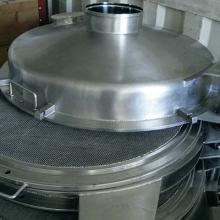
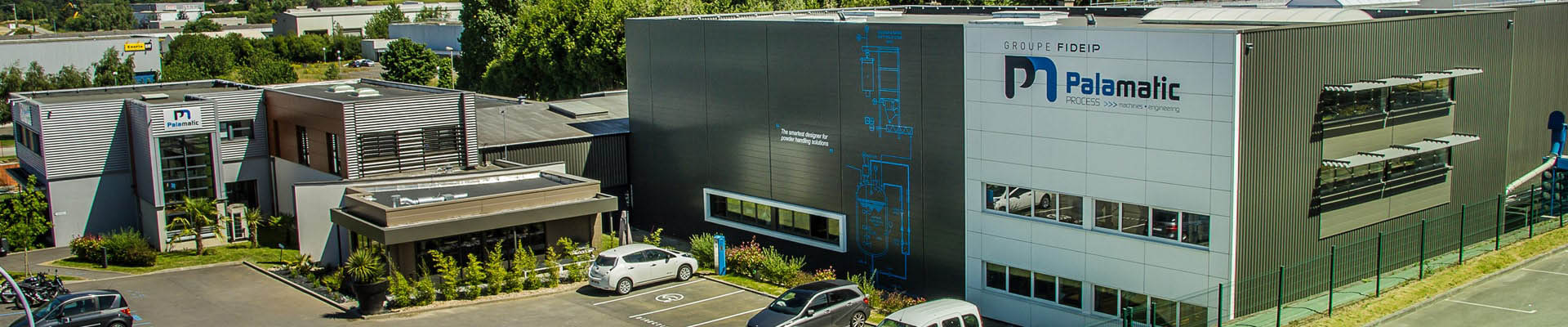
The hygiene of finished products is a crucial point in industrial processes. The treatment of foreign bodies, at the entrance to the line and at the exit of production, has become a standard in all high value-added industries.
Industrial sieves allow the continuous separation of solid products and the elimination of agglomerates. Palamatic Process has developed a range of vibrating screens and rotating centrifugal screens for the control and protection of your production line.
These two types of sieves exist in a hygienic version called Easy Clean Design.
Industrial sieves are essential equipment for the continuous separation of solid products and the elimination of agglomerates. They come in several models, each offering specific advantages to optimize your production process.
The vibrating screen is designed for reject removal and is ideal for high capacity safety sieving of powders. Its main objective is to improve product quality, increase your company's production by reducing downtime and cleaning. This type of sieve is particularly effective in ensuring continuous, high-quality production.
Palamatic Process offers a range of centrifugal screens designed to control and protect your production line. These sieves eliminate foreign bodies and reduce aggregates thanks to particle size separation of powders and bulk products. With Palamatic Process, you are guaranteed to obtain a clean product, without clods or foreign bodies, thus optimizing the quality and safety of your production line.
All of our industrial screens can be installed on a pneumatic transfer line. This configuration allows you to optimize flow rates without pressure loss, guaranteeing maximum efficiency of your production process. The aim of the sampler is to obtain a representative sample of the material produced.
This equipment makes it possible to guarantee confined sampling, while guaranteeing the safety of the operator by avoiding any contact with the product. It is essential to ensure the quality and conformity of your products.
The magnetic detector is designed to remove all metals from the preparation, thus avoiding any foreign bodies. It plays a crucial role in ensuring the safety and quality of your finished products.
The vibrating screen works by mechanical vibrations, which makes it suitable for sieving dry or wet products. It is particularly effective for separating particles of different sizes and is suitable for medium to high flow rates. In addition, it is less aggressive on fragile products, making it an ideal choice for delicate materials.
The centrifugal sieve uses centrifugal force for sieving. It is particularly effective for fine powders and products that are difficult to sift. This type of screen allows higher flow rates in a smaller footprint, but it is more aggressive and can generate heat. It is perfect for breaking up products.
Choosing the right sieve for an industrial application depends on several major factors. First of all, it is necessary to consider the characteristics of the product to be sifted. This includes the nature of the product (powder, granules, fibers), particle size, density and fluidity, as well as sensitivity to heat or shock. The requirements of the production process are also decisive. The required flow rate, useful sieving precision, space constraints and the production environment (ATEX, hygienic) must be taken into account. The objective of sieving is another important criterion, for quality control, particle separation, deagglomeration or product recovery.
Industrial sieves play an important role in improving the quality of the final product in several ways. First, they eliminate contaminants by removing foreign bodies and impurities, ensuring the purity and safety of the final product. Then, the sieves guarantee particle uniformity, which improves the texture and consistency of the product. They also allow crumbling by breaking up agglomerates, thus providing better homogeneity of the product. Industrial sieves are also essential for quality control. They contribute to compliance with industry quality standards and thus facilitate product certification and traceability.