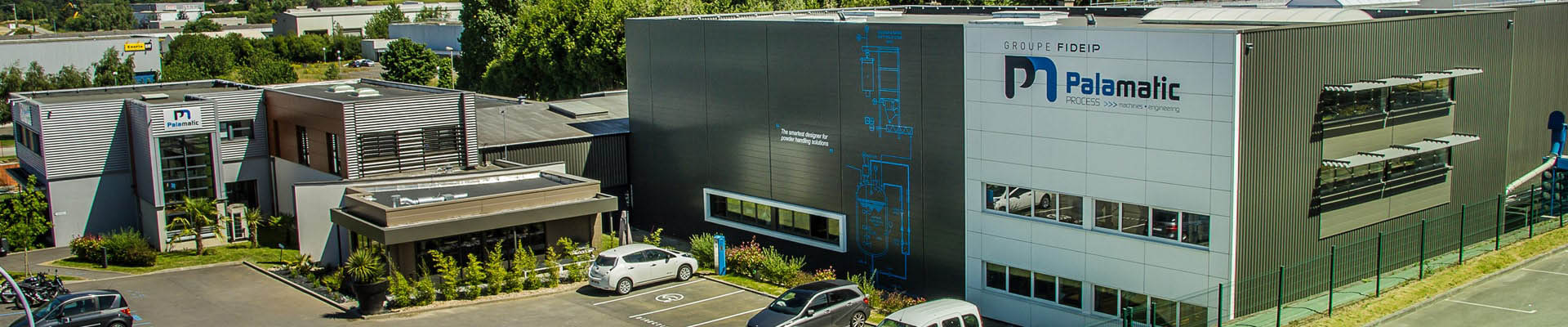
Case studies - Rubber
Storage, deconditioning, conveying, dosage, micro-ingredients preparation, incorporation banbury mixer arm type "Z".
The production of rubber mixtures can involve between 10 and 20 ingredients (sulphur, organic peroxide, zinc oxide, magnesia oxide, blowing agents, calcium carbonate, barite, carbon black, Kevlar, talc, precipitated silica, Teflon...). All these components are introduced with precise weight control into the "banbury" or "Z-arm type" mixer.
Case studies with our customers
Rubber parts production line
Chemical
Preparation process for the micro-ingredients
Chemical
Bag unloading station for reactor loading
Chemical
Process for feeding 2 lines of carbon black from flowbins
Chemical
Preparation and dosing workstation for metal powders
Chemical
The storage of powders (calcium carbonate, barite) is carried out in silos. Big bag discharging stations ensure the loading of carbon blacks according to the different grades.
Weighing hoppers allow the preparation of the doses before introduction into the mixer. A "skid" station for the preparation of pre-weighing is located along the line to ensure that the "recipe" is carried out.
Pre-weighing is carried out manually by an operator on an ergonomic weighing station or automatically via a carousel of weight screw feeders.