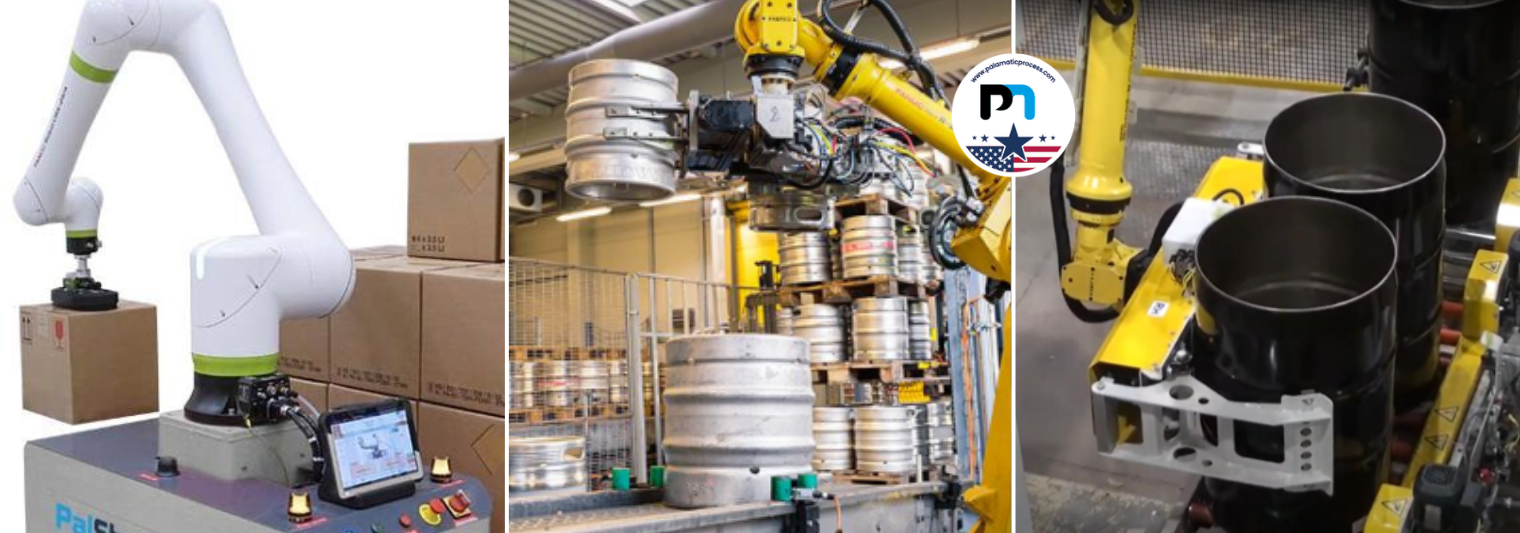
Industrial robots, pioneers of this revolution, have been synonymous with speed and power for several decades. But the emergence of cobots (collaborative robots) has turned the landscape upside down.
These machines are specially designed to interact safely with humans, paving the way for collaborative robotics that is no longer limited to large companies. So what are the fundamental differences between a cobot and an industrial robot? This article explores their characteristics, applications and respective benefits.
1. Industrial robots, definition and operation
What is an industrial robot?
An industrial robot is an autonomous or semi-autonomous machine capable of performing repetitive and demanding tasks. Designed to replace humans in industrial environments, these robots are programmed to offer maximum productivity.
Examples of use:
- Automotive assembly (welding, painting, screwing).
- Handling of heavy loads in logistics warehouses.
- Cutting and polishing in the metallurgical industry.
Main characteristics:
Precision and speed:
- Perfect for tasks requiring extreme repeatability.
- The robots can operate 24 hours a day without interruption.
Load capacity:
- Some industrial robots can lift loads of more than 500 kg.
Securing the workspace:
- Operation in cages or delimited areas to protect the operators.
Advantages:
- Raw power: Ideal for tasks requiring strength and endurance.
- Maximum efficiency: Suitable for large series.
- Robustness: Designed to withstand extreme environments.
Limitations:
- Reduced flexibility: Requires complex reprogramming in the event of a change in task.
- High cost: Significant initial investment, plus maintenance costs.
- Dangerous: Their operation requires strict safety devices.
2. What is a cobot ?
A cobot is a collaborative robot designed to work hand in hand with human operators. Unlike traditional robots, cobots incorporate safety sensors and learning technologies that enable safe interaction.
Main features:
Collaborative design:
- Collision detection and automatic shutdown in case of contact.
- Ergonomic design to prevent accidents.
Ease of integration:
- Plug-and-play in existing production lines.
- Intuitive programming thanks to graphical interfaces.
Versatility:
- Suitable for a variety of tasks, from light handling to assembly.
Advantages:
- Built-in safety: No need for physical barriers.
- Flexibility: Rapid reprogramming to change applications.
- Low cost: Accessible to SMEs, with a rapid return on investment.
- Compactness: Perfect for restricted workspaces.
Limitations:
- Limited payload: Generally between 5 and 20 kg.
- Lower speed: Not as fast as industrial robots.
- Limited specialization: Not always suitable for demanding environments.
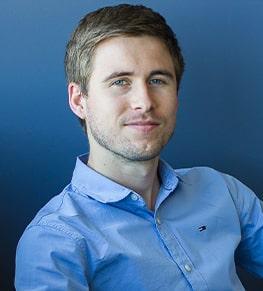
Planning to add a robot or cobot to your operations ?
I’m available to help assess your project and deliver a tailored automation solution.
Guillaume, expert in collaborative robotics and manufacturing automation
3. Cobots vs robots, the key differences
Safety
Cobots:
- Designed to operate without physical barriers.
- Equipped with advanced sensors to detect the presence of humans.
- Ideal for environments where safety is a priority (SMEs, laboratories, etc.).
Robots:
- Operate in cages to avoid accidents.
- More suitable for environments where speed and power take precedence over collaboration.
Flexibility
Cobots:
- Easy to program using simple interfaces (tablets or applications).
- Suitable for small series or environments where tasks change frequently.
Robots:
- More complex programming, often reserved for experts.
- Not very suitable for environments requiring frequent modifications.
The cost
Cobots:
- Average cost: €30,000 to €50,000.
- Quick return on investment thanks to their ease of integration.
Robots:
- Average cost: often more than €100,000.
4. Why choose a cobot ?
Benefits for small and medium-sized enterprises (SMEs)
Cobots democratize access to robotization thanks to their affordability and ease of use. Unlike industrial robots, which require heavy investment, cobots allow for gradual adoption.
A solution to labor shortages
In sectors such as logistics and industry, where the shortage of skilled labor is a major problem, cobots offer an effective alternative. They allow operators to focus on tasks with higher added value.
Specific applications
Collaborative welding:
- Welding cobots (e.g. Universal Robots UR10 or Fanuc CRX) automate repetitive tasks while allowing for human intervention.
Palletizing:
- Very popular in warehouses and packaging lines.
Assembly:
- Used to assemble delicate electronic components.
Logistics:
- Sorting parcels in distribution centers.
5. Towards co-existence of cobots and robots
Cobots are not replacing industrial robots
Collaborative robotics is ideal for tasks requiring flexibility and human interaction, while traditional robots remain indispensable for heavy and massive processes.
Examples of coexistence
A production line can include robots for the manufacturing stages and cobots for logistics or inspection.
Future trends
AI and machine learning: Cobots are becoming increasingly autonomous.
Mobile applications: Cobots integrated with AGVs (Automated Guided Vehicles).
6. Conclusion
The choice between a cobot and an industrial robot depends on the specific needs of your company. If your priority is safety, flexibility and a quick return on investment, cobots are an essential solution. On the other hand, for massive tasks requiring speed and power, traditional robots are still the best choice.
In any case, robotization is no longer the sole preserve of large companies. With cobots, technology is becoming accessible to everyone.