Automatic powder dosing unit
Automated ingredient dosing:
The DosingRobot® provides preparation and automatic dosing of small quantities of powdered ingredients. Its robotic arm guarantees precise dosing without cross contamination. This industrial station replaces the tedious manual dosing of smaller quantities of powdered ingredients.
- Eliminate risk of cross contamination
- 24/7 automatic operation with error-free dosing
- Full batch traceability
- Flexibility of recipes and productions
- Operates on the same production line with and without allergens
Models
DosingRobot® DR12 | DosingRobot® DR18 | DosingRobot®DR36 | |
---|---|---|---|
Maximum number of ingredients | 12 | 18 | 36 |
Batch production capacity per hour |
4 | 4 | 8 |
Floor space in m² | 15 | 21 | 35 |
Full-time equivalent operator | 0.2 | 0.3 | 0.5 |
Container capacity in liters | 200 | 200 | 200 |
The DosingRobot® automatic powder dosing solution
This premix packaging unit is designed for industries having to automate the dosing and mixing of dry ingredients. This secure powder dosing unit (premix) eliminates the risk of cross-contamination.
In addition, a mesh enclosure secures access to the weighing and dosing equipment area.
How to remove cross contamination in an automatic powder dosing unit?
A 6-axis robotic arm grips a food grade stainless steel container and places it under the desired weight dispensers. The robot trajectories are optimized so that the container only passes under the material dosing units. Therefore, the container cannot physically be contaminated with a third-party product. This is a huge advantage over conventional dosing units in which the container passes under each dosing unit. Even with a closed safety valve, some product may fall into the container as it passes.
This design makes it possible to do premixes with and without allergens on the same line, and guarantee optimal purity and a complete absence of contamination.
This warranty is perfect for applications in the food, pharmaceutical and chemical industries.
These industries condition raw materials that are fragile, critical or even potentially harmful in some cases. All the colorants, pigments, active ingredients, flavors, additives and minor ingredients can therefore be passed through this automatic dosing line.
The DosingRobot® line guarantees their weighing and packaging with great precision.
How does this automatic dosing line work?
Depending on the dosing line installed, 12, 18 or 36 powder feeding units make up the installation. The feeders are connected to a specially designed rack. Each feeder can be screw or vibrating type, depending on the product to be dosed. A powder storage hopper is located above the loss-in-weight dosing unit. The storage capacity is adapted according to the process batch requirements. Depending on the final design, these weighed hoppers are fed by a dedicated transfer line, such as pneumatic transfer or screw conveyors and is only dedicated to powders in the TOP of recipes. The rest of the ingredients for the premix are fed from outside the area over a metal catwalk.
The container of the mixture arrives in the screen enclosure by an automated roller conveyor. This conveyor serves as a buffer stock for the premixes.
AUTOMATIC DOSING OF POWDERS
The robotic arm grasps the container and places it under each powder dosing machine. The trajectories are optimized so as to pass only under the product dispensers called for by the recipe. The risk of cross contamination is therefore eliminated.
Volumetric or loss-in-weight screw feeders dose the products one by one into the container, according to the recipe. The precision of the screw feeders is ensured by a valve allowing perfect control of the drop tail. For sensitive or harmful products, a protective bib can be added as an option. Vibrating feeder technology can be considered for the dosing of fragile products and crumbly dry ingredients.
The computer monitoring precisely pilots each piece of equipment in sequence. At the end of the preparation, the dosage information is transmitted and stored in dedicated databases. After the batch is finalized, a batch report is recorded and automatically generated.
At the end of the dosing cycle, the container is placed on a conveyor and moved to the rest of the process, or directly to a container mixer. This specific mixer makes it possible to avoid transfer or a reconditioning operation. The container is mixed directly and therefore guarantees non-cross contamination.
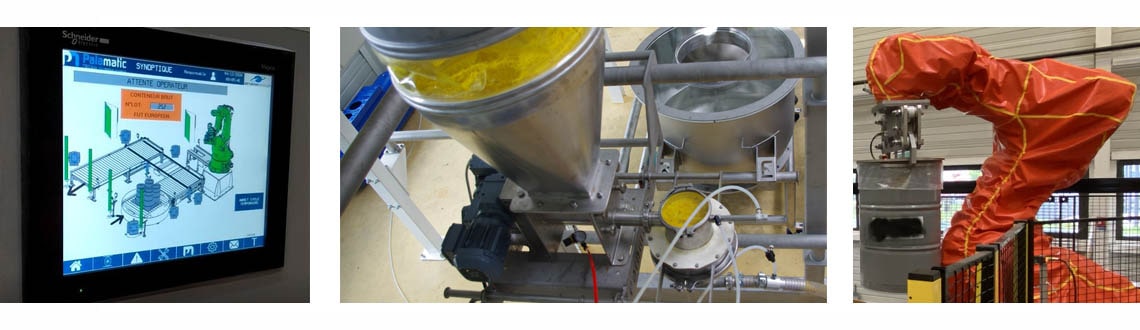
How is dosing accuracy obtained?
Precision dosing is ensured by screw or vibrating feeders. These powder dispensers are suitable for each of the ingredients to be mixed. Vibrating feeders have two types of troughs, tubular or rectangular, that are adapted according to the requirements of the material characteristics (including combustion), product contamination or process security. Screw feeders have several types of dosing coils. Compact and heavy powders are dosed by full coils while light and fragile products will be dosed by pigtail-style coils.
The dosing of micro-ingredients is provided by micro-feeders coupled to our tilting weighing spoon. This rotary scale ensures very high dosing precision. Only the product and the spoon are weighed, making it possible to use precision scales and achieve high levels of fine of dosing.
Industrial supervision
All production is supervised by industrial automation designed by the Palamatic industrial supervision system. The traceability of weight dosing of the ingredients is provided by databases connected to industrial IT. Food safety is respected at all times.
The automation and traceability can be integrated from either the central or local supervision stations. The Pal'Touch® screen with its dedicated dosing program makes it easy to create or modify a recipe.
What actions for the weighing operator?
The operator only fills the buffer cells of the dosing units. The integrated level probes tell the automaton which cells need to be loaded. The operator then loads and scans the filled cell. For customers needing large storage capacities, our team can automate the material replenishment process via pneumatic transfer lines coming directly from silos or bulk bag unloading stations.
Modular dosing design
This process line can easily adapt to numerous production changes. Its exceptional modularity allows for quick additions of new ingredients. A product with increased demand can also easily receive an automatic reloading of the designated buffer hopper.
The DosingRobot® unit has been designed to meet the needs for great flexibility of industrial production tools.
The DosingRobot® automatic powder dosing unit adapts to all the precision, repeatability and modularity requirements of manufacturers.
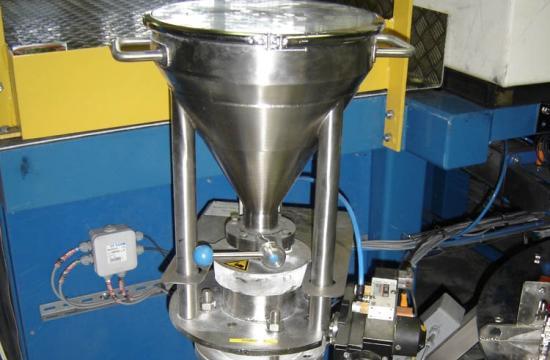
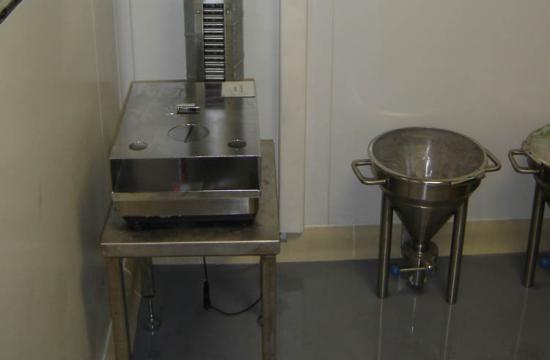
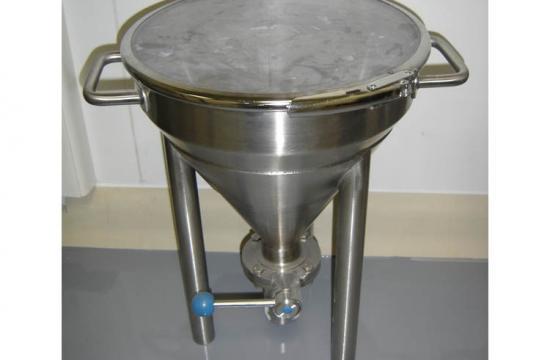
Read about our customers' installations using the DosingRobot® automatic powder dosing unit.
All equipment integrated into the DosingRobot® automatic powder dosing unit.