Processed powder: spice mixture with an apparent density of 500 kg/m³
Spice dosing
The company supplies products and flavours to professionals in the delicatessen and salting industry, caterers and ready meals.
The customer was looking to replace his manual dosing system, in the small-size packaging room, with a weight metering device with a packing filling head for 5 to 25 kg bags and 10 to 27 liter buckets, with a capacity of 1.5 tons per hour. The entire dosing system must be mounted on a frame on wheels to allow cleaning in the washing room.
The raw materials pass through a vibrating screener which aims to remove foreign bodies and agglomerates from industrial production lines involving raw ingredients and bulk materials handling. To guarantee current hygienic standards in the food industry, a magnetic detection system is installed at the outlet of the vibrating screen to retain ferrous metal particles, even those of low magnetism or very fine size. The bars, positioned at the heart of the bulk material flow, retain the metal particles to ensure the protection of machines and systems in the production line.
The bulk material passes through a drop pipe, which is connected to an industrial dust collection pipe, and falls into a D13 screw dispenser, connected by a flexible connector with an integrated discharge shaft. A butterfly valve is positioned between the pipe and the flexible connector to intercept the flow of gravity-operated bulk materials. The dosing unit allows batch or continuous volumetric or weight metering. The parts in direct contact with the material processed are made of 316 L stainless steel, while the non-contact parts are made of 304 L stainless steel. The D13 metering device provides a uniform, progressive and controlled flow of the spice mixture held in a buffer hopper. The system achieves a flow rate of 6,458 liters per hour for this application.
The screw feeder is installed on a complete packing system (filling head and weigher tray) installed on a mobile frame that facilitates the cleaning of the unit. This complete system is called "PalSack® 01 Filling Machine". It can fill 1.5 tons per hour with an accuracy of 150 grams.
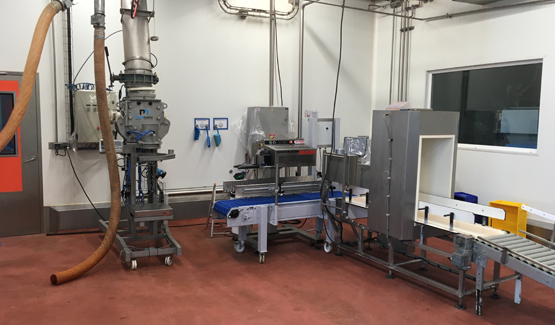
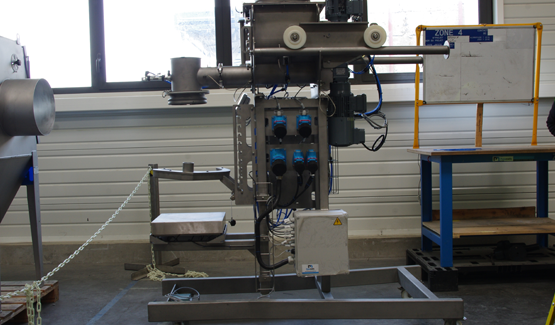
Bag conditioner
The operator positions the bag or pouch around the inflatable seal of the filling head. By means of a pneumatic pedal, it allows the seal to be inflated, which creates the tightness. The upstream dosing device fills the bag. The PLC is equipped with a "high" and "low" speed system in order to adjust the dosing accuracy as precisely as possible. The volumes are balanced via the double jacketed filling tube. Depending on the size of the bag, the operator positions the appropriate filling head. The head is placed using clamps and flanges.
Bucket conditioning
The operator disconnects the bag filling head and the flexible connector to position the bucket filling head. It is equipped with a vacuum system and does not touch the bucket at any time. A blocking stop is also provided to allow the rapid positioning of the bucket. The operator positions the bucket under the head and authorizes filling. The filling of the bucket can begin.
For both configurations, whether for bags or buckets, a dedusting ring is manually positioned at the vertical outlet of the D13 metering device. This metering device collects the dust generated during the filling process and is connected to the industrial dust collection system. It is adjustable according to the height of the different bags and buckets.
Once the bags or buckets have been filled, the mechanized roller conveyors take them to a bag welding machine and labeling machines.