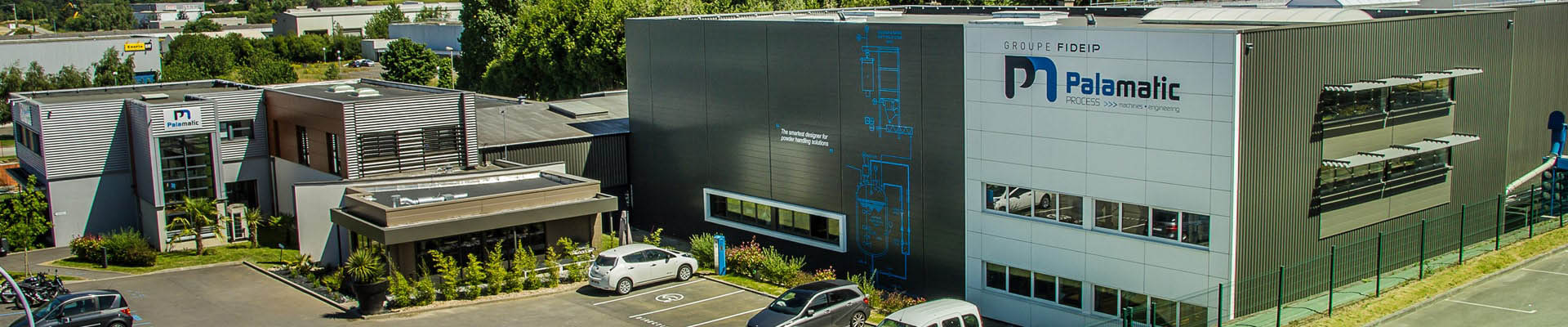
Industrial dust collection - Dust containment:
Flexible fitting, BFM® Fitting Sleeve
-
Ergonomics4
-
Ease of integration4
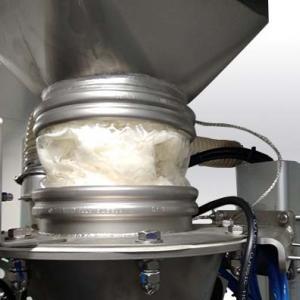
Sack compactor
-
Overall dimensions2
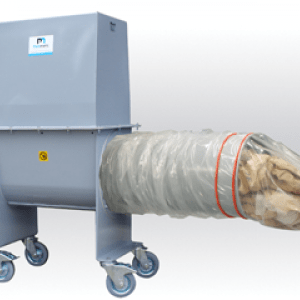
Built-in dust collector
-
Rate5
-
Efficiency5
-
Ease of integration5
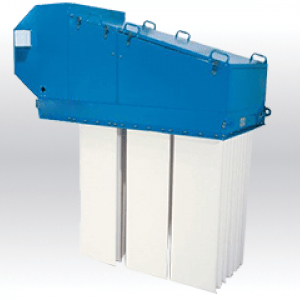
Dust control - Dedusting ring
-
Rate2
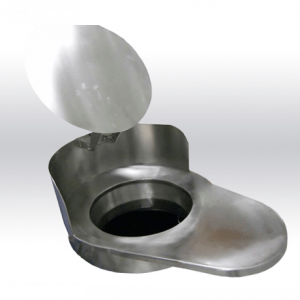
Centralized dust collector
-
Rate5
-
Efficiency5
-
Ease of integration2
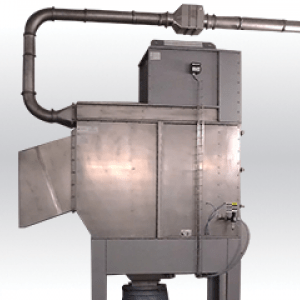
Bulk bag compactor - CBB125
-
Containment5
-
Ease of implementation3
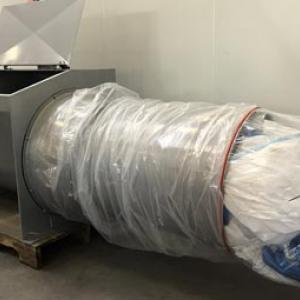
Dust control - Suction booth
-
Rate4
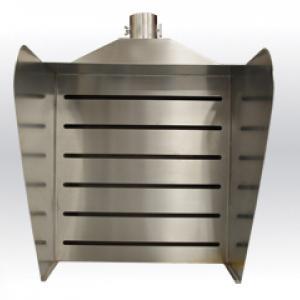
Hopper venting filter
-
Efficiency5
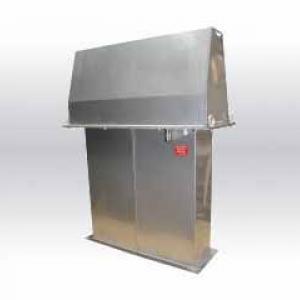
Palamatic Process has developed industrial dust collection systems for all types of industrial production lines involving raw ingredients and bulk materials handling. Sensors positioned at the various dust emission points are connected to a centralized dust collection unit that provides the treatment of free floating particles.
Processing powders and bulk materials can produce dust that can cause respiratory problems or allergic reactions for operators working on these powder handling lines.
The various powder handling and production processes such as bulk bag filling, bulk bag discharging, sack filling, bag dumping, mixing, dosing, crushing, grinding, reactor feeding, dosing and storage involve the installation and use of centralized or built-in industrial dust collection systems. Indeed, it is imperative to protect operators while complying with safety, health and environmental regulations.
Once the air has been cleaned of impurities using an industrial dust filter, it can be safely released back into the atmosphere.
Dust collection is carried out thanks to the use of various industrial equipment such as pouyès rings, suction booth or hopper venting filter for balancing the volumes in the hoppers and dosing equipment.
Dust extraction in industrial processes guarantees a safe working atmosphere by safeguarding the health of operators. The installation of an industrial filtration system also provides proper functioning of the various industrial equipment and improves the production process.
Palamatic Process dust collection systems can be easily integrated into powder production lines for a healthy working environment and a clean process.
The treatment of dust by the installation of an industrial vacuum system makes it possible to reduce the dust particles present in the air which can alter the quality of the working environment of the powder handling lines.
There are different types of dust collectors: cartridge dust collector, pocket dust collector, sleeve dust collector. These industrial filtration systems are defined according to the characteristics of the treated powders: hygroscopy, granulometry, explosiveness...
Dust vacuuming and dust collection, thanks to an automatic cleaning system, can be carried out in a drum, bulk bag or reintroduced into the process to reduce product loss.
You wish to set up a dust removal system? Discover our white paper to help you make your choice: How can I optimize my dust collection network?