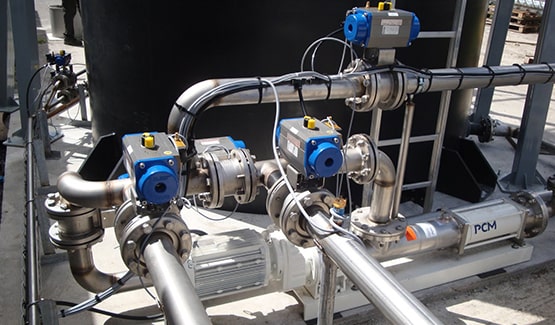
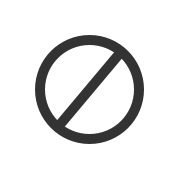
SKID for packing liquid urea into tanktainers:
Palamatic Process offers an EasyFlow® EF01 big bag emptying station that permits the positioning of the big bag on the discharge tray fitted with a sealing skirt with an electric hoist and a handling cross. In order to facilitate the flow of bulk urea, the dispensing tray is installed on silent-blocks and a 0.1 kW vibrating motor ensures vibration. The operator opens the unlacing cabinet and unties the big bag knot to permit the urea to be discharged.
A knife-type lump breaker, the EC50 model, is positioned at the outlet of the big bag emptying station to break up any clods that have formed in the big bag. It is composed of eight blades mounted asymmetrically on a very resistant shaft. This shaft is driven by a geared motor with a very high torque, which reduces very hard clods to a size acceptable for pneumatic conveying.
The urea is then conveyed through a tubular conveying screw and then a bucket elevator to the mixing tank. Bucket elevators offer a flow rate of 174 m³/hour and can have an elevation of between 3 and 45 meters to ensure the lifting of bulk solids. Antistatic nylon buckets have a capacity of 0.1 to 8.6 litres.
The urea, once it has passed through the bucket conveyor, falls into the 30 m³ dissolution tank and agitator that are positioned outside the plant. The tank is therefore anti-UV treated and the agitator motor is tropicalized. The quantity of demined water introduced into the tank is calculated by three scales with a unit capacity of 10 tonnes. Once the mixing is completed, two progressive cavity outlet pumps convey the material, at a flow rate of 32 m³/hour for this application, to two bag filters implanted on feet before filling a tanktainer.
Automaton:
The line is managed by global supervision.
The traceability of the production batches is managed by a daily archiving in excel format of each preparation. A printer completes the traceability system by labelling each sample taken.
The control cabinet controls all the equipment, with recipe management.
The control and protection of the motors is ensured with defect management.
The overall vision of the system is achieved by a supervision screen and a PC.