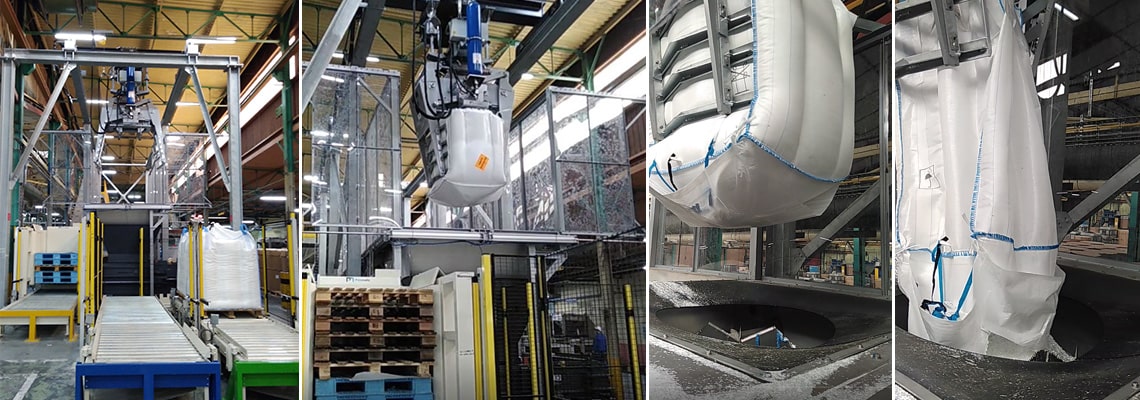
- 1. Strategic raw materials supply: the issues with geopolitics
- 2. Converting raw materials into sulfates: a precise and meticulous process
- 3. Precise filtration and "Filter Cake" extraction: sulfate purity is the heart of the process
- 4. Advanced transformation into hydroxides: rigorous technical expertise
- 5. Mixing hydroxides and creating CPTED: a precise chemical process
- 6. Thermal transformation from PCAM to CAM: calcination at 700°C
Gigafactories are driving the energy revolution, coordinating complex operations that start with the supply of raw materials.
Working closely with trusted suppliers, they ensure privileged access to lithium, cobalt, manganese and nickel, essential materials for the manufacture of lithium-ion batteries.
1. Strategic raw materials supply: the issues with geopolitics
The supply of raw materials for Gigafactories is a major geopolitical challenge, where the stakes are high and complicated. Certain countries dominate the production of key raw materials, creating a delicate situation.
For example, the DRC (Democratic Republic of the Congo) is a giant in the production of cobalt, which gives it significant power in the world. Therefore, it is crucial that the region remains politically stable to guarantee a steady supply. Lithium, comes mainly from Chile and Australia, making the industry highly dependent on these countries.
For manganese, South Africa and Gabon are major players, underlining the importance of working closely with them to guarantee the supply chain is not interrupted. Finally, Indonesia has become a world leader in nickel production, adding another layer of complexity to the supply chain.
Navigating this geopolitical situation requires strategic vision and strong partnerships to ensure a stable supply of raw materials essential to the energy revolution.
2. Converting raw materials into sulfates: a precise and meticulous process
At the heart of Gigafactories' work lies the precise transformation of raw materials into nickel, manganese and cobalt sulfates. This process demonstrates a thorough understanding of the details required to obtain the best possible sulfate quality, a very important step in battery manufacturing.
To achieve this transformation, each material is drained with great precision into special reactors. Sulfuric acid and oxygen peroxide are used to create an exact chemical reaction. The proportions and additions of other elements vary according to the needs of the manufacturers, meaning each step must be precisely adapted. This attention to detail ensures the purity of the sulfates, which is essential to the success of the rest of the manufacturing process.
3. Precise filtration and "Filter Cake" extraction: sulfate purity is the heart of the process
Extremely precise filtration is a very important stage in the production of Gigafactories. It is thanks to this delicate step that the "Filter Cake" is created, containing a pure concentration of nickel, manganese or cobalt sulfates, ready for use in the next stages of the process.
The filter press plays an essential role at this stage. It not only collects the "cake", but also removes the remaining liquid, allowing the sulfates to crystallize. Screws are sometimes added to the filter press outlet to break up the "cake", resulting in a more uniform powder. Once this stage is complete, big bag fillers either pack and prepare the powder for the next phase of the process, or for transport to the Gigafactories.
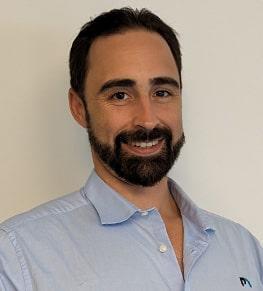
Do you work in the battery industry and have a powder handling project?
I'm available to discuss the subject with you.
Tarik, powder expert
4. Advanced transformation into hydroxides: rigorous technical expertise
The transformation of sulfates into hydroxides is an operation that requires a great deal of technical expertise. Sulfates are poured into a reactor with sodium hydroxide and other products added in varying quantities according to the company's needs.
The mixture remains in the reactor for some time before being fed to filter presses. Once again, the "filter cake" is isolated to recover the nickel, lithium, manganese or cobalt hydroxide "cake". This step is very important and must be carried out with precision to obtain a pure powder that will have an impact on the quality of the battery's cathode.
5. Mixing hydroxides and creating CPTED: a precise chemical process
During this essential step, the nickel, manganese and cobalt hydroxides are carefully mixed in a conical mixer.
The main objective is to ensure a perfectly uniform mixture, which takes a specific amount of time to achieve. It is in this mixture that PCAM (Cathode Active Material Precursors) takes shape, which is crucial to the quality of the positive electrode.
6. Thermal transformation from PCAM to CAM: calcination at 700°C
The thermal transformation phase, which takes place at 700°C in special calciners, is a crucial step. PCAM, which results from mixing of NMC hydroxides, undergoes a major change at high temperature. This complicated process takes place in rotary calciners, where PCAM is mixed with lithium hydroxide (or lithium carbonate) and special additives, reproducing an essential reaction.
This process consists of two heat treatment stages, which release gases and form CAM (Cathode Active Material). The exact duration of this process varies, but it is crucial to CAM's final crystalline structure and electrochemical performance.
All these operations, from sourcing strategies to meticulous transformation processes, position Gigafactories as major players in the evolution of energy. Geopolitical stability, technical expertise and respect for protocol are the cornerstones of this success.
By orchestrating these different stages harmoniously, these innovative facilities are laying the foundations for a sustainable energy transition, shaping the future of lithium-ion batteries. In this future, strategic vision combines with technical rigor to propel the energy revolution towards sustainable horizons.