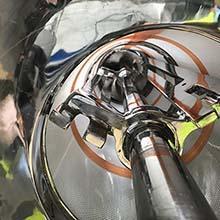
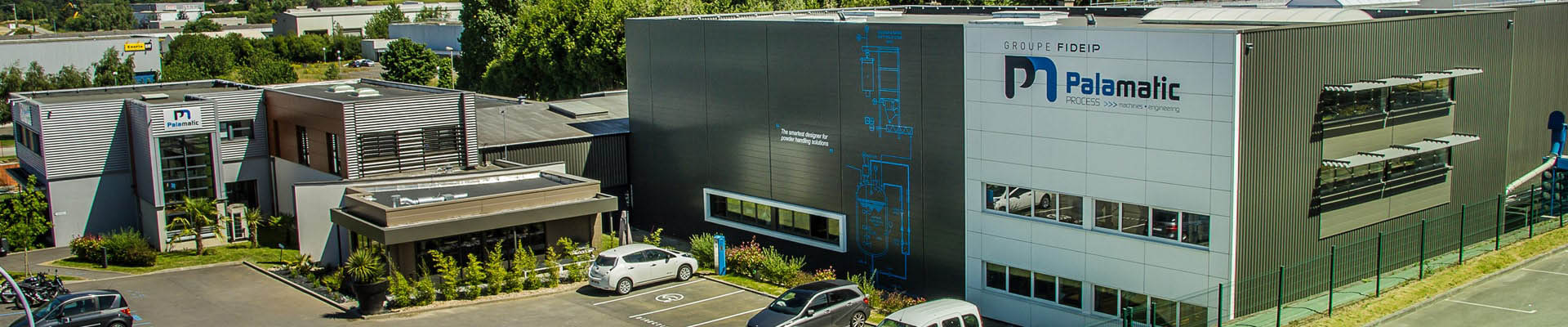
Industrial sieves allow the continuous separation of solid products and the elimination of agglomerates during powder processing.
Palamatic Process has developed a range of vibrating screens and centrifugal screens for the control and protection of your production process. Other equipment such as the powder sampler or the magnetic detector can also meet this type of need.
Range of vibrating screens
The vibrating sifter, also called vibrating sieve, vibrating screener or vibrating screen, eliminates rejects with precision and ensures safety from the reception of materials and at the end of the process. It can be installed on a new or existing production line. Very easy to use, this vibrating screen is also easy to maintain thanks to easy assembly and disassembly to minimize cleaning time. This equipment is intended for all sectors such as the food industry, the pharmaceutical sector, chemicals and even synthetics. It can be installed on a pneumatic transfer line or in gravity mode. A hygienic version of the Palamatic GSC vibrating screener is available for industries with strict quality standards.
Some characteristics of the PALAMATIC vibrating sieve range:
The centrifugal (or rotary) sieve separates foreign bodies from powders and granules. The product is transported into the sieving grid by the feed auger where it is rotated by the rotating blades. The fines pass through the screen while the waste is ejected towards the reject outlet. The rotating sieves thus ensure a very high level of hygiene and respect for the product handled. This type of screen can also be installed on a pneumatic transfer line. This makes it possible to optimize flow rates without loss of pressure. A hygienic version is available for the centrifugal sieve.
Some characteristics of the PALAMATIC PROCESS centrifugal sieve range:
Are you hesitating between a centrifugal sieve or a vibrating sieve? Palamatic Process powder experts answer your questions and are available to help you find the solution best suited to your needs and process constraints.
Palamatic Process GSC vibrating screens offer several significant advantages. Firstly, they guarantee high capacity safety sieving for powders, thus providing high performance. Then, they efficiently eliminate rejects, which helps improve the quality of the final product. In addition, their design reduces downtime and cleaning, which has the effect of increasing production and therefore productivity. Additionally, with a hygiene score of 5/5, these vibrating screens are ideal for industries that require high hygiene standards. Finally, they are available in 3 different models, which allows them to adapt to different applications, thus offering great flexibility.
The "Easy Clean Design" option is a hygienic version available for Palamatic Process vibrating screens and rotating centrifugal screens. This special design offers easier and faster cleaning, thanks to better accessibility to internal components. It also reduces the risk of cross-contamination, which is crucial in production environments where hygiene is paramount. This option is also designed to meet the strict hygiene standards of certain industries, such as food processing or pharmaceuticals, thus ensuring increased compliance. This option is particularly useful in production environments where frequent product changes require regular and efficient cleaning.
Industrial screens can be integrated into a pneumatic transfer line to optimize flow rates, ensure a continuous process, save space, facilitate integration and provide versatility to suit production needs. This integration enables continuous quality control while maintaining pneumatic transfer efficiency, thereby optimizing the entire production process.