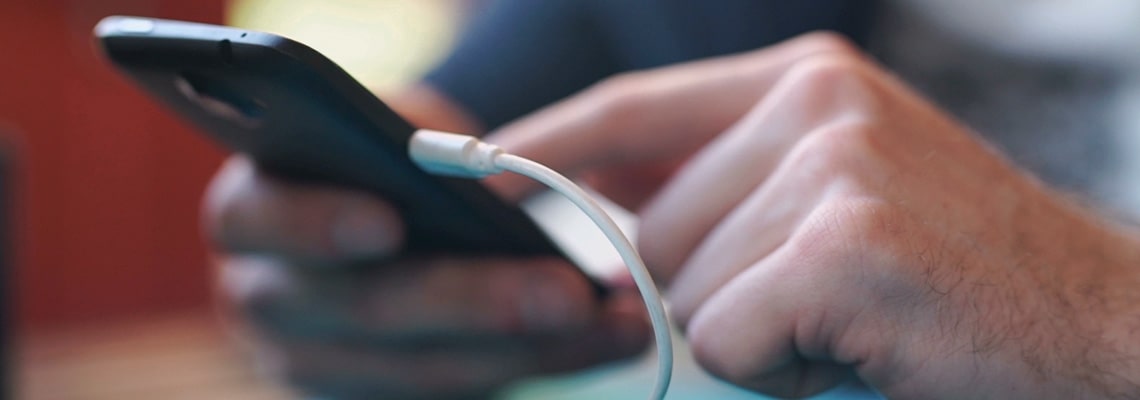
- 1. Mining for tomorrow's batteries
- 2. Purification and Preparation: A Critical Step Toward High Quality Batteries
- 3. The essence of battery power: The magic of electrode manufacturing
- 4. Battery assembly: Harmonizing components for optimal power
- 5. Protection and aesthetics for a battery ready for action
- 6. Quality Control and Shipping: Strict Standards for Reliable, High Performance Batteries
- 7. Palamatic Process: Recognized expertise in battery manufacturing for sustainable energy solutions
Constantly evolving, the battery manufacturing process plays a critical role in creating efficient and sustainable energy solutions. For more than 20 years, Palamatic Process has been supporting our customers by providing mineral handling solutions and helping to create films for battery winding. In this article, we dive deep into the battery manufacturing process, exploring each key step that transforms raw materials into a reliable source of energy.
From ore extraction and purification to electrode manufacturing and careful battery assembly, we'll uncover the secrets of this technology. Then, we'll cover the shaping, packaging, quality control and shipping that complete the process to deliver long-lasting, high-performance batteries.
Dive into the world of battery manufacturing, where precision, innovation and sustainability are the key words.
1. Mining for tomorrow's batteries
To bring these energy sources to life, it is essential to locate and extract the necessary raw materials. Ores are minerals buried deep in the earth, containing metals such as lithium, cobalt, nickel and other materials that are essential for battery production. To ensure optimal extraction, advanced methods are used, ranging from geophysics to geochemical prospecting.
These state-of-the-art techniques enable the precise location of minerals, ensuring responsible and sustainable resource extraction. With this stage of mineral extraction, we can begin the battery manufacturing process by implementing environmentally friendly practices and ensuring the supply of raw materials essential to the energy transition.
2. Purification and Preparation: A Critical Step Toward High Quality Batteries
Once the valuable ores are extracted, a crucial step comes into play: purification and preparation.
This step involves cleaning and transforming the ores into usable materials. Here, the metals are separated from the other elements present in the ores. This operation ensures a precise and homogeneous chemical composition for optimal battery performance.
The ores are transformed into powders or liquids, ready to be integrated into the different phases of battery manufacturing. Thanks to this careful purification, only the purest and most suitable materials are used, guaranteeing high-quality, long-lasting and high-performance batteries
3. The essence of battery power: The magic of electrode manufacturing
Once the ores have been purified, the manufacturing of the electrodes begins. Electrodes are the thin layers that are vital to the process of energy storage and transfer within the battery. The electrodes are divided into two types: the anode and the cathode. Their creation involves a mixture of metal powders made with other carefully selected ingredients to form a specific paste. This paste is then gently spread on metal sheets, dried and cut. This step is of paramount importance, as the composition and structure of the electrodes have a direct impact on the performance and life of the battery.
4. Battery assembly: Harmonizing components for optimal power
After preparing the key components such as the electrodes, they are meticulously stacked, alternating the anode and cathode, and separated by an insulating material called a separator. The separator plays an essential role in preventing short circuits and promoting selective ion transfer.
Once the electrodes are stacked, a precious liquid called electrolyte is added. This electrolyte allows the electrons to move freely inside the battery, promoting the flow of energy and ensuring a smooth flow of electrical charges.
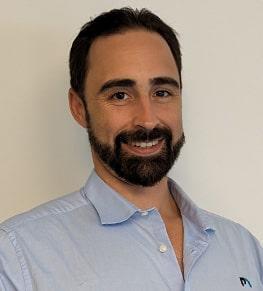
Do you have a handling project in the battery sector?
I am available to advise you.
Tarik, powder expert
5. Protection and aesthetics for a battery ready for action
To ensure adequate protection, the battery is then placed in a sturdy case, guaranteeing both safety and durability. These cases can be made of metal or plastic, and are often designed in a rectangular shape for convenience and easy integration into various devices.
However, shaping is not limited to protection, it also plays an aesthetic role. Cases can be designed with elegant and ergonomic designs, reflecting a commitment to innovation and attention to detail. As a result, the perfectly shaped and carefully packaged battery is ready to be used in a variety of energy applications.
6. Quality Control and Shipping: Strict Standards for Reliable, High Performance Batteries
Each unit goes through a rigorous quality control process to ensure that the battery functions properly and meets standards. Performance, capacity, strength and safety tests are performed to ensure optimum reliability. If the battery passes all tests and meets all requirements, it is then carefully prepared for shipment. It is meticulously packaged to ensure adequate protection during transport, using quality materials and advanced packaging techniques. Ready to be used in final products, the battery is then shipped to manufacturers of phones, computers, electric cars and other electronic devices
7. Palamatic Process: Recognized expertise in battery manufacturing for sustainable energy solutions
From ore extraction to careful assembly, purification, electrode manufacturing, shaping and packaging, to quality control and shipping, every step is critical to creating high-performance, sustainable batteries.
At Palamatic Process, expertise and know-how in battery manufacturing ensures a commitment to quality, innovation and sustainability in every production process.
Whether you are a manufacturer of phones, computers, electric cars or any other electronic device, take advantage of state-of-the-art expertise and technologies to help you achieve reliable, high-performance batteries that meet user requirements.
Feel free to contact our solution managers today to discuss your battery manufacturing needs. Together, we can create energy efficient and environmentally friendly solutions.